Wrench Technology: From Hand Tools to Smart Systems
Wrench technology sets the stage for this enthralling narrative, offering readers a glimpse into a story that is rich in detail and brimming with originality from the outset. From the […]
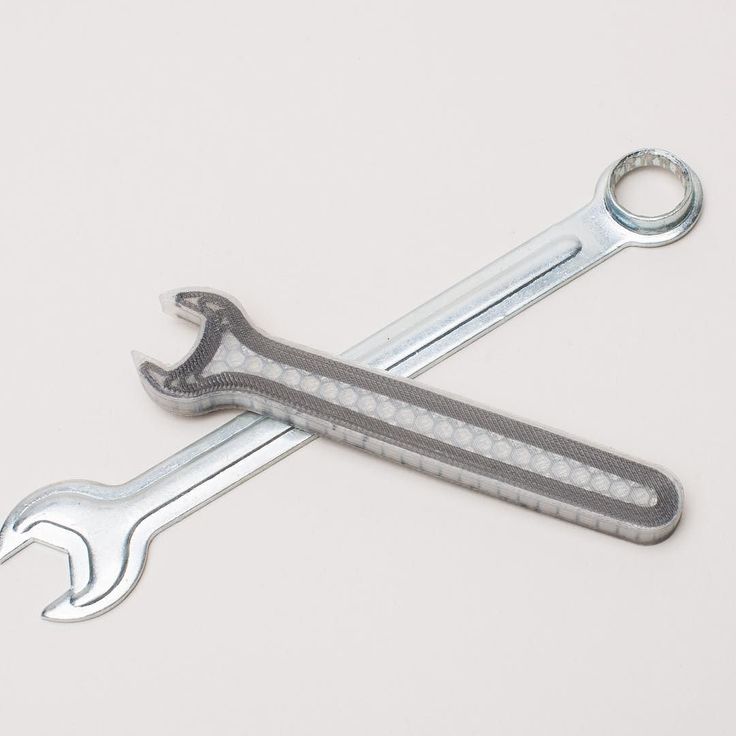
Wrench technology sets the stage for this enthralling narrative, offering readers a glimpse into a story that is rich in detail and brimming with originality from the outset. From the humble beginnings of hand-operated wrenches to the sophisticated powered tools of today, the evolution of wrench technology reflects the ingenuity and relentless pursuit of efficiency that defines human progress. This journey delves into the mechanics, applications, and trends shaping the world of wrench technology, highlighting its profound impact on various industries and society as a whole.
This exploration begins by tracing the historical roots of wrench technology, examining how traditional hand tools have evolved into modern power-driven systems. It then dives into the fundamental principles that govern wrench operation, including torque, leverage, and the innovative mechanisms employed in powered wrenches. The diverse applications of wrench technology across industries like automotive, aerospace, manufacturing, and construction will be examined, demonstrating its crucial role in ensuring safety, quality, and productivity.
Wrench Technology
Wrench technology has evolved significantly over time, transforming from simple hand tools to sophisticated powered devices. This evolution has revolutionized various industries, enhancing productivity and efficiency. This article will delve into the history of wrench technology, explore different types of wrenches, and examine their impact on various sectors.
Evolution of Wrench Technology
The evolution of wrench technology can be traced back to ancient times when simple hand tools were used for tightening and loosening nuts and bolts. These early wrenches were often made of wood or metal and were limited in their functionality. The invention of the adjustable wrench in the 19th century marked a significant advancement, allowing for greater versatility and adaptability.
The development of powered wrenches in the 20th century further revolutionized wrench technology. These tools, powered by electricity or compressed air, provided greater torque and speed, significantly increasing productivity and reducing manual labor. The introduction of impact wrenches, capable of delivering high-impact force, further expanded the capabilities of wrench technology, enabling faster and more efficient tightening and loosening of fasteners.
Types of Wrenches and Their Applications
Wrenches can be broadly categorized into two main types: hand wrenches and powered wrenches. Each type encompasses a variety of tools designed for specific applications.
Hand Wrenches
Hand wrenches are manual tools used for tightening and loosening nuts and bolts. They are typically made of metal and come in various sizes and shapes, depending on the size and type of fastener being used. Some common types of hand wrenches include:
- Open-end wrenches: These wrenches have an open end that fits over a nut or bolt head. They are typically used for general-purpose tightening and loosening.
- Box-end wrenches: These wrenches have a closed end that fits over a nut or bolt head. They provide a more secure grip than open-end wrenches and are often used for more demanding applications.
- Combination wrenches: These wrenches combine an open end and a box end, providing versatility for different applications.
- Adjustable wrenches: These wrenches have an adjustable jaw that can be tightened or loosened to fit different sizes of nuts and bolts. They are highly versatile and can be used for a wide range of applications.
- Torque wrenches: These wrenches are designed to apply a specific amount of torque to a fastener, ensuring that it is tightened to the correct specifications. They are often used in critical applications where over-tightening or under-tightening could lead to damage or failure.
Powered Wrenches
Powered wrenches are motorized tools that provide greater torque and speed than hand wrenches. They are often used in industrial and manufacturing settings where efficiency and productivity are paramount. Some common types of powered wrenches include:
- Electric wrenches: These wrenches are powered by electricity and are typically used for applications that require high torque and speed. They are often used in automotive repair, manufacturing, and construction.
- Pneumatic wrenches: These wrenches are powered by compressed air and are typically used for applications that require high torque and speed. They are often used in heavy-duty industries such as construction, mining, and manufacturing.
- Impact wrenches: These wrenches deliver high-impact force to loosen or tighten fasteners. They are often used in applications where traditional wrenches are not effective, such as loosening rusted or seized fasteners.
Impact of Wrench Technology on Productivity and Efficiency
Wrench technology has significantly impacted productivity and efficiency in various sectors. Here are some examples:
Automotive Industry
In the automotive industry, wrench technology has played a crucial role in streamlining vehicle assembly and repair processes. Powered wrenches have enabled faster and more efficient tightening and loosening of fasteners, reducing assembly times and increasing productivity. Impact wrenches have proven particularly useful for loosening rusted or seized fasteners, which can be challenging to remove with traditional hand wrenches.
Construction Industry
Wrench technology has revolutionized construction processes, enabling faster and more efficient assembly of structures. Powered wrenches, particularly impact wrenches, are widely used in construction for tightening and loosening bolts, nuts, and other fasteners. They have significantly reduced manual labor, improved safety, and increased productivity.
Manufacturing Industry
In the manufacturing industry, wrench technology is essential for assembling and repairing machinery and equipment. Powered wrenches are used extensively in manufacturing to tighten and loosen fasteners, ensuring that components are securely assembled and that equipment operates efficiently.
Aerospace Industry
Wrench technology plays a critical role in the aerospace industry, where precision and reliability are paramount. Torque wrenches are used extensively in aerospace applications to ensure that fasteners are tightened to the correct specifications, preventing over-tightening or under-tightening that could compromise structural integrity.
Mechanics and Principles of Wrench Technology
Wrenches are essential tools in various industries, from automotive repair to construction. Their fundamental principle lies in the application of torque and leverage to loosen or tighten fasteners. Understanding these mechanics is crucial for selecting the right wrench for a specific task and ensuring efficient and safe operation.
Torque and Leverage, Wrench technology
Torque, the rotational force applied to an object, is the primary principle behind wrench operation. When a wrench is applied to a nut or bolt, the force exerted on the handle creates a torque that acts on the fastener. This torque is directly proportional to the force applied and the distance from the force application point to the center of the fastener. Leverage, the mechanical advantage gained by using a tool to amplify force, plays a crucial role in wrench operation. By extending the lever arm, the wrench allows a user to exert a greater force on the fastener with less effort. The longer the handle of the wrench, the greater the leverage and the higher the torque applied.
Torque = Force x Distance
Powered Wrench Mechanisms
Powered wrenches offer significant advantages in terms of speed, efficiency, and torque output, especially in heavy-duty applications. They employ various mechanisms to generate the necessary force:
- Pneumatic Wrenches: These wrenches use compressed air to drive a piston, which in turn rotates a drive shaft connected to the wrench head. Pneumatic wrenches are known for their high power output, making them suitable for applications requiring high torque.
- Electric Wrenches: These wrenches utilize an electric motor to generate torque. They offer greater control and precision compared to pneumatic wrenches, making them suitable for delicate applications.
- Hydraulic Wrenches: Hydraulic wrenches use hydraulic fluid pressure to generate force. They are often employed in heavy-duty applications where extremely high torque is required, such as in bridge construction or pipeline work.
Materials Science and Wrench Durability
The choice of materials plays a crucial role in wrench durability and performance.
- Steel: Steel is the most common material used in wrench construction due to its strength, durability, and affordability. Different grades of steel offer varying levels of hardness and resistance to wear and tear.
- Chromium-Molybdenum (Cr-Mo) Steel: Cr-Mo steel is a high-strength alloy commonly used for wrenches requiring exceptional durability and resistance to corrosion. It is often used in professional-grade wrenches designed for heavy-duty applications.
- Titanium: Titanium is a lightweight and corrosion-resistant material that offers excellent strength-to-weight ratio. While more expensive than steel, titanium wrenches are often used in aerospace and other applications where weight reduction is critical.
Applications of Wrench Technology
Wrench technology, encompassing a diverse range of tools and techniques, finds widespread application across various industries. Its fundamental role in securing, assembling, and disassembling components makes it an indispensable element in countless operations, contributing significantly to the efficiency, safety, and quality of manufacturing, construction, and maintenance processes.
Automotive Industry
The automotive industry heavily relies on wrench technology for various tasks, from assembling vehicles to performing routine maintenance.
- Assembly Line Operations: Wrenches are essential for tightening bolts and nuts during the assembly of engines, transmissions, chassis, and other components, ensuring a secure and durable connection between parts.
- Maintenance and Repair: Mechanics use a wide array of wrenches to remove and replace parts during maintenance and repair procedures, enabling them to access and work on various components, such as wheels, brakes, suspension systems, and engine components.
- Torque Specifications: Torque wrenches play a critical role in ensuring the proper tightness of fasteners, preventing over-tightening or under-tightening that could lead to component damage or failure.
Aerospace Industry
The aerospace industry demands exceptional precision and reliability in all aspects of its operations, making wrench technology a vital tool for maintaining the safety and functionality of aircraft.
- Aircraft Assembly: Wrenches are used extensively in the assembly of aircraft components, including the fuselage, wings, and landing gear, ensuring a secure and robust structure.
- Engine Maintenance: Aircraft engines require meticulous maintenance, and wrenches are essential for accessing and replacing components, such as spark plugs, fuel injectors, and turbine blades, ensuring optimal engine performance.
- Safety and Quality Control: Torque wrenches are crucial in aerospace applications, ensuring that fasteners are tightened to precise specifications, preventing potential failures that could compromise the integrity of the aircraft.
Manufacturing Industry
Wrench technology is a fundamental aspect of manufacturing processes, enabling the efficient and precise assembly and repair of a wide range of products.
- Assembly Lines: Wrenches are indispensable for tightening bolts and nuts during the assembly of various products, ensuring a secure and durable connection between components.
- Machinery Maintenance: Wrenches are used for maintenance and repair tasks on various types of machinery, ensuring the smooth operation of production lines and equipment.
- Quality Control: Torque wrenches are employed to ensure that fasteners are tightened to the correct specifications, preventing over-tightening or under-tightening that could lead to product defects or malfunctions.
Construction Industry
Wrench technology plays a crucial role in the construction industry, ensuring the secure and durable assembly of structures and infrastructure.
- Structural Assembly: Wrenches are used to tighten bolts and nuts during the assembly of steel beams, columns, and other structural components, ensuring a stable and robust framework.
- Equipment Maintenance: Wrenches are essential for maintaining construction equipment, such as cranes, excavators, and bulldozers, ensuring their proper functionality and safety.
- Safety and Quality Control: Torque wrenches are employed to ensure that fasteners are tightened to the correct specifications, preventing potential failures that could compromise the structural integrity of buildings and infrastructure.
Trends and Innovations in Wrench Technology
The field of wrench technology is constantly evolving, driven by the need for greater efficiency, precision, and safety in various industries. From the traditional hand wrench to sophisticated automated tightening systems, wrench technology has come a long way. Emerging trends are shaping the future of this technology, promising significant advancements in both design and functionality.
Smart Wrenches and Automated Tightening Systems
The development of smart wrenches and automated tightening systems represents a significant shift in wrench technology. These systems integrate sensors, data processing capabilities, and communication technologies, allowing for real-time monitoring, data collection, and control of tightening processes.
- Real-time Torque Monitoring and Control: Smart wrenches incorporate sensors to monitor and control the applied torque during fastening. This enables precise control over tightening processes, ensuring optimal fastener tension and preventing over-tightening or under-tightening.
- Data Logging and Analysis: Smart wrenches can record data related to torque, angle, and time during tightening processes. This data can be analyzed to identify trends, optimize tightening procedures, and ensure consistent quality.
- Remote Monitoring and Control: Automated tightening systems allow for remote monitoring and control of tightening processes. This enables operators to track progress, adjust parameters, and intervene in real-time, enhancing efficiency and safety.
Challenges and Opportunities for Future Innovations
The evolution of wrench technology is not without its challenges. However, these challenges also present opportunities for innovation and advancement.
- Integration with Existing Systems: Integrating smart wrenches and automated tightening systems with existing manufacturing and assembly lines can be complex. Developers must ensure seamless compatibility and integration with existing equipment and software.
- Cybersecurity: As smart wrenches become increasingly connected, cybersecurity concerns arise. Ensuring data security and protecting against unauthorized access is crucial for maintaining system integrity and preventing potential disruptions.
- Cost Considerations: Implementing smart wrench and automated tightening systems can involve significant upfront costs. Balancing cost-effectiveness with the benefits of advanced technology is essential for widespread adoption.
Innovative Wrench Designs
Several innovative wrench designs have emerged in recent years, addressing specific challenges and offering enhanced functionalities.
- Torque-Limiting Wrenches: These wrenches incorporate a mechanism that prevents over-tightening, ensuring consistent fastener tension and minimizing the risk of damage.
- Ergonomic Wrenches: Ergonomic designs focus on improving user comfort and reducing strain on the hands and wrists. This is particularly important in applications involving repetitive tightening tasks.
- Multi-Purpose Wrenches: Some wrenches are designed to accommodate a wide range of fastener sizes and shapes, reducing the need for multiple tools.
Impact of Wrench Technology on Society
Wrench technology, encompassing tools, techniques, and principles, has had a profound impact on society, shaping industries, influencing work practices, and contributing to overall societal progress. This section delves into the various ways wrench technology has impacted worker safety and ergonomics, boosted productivity and efficiency, and promoted sustainability and environmental protection.
Impact on Worker Safety and Ergonomics
Wrench technology has significantly improved worker safety and ergonomics in various industries. The development of specialized wrenches, ergonomic handles, and torque-limiting tools has minimized the risk of injuries associated with manual tightening and loosening of fasteners.
- Ergonomic Design: Wrenches with ergonomic handles and grips reduce strain on wrists, hands, and forearms, promoting comfortable and safe use. These designs incorporate features like cushioned grips, angled handles, and balanced weight distribution, reducing fatigue and the risk of repetitive strain injuries.
- Torque Control: Torque-limiting wrenches ensure consistent and accurate tightening of fasteners, preventing over-tightening that can lead to damage to materials and potential injuries. These tools often feature adjustable torque settings, allowing users to tailor the force applied to specific applications.
- Safety Features: Some wrenches incorporate safety features such as breakaway mechanisms or overload protection, which prevent excessive force from being applied, safeguarding both the worker and the equipment.
The adoption of these technologies has led to a reduction in workplace injuries, improved worker productivity, and a safer working environment.
Economic Impact of Wrench Technology
Wrench technology has significantly impacted economic productivity and efficiency across various industries.
- Increased Productivity: Specialized wrenches, such as impact wrenches and torque wrenches, have dramatically increased productivity in assembly and manufacturing processes. These tools allow for faster and more efficient tightening and loosening of fasteners, reducing assembly time and improving overall output.
- Reduced Costs: Wrench technology has also contributed to cost reduction through minimized material waste and reduced downtime. Precise torque control prevents over-tightening, reducing the risk of fastener damage and component failure, minimizing the need for rework and replacement.
- Improved Quality: The use of torque-limiting wrenches ensures consistent tightening of fasteners, leading to improved product quality and reliability. This, in turn, reduces the incidence of defects and warranty claims, further contributing to cost savings.
The economic benefits of wrench technology have been substantial, driving growth and innovation in various industries.
Role of Wrench Technology in Sustainability and Environmental Protection
Wrench technology has also played a significant role in promoting sustainability and environmental protection.
- Reduced Waste: Precise torque control minimizes over-tightening, reducing the risk of fastener damage and component failure. This reduces the need for replacement parts and minimizes material waste, contributing to a more sustainable manufacturing process.
- Energy Efficiency: Wrench technology has led to the development of energy-efficient tools, such as cordless impact wrenches, reducing reliance on fossil fuels and minimizing carbon emissions.
- Resource Conservation: Wrench technology has facilitated the use of lightweight and durable materials in manufacturing, reducing the overall resource consumption and promoting a more sustainable approach to production.
By reducing waste, conserving resources, and promoting energy efficiency, wrench technology has contributed to a more sustainable and environmentally responsible approach to manufacturing and other industries.
Closure
As we conclude our journey through the fascinating world of wrench technology, it becomes evident that this seemingly simple tool has played a pivotal role in shaping modern society. From enhancing worker safety and ergonomics to driving economic growth and fostering sustainability, wrench technology continues to evolve, promising even greater innovations and impacts in the years to come. The future of wrench technology is brimming with possibilities, fueled by the relentless pursuit of efficiency, precision, and smart solutions. As we embrace these advancements, we can anticipate a future where wrench technology plays an even more integral role in shaping the world around us.
Wrench technology, like many fields, has seen advancements in efficiency and precision. From torque-sensing wrenches to automated assembly lines, the tools we use are constantly evolving. A similar evolution can be seen in lighting technology, with companies like FX Technology Co.
Ltd leading the way with their energy-efficient and long-lasting LED lights. This shift towards sustainability and innovation mirrors the drive in wrench technology to create tools that are more reliable and environmentally conscious.