SPC Technologies: A Guide to Process Control
SPC Technologies, the cornerstone of modern manufacturing and quality assurance, empowers businesses to achieve unparalleled levels of efficiency and precision. By leveraging statistical methods and data analysis, SPC technologies enable […]
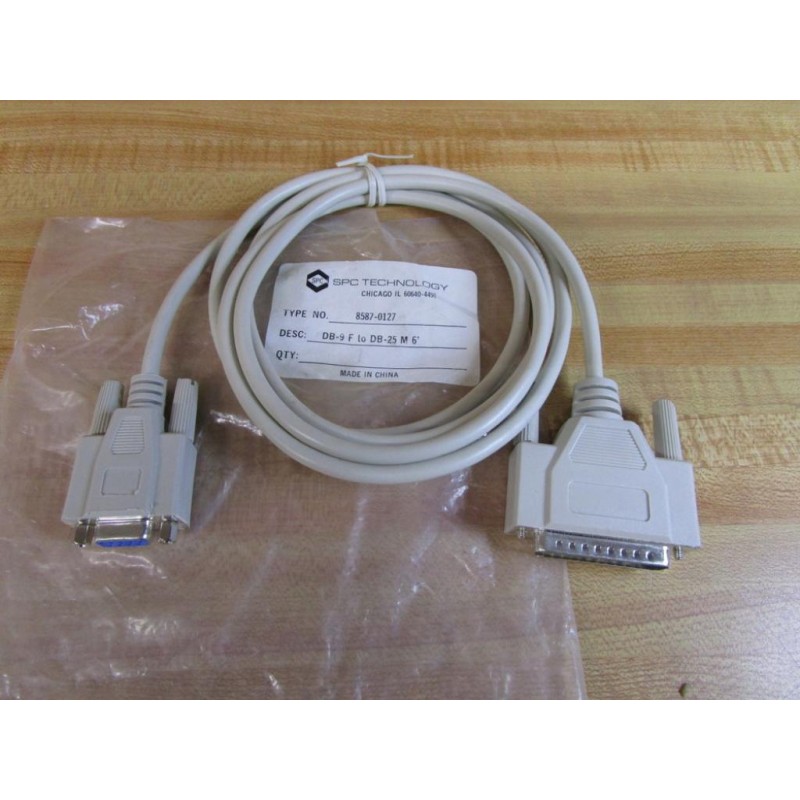
SPC Technologies, the cornerstone of modern manufacturing and quality assurance, empowers businesses to achieve unparalleled levels of efficiency and precision. By leveraging statistical methods and data analysis, SPC technologies enable companies to identify and eliminate sources of variation in their processes, ultimately leading to consistent product quality and improved operational performance.
This comprehensive guide delves into the world of SPC technologies, exploring their history, diverse applications, and the transformative impact they have on various industries. From the fundamental principles to the latest advancements, we will examine how SPC technologies are shaping the future of manufacturing and driving innovation across the globe.
SPC Technologies
SPC technologies, or Statistical Process Control technologies, are a collection of tools and techniques used to monitor and control the variation in a process. The primary goal of SPC is to identify and eliminate sources of variation that lead to defects, inconsistencies, and inefficiencies in a process.
Historical Overview of SPC Technologies
The development of SPC technologies can be traced back to the early 20th century. Key milestones include:
- 1920s: Walter A. Shewhart, a statistician at Bell Labs, introduced the concept of statistical control charts. These charts helped visualize process variation and identify when a process was out of control.
- 1930s: W. Edwards Deming, an American statistician, popularized the use of statistical methods for quality control in manufacturing. He emphasized the importance of reducing variation in processes to improve quality and productivity.
- 1950s: The development of the computer enabled the automation of SPC processes. Statistical software packages emerged, making it easier to analyze data and generate control charts.
- 1980s: The rise of total quality management (TQM) and the focus on continuous improvement further increased the adoption of SPC technologies in various industries.
Fundamental Principles and Methodologies of SPC Technologies
SPC technologies are based on the following fundamental principles:
- Variation is inherent in all processes: No process can be perfectly consistent. There will always be some degree of variation in the output.
- Variation can be measured and controlled: SPC tools and techniques allow us to measure the variation in a process and identify the sources of that variation. By understanding the sources of variation, we can take steps to control them.
- Control charts are used to monitor process variation: Control charts are graphical tools that display data over time. They help us to determine if a process is in statistical control or if it is exhibiting unusual variation.
- The process must be in statistical control before improvements can be made: Before we can improve a process, we need to ensure that it is stable and predictable. This means that the variation in the process is under control.
SPC Methodologies
SPC methodologies involve a variety of tools and techniques, including:
- Control charts: Control charts are used to monitor process variation over time. They are typically used to track key process parameters, such as the average, range, or standard deviation.
- X-bar and R charts: Used to monitor the average and range of a process.
- p charts: Used to monitor the proportion of defective items in a process.
- c charts: Used to monitor the number of defects in a sample.
- Process capability analysis: This analysis helps to determine if a process is capable of meeting the specified requirements. It involves measuring the process variation and comparing it to the tolerance limits.
- Root cause analysis: This is a structured approach to identifying the underlying causes of problems in a process.
- Design of experiments (DOE): DOE is a powerful tool for optimizing processes. It involves systematically changing the input variables to a process and observing the effect on the output.
Types of SPC Technologies
SPC technologies are a vital part of modern manufacturing and process improvement efforts. They provide a framework for monitoring, analyzing, and controlling processes to achieve desired outcomes. This section explores various types of SPC technologies and their applications, benefits, and limitations.
Statistical Process Control Charts
Statistical Process Control (SPC) charts are visual tools that help monitor process variation over time. They plot data points representing measurements taken from a process, typically against the process’s upper and lower control limits. These limits are calculated based on historical data and represent the expected range of variation for a stable process.
SPC charts can be used to:
- Identify trends and patterns in process data.
- Detect special causes of variation that may indicate problems.
- Monitor process performance and identify areas for improvement.
- Demonstrate process capability and consistency.
Common types of SPC charts include:
- X-bar and R charts: Used to monitor the average and range of a process.
- X-bar and S charts: Used to monitor the average and standard deviation of a process.
- p charts: Used to monitor the proportion of defective items in a sample.
- c charts: Used to monitor the number of defects in a sample.
- u charts: Used to monitor the average number of defects per unit.
SPC charts are effective in identifying trends and patterns in process data, enabling proactive problem-solving and continuous improvement.
Statistical Software
Statistical software packages provide powerful tools for analyzing and interpreting data, including SPC data. These software packages can perform various statistical analyses, such as:
- Descriptive statistics: Calculate measures of central tendency and dispersion.
- Hypothesis testing: Test hypotheses about process parameters.
- Regression analysis: Identify relationships between variables.
- ANOVA: Analyze the differences between group means.
- SPC charting: Create and analyze various SPC charts.
Some popular statistical software packages include:
- Minitab: A widely used software package for SPC and other statistical analysis.
- JMP: A comprehensive statistical software package with strong visualization capabilities.
- R: A free and open-source statistical programming language.
- SPSS: A powerful statistical software package used for social science research.
Statistical software packages provide advanced tools for analyzing SPC data, facilitating data-driven decision-making and process optimization.
Data Acquisition Systems
Data acquisition systems (DAS) are essential for collecting and recording process data for SPC analysis. These systems can be hardware or software-based and typically consist of:
- Sensors: Devices that measure process variables, such as temperature, pressure, or flow rate.
- Data loggers: Devices that store and record sensor data.
- Software: Programs that manage data acquisition and communication.
DAS can be integrated with SPC software packages, allowing for real-time data monitoring and analysis. They provide a continuous stream of data, enabling more frequent and accurate process monitoring and control.
DAS play a crucial role in SPC by providing the necessary data for analysis and monitoring, facilitating timely intervention and process improvement.
Process Automation Systems
Process automation systems are used to control and adjust process parameters automatically based on real-time data. They can be integrated with SPC systems to:
- Adjust process settings: Automatically adjust parameters based on SPC chart signals.
- Prevent defects: Trigger alarms or corrective actions when process deviations occur.
- Improve efficiency: Optimize process performance by minimizing variation and waste.
Examples of process automation systems include:
- PLC (Programmable Logic Controllers): Used for controlling industrial processes.
- SCADA (Supervisory Control and Data Acquisition): Used for monitoring and controlling large-scale systems.
Process automation systems, integrated with SPC, can significantly enhance process control and efficiency, reducing human error and improving overall process performance.
Applications of SPC Technologies
Statistical Process Control (SPC) technologies have found widespread applications across diverse industries, revolutionizing manufacturing processes and driving improvements in quality, efficiency, and productivity. These technologies empower organizations to identify and address potential issues proactively, ultimately leading to enhanced customer satisfaction and competitive advantage.
Manufacturing
SPC technologies are indispensable in manufacturing, where consistent quality and efficient production are paramount. They are used extensively to monitor and control various processes, including:
- Process Monitoring: SPC charts, such as X-bar and R charts, are employed to track key process parameters over time, enabling manufacturers to identify trends, deviations, and potential issues before they escalate. This proactive approach allows for timely adjustments to prevent defects and ensure consistent product quality.
- Process Optimization: SPC analysis helps manufacturers understand the sources of variability in their processes and identify areas for improvement. By analyzing data, they can pinpoint factors that contribute to defects and implement targeted interventions to reduce variation and enhance process stability.
- Quality Control: SPC plays a crucial role in maintaining product quality by setting up control limits based on historical data. When process measurements fall outside these limits, it signals a potential issue requiring investigation and corrective action. This ensures that products meet predefined quality standards and customer expectations.
Healthcare
In healthcare, SPC technologies are increasingly employed to improve patient safety, enhance operational efficiency, and optimize resource allocation. Examples of their application include:
- Monitoring Patient Outcomes: SPC charts can be used to track critical patient parameters, such as blood pressure, heart rate, and medication adherence, enabling healthcare professionals to identify early signs of complications and intervene promptly.
- Improving Healthcare Processes: SPC methodologies can be applied to analyze and improve processes like patient wait times, medication dispensing, and surgical procedures. By identifying bottlenecks and areas for improvement, healthcare organizations can enhance efficiency and reduce errors.
- Ensuring Medical Device Safety: SPC is used in the manufacturing of medical devices to ensure their reliability and safety. By monitoring critical production parameters, manufacturers can identify potential defects and prevent the release of faulty devices, safeguarding patient health.
Finance
SPC technologies are employed in finance to manage risk, improve forecasting accuracy, and optimize resource allocation. Their applications include:
- Risk Management: SPC charts can be used to monitor key financial metrics, such as credit risk, market volatility, and investment performance, enabling financial institutions to identify and mitigate potential risks proactively.
- Forecasting and Planning: SPC analysis can be used to improve the accuracy of financial forecasts and predictions by identifying trends and patterns in historical data. This allows organizations to make informed decisions about investments, budgeting, and resource allocation.
- Fraud Detection: SPC can be employed to detect anomalies in financial transactions, such as unusual spending patterns or suspicious account activity, which can be indicative of fraud. This helps financial institutions protect themselves from financial losses and maintain customer trust.
Benefits and Challenges of SPC Technologies
SPC technologies offer a range of advantages for businesses across various sectors. However, implementing these technologies also comes with certain challenges and limitations. This section delves into the benefits, challenges, and cost-benefit analysis of adopting SPC technologies.
Advantages of SPC Technologies
The advantages of adopting and utilizing SPC technologies are numerous, contributing to improved efficiency, productivity, and overall business performance.
- Enhanced Quality Control: SPC technologies provide real-time data and insights into production processes, enabling early detection of deviations from quality standards. This proactive approach allows for timely corrective actions, minimizing defects and ensuring consistent product quality.
- Increased Productivity: By identifying and eliminating process inefficiencies, SPC technologies optimize production workflows. This leads to faster production cycles, reduced downtime, and ultimately, increased productivity.
- Reduced Costs: SPC technologies help minimize waste, rework, and scrap by preventing defects early on. This translates to significant cost savings in the long run, as businesses can reduce material consumption and labor costs.
- Improved Decision-Making: SPC technologies provide data-driven insights that support informed decision-making. This allows businesses to make strategic choices regarding process adjustments, resource allocation, and quality improvements.
- Enhanced Customer Satisfaction: Consistent product quality and timely delivery are crucial for customer satisfaction. SPC technologies ensure these aspects, leading to increased customer loyalty and positive brand perception.
Challenges of Implementing SPC Technologies
While the benefits of SPC technologies are undeniable, implementing them effectively can pose certain challenges.
- Initial Investment Costs: Implementing SPC technologies often involves significant upfront investments in hardware, software, and training. This can be a barrier for small and medium-sized enterprises with limited budgets.
- Data Management and Analysis: SPC technologies generate vast amounts of data that require sophisticated data management and analysis capabilities. This can be challenging for businesses without the necessary expertise or infrastructure.
- Process Integration: Integrating SPC technologies into existing production processes can be complex and time-consuming. This requires careful planning, coordination, and collaboration among different departments.
- Resistance to Change: Some employees may resist the adoption of new technologies due to concerns about job security or the learning curve associated with new tools and processes. Effective communication and training programs are essential to overcome this resistance.
- Lack of Standardization: The absence of industry-wide standards for SPC data collection and analysis can create challenges in data sharing and interoperability between different systems.
Cost-Benefit Analysis of Investing in SPC Technologies
The cost-benefit analysis of investing in SPC technologies should consider both the initial investment costs and the potential long-term benefits.
- Quantifying Benefits: To determine the return on investment (ROI), businesses need to quantify the potential benefits of SPC technologies, such as reduced defect rates, increased productivity, and cost savings.
- Evaluating ROI: By comparing the estimated benefits with the initial investment costs, businesses can assess the financial viability of adopting SPC technologies. This analysis should also consider factors like the time it takes to realize the benefits.
- Long-Term Perspective: The cost-benefit analysis should adopt a long-term perspective, considering the sustained benefits of SPC technologies over time. For example, continuous quality improvement and reduced operational costs can lead to significant long-term gains.
- Case Studies and Industry Benchmarks: Examining case studies and industry benchmarks can provide valuable insights into the real-world impact of SPC technologies. This can help businesses make informed decisions based on actual data and experience.
Future Trends and Developments in SPC Technologies
SPC technologies are constantly evolving, driven by advancements in computing power, sensor technology, and data analytics. This evolution is leading to new capabilities and applications that are transforming various industries.
Advancements in Sensor Technology
The development of more sophisticated and miniaturized sensors is playing a crucial role in the advancement of SPC technologies. These sensors can now collect a wider range of data with higher accuracy and at faster rates. For instance, the use of MEMS (Micro-Electro-Mechanical Systems) sensors in manufacturing processes enables real-time monitoring of critical parameters like temperature, pressure, and vibration, providing valuable insights for process optimization and defect prevention.
Integration with Artificial Intelligence and Machine Learning
The integration of AI and ML algorithms into SPC systems is revolutionizing the way data is analyzed and interpreted. AI-powered systems can identify patterns and anomalies in real-time, predict potential problems before they occur, and even automate adjustments to processes to maintain optimal performance. This is particularly beneficial for complex manufacturing processes where human intervention is limited or impractical. For example, AI-driven SPC systems can be used to predict tool wear in CNC machines, allowing for proactive maintenance and reducing downtime.
Cloud-Based SPC Platforms
Cloud-based SPC platforms are gaining popularity due to their scalability, accessibility, and cost-effectiveness. These platforms enable companies to store and analyze large datasets from multiple sources, facilitating collaboration and data sharing across different departments and locations. This allows for a more holistic view of the production process and enables informed decision-making based on real-time data. Cloud-based SPC platforms also offer the advantage of being easily integrated with other business systems, such as ERP and CRM, providing a comprehensive view of operations.
Real-Time Data Analytics and Predictive Maintenance, Spc technologies
Real-time data analytics is becoming increasingly important in SPC, enabling businesses to identify and address issues as they occur. This allows for faster corrective actions, reducing downtime and improving overall efficiency. Predictive maintenance is another emerging trend, leveraging data analysis to predict potential equipment failures and schedule maintenance before they occur. This approach minimizes downtime, reduces maintenance costs, and improves overall equipment reliability.
The Role of Research and Development
Research and development play a critical role in shaping the future of SPC technologies. Ongoing research focuses on developing new sensor technologies, refining AI algorithms, and exploring novel applications for SPC. For example, research in the field of machine learning is exploring the development of deep learning models that can learn complex patterns in data, leading to more accurate predictions and insights. These advancements will continue to drive innovation in SPC and enable businesses to achieve greater efficiency and productivity.
Epilogue
As we conclude our exploration of SPC technologies, it becomes evident that their role in achieving operational excellence is undeniable. By embracing SPC principles and implementing these technologies, businesses can unlock significant benefits, including reduced waste, improved product quality, enhanced customer satisfaction, and a competitive edge in the marketplace. The future of SPC technologies holds immense promise, with ongoing research and development continually pushing the boundaries of what is possible. As the world becomes increasingly data-driven, SPC technologies will play an increasingly vital role in shaping the future of manufacturing and driving innovation across all industries.
SPC technologies are becoming increasingly popular for their durability and versatility. They’re often used in commercial and industrial settings, but residential applications are growing too. One company that specializes in SPC flooring is nestor technologies inc , offering a wide range of styles and finishes.
Whether you’re looking for a classic wood look or a modern, sleek design, SPC technologies offer a durable and stylish solution for your flooring needs.