Preconstruction Technology: Shaping Modern Construction
Preconstruction technology is revolutionizing the construction industry, transforming traditional methods into a data-driven, efficient, and collaborative process. This innovative approach encompasses a range of technologies and tools that enable construction […]
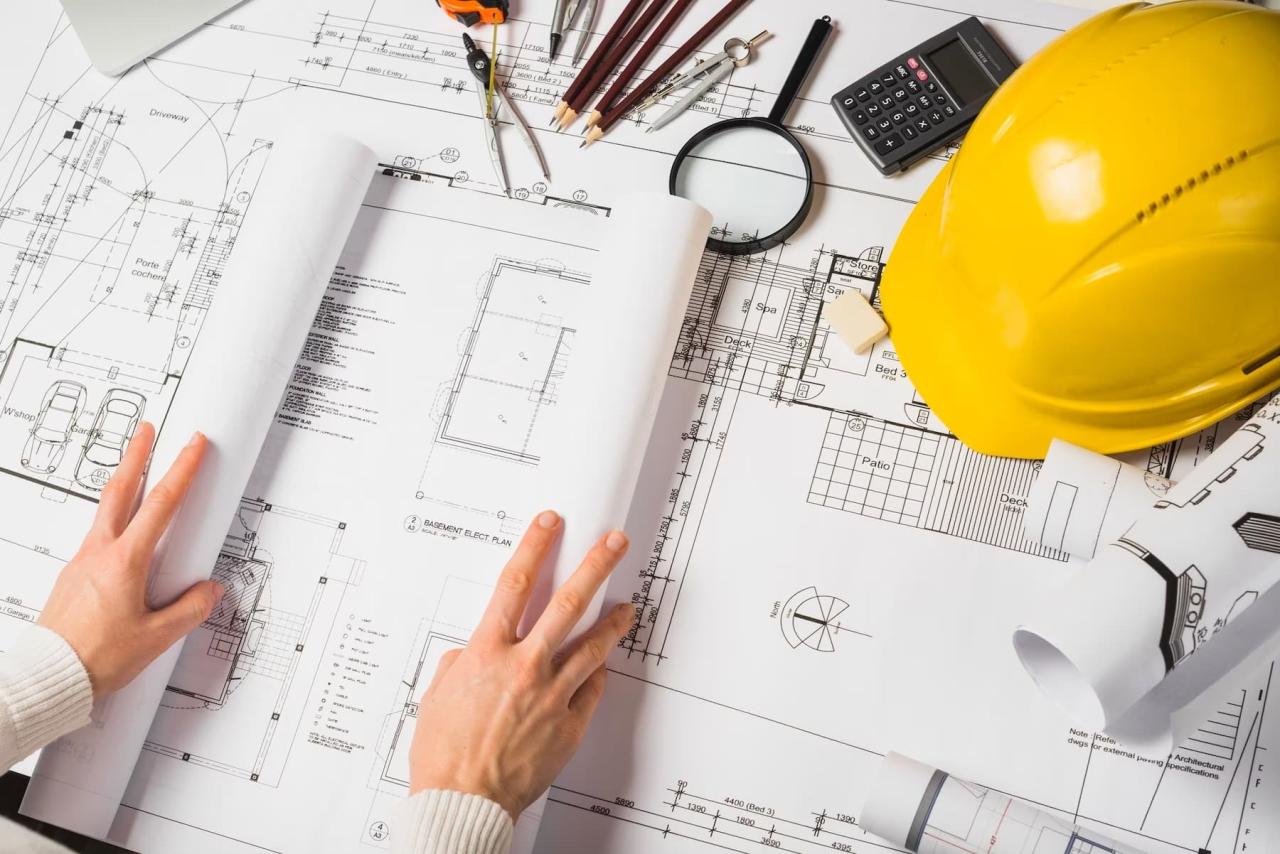
Preconstruction technology is revolutionizing the construction industry, transforming traditional methods into a data-driven, efficient, and collaborative process. This innovative approach encompasses a range of technologies and tools that enable construction professionals to plan, design, estimate costs, and manage risks with unprecedented accuracy and speed.
From Building Information Modeling (BIM) to Virtual Reality (VR) and Augmented Reality (AR), preconstruction technology empowers stakeholders to visualize projects in detail, identify potential issues early on, and optimize project outcomes. The adoption of these technologies is transforming the way construction projects are conceived, planned, and executed, paving the way for a future of smarter, more sustainable, and cost-effective construction.
Definition and Scope of Preconstruction Technology
Preconstruction technology is a vital element in the modern construction industry, revolutionizing traditional methods and enhancing efficiency, accuracy, and overall project success. It encompasses a range of digital tools and processes that are employed during the preconstruction phase, which is the critical period before actual construction commences.
Preconstruction technology plays a crucial role in transforming the way construction projects are planned, designed, and executed, ultimately leading to better outcomes.
Key Areas of Application
Preconstruction technology is implemented across various stages of the construction lifecycle, contributing to a more informed and efficient approach.
- Planning: Preconstruction technology facilitates comprehensive project planning by enabling the creation of detailed 3D models, virtual site walkthroughs, and simulations. These tools allow stakeholders to visualize the project’s scope, identify potential challenges, and optimize the construction process.
- Design: Preconstruction technology empowers architects and engineers to create highly detailed and accurate designs using Building Information Modeling (BIM). BIM software enables the creation of intelligent 3D models that contain comprehensive data about the project, including materials, dimensions, and specifications. This data can be used for design coordination, clash detection, and analysis.
- Cost Estimation: Preconstruction technology significantly improves cost estimation accuracy. By leveraging BIM data, software tools can generate detailed cost breakdowns based on material quantities, labor requirements, and other factors. This helps in creating realistic budgets, minimizing cost overruns, and making informed financial decisions.
- Risk Management: Preconstruction technology enables proactive risk identification and mitigation. By analyzing data from BIM models, simulations, and historical project data, construction teams can identify potential risks, assess their impact, and develop strategies to minimize their likelihood and consequences. This helps in reducing project delays, accidents, and financial losses.
Benefits of Implementing Preconstruction Technology
The adoption of preconstruction technology offers numerous benefits for construction projects, leading to improved efficiency, reduced costs, and enhanced project outcomes.
- Enhanced Collaboration: Preconstruction technology facilitates seamless collaboration among stakeholders, including architects, engineers, contractors, and owners. By sharing digital models and data, all parties involved have access to the same information, promoting better communication, coordination, and decision-making.
- Reduced Errors and Waste: Preconstruction technology helps minimize errors and waste by providing accurate data and simulations. Clash detection tools identify potential conflicts between different elements of the design, preventing costly rework and material waste. This contributes to a more efficient and sustainable construction process.
- Improved Project Scheduling: Preconstruction technology enables the creation of detailed schedules and timelines based on accurate data and simulations. This allows construction teams to plan and manage the project effectively, reducing delays and ensuring on-time completion.
- Enhanced Safety: Preconstruction technology contributes to a safer construction environment. By identifying potential hazards through simulations and virtual walkthroughs, teams can implement preventive measures and train workers on safety protocols, minimizing the risk of accidents and injuries.
- Increased Profitability: By optimizing project planning, design, and execution, preconstruction technology helps reduce costs, improve efficiency, and minimize risks. This leads to increased profitability for construction projects, ensuring a more sustainable and successful business model.
Key Technologies and Tools: Preconstruction Technology
Preconstruction technology relies on a diverse range of tools and technologies to optimize the design, planning, and execution of construction projects. These technologies enhance communication, collaboration, and efficiency throughout the project lifecycle.
Building Information Modeling (BIM)
BIM is a digital representation of a construction project, encompassing its physical and functional characteristics. BIM software creates a comprehensive 3D model that integrates various project data, including architectural plans, structural details, MEP systems, and cost estimates.
Functionalities and Applications
- Design Coordination: BIM facilitates seamless collaboration among architects, engineers, and contractors, enabling early detection and resolution of clashes and interferences.
- Cost Estimation and Budgeting: By integrating cost data with the 3D model, BIM enables accurate cost estimation and budgeting, allowing for informed decision-making.
- Construction Planning and Sequencing: BIM facilitates the development of detailed construction plans, including sequencing, scheduling, and resource allocation.
- Virtual Construction and Simulation: BIM enables virtual construction simulations, allowing stakeholders to visualize the project and identify potential challenges before construction begins.
- Facility Management: BIM data can be utilized for facility management purposes, providing insights into building performance, maintenance needs, and operational efficiency.
Advantages and Disadvantages
- Advantages:
- Improved communication and collaboration among project stakeholders.
- Enhanced design coordination and clash detection.
- Accurate cost estimation and budgeting.
- Optimized construction planning and scheduling.
- Reduced risk and potential for errors.
- Increased productivity and efficiency.
- Disadvantages:
- High initial investment in software and training.
- Complexity of BIM software and workflows.
- Requirement for skilled BIM professionals.
- Potential for data management challenges.
Virtual Reality (VR) and Augmented Reality (AR)
VR and AR technologies are transforming the preconstruction process by providing immersive and interactive experiences. VR immerses users in a simulated environment, while AR overlays digital information onto the real world.
Functionalities and Applications
- Design Visualization and Review: VR and AR enable stakeholders to experience the project in a realistic 3D environment, facilitating design review and feedback.
- Construction Planning and Simulation: VR and AR can simulate construction processes, allowing for identification of potential challenges and optimization of workflows.
- Site Visualization and Navigation: AR can overlay digital information onto the construction site, providing real-time guidance and insights for workers.
- Client Engagement and Marketing: VR and AR can enhance client engagement by providing immersive experiences that showcase the final project.
Advantages and Disadvantages
- Advantages:
- Improved design visualization and stakeholder engagement.
- Enhanced construction planning and risk assessment.
- Reduced potential for errors and rework.
- Increased client satisfaction and project buy-in.
- Disadvantages:
- High cost of VR and AR equipment and software.
- Requirement for specialized expertise and training.
- Limited availability of high-quality VR and AR content.
- Potential for user discomfort or motion sickness.
Laser Scanning and 3D Modeling
Laser scanning technology captures accurate 3D measurements of existing structures and environments. This data is then used to create detailed 3D models that provide a comprehensive representation of the site.
Functionalities and Applications
- Site As-Built Documentation: Laser scanning provides accurate as-built documentation, capturing existing conditions for design and construction purposes.
- Clash Detection and Coordination: 3D models created from laser scan data enable the detection and resolution of clashes between existing structures and proposed designs.
- Quantity Takeoff and Cost Estimation: Laser scanning data can be used to generate accurate quantity takeoffs, facilitating cost estimation and budgeting.
- Heritage Preservation and Restoration: Laser scanning plays a crucial role in documenting and preserving historical structures and artifacts.
Advantages and Disadvantages
- Advantages:
- Highly accurate and detailed 3D representation of existing conditions.
- Enhanced design coordination and clash detection.
- Accurate quantity takeoffs and cost estimation.
- Reduced risk of errors and rework.
- Disadvantages:
- High cost of laser scanning equipment and software.
- Requirement for skilled professionals to operate the equipment.
- Potential for data processing challenges.
- Limited accessibility to certain areas due to equipment limitations.
Construction Management Software
Construction management software provides a centralized platform for managing all aspects of a construction project, from planning and scheduling to cost control and communication.
Functionalities and Applications
- Project Planning and Scheduling: Construction management software facilitates the development and management of project schedules, including task assignments, deadlines, and resource allocation.
- Cost Control and Budgeting: Software enables tracking of project expenses, comparing actual costs to budget, and identifying potential cost overruns.
- Communication and Collaboration: Construction management software provides tools for communication and collaboration among project stakeholders, including document sharing, task assignments, and progress updates.
- Risk Management and Issue Tracking: Software allows for the identification and mitigation of project risks, as well as tracking and resolution of issues.
- Document Management and Reporting: Construction management software provides a centralized repository for project documents, enabling easy access and retrieval.
Advantages and Disadvantages
- Advantages:
- Improved project planning, scheduling, and coordination.
- Enhanced cost control and budget management.
- Effective communication and collaboration among stakeholders.
- Real-time project tracking and reporting.
- Increased efficiency and productivity.
- Disadvantages:
- High cost of software licenses and implementation.
- Requirement for user training and adoption.
- Potential for data security and privacy concerns.
- Limited integration with other software systems.
Data Analytics and Machine Learning
Data analytics and machine learning techniques are increasingly being applied in preconstruction to extract valuable insights from project data. This data can be used to optimize design, planning, and execution decisions.
Functionalities and Applications
- Predictive Analytics: Machine learning algorithms can analyze historical project data to predict potential delays, cost overruns, and other risks.
- Resource Optimization: Data analytics can help optimize resource allocation, scheduling, and material procurement based on historical data and real-time insights.
- Construction Risk Management: Machine learning models can identify and assess construction risks, enabling proactive mitigation strategies.
- Quality Control and Monitoring: Data analytics can be used to monitor construction progress, identify potential quality issues, and ensure compliance with standards.
Advantages and Disadvantages
- Advantages:
- Improved project forecasting and risk management.
- Optimized resource allocation and scheduling.
- Enhanced quality control and monitoring.
- Data-driven decision-making.
- Disadvantages:
- Requirement for skilled data scientists and analysts.
- Potential for data bias and inaccurate predictions.
- High cost of data collection, storage, and analysis.
- Limited availability of relevant historical data.
Applications of Preconstruction Technology
Preconstruction technology is not just about using fancy software; it’s about using these tools to make the entire construction process more efficient, cost-effective, and less prone to errors. It’s about leveraging technology to make informed decisions throughout the project lifecycle, from the initial planning stages to the final handover.
Planning and Feasibility Studies
Preconstruction technology plays a crucial role in determining the viability of a project before any significant investments are made. This phase involves gathering data, analyzing potential risks, and evaluating the project’s feasibility.
- Building Information Modeling (BIM): BIM allows architects and engineers to create detailed 3D models of the proposed structure. This digital representation helps in visualizing the design, identifying potential clashes, and assessing the project’s overall feasibility. For example, a BIM model can be used to analyze the building’s energy efficiency, ensuring compliance with sustainability standards.
- Geographic Information Systems (GIS): GIS technology helps analyze the site’s topography, soil conditions, and existing infrastructure. This information is crucial for planning the project’s layout, determining the best access routes, and identifying potential environmental impacts. For example, GIS can be used to map out the location of utilities, minimizing the risk of damage during construction.
- Site Analysis Software: These tools help analyze site conditions, including sun exposure, wind patterns, and noise levels. This data is essential for optimizing the building’s design and ensuring its functionality. For instance, site analysis software can help determine the best location for windows to maximize natural light and minimize heat gain.
Design and Engineering
Preconstruction technology empowers designers and engineers to create more efficient and sustainable designs while minimizing errors and rework.
- BIM: BIM facilitates collaboration between different disciplines, including architects, engineers, and contractors. This real-time data sharing ensures everyone is working from the same blueprint, minimizing conflicts and costly rework. For example, BIM can be used to coordinate the placement of mechanical, electrical, and plumbing systems, ensuring they fit seamlessly within the building’s structure.
- Computer-Aided Design (CAD): CAD software allows architects and engineers to create detailed drawings and specifications. This technology facilitates precise design communication and ensures all stakeholders are working from the same set of blueprints. For instance, CAD can be used to generate shop drawings for specific building components, ensuring they are manufactured to the exact specifications.
- Virtual Reality (VR): VR technology allows stakeholders to experience the building virtually, providing an immersive understanding of the design. This enables early identification of potential issues and allows for adjustments before construction begins. For example, VR can be used to simulate the building’s interior spaces, helping clients visualize the finished product and make informed decisions about design elements.
Cost Estimation and Budgeting
Preconstruction technology provides accurate and detailed cost estimates, enabling better budget planning and risk management.
- BIM: BIM models can be used to generate detailed cost estimates by automatically calculating the quantity of materials needed for each building component. This data can be used to create accurate budgets and track expenses throughout the project lifecycle. For instance, BIM can help estimate the cost of concrete, steel, and other materials, providing a comprehensive breakdown of project expenses.
- Cost Estimation Software: These specialized tools analyze historical data and current market conditions to generate accurate cost estimates for different project elements. This information helps in making informed decisions about materials, labor, and other project expenses. For example, cost estimation software can be used to predict the cost of labor based on local market rates and the project’s complexity.
- Data Analytics: Data analytics tools analyze historical construction data to identify trends and patterns in project costs. This information helps predict future expenses and develop more accurate budgets. For example, data analytics can be used to identify the factors that contribute to cost overruns and develop strategies to mitigate them.
Risk Assessment and Mitigation
Preconstruction technology empowers project teams to proactively identify and manage potential risks, minimizing delays and cost overruns.
- BIM: BIM models can be used to conduct virtual site walks, identifying potential hazards and safety concerns. This allows for early mitigation strategies and reduces the risk of accidents during construction. For example, BIM can be used to identify areas where workers might be exposed to fall hazards and implement safety protocols like scaffolding or fall arrest systems.
- Risk Assessment Software: These tools help identify and analyze potential risks, including weather delays, material shortages, and labor issues. This data allows for the development of mitigation plans and contingency strategies. For example, risk assessment software can be used to identify the probability of a weather delay and develop alternative construction schedules.
- Predictive Analytics: Predictive analytics uses historical data and machine learning algorithms to forecast potential risks and predict their impact on the project. This allows for proactive risk management and helps allocate resources efficiently. For example, predictive analytics can be used to forecast potential labor shortages and develop strategies for recruiting and retaining skilled workers.
Construction Scheduling and Logistics
Preconstruction technology helps optimize construction schedules, improve resource allocation, and streamline logistics.
- Construction Management Software: These tools help create detailed project schedules, track progress, and manage resources. This allows for real-time monitoring of project timelines and ensures everyone is working towards the same goals. For example, construction management software can be used to track the progress of individual tasks, identify potential delays, and adjust the schedule accordingly.
- 4D BIM: 4D BIM adds the dimension of time to the BIM model, creating a virtual simulation of the construction process. This allows for visualizing the project’s progress over time, identifying potential bottlenecks, and optimizing the construction schedule. For example, 4D BIM can be used to simulate the sequence of construction activities, ensuring efficient material delivery and minimizing delays.
- GPS Tracking: GPS tracking technology allows for real-time monitoring of equipment and materials, optimizing delivery schedules and minimizing downtime. This data can also be used to track the progress of construction activities and identify potential bottlenecks. For example, GPS tracking can be used to monitor the movement of heavy equipment, ensuring it arrives on site at the right time and in the right order.
Impact on Construction Processes and Outcomes
Preconstruction technology revolutionizes traditional construction methods and workflows, bringing about significant changes in how projects are planned, designed, and executed. The integration of these technologies introduces a paradigm shift in the industry, enhancing project efficiency, accuracy, and collaboration, ultimately leading to improved project outcomes.
Impact on Traditional Construction Methods and Workflows
Preconstruction technology significantly alters traditional construction methods and workflows by introducing digital tools and processes. These technologies enable a more streamlined and data-driven approach to construction projects, transforming how architects, engineers, and contractors collaborate and manage various project phases.
- Digital Modeling and Visualization: Building Information Modeling (BIM) and other digital modeling software replace traditional 2D drawings with 3D models, providing a comprehensive and interactive representation of the project. This allows stakeholders to visualize the project in its entirety, identify potential clashes, and make informed decisions during the design phase.
- Virtual Reality and Augmented Reality: VR and AR technologies offer immersive experiences, enabling stakeholders to walk through virtual models of the project, identify potential issues, and gain a better understanding of the design intent.
- Data Analytics and Predictive Modeling: Preconstruction technology leverages data analytics to identify trends, analyze risks, and predict potential issues. This allows for better project planning, resource allocation, and risk mitigation.
Improvement in Project Efficiency, Accuracy, and Collaboration
Preconstruction technology enhances project efficiency, accuracy, and collaboration by providing real-time data, facilitating communication, and automating repetitive tasks.
- Real-Time Data and Communication: Cloud-based platforms and collaborative software enable real-time data sharing and communication among stakeholders, eliminating delays and ensuring everyone is working with the latest information.
- Automated Tasks and Processes: Preconstruction technology automates repetitive tasks, such as quantity takeoffs, cost estimations, and scheduling, freeing up time for more strategic activities.
- Improved Collaboration and Coordination: Digital platforms facilitate better communication and coordination among stakeholders, reducing misunderstandings and streamlining workflows.
Reduction in Construction Costs, Delays, and Enhancement of Project Quality
By optimizing processes and improving communication, preconstruction technology contributes to reducing construction costs, minimizing delays, and enhancing project quality.
- Cost Reduction: Preconstruction technology helps identify potential cost overruns early in the design phase, enabling cost-effective design decisions and reducing rework during construction.
- Delay Mitigation: Improved planning, coordination, and communication facilitated by preconstruction technology minimize delays caused by unforeseen circumstances or miscommunication.
- Quality Enhancement: Accurate modeling, detailed visualizations, and real-time data sharing contribute to better construction quality by minimizing errors and ensuring adherence to design specifications.
Comparison of Preconstruction Technology with Traditional Methods
Feature | Traditional Methods | Preconstruction Technology |
---|---|---|
Design and Visualization | 2D drawings, limited visualization | 3D modeling, BIM, VR, AR, immersive visualization |
Communication and Collaboration | Limited communication, potential for misunderstandings | Real-time data sharing, cloud-based platforms, improved communication and collaboration |
Cost Estimation and Control | Manual calculations, potential for errors | Automated cost estimation, data analytics, better cost control |
Scheduling and Project Management | Manual scheduling, potential for delays | Automated scheduling, real-time tracking, improved project management |
Risk Management | Limited risk identification and mitigation | Data analytics, predictive modeling, proactive risk management |
Quality Control | Manual inspections, potential for errors | Digital inspections, automated quality control, improved quality assurance |
Challenges and Future Trends
While preconstruction technology offers numerous benefits, its implementation also presents several challenges that need to be addressed for its successful adoption and widespread use in the construction industry. These challenges are intertwined with the evolving trends in the field, which are shaping the future of preconstruction technology.
Challenges Associated with Implementing Preconstruction Technology
Implementing preconstruction technology effectively requires overcoming several hurdles, ranging from data management to workforce training.
- Data Management and Security: Preconstruction technology relies heavily on data, including project designs, cost estimates, and schedules. Managing this data effectively is crucial, as it needs to be accurate, accessible, and secure. Ensuring data integrity and protecting sensitive information from unauthorized access are paramount.
- Integration with Existing Systems: Integrating preconstruction technology with existing systems, such as project management software and building information modeling (BIM) platforms, can be complex and time-consuming. Ensuring seamless data flow and interoperability between different systems is essential for maximizing the benefits of preconstruction technology.
- Training and Workforce Development: Implementing preconstruction technology requires a skilled workforce that can effectively utilize the technology. This involves training existing staff and attracting new talent with the necessary skills. Training programs should cover the use of specific software, data analysis techniques, and the latest advancements in preconstruction technology.
- Cost of Adoption: Implementing preconstruction technology can be expensive, involving investments in software, hardware, and training. The cost of adoption can be a barrier for smaller construction companies or those with limited budgets. However, the long-term benefits of preconstruction technology, such as improved efficiency and reduced costs, can outweigh the initial investment.
Future Trends in Preconstruction Technology
Preconstruction technology is continuously evolving, driven by advancements in artificial intelligence, the Internet of Things, and virtual reality. These trends are shaping the future of preconstruction, enabling more efficient, sustainable, and innovative construction projects.
- Advancements in AI and Machine Learning: AI and machine learning are transforming preconstruction by automating tasks, improving data analysis, and enhancing predictive modeling. AI-powered tools can analyze vast amounts of data to identify patterns, optimize designs, and predict project outcomes with greater accuracy. Examples include AI-driven cost estimation tools that can provide more accurate and detailed cost breakdowns based on historical data and project specifications.
- Integration of IoT and Smart Sensors: The Internet of Things (IoT) and smart sensors are connecting construction sites and providing real-time data on various aspects of the project, such as environmental conditions, equipment usage, and worker safety. This data can be used to optimize construction processes, improve efficiency, and enhance safety measures. For instance, smart sensors can monitor the temperature and humidity of concrete during pouring, ensuring optimal curing conditions and preventing defects.
- Development of New Virtual and Augmented Reality Applications: Virtual reality (VR) and augmented reality (AR) are creating immersive experiences for construction professionals, allowing them to visualize and interact with project designs in a realistic and interactive way. VR and AR applications can be used for site walkthroughs, design reviews, and training simulations, enhancing collaboration and reducing errors during the preconstruction phase.
- Increased Use of Data Analytics and Predictive Modeling: Data analytics and predictive modeling are becoming increasingly important in preconstruction, enabling construction professionals to make data-driven decisions and anticipate potential risks. By analyzing historical data and project trends, construction teams can identify potential issues, optimize resource allocation, and improve project scheduling.
Concluding Remarks
As preconstruction technology continues to evolve, its impact on the construction industry will only intensify. With advancements in artificial intelligence, the Internet of Things (IoT), and data analytics, we can expect even more innovative solutions that will further streamline construction processes, improve project outcomes, and enhance the overall construction experience. The future of construction is undoubtedly intertwined with the transformative power of preconstruction technology.
Preconstruction technology helps streamline the building process, offering insights into potential challenges and cost estimations. One innovative tool in this realm is the technological table , which allows for real-time collaboration and data sharing among stakeholders. This collaborative approach can significantly improve communication and efficiency, ultimately leading to a smoother and more successful preconstruction phase.