Phase Technologies Pump Controllers: Managing Fluid Flow
Phase Technologies pump controllers are essential components in modern fluid management systems, providing precise control over pumps for a wide range of applications. These controllers offer sophisticated features like speed […]
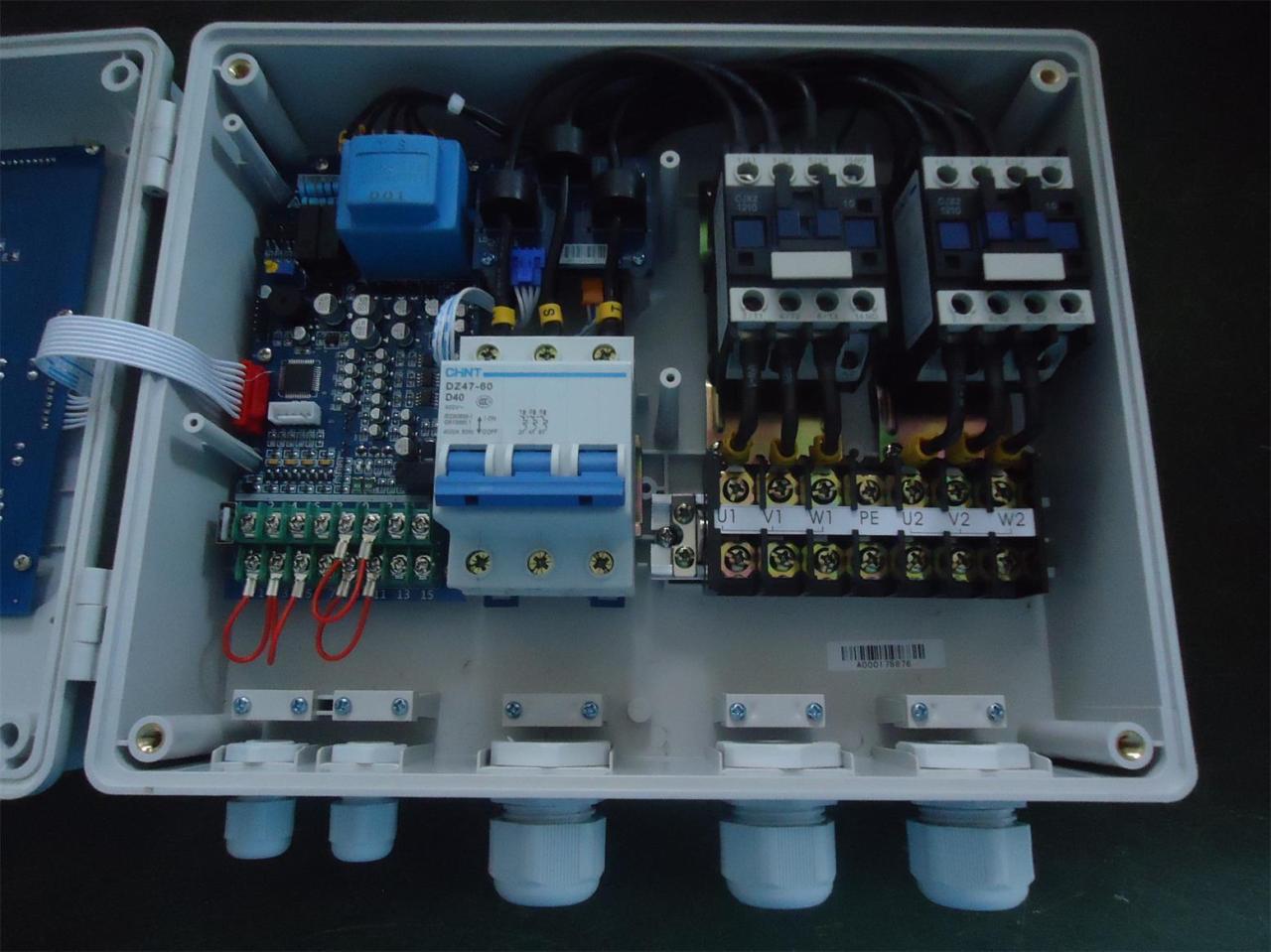
Phase Technologies pump controllers are essential components in modern fluid management systems, providing precise control over pumps for a wide range of applications. These controllers offer sophisticated features like speed regulation, pressure monitoring, and flow control, ensuring efficient and reliable operation.
The controllers are designed to work with various types of pumps, including centrifugal, positive displacement, and submersible pumps, making them adaptable to diverse industrial and commercial needs. Their user-friendly interfaces and programmable settings allow for customization and optimization to meet specific application requirements.
Introduction to Phase Technologies Pump Controllers
Phase Technologies is a leading provider of innovative and reliable pump control solutions for various industries. They specialize in designing and manufacturing advanced controllers that optimize pump performance, enhance efficiency, and ensure reliable operation.
Pump controllers are essential components in fluid management systems, playing a crucial role in regulating the flow, pressure, and speed of pumps. They provide precise control over pump operations, allowing for efficient and effective fluid transfer. These controllers are designed to monitor various parameters such as flow rate, pressure, and motor current, and adjust pump operation accordingly to meet specific requirements.
Types of Pumps Controlled by Phase Technologies Controllers
Phase Technologies controllers are compatible with a wide range of pumps, including:
- Centrifugal pumps: These pumps use a rotating impeller to create centrifugal force, which moves fluids from the center of the pump to the periphery.
- Positive displacement pumps: These pumps use a mechanism to displace a fixed volume of fluid with each rotation, providing a constant flow rate.
- Submersible pumps: These pumps are designed to be submerged in the fluid being pumped, often used in applications such as water wells and wastewater treatment.
- Diaphragm pumps: These pumps use a diaphragm to move fluid, often used in applications requiring precise flow control.
- Rotary pumps: These pumps use rotating elements to move fluid, often used in applications requiring high flow rates.
Functionality and Features of Phase Technologies Pump Controllers
Phase Technologies pump controllers are sophisticated devices designed to manage and optimize the performance of pumping systems across various applications. These controllers offer a comprehensive suite of functionalities, including speed control, pressure regulation, flow monitoring, and safety features, all integrated into a user-friendly platform.
Speed Control
Speed control is a fundamental feature of Phase Technologies pump controllers. It allows users to adjust the pump’s operating speed to meet specific demands. The controllers employ advanced algorithms to ensure smooth and precise speed regulation, optimizing energy efficiency and pump lifespan. The speed control mechanisms can be configured to respond to changes in pressure, flow, or other system parameters, ensuring optimal performance across varying operating conditions.
Pressure Regulation
Pressure regulation is another key functionality of Phase Technologies pump controllers. The controllers maintain consistent pressure levels within the system, ensuring reliable and efficient operation. This is achieved through sophisticated control algorithms that adjust pump speed or other system parameters to compensate for pressure fluctuations. Pressure regulation is crucial in applications where consistent pressure is critical, such as water distribution systems, irrigation systems, and industrial processes.
Flow Monitoring
Phase Technologies pump controllers provide comprehensive flow monitoring capabilities. They accurately measure and display the flow rate of the pumped fluid, providing valuable insights into system performance. This information can be used to identify potential problems, optimize system efficiency, and ensure accurate billing for water or other fluids. The flow monitoring data can also be used to trigger alarms or adjust pump operation to maintain desired flow rates.
Safety Features
Safety is paramount in any pumping system, and Phase Technologies pump controllers incorporate a range of safety features to protect both equipment and personnel. These features include:
- Overload protection: This feature prevents the pump from overheating or damaging itself by automatically shutting down the system if excessive load is detected.
- Dry run protection: This feature prevents the pump from running dry, which can cause damage to the pump and potentially lead to a fire. It detects low liquid levels and shuts down the pump before damage occurs.
- Phase loss detection: This feature detects a loss of power to the pump and shuts down the system to prevent damage or injury. This is particularly important in industrial applications where power outages can occur.
Operating Modes and Control Algorithms
Phase Technologies pump controllers offer a variety of operating modes to cater to different applications and requirements. These modes include:
- Constant speed: This mode operates the pump at a fixed speed, regardless of changes in pressure or flow.
- Variable speed: This mode adjusts the pump speed to maintain a constant pressure or flow rate, optimizing energy efficiency.
- Pressure control: This mode maintains a constant pressure within the system by adjusting pump speed or other system parameters.
- Flow control: This mode maintains a constant flow rate by adjusting pump speed or other system parameters.
The controllers employ advanced control algorithms to achieve precise and efficient operation in each mode. These algorithms can be configured to meet specific system requirements and optimize performance.
User Interface and Programming Options
Phase Technologies pump controllers offer a user-friendly interface for configuring and managing the system. The interface is typically accessed via a display panel on the controller or through a remote connection. The interface allows users to:
- Monitor system parameters: This includes real-time data on pressure, flow, speed, and other relevant variables.
- Configure operating modes: Users can select the desired operating mode and adjust parameters to meet specific needs.
- Set alarms and notifications: Users can configure the controller to trigger alarms or notifications based on predefined conditions, such as high pressure, low flow, or equipment failure.
- Access historical data: The controllers can store historical data on system performance, allowing users to analyze trends and optimize operation.
The controllers may also offer programming options for advanced users, allowing them to customize control algorithms and system settings.
Applications of Phase Technologies Pump Controllers
Phase Technologies pump controllers are versatile and find applications in various industries, playing a crucial role in optimizing pumping operations across diverse sectors. Their adaptability and advanced features make them suitable for managing various pump types, from simple single-phase pumps to complex multi-stage systems.
Water Treatment
Water treatment plants rely heavily on pumps for various processes, including water intake, filtration, disinfection, and distribution. Phase Technologies pump controllers offer precise control over pump operation, ensuring efficient and reliable water treatment.
- Water Intake: Controllers regulate the flow rate of raw water into the treatment plant, optimizing intake based on demand and water quality.
- Filtration: Precise control over pump speed and pressure is essential for efficient filtration. Controllers ensure optimal flow rates through filters, minimizing clogging and maximizing filter life.
- Disinfection: Accurate dosing of disinfectants is crucial for water safety. Controllers can manage pump operation to deliver precise amounts of disinfectant based on flow rates and water quality parameters.
- Distribution: Controllers ensure consistent water pressure throughout the distribution network, minimizing pressure fluctuations and ensuring reliable water supply to consumers.
HVAC Systems
Heating, ventilation, and air conditioning (HVAC) systems rely on pumps for circulating water or refrigerant. Phase Technologies pump controllers contribute to energy efficiency and optimal comfort levels in buildings.
- Chilled Water Systems: Controllers regulate pump operation to maintain precise temperatures in chilled water loops, ensuring efficient cooling of buildings.
- Heating Systems: Controllers manage pump speed and pressure to optimize hot water circulation, ensuring consistent heating throughout the building.
- Variable-Speed Pumps: Controllers can be used with variable-speed pumps, allowing for precise control over flow rates and energy consumption, minimizing energy waste and maximizing comfort.
Chemical Processing
Chemical processing plants require precise control over pump operation for safe and efficient production. Phase Technologies pump controllers ensure accurate chemical dosing, minimize process variations, and enhance safety.
- Chemical Dosing: Controllers manage pump operation to deliver precise amounts of chemicals, ensuring accurate mixing and reactions in chemical processes.
- Process Control: Controllers can monitor and adjust pump operation based on process parameters, ensuring consistent product quality and minimizing waste.
- Safety: Controllers can incorporate safety features, such as over-current protection and dry-run prevention, to prevent accidents and ensure safe operation.
Agriculture
Irrigation systems rely on pumps to distribute water to crops. Phase Technologies pump controllers optimize water usage, minimizing waste and maximizing crop yields.
- Precision Irrigation: Controllers can be used to control irrigation systems based on soil moisture sensors, ensuring water is delivered only when needed and reducing water waste.
- Variable-Speed Pumps: Controllers can be used with variable-speed pumps, allowing for precise control over flow rates and water pressure, optimizing water usage for different crops and soil types.
- Remote Monitoring: Controllers can be equipped with remote monitoring capabilities, allowing farmers to monitor pump operation and adjust settings from anywhere, ensuring efficient water management.
Technical Specifications and Design Considerations
Phase Technologies pump controllers are designed with a comprehensive set of features and specifications that cater to a wide range of pumping applications. Understanding these specifications and design considerations is crucial for selecting the appropriate controller for your specific needs.
Input/Output Capabilities
The input/output capabilities of a pump controller determine its ability to interface with other components in the pumping system.
- Analog Inputs: These inputs are used to receive signals from sensors such as pressure transducers, flow meters, and level switches. Analog inputs typically have a range of 4-20 mA or 0-10 V, allowing for precise measurement and control.
- Digital Inputs: These inputs are used to receive on/off signals from switches, relays, or other digital devices. They can be used to trigger events, monitor system status, or provide feedback.
- Analog Outputs: These outputs are used to control the speed or flow rate of the pump. They can be configured to provide a variable voltage or current signal to the pump motor or valve.
- Digital Outputs: These outputs are used to control external devices such as alarms, solenoids, or relays. They can be configured to provide a high or low signal to activate or deactivate these devices.
Communication Protocols
Pump controllers often support various communication protocols for seamless integration with other systems and devices.
- Modbus: This is a widely used serial communication protocol for industrial automation systems. Modbus allows the pump controller to communicate with other devices such as PLCs, HMIs, and SCADA systems.
- Ethernet: This protocol enables communication over a network, allowing for remote monitoring and control of the pump system. Ethernet-enabled controllers can be accessed from anywhere with an internet connection.
- Wireless Protocols: Some controllers support wireless communication protocols such as Wi-Fi or Bluetooth, providing flexibility in system design and installation.
Power Requirements
The power requirements of a pump controller should be carefully considered to ensure compatibility with the available power supply.
- Voltage: Pump controllers are typically available in various voltage options, such as 12 VDC, 24 VDC, 110 VAC, or 220 VAC. It is essential to select a controller with the appropriate voltage rating for the intended application.
- Current: The current draw of the controller should be within the capacity of the power supply. Exceeding the power supply’s rating can lead to overheating or damage to the controller.
Environmental Ratings
The environmental ratings of a pump controller determine its ability to operate in specific conditions.
- Temperature: The operating temperature range of the controller should be compatible with the ambient temperature of the installation location. Some controllers are designed for extreme temperatures, while others are suitable for more moderate environments.
- Humidity: The humidity rating indicates the controller’s ability to withstand moisture. Controllers designed for outdoor applications typically have higher humidity ratings than those intended for indoor use.
- Ingress Protection (IP) Rating: This rating indicates the controller’s resistance to dust, water, and other environmental factors. Higher IP ratings indicate greater protection.
Design Considerations
When selecting a Phase Technologies pump controller, several design considerations should be taken into account.
- Pump Type: Different pump types require specific control strategies. For example, centrifugal pumps may require variable frequency drives (VFDs) for speed control, while positive displacement pumps may use pressure or flow control mechanisms.
- Application Requirements: The specific requirements of the application, such as flow rate, pressure, and operating conditions, will influence the choice of controller. For example, a high-pressure application may require a controller with advanced pressure control capabilities.
- System Integration: The controller should be compatible with existing systems and devices, including sensors, actuators, and communication networks. It should also be easy to configure and integrate with the overall control system.
- Reliability and Durability: The controller should be designed for reliable operation in the intended environment. Factors such as component quality, construction materials, and environmental ratings play a crucial role in determining reliability and durability.
- Maintenance and Support: Consider the availability of spare parts, technical support, and documentation for the selected controller. Ease of maintenance and troubleshooting can significantly impact the overall system performance and longevity.
Components and Subsystems
A typical Phase Technologies pump controller consists of several components and subsystems that work together to provide reliable control.
- Microprocessor: The central processing unit (CPU) of the controller, responsible for executing control algorithms and managing the overall system operation.
- Input/Output Modules: These modules provide interfaces for connecting sensors, actuators, and other devices to the controller.
- Communication Interface: This module enables communication with other systems and devices via protocols such as Modbus, Ethernet, or wireless protocols.
- Power Supply: This component provides the necessary power for the controller to operate.
- Enclosure: The housing that protects the controller’s internal components from environmental factors.
- Software: The control algorithms and user interface that define the controller’s functionality and operation.
Installation, Configuration, and Maintenance
Proper installation, configuration, and maintenance of a Phase Technologies pump controller are crucial for ensuring optimal performance, reliability, and longevity. This section provides a comprehensive guide to these processes, covering essential steps and considerations for achieving a successful implementation.
Installation
The installation process begins with carefully selecting a suitable location for the controller. The chosen site should provide adequate ventilation, protection from environmental elements, and easy access for maintenance. Once the location is determined, follow these steps:
- Mount the controller securely to a wall or panel using the provided mounting brackets.
- Connect the power supply to the controller, ensuring the voltage and current ratings are compatible.
- Connect the pump motor to the controller’s output terminals, following the wiring diagram provided in the user manual.
- Connect any additional sensors or devices, such as flow meters, pressure sensors, or level switches, to the appropriate input terminals on the controller.
- Verify all connections are secure and properly labeled.
Configuration
After installation, the pump controller needs to be configured to meet the specific requirements of the pumping system. This involves setting parameters such as:
- Pump operating modes (e.g., constant pressure, variable speed, flow control).
- Set points for pressure, flow rate, and other parameters.
- Alarm thresholds for high/low pressure, flow rate, and other conditions.
- Control logic and sequences for pump operation.
- Communication protocols for data logging and remote monitoring.
Wiring
Proper wiring is essential for safe and reliable operation of the pump controller. The wiring diagram provided in the user manual should be strictly followed. Use high-quality wires with appropriate gauge and insulation for the specific application. Ensure all connections are made securely and properly labeled for easy identification.
Calibration
Calibration is crucial for ensuring the accuracy of the pump controller’s measurements and control. This involves adjusting the controller’s settings to match the actual characteristics of the pump and the pumping system. Calibration procedures are typically Artikeld in the user manual.
Programming
The pump controller may require programming to implement specific control logic or sequences. The programming language and interface will vary depending on the controller model. Refer to the user manual for detailed instructions on programming the controller.
Maintenance
Routine maintenance is essential for keeping the pump controller operating reliably. This includes:
- Regularly inspecting the controller for any signs of damage or wear.
- Cleaning the controller’s enclosure and components to remove dust and debris.
- Verifying the connections are secure and properly labeled.
- Performing calibration checks to ensure the controller is operating accurately.
- Updating the firmware or software as needed.
Troubleshooting, Phase technologies pump controller
Common issues with pump controllers can be resolved by following these troubleshooting steps:
- Verify the power supply is working correctly.
- Check the wiring connections for any loose or damaged wires.
- Inspect the pump motor for any signs of malfunction.
- Review the controller’s alarm logs for any error messages.
- If necessary, contact the manufacturer for technical support.
Integration and Compatibility
Phase Technologies pump controllers are designed to seamlessly integrate with various systems and equipment, enhancing overall system efficiency and functionality. Their compatibility with diverse pump types, sensors, actuators, and communication protocols allows for flexible and scalable solutions tailored to specific needs.
Compatibility with Various Pump Types
The ability to interface with various pump types is crucial for ensuring the controller’s versatility. Phase Technologies controllers are compatible with a wide range of pumps, including:
- Centrifugal pumps
- Positive displacement pumps
- Submersible pumps
- Vertical turbine pumps
- Progressive cavity pumps
This compatibility allows for optimal control and monitoring of various pump applications across different industries.
Compatibility with Sensors and Actuators
Phase Technologies controllers are equipped with multiple input and output channels for seamless integration with various sensors and actuators. This enables precise monitoring of system parameters and responsive control actions. Common sensors compatible with the controllers include:
- Flow meters
- Pressure sensors
- Level sensors
- Temperature sensors
Similarly, the controllers can interact with various actuators such as:
- Variable frequency drives (VFDs)
- Solenoid valves
- Control relays
- Motor starters
This comprehensive compatibility ensures precise control and automation of pump systems based on real-time data.
Communication Protocols
Phase Technologies controllers support various communication protocols, facilitating seamless integration with existing control systems and data networks. Common protocols supported include:
- Modbus
- Ethernet
- RS-485
- Profibus
- CANbus
This ensures compatibility with a wide range of industrial automation systems, enabling data exchange and remote monitoring.
Integration with Other Systems
Phase Technologies pump controllers can be integrated with various systems and equipment, enhancing overall system efficiency and functionality. Examples include:
- SCADA Systems: Integration with supervisory control and data acquisition (SCADA) systems enables centralized monitoring and control of multiple pump systems from a single location. This allows for real-time data visualization, trend analysis, and remote troubleshooting, improving operational efficiency and minimizing downtime.
- Building Management Systems (BMS): Integration with BMS systems allows for efficient control and monitoring of pumps within buildings, optimizing energy consumption and ensuring comfort. This can include controlling pumps for HVAC systems, water supply, and fire suppression systems.
- Industrial Automation Systems: Integration with industrial automation systems enables seamless control and monitoring of pumps within complex industrial processes. This allows for coordinated control of pumps with other equipment, optimizing production efficiency and minimizing downtime.
Industry Standards and Certifications: Phase Technologies Pump Controller
Phase Technologies pump controllers are designed and manufactured to meet stringent industry standards and certifications, ensuring their safety, reliability, and compatibility in various applications. These certifications serve as a testament to the quality and adherence to global safety and performance guidelines.
Safety and Compliance
The safety and compliance of Phase Technologies pump controllers are paramount. They are designed and tested to meet the requirements of internationally recognized safety standards, such as UL (Underwriters Laboratories) and CE (Conformité Européenne). These certifications ensure that the controllers are safe for use in various environments and applications.
- UL Certification: This certification signifies that the pump controller has been tested and meets the safety standards set by UL, a globally recognized independent safety science company. UL certification is crucial for products sold in North America and other countries that adhere to UL standards.
- CE Marking: The CE marking indicates that the pump controller complies with European Union (EU) safety, health, and environmental protection requirements. It ensures that the product meets the essential requirements of the relevant EU directives and can be freely marketed within the EU.
Quality and Reliability
Industry certifications like UL, CE, and others are not only about safety but also about the quality and reliability of the product. These certifications involve rigorous testing and evaluation processes to ensure that the pump controllers meet the highest standards of performance and durability.
- Testing Procedures: Certifications like UL and CE involve comprehensive testing procedures that cover various aspects, including electrical safety, mechanical strength, environmental resistance, and electromagnetic compatibility. These tests are conducted by independent certification bodies, ensuring impartiality and credibility.
- Quality Control: The certification process also includes rigorous quality control measures throughout the manufacturing process. These measures ensure that the products meet the specified standards and maintain their high quality. This involves regular inspections, audits, and traceability of materials and components.
Benefits of Certifications
Certifications provide numerous benefits for both the manufacturer and the end-user. For Phase Technologies, certifications demonstrate their commitment to quality and safety, building trust and confidence among customers. For end-users, certifications provide assurance that the pump controller is safe, reliable, and meets the required standards for their specific application.
- Enhanced Safety: Certifications like UL and CE ensure that the pump controller meets stringent safety standards, reducing the risk of accidents or hazards during operation.
- Improved Reliability: Rigorous testing and quality control measures associated with certifications ensure that the pump controllers are reliable and perform as expected over their lifespan.
- Global Market Access: Certifications like UL and CE enable Phase Technologies to sell their pump controllers in various international markets, expanding their reach and customer base.
Future Trends and Innovations
The field of pump control technology is constantly evolving, driven by advancements in digitalization, automation, and a growing emphasis on energy efficiency and sustainability. Phase Technologies is well-positioned to leverage these trends and continue to innovate, offering solutions that meet the evolving needs of its customers.
Integration with Smart Technologies
The increasing adoption of smart technologies presents significant opportunities for pump control systems. Smart pumps can be integrated with Building Management Systems (BMS) and Internet of Things (IoT) platforms, enabling real-time monitoring, remote control, and predictive maintenance. This integration can lead to improved operational efficiency, reduced downtime, and optimized energy consumption.
- Data-Driven Insights: Smart pump controllers can collect and analyze data on pump performance, operating conditions, and energy consumption. This data can be used to identify potential problems before they occur, optimize pump settings for efficiency, and track energy usage over time.
- Remote Monitoring and Control: Remote monitoring and control capabilities allow operators to monitor pump performance and make adjustments from anywhere with an internet connection. This can significantly reduce response times to issues and improve overall system availability.
- Predictive Maintenance: By analyzing data patterns, smart pump controllers can predict potential failures and recommend maintenance schedules. This proactive approach can help prevent costly downtime and extend the lifespan of pumps.
Wrap-Up
Phase Technologies pump controllers are critical for optimizing fluid management systems across various industries. Their advanced functionalities, adaptability, and integration capabilities make them invaluable tools for improving efficiency, safety, and overall performance. As technology continues to evolve, we can expect to see even more innovative features and applications emerge in the realm of pump control.
Phase Technologies pump controllers are known for their reliability and precision in managing fluid flow. While they excel in their core function, advancements in new air technologies are opening up exciting possibilities for integrating air handling systems with pump control, leading to greater energy efficiency and improved overall system performance.
This integration could see Phase Technologies pump controllers become even more versatile and adaptable to the demands of modern, sustainable building systems.