OEM Technologies: Shaping Industries and Driving Innovation
OEM Technologies, the backbone of modern manufacturing and technology, play a pivotal role in shaping industries and driving innovation. These technologies, often supplied by Original Equipment Manufacturers (OEMs), encompass a […]
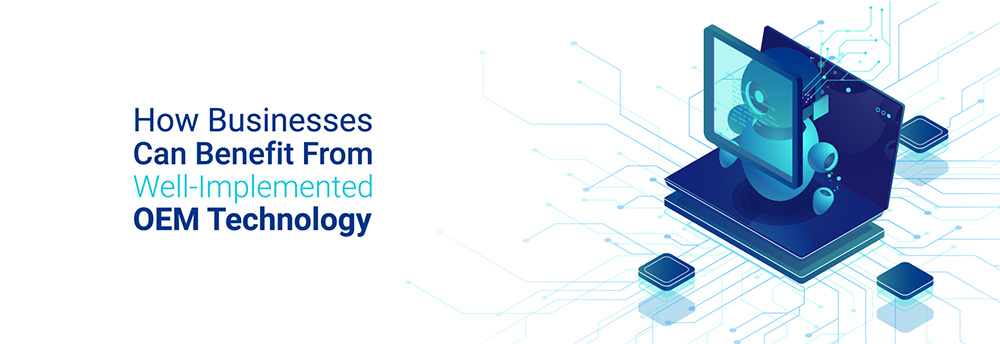
OEM Technologies, the backbone of modern manufacturing and technology, play a pivotal role in shaping industries and driving innovation. These technologies, often supplied by Original Equipment Manufacturers (OEMs), encompass a wide range of hardware, software, and services that form the building blocks of countless products and systems.
OEM technologies are distinct from those developed by Original Design Manufacturers (ODMs), who typically design and manufacture products according to specifications provided by OEMs. This distinction is crucial as it highlights the different roles played by each entity in the product development and supply chain.
Definition of OEM Technologies
OEM (Original Equipment Manufacturer) technologies are components or products that are manufactured by one company and then incorporated into the final products of another company. These technologies are often used in various industries, including electronics, automotive, and manufacturing.
OEM technologies play a crucial role in the manufacturing and technology industries by enabling companies to focus on their core competencies and leverage the expertise of specialized manufacturers. This allows for greater efficiency, cost savings, and faster product development cycles.
OEM vs. ODM
The difference between OEM and ODM (Original Design Manufacturer) lies in the level of design control. OEMs typically manufacture components or products based on designs provided by the original equipment manufacturer (OEM). In contrast, ODMs are responsible for both designing and manufacturing the product, often working closely with the OEM to meet their specific requirements.
Advantages of Using OEM Technologies
Using OEM technologies offers several advantages, including:
- Cost savings: By outsourcing the production of components or products, companies can reduce their manufacturing costs and focus on their core competencies.
- Access to specialized expertise: OEM manufacturers often have specialized expertise and technologies that may not be readily available in-house.
- Faster product development cycles: OEMs can leverage their existing manufacturing infrastructure and processes to expedite product development and bring products to market faster.
- Improved product quality: OEM manufacturers often have rigorous quality control processes and expertise in specific manufacturing techniques, which can lead to higher product quality.
Disadvantages of Using OEM Technologies
While there are several advantages to using OEM technologies, there are also some potential disadvantages:
- Loss of control over design and manufacturing: Companies may lose some control over the design and manufacturing process when outsourcing to OEMs.
- Potential for intellectual property issues: Sharing designs and specifications with OEMs can raise concerns about intellectual property protection.
- Dependency on OEMs: Companies may become reliant on their OEM partners, which can create vulnerabilities if the OEM experiences production issues or delays.
- Supply chain disruptions: Disruptions in the OEM’s supply chain can impact the availability of components or products, potentially delaying production schedules.
Types of OEM Technologies
OEM technologies encompass a wide range of products and services that manufacturers utilize to integrate into their own final products. These technologies are often customized to meet specific requirements and enhance the functionality, performance, or aesthetics of the end product. Understanding the various types of OEM technologies is crucial for businesses seeking to optimize their product development and manufacturing processes.
Hardware OEM Technologies
Hardware OEM technologies refer to physical components or systems that are incorporated into other products. These technologies are often designed and manufactured specifically for integration purposes, ensuring compatibility and seamless operation within the final product.
- Microprocessors and Chipsets: These are the brains of many electronic devices, providing the computational power necessary for various functions. Examples include Intel Core processors used in laptops and desktops, and Qualcomm Snapdragon chipsets used in smartphones.
- Memory Modules: These store data and instructions for the device, enabling it to function. Examples include DDR5 RAM modules used in high-performance computers, and eMMC storage chips used in smartphones.
- Displays: These provide the visual interface for users, ranging from small screens on smartwatches to large displays on televisions. Examples include OLED panels used in premium smartphones and LCD panels used in laptops.
- Sensors: These detect various environmental conditions or user interactions, providing data for the device to process. Examples include accelerometers used in smartphones to detect movement, and pressure sensors used in touchscreens.
- Connectivity Modules: These enable communication between devices, including Wi-Fi, Bluetooth, and cellular modules. Examples include Intel Wi-Fi 6 modules used in laptops, and Qualcomm Snapdragon X55 modems used in smartphones.
Software OEM Technologies
Software OEM technologies refer to software applications or tools that are integrated into other products, providing specific functionalities or enhancing the user experience. These technologies are often customized to meet the specific needs of the final product, ensuring seamless integration and optimal performance.
- Operating Systems: These provide the foundation for all other software to run, managing the device’s resources and providing a user interface. Examples include Android used in smartphones, iOS used in iPhones, and Windows used in personal computers.
- Embedded Software: This software is specifically designed for specific hardware platforms and is often used to control the device’s functions. Examples include firmware for printers, control software for industrial robots, and embedded operating systems for smart appliances.
- Application Programming Interfaces (APIs): These allow different software components to communicate and share data, enabling seamless integration and interoperability. Examples include Google Maps API used in navigation apps, and Stripe API used in e-commerce platforms.
- Software Development Kits (SDKs): These provide tools and resources for developers to create software applications that are compatible with a specific platform. Examples include Android SDK for developing Android apps, and iOS SDK for developing iOS apps.
- Middleware: This software acts as a bridge between different software components, enabling them to communicate and share data effectively. Examples include message queues used in distributed systems, and application servers used in web applications.
Services OEM Technologies
Services OEM technologies refer to services provided by OEMs to support their hardware and software products. These services are often crucial for ensuring the smooth operation, maintenance, and ongoing support of the final product, contributing to customer satisfaction and product longevity.
- Technical Support: This provides assistance to customers who encounter issues with the product, ensuring timely resolution and minimizing downtime.
- Warranty and Repair Services: These cover the product against defects or malfunctions, providing peace of mind to customers and ensuring the product’s long-term reliability.
- Software Updates and Patches: These provide ongoing improvements and security enhancements to the product, ensuring it remains up-to-date and protected from vulnerabilities.
- Customization and Integration Services: These offer tailored solutions to meet specific customer requirements, ensuring the product is perfectly suited to their needs.
- Training and Documentation: These provide the necessary resources for customers to understand and use the product effectively, maximizing its potential and enhancing the user experience.
OEM Business Models
OEM companies employ various business models to cater to the specific needs of their customers and the nature of their products. These models define how OEMs interact with Original Design Manufacturers (ODMs) and end customers, ultimately shaping their overall revenue streams and market positioning.
OEM-ODM Relationships
OEM-ODM relationships are crucial to the success of OEM business models. ODMs specialize in designing and manufacturing products based on OEM specifications, allowing OEMs to focus on branding, marketing, and distribution.
- Contract Manufacturing: In this model, OEMs outsource the entire manufacturing process to ODMs. The OEM provides design specifications and handles marketing, sales, and distribution. This model is common for companies with limited manufacturing capabilities or those seeking to reduce operational costs.
- Joint Development: This model involves a closer collaboration between OEMs and ODMs, where both parties contribute to product design and development. OEMs leverage ODM expertise in manufacturing and cost optimization, while ODMs gain access to OEM market knowledge and branding capabilities.
- Strategic Partnerships: This model represents a long-term commitment between OEMs and ODMs, characterized by shared investments, joint product development, and co-branding efforts. This model fosters mutual growth and enables both parties to access each other’s strengths.
OEM-End Customer Relationships
OEMs engage with end customers through various channels, depending on their business model and target market.
- Direct Sales: OEMs directly sell their products to end customers through their own sales force, website, or retail outlets. This model offers greater control over pricing and customer relationships, but requires significant investment in sales and marketing infrastructure.
- Indirect Sales: OEMs rely on distributors, retailers, or value-added resellers (VARs) to reach end customers. This model allows OEMs to access wider markets and reduce sales and marketing costs, but requires careful channel management and coordination.
- Subscription Models: OEMs offer their products or services on a recurring subscription basis, providing customers with continuous access and support. This model generates consistent revenue streams and fosters long-term customer relationships, but requires effective customer retention strategies.
Benefits and Challenges of OEM Business Models
Different OEM business models offer unique advantages and disadvantages, depending on the specific context and industry.
- Benefits:
- Cost Optimization: Outsourcing manufacturing to ODMs can significantly reduce production costs, allowing OEMs to offer competitive pricing.
- Faster Time-to-Market: By leveraging ODM expertise, OEMs can shorten product development cycles and introduce new products more quickly.
- Access to Specialized Expertise: ODMs possess specialized manufacturing capabilities and technical knowledge that OEMs may lack, enabling them to produce complex products.
- Focus on Core Competencies: Outsourcing non-core functions allows OEMs to focus on their core strengths, such as branding, marketing, and customer service.
- Challenges:
- Quality Control: Ensuring consistent product quality when outsourcing manufacturing can be challenging, requiring rigorous quality control processes.
- Intellectual Property Protection: Sharing design specifications with ODMs raises concerns about intellectual property protection and potential leakage.
- Communication and Coordination: Effective communication and coordination between OEMs and ODMs are essential for successful product development and delivery.
- Dependency on ODMs: Over-reliance on ODMs can create vulnerability, making OEMs susceptible to disruptions in supply chains or changes in ODM pricing.
Impact of OEM Technologies on Industries
OEM technologies have significantly impacted various industries, driving innovation, efficiency, and overall growth. The adoption of these technologies has led to the development of new products and services, streamlined production processes, and enhanced customer experiences.
Impact on the Automotive Industry
OEM technologies have revolutionized the automotive industry, leading to advancements in vehicle design, manufacturing, and overall performance.
- Advanced Driver-Assistance Systems (ADAS): OEM technologies have enabled the development of ADAS features, such as lane departure warning, adaptive cruise control, and automated emergency braking, enhancing safety and driver convenience.
- Electric Vehicles (EVs): OEM technologies have played a crucial role in the development of EVs, enabling the production of high-performance batteries, efficient electric motors, and sophisticated charging systems.
- Connected Car Technologies: OEM technologies have facilitated the integration of connectivity features in vehicles, allowing for real-time traffic updates, remote diagnostics, and over-the-air software updates.
Impact on the Electronics Industry
OEM technologies have driven innovation and efficiency in the electronics industry, leading to the development of smaller, more powerful, and more affordable devices.
- Miniaturization and Integration: OEM technologies have enabled the miniaturization of electronic components and the integration of multiple functionalities into smaller devices.
- Advanced Semiconductor Technologies: OEM technologies have led to advancements in semiconductor fabrication, resulting in faster, more efficient, and more powerful processors.
- Internet of Things (IoT): OEM technologies have facilitated the development of IoT devices, enabling seamless connectivity and data exchange between devices and the cloud.
Impact on the Healthcare Industry
OEM technologies have transformed the healthcare industry, enabling more accurate diagnoses, personalized treatments, and improved patient outcomes.
- Medical Imaging: OEM technologies have led to advancements in medical imaging techniques, such as magnetic resonance imaging (MRI) and computed tomography (CT) scans, providing high-resolution images for diagnosis.
- Medical Devices: OEM technologies have enabled the development of sophisticated medical devices, such as pacemakers, artificial limbs, and robotic surgery systems, improving patient care.
- Telemedicine: OEM technologies have facilitated the adoption of telemedicine, enabling remote consultations, diagnosis, and treatment, expanding access to healthcare services.
Future Trends in OEM Technologies
The OEM landscape is constantly evolving, driven by technological advancements that are reshaping industries and creating new opportunities. Emerging trends like cloud computing, IoT, and artificial intelligence are playing a pivotal role in this transformation, influencing how OEMs design, manufacture, and deliver products and services.
Impact of Cloud Computing on OEM Technologies
Cloud computing offers a transformative platform for OEMs, enabling them to access scalable computing resources, storage, and software applications on demand. This has significant implications for the OEM industry, impacting various aspects of their operations:
- Enhanced Product Development: Cloud-based platforms provide OEMs with access to powerful computing resources, enabling them to accelerate product development cycles, perform complex simulations, and optimize designs.
- Improved Supply Chain Management: Cloud-based solutions facilitate real-time data sharing and collaboration across the supply chain, improving inventory management, production planning, and logistics efficiency.
- Data Analytics and Insights: Cloud-based data analytics platforms enable OEMs to gather and analyze data from various sources, gaining valuable insights into customer behavior, market trends, and product performance.
Impact of IoT on OEM Technologies
The Internet of Things (IoT) connects devices, machines, and systems, generating vast amounts of data that can be leveraged by OEMs to enhance product functionality, optimize operations, and create new revenue streams. The impact of IoT on OEM technologies is multifaceted:
- Connected Products and Services: OEMs can embed sensors and connectivity into their products, enabling them to collect data on product usage, performance, and environmental conditions. This data can be used to provide predictive maintenance, remote diagnostics, and personalized customer experiences.
- Smart Manufacturing and Automation: IoT enables OEMs to automate manufacturing processes, optimize production lines, and improve overall efficiency. Data collected from sensors and connected devices can be used to monitor equipment health, identify potential problems, and optimize resource allocation.
- New Business Models: IoT opens up new avenues for OEMs to generate revenue. They can offer subscription-based services, data analytics, and remote monitoring solutions based on the data collected from connected devices.
Impact of Artificial Intelligence on OEM Technologies
Artificial intelligence (AI) is rapidly transforming the OEM industry, empowering OEMs to automate tasks, improve decision-making, and create innovative products and services. AI technologies are impacting various aspects of OEM operations:
- Product Design and Engineering: AI-powered tools can assist engineers in designing and optimizing products, reducing development time and improving product performance. AI algorithms can analyze large datasets of design parameters, simulations, and customer feedback to identify optimal solutions.
- Production Optimization: AI can be used to optimize production processes, reducing waste, improving efficiency, and minimizing downtime. AI algorithms can analyze data from sensors and production lines to identify bottlenecks, predict maintenance needs, and optimize resource allocation.
- Customer Service and Support: AI-powered chatbots and virtual assistants can provide customers with instant support, answering questions, resolving issues, and providing personalized recommendations. AI can also analyze customer data to identify patterns and predict future needs, enabling OEMs to provide proactive support.
Final Summary
The impact of OEM technologies on industries is undeniable. From automotive to electronics and healthcare, these technologies have revolutionized manufacturing processes, enhanced product performance, and driven efficiency. As we look to the future, emerging trends like cloud computing, IoT, and artificial intelligence are poised to further transform the OEM landscape, opening up new possibilities for innovation and growth.
OEM technologies are a key part of many industries, from consumer electronics to automotive. These technologies can be complex, but they are often made easier to use through intuitive interfaces and user-friendly designs. This is especially important when it comes to technology for seniors, who may have less experience with modern devices.
For those looking for resources on making technology accessible for seniors, check out this guide on technology for seniors made easy. OEMs can play a crucial role in making sure technology is accessible and user-friendly for everyone, regardless of age or experience level.