Metal Recycling Technologies: A Sustainable Future
Metal recycling technologies are essential for building a sustainable future. As global metal consumption continues to rise, recycling plays a crucial role in conserving natural resources, reducing pollution, and creating […]
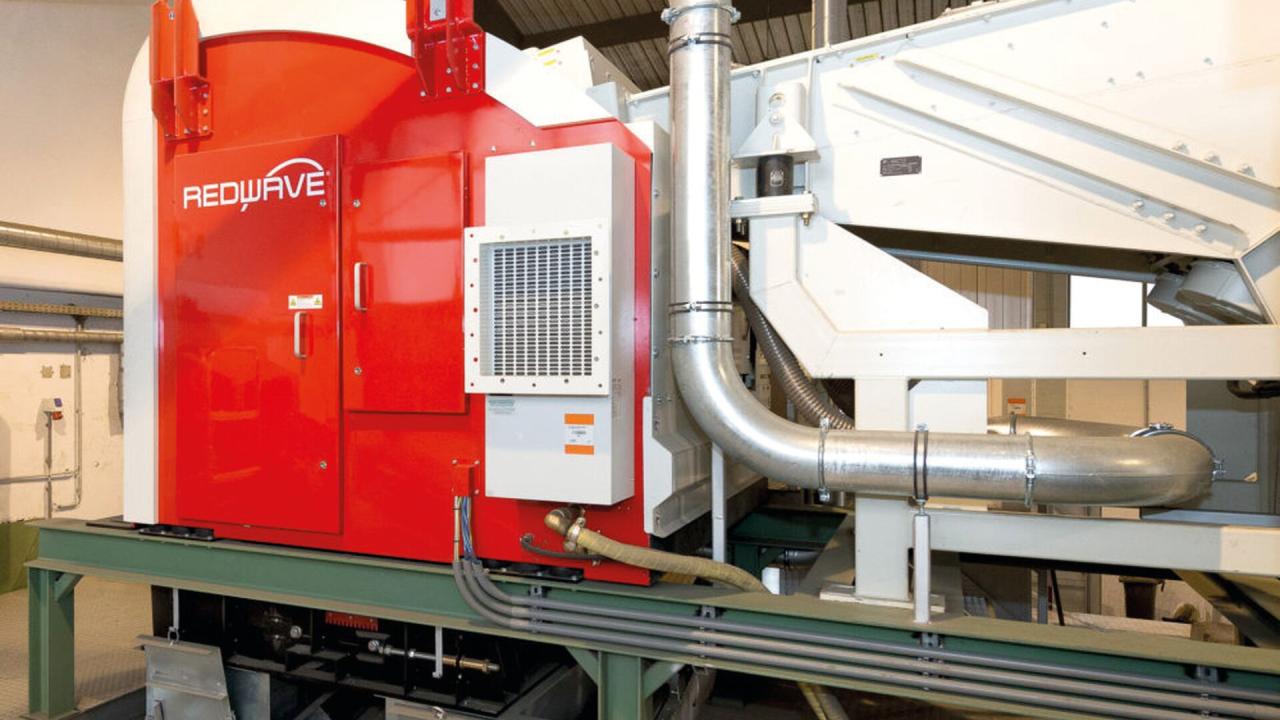
Metal recycling technologies are essential for building a sustainable future. As global metal consumption continues to rise, recycling plays a crucial role in conserving natural resources, reducing pollution, and creating a circular economy. Metal recycling processes involve various technologies, each with its own advantages and disadvantages, and contribute to a greener approach to resource management.
This exploration delves into the diverse world of metal recycling technologies, examining their principles, applications, and environmental impact. From mechanical recycling to pyrometallurgical and hydrometallurgical methods, we uncover the intricacies of these processes and explore the potential of emerging technologies. By understanding the various approaches to metal recycling, we can gain valuable insights into the industry’s future and its role in shaping a more sustainable world.
Introduction to Metal Recycling
Metal recycling plays a crucial role in building a sustainable future by promoting a circular economy. It involves recovering and reusing valuable metals instead of extracting new ones, minimizing environmental impact and maximizing resource efficiency.
Global Metal Consumption and Recycling Rates
Metal recycling significantly reduces the need for new metal extraction, which has significant environmental implications. Globally, the demand for metals is steadily increasing due to industrial growth and technological advancements. According to the International Resource Panel, the world consumed approximately 100 billion tonnes of materials in 2017, with metals accounting for a significant portion.
The recycling rate of metals varies widely depending on the type of metal and regional infrastructure. Some metals, such as aluminum and copper, have relatively high recycling rates, while others, like lead and tin, have lower rates. The global average recycling rate for metals is estimated to be around 35%, leaving a substantial amount of potential for improvement.
Environmental Benefits of Metal Recycling
Metal recycling offers numerous environmental benefits, making it a crucial component of sustainable practices.
- Reduced Mining and Extraction: Recycling metals significantly reduces the need for mining and extraction, minimizing environmental damage associated with these processes. Mining operations often involve deforestation, habitat destruction, and soil and water contamination.
- Lower Greenhouse Gas Emissions: Producing metals from raw materials is energy-intensive and generates significant greenhouse gas emissions. Recycling metals requires significantly less energy, leading to lower emissions and mitigating climate change.
- Conservation of Natural Resources: Recycling metals helps conserve finite natural resources. Extracting new metals requires large amounts of energy, water, and land, which are becoming increasingly scarce.
- Reduced Waste Generation: Recycling metals diverts waste from landfills, reducing the environmental burden associated with waste disposal. Landfills can release harmful pollutants into the environment, impacting air and water quality.
Economic Benefits of Metal Recycling
Metal recycling provides significant economic benefits, contributing to job creation and economic growth.
- Cost Savings: Recycling metals is generally cheaper than producing new metals from raw materials. This cost savings is passed on to consumers and businesses, making recycled products more affordable.
- Job Creation: The metal recycling industry creates numerous jobs in collection, processing, and manufacturing. This contributes to economic growth and supports local communities.
- Increased Resource Security: Recycling metals enhances resource security by reducing reliance on imports and promoting domestic production.
- Technological Innovation: Recycling processes often drive technological innovation, leading to more efficient and sustainable methods for recovering and reusing metals.
Types of Metal Recycling Technologies
Metal recycling is an essential process that conserves natural resources, reduces pollution, and promotes sustainable practices. The technology used in metal recycling varies depending on the type of metal, its form, and the desired end product. This section delves into the different types of metal recycling technologies, exploring their principles, applications, advantages, and disadvantages.
Mechanical Recycling Technologies
Mechanical recycling technologies are the most common and widely used methods for recovering metals from scrap. These technologies involve physical processes that separate and purify metals from other materials.
- Sorting and Shredding: This initial stage involves sorting the scrap metal based on its type and size. Shredders then break down large pieces of scrap into smaller, more manageable sizes. This process enhances the efficiency of subsequent recycling steps.
- Magnetic Separation: This technique exploits the magnetic properties of ferrous metals like iron and steel. Powerful magnets are used to separate ferrous metals from non-ferrous metals, such as aluminum and copper.
- Eddy Current Separation: This method uses electromagnetic fields to separate non-ferrous metals based on their conductivity. Eddy currents are induced in conductive materials, causing them to be repelled by the magnetic field, thus separating them from non-conductive materials.
Pyrometallurgical Recycling Technologies
Pyrometallurgical recycling involves using high temperatures to extract metals from their ores or scrap. These technologies rely on chemical reactions and physical processes to refine and purify metals.
- Smelting: This process involves melting scrap metal and adding fluxes to remove impurities. The molten metal is then poured into molds to solidify into ingots or other shapes.
- Refining: This step further purifies the molten metal by removing remaining impurities. Various refining techniques, such as electrolysis or vacuum refining, are used depending on the metal type and desired purity level.
Hydrometallurgical Recycling Technologies
Hydrometallurgical recycling involves using aqueous solutions to dissolve and extract metals from their ores or scrap. This technology relies on chemical reactions and leaching processes to separate metals from other materials.
- Leaching: This process involves dissolving metals from their ores or scrap using a suitable chemical solution, such as acids or bases. The dissolved metals are then extracted from the solution using various techniques, such as precipitation or solvent extraction.
- Electrolysis: This technique uses an electric current to deposit metals from a solution onto an electrode. This process is commonly used to recover precious metals, such as gold and silver, from electronic waste or other sources.
Biometallurgical Recycling Technologies
Biometallurgical recycling utilizes microorganisms to extract metals from their ores or scrap. This technology leverages the metabolic processes of certain bacteria and fungi to dissolve and recover metals.
- Bioleaching: This process involves using microorganisms to oxidize and dissolve metals from their ores or scrap. The microorganisms release acids or other chemicals that react with the metal, forming soluble metal ions that can be extracted.
- Biosorption: This technique involves using microorganisms to absorb and accumulate metals from solutions. The microorganisms can then be separated from the solution and the metals can be recovered from the biomass.
Recycling Technologies for Specific Metals
- Aluminum Recycling: Aluminum recycling typically involves mechanical processes, such as sorting, shredding, and melting. Aluminum is highly recyclable, and the process requires significantly less energy than producing aluminum from bauxite ore.
- Steel Recycling: Steel recycling also relies on mechanical processes, such as sorting, shredding, and melting. Steel scrap is often used as a raw material in steelmaking, reducing the need for virgin iron ore.
- Copper Recycling: Copper recycling can involve mechanical, pyrometallurgical, and hydrometallurgical processes. Copper scrap is often processed through smelting and refining to recover high-purity copper.
- Precious Metals Recycling: Precious metals, such as gold, silver, and platinum, are often recycled from electronic waste, jewelry, and other sources. Hydrometallurgical and pyrometallurgical processes are commonly used to recover these valuable metals.
Mechanical Recycling Technologies: Metal Recycling Technologies
Mechanical recycling technologies are a cornerstone of metal recycling, relying on physical processes to separate, sort, and prepare metals for reuse. These technologies are essential for transforming scrap metal into valuable resources, minimizing waste, and reducing the environmental impact of metal production.
Metal Separation and Sorting
Metal separation and sorting are crucial steps in mechanical recycling, ensuring that different metal types are processed efficiently and effectively.
- Magnetic Separation: This process utilizes magnets to separate ferrous metals (iron, steel) from non-ferrous metals. Powerful electromagnets are used to attract and collect ferrous materials, leaving non-ferrous metals behind. This technique is commonly employed in recycling facilities to separate steel cans from aluminum cans.
- Eddy Current Separation: This method exploits the principle of electromagnetic induction to separate non-ferrous metals based on their conductivity. A rotating magnetic field induces eddy currents in conductive materials, creating a repulsive force that propels the non-ferrous metals away from the magnetic field. This technique is particularly effective for separating aluminum, copper, and brass from other materials.
- Density Separation: This technique utilizes differences in density to separate metals. A common method is air classification, where a stream of air is used to separate lighter materials from heavier ones. This process is effective for separating aluminum cans from heavier materials like steel cans.
- Optical Sorting: Advanced optical sorting systems use cameras and sensors to identify and separate different metal types based on their color, shape, and other visual characteristics. This technology is particularly useful for separating mixed metal scrap, allowing for precise sorting and recovery of valuable materials.
Metal Shredding
Metal shredding is a critical process in mechanical recycling, reducing the size of scrap metal to facilitate further processing and transportation.
- Shredders: These machines use rotating blades to cut and tear metal scrap into smaller pieces, typically called “shred” or “fluff.” Shredders are designed to handle various types of scrap, including automobiles, appliances, and industrial scrap. They can reduce the volume of scrap significantly, making it easier to transport and handle.
- Types of Shredders: Shredders are available in various sizes and configurations to accommodate different types and volumes of scrap. Some common types include hammer mills, shear shredders, and single-shaft shredders.
- Benefits of Shredding: Shredding offers several benefits in metal recycling. It reduces the volume of scrap, making it easier to handle and transport. It also exposes more surface area, facilitating further processing and separation. Additionally, shredding can break down complex scrap into smaller pieces, making it easier to recover valuable metals.
Metal Compaction
Metal compaction is a process that reduces the volume of scrap metal, making it more efficient to transport and store.
- Baling: Baling is a common method of metal compaction, using hydraulic presses to compress scrap metal into rectangular blocks, known as bales. Bales are easier to handle, transport, and store than loose scrap, reducing transportation costs and storage space requirements.
- Compactors: Compactors are machines that use mechanical force to reduce the volume of scrap metal. They are often used in industrial settings to compress scrap metal generated during manufacturing processes.
- Benefits of Compaction: Compaction significantly reduces the volume of scrap metal, making it more efficient to transport and store. It also increases the density of scrap, making it more valuable for downstream processing.
Mechanical Recycling Technologies: Applications and Limitations
Technology | Applications | Limitations |
---|---|---|
Magnetic Separation | Separating ferrous metals (iron, steel) from non-ferrous metals in mixed scrap | Not effective for separating non-ferrous metals |
Eddy Current Separation | Separating non-ferrous metals (aluminum, copper, brass) from other materials | May not be effective for separating metals with similar conductivity |
Density Separation | Separating materials based on their density, such as aluminum cans from heavier materials | May not be effective for separating materials with similar densities |
Optical Sorting | Separating mixed metal scrap based on color, shape, and other visual characteristics | May not be effective for separating materials with similar visual properties |
Shredding | Reducing the size of scrap metal to facilitate further processing and transportation | Can generate dust and noise |
Compaction (Baling) | Reducing the volume of scrap metal for efficient transport and storage | May not be suitable for all types of scrap metal |
Pyrometallurgical Recycling Technologies
Pyrometallurgical recycling is a high-temperature process that uses heat and chemical reactions to extract and purify metals from various sources. This technology is particularly well-suited for recycling complex metal mixtures, such as those found in electronic waste and scrap metal.
Smelting
Smelting is the first step in pyrometallurgical recycling, involving the melting and separation of metals from their ores or other materials. This process is typically carried out in furnaces at high temperatures, ranging from 1000 to 1600°C. The heat breaks down the chemical bonds holding the metals and impurities together, allowing the metals to melt and separate from the waste materials.
Refining
Refining is the process of removing impurities from the molten metal after smelting. This process aims to produce high-purity metals, suitable for various applications. Refining techniques vary depending on the metal being processed and the desired purity level. Common methods include:
- Electrolytic refining: This method uses an electric current to separate impurities from the molten metal. It is commonly used to refine copper, gold, and silver.
- Vacuum refining: This method involves removing impurities by heating the metal in a vacuum. It is often used to refine metals like titanium and zirconium.
- Fire refining: This method involves oxidizing impurities by reacting them with air or oxygen at high temperatures. It is commonly used to refine lead and tin.
Alloying
Alloying involves combining different metals to create new materials with specific properties. This process can be used to improve the strength, hardness, corrosion resistance, or other characteristics of metals. Alloying is often a final step in pyrometallurgical recycling, where the purified metals are combined to create specific alloys.
Environmental Considerations
While pyrometallurgical recycling offers advantages in terms of metal recovery, it also presents environmental challenges:
- Air pollution: Smelting and refining processes can release harmful gases and particulate matter into the atmosphere, contributing to air pollution and respiratory problems.
- Water pollution: Wastewater from pyrometallurgical processes can contain heavy metals and other toxic substances, posing a risk to water quality and aquatic life.
- Greenhouse gas emissions: The high temperatures involved in pyrometallurgical recycling require significant energy input, leading to greenhouse gas emissions.
Hydrometallurgical Recycling Technologies
Hydrometallurgical recycling is a crucial process in recovering valuable metals from various sources, including electronic waste, mining residues, and industrial byproducts. This method utilizes aqueous solutions to dissolve and extract metals, offering an environmentally friendly alternative to traditional pyrometallurgical processes.
Principles and Processes
Hydrometallurgical recycling involves a series of chemical and physical processes to extract metals from their sources. The core principle is the selective dissolution of metals using appropriate chemical reagents, followed by separation and purification techniques. This method relies on the differences in chemical reactivity and solubility of various metals in specific solutions.
The primary steps involved in hydrometallurgical recycling include:
* Leaching: This is the initial stage where the metal-containing material is contacted with a suitable leaching solution to dissolve the desired metals. The leaching solution can be acidic, alkaline, or a combination of both, depending on the specific metals being targeted.
* Solvent Extraction: After leaching, the metal-containing solution is treated with a solvent that selectively extracts the desired metals. This process separates the target metals from impurities and other metals present in the solution.
* Electrowinning: This step involves the recovery of the extracted metals in their pure form using an electrolytic process. The metal ions in the solution are reduced at the cathode, resulting in the deposition of pure metal.
Leaching in Hydrometallurgical Recycling
Leaching is a fundamental step in hydrometallurgical recycling, involving the dissolution of metals from their sources using a suitable chemical reagent. This process is highly selective, targeting specific metals based on their chemical reactivity and solubility in the leaching solution. The effectiveness of leaching depends on factors such as:
* Chemical Composition of the Leaching Solution: The choice of leaching solution is crucial for dissolving the desired metals while minimizing the dissolution of unwanted components. For instance, acidic solutions are often used for leaching copper, zinc, and nickel, while alkaline solutions are employed for aluminum and gold.
* Temperature and Pressure: Higher temperatures and pressures generally accelerate the leaching process, increasing the rate of metal dissolution.
* Particle Size of the Feed Material: Smaller particle sizes provide a larger surface area for contact with the leaching solution, enhancing the dissolution rate.
* Agitation: Stirring or agitation of the leaching solution helps ensure good contact between the solution and the feed material, promoting efficient metal dissolution.
Solvent Extraction in Hydrometallurgical Recycling
Solvent extraction plays a crucial role in separating and purifying the desired metals from the leaching solution. This process utilizes an organic solvent that selectively extracts the target metal ions from the aqueous solution. The choice of solvent is based on its ability to form stable complexes with the metal ions, resulting in their transfer from the aqueous phase to the organic phase.
The effectiveness of solvent extraction depends on factors such as:
* Choice of Solvent: The solvent must be compatible with the target metal ions and have a high selectivity for them.
* pH of the Aqueous Solution: The pH of the aqueous solution influences the formation of metal complexes and the distribution of metal ions between the aqueous and organic phases.
* Temperature: Temperature can affect the solubility of metal complexes in the solvent and the rate of extraction.
* Contact Time: Sufficient contact time between the aqueous and organic phases is necessary for efficient metal extraction.
Electrowinning in Hydrometallurgical Recycling
Electrowinning is the final step in hydrometallurgical recycling, where the extracted metal ions are reduced to their pure metallic form. This process involves passing an electric current through an electrolytic cell containing the metal-containing solution. The metal ions migrate towards the cathode, where they gain electrons and are deposited as pure metal.
The effectiveness of electrowinning depends on factors such as:
* Current Density: The current density applied to the cell influences the rate of metal deposition. Higher current densities generally result in faster deposition but can lead to lower purity.
* Electrolyte Composition: The composition of the electrolyte solution affects the efficiency of metal deposition.
* Temperature: Temperature can influence the rate of metal deposition and the quality of the deposited metal.
* Cathode Material: The choice of cathode material can affect the purity and quality of the deposited metal.
Comparison of Hydrometallurgical and Pyrometallurgical Recycling
Hydrometallurgical and pyrometallurgical recycling are two primary methods for metal recovery, each with its own advantages and disadvantages.
Feature | Hydrometallurgical Recycling | Pyrometallurgical Recycling |
---|---|---|
Process Temperature | Lower temperatures (ambient to 100°C) | High temperatures (above 1000°C) |
Energy Consumption | Lower energy consumption | Higher energy consumption |
Environmental Impact | Generally lower environmental impact | Potential for air and water pollution |
Metal Recovery Efficiency | High recovery efficiency for certain metals | Can be lower for certain metals |
Flexibility | More flexible for processing complex materials | Less flexible for complex materials |
Hydrometallurgical recycling is often favored for its lower energy consumption, reduced environmental impact, and high recovery efficiency for certain metals. However, it may not be suitable for all metal types and can be more complex for processing complex materials. Pyrometallurgical recycling, on the other hand, is typically more energy-intensive and can have a higher environmental impact, but it can be more effective for processing certain metal types.
Examples of Hydrometallurgical Recycling Applications
Hydrometallurgical recycling finds wide application in various industries, including:
* Electronic Waste Recycling: Hydrometallurgical processes are commonly used to recover valuable metals such as gold, silver, copper, and platinum from electronic waste, contributing to responsible e-waste management.
* Mining Residues: Hydrometallurgical methods are employed to extract valuable metals from mining residues, minimizing waste generation and maximizing resource recovery.
* Industrial Byproducts: Hydrometallurgical recycling can be used to recover valuable metals from industrial byproducts, reducing waste and promoting sustainable practices.
* Battery Recycling: Hydrometallurgical processes are vital for recycling lithium-ion batteries, enabling the recovery of critical metals like lithium, cobalt, and nickel for reuse.
Emerging Metal Recycling Technologies
Metal recycling is a crucial aspect of sustainable development, and the industry is continuously evolving to meet the growing demand for recycled materials and reduce environmental impact. Emerging technologies are playing a significant role in enhancing metal recycling processes, making them more efficient, cost-effective, and environmentally friendly. These innovations address challenges associated with traditional methods, opening new possibilities for resource recovery and circular economy practices.
Bioleaching, Metal recycling technologies
Bioleaching is a promising technology that utilizes microorganisms to extract metals from complex ores and industrial wastes. This process involves the use of bacteria or fungi that can oxidize metal sulfides, releasing metal ions into solution. The metal ions can then be recovered using various techniques, such as precipitation or electrolysis.
Bioleaching offers several advantages over traditional methods, such as:
- Lower energy consumption
- Reduced environmental impact
- Ability to process low-grade ores and complex materials
However, bioleaching also presents some challenges, including:
- Slower reaction rates compared to traditional methods
- Potential for contamination of the leachate
- Requirement for specific environmental conditions
Plasma Arc Melting
Plasma arc melting (PAM) is a high-temperature melting process that utilizes a plasma arc to melt and refine metals. This technology can be applied to recycle various metal scrap, including electronic waste and other complex materials. The high temperatures generated by the plasma arc allow for the separation of metals from non-metallic components and the removal of impurities.
PAM offers several advantages, such as:
- High melting efficiency
- Ability to process complex materials
- Reduced emissions compared to traditional smelting processes
However, PAM also has some limitations, including:
- High energy consumption
- Potential for dust and fume emissions
- Limited capacity for processing large volumes of materials
Selective Laser Melting
Selective laser melting (SLM) is an additive manufacturing process that uses a laser to melt and fuse powdered metal materials layer by layer. This technology can be used to create complex metal parts with high precision and intricate designs. SLM has the potential to revolutionize metal recycling by enabling the creation of new products from recycled materials.
SLM offers several advantages, such as:
- High material utilization efficiency
- Ability to create complex geometries
- Reduced waste generation
However, SLM also presents some challenges, including:
- High cost of equipment and materials
- Limited production scale
- Potential for porosity and other defects
Comparison of Traditional and Emerging Metal Recycling Technologies
Technology | Advantages | Disadvantages |
---|---|---|
Traditional Smelting | High throughput, well-established technology | High energy consumption, environmental impact |
Bioleaching | Lower energy consumption, environmentally friendly | Slow reaction rates, potential for contamination |
Plasma Arc Melting | High melting efficiency, ability to process complex materials | High energy consumption, potential for emissions |
Selective Laser Melting | High material utilization, ability to create complex geometries | High cost, limited production scale |
Metal Recycling Industry Trends
The metal recycling industry is undergoing a significant transformation, driven by a confluence of factors, including technological advancements, environmental regulations, and evolving market demand. These forces are shaping the industry’s trajectory and presenting both challenges and opportunities for stakeholders.
Technological Advancements
Technological advancements are playing a pivotal role in driving the growth and efficiency of the metal recycling industry. New technologies are enabling more effective metal separation, sorting, and processing, leading to higher recovery rates and reduced environmental impact.
- Advanced Sorting Technologies: The development of advanced sorting technologies, such as X-ray fluorescence (XRF) and near-infrared (NIR) spectroscopy, has significantly enhanced the ability to identify and separate different types of metals with high accuracy. These technologies are enabling more efficient recovery of valuable metals from complex scrap streams.
- Robotics and Automation: The integration of robotics and automation in metal recycling facilities is increasing efficiency and productivity while reducing labor costs and improving safety. Automated sorting systems and robotic arms are being deployed to handle heavy and hazardous materials, minimizing human exposure to risks.
- Digitalization and Data Analytics: The use of digital technologies, such as sensors, Internet of Things (IoT) devices, and data analytics platforms, is enabling real-time monitoring of metal recycling operations. This data can be used to optimize processes, improve resource utilization, and track environmental performance.
Environmental Regulations
Stringent environmental regulations are driving the adoption of sustainable practices in the metal recycling industry. Governments worldwide are implementing policies to reduce waste generation, promote resource recovery, and minimize environmental pollution.
- Extended Producer Responsibility (EPR): EPR schemes hold producers responsible for the end-of-life management of their products, including recycling. This incentivizes manufacturers to design products for recyclability and encourages consumers to recycle. The implementation of EPR has significantly increased the volume of scrap metal available for recycling.
- Waste Management Regulations: Regulations on waste management and disposal are pushing industries to prioritize recycling over landfilling. These regulations are making metal recycling more attractive by reducing the cost of disposal and increasing the value of recyclable materials.
- Carbon Emission Targets: Governments are setting ambitious carbon emission reduction targets, and metal recycling plays a significant role in achieving these goals. Recycling metals requires significantly less energy than producing them from virgin materials, reducing greenhouse gas emissions and promoting a circular economy.
Market Demand
The growing demand for metals, driven by factors such as urbanization, industrialization, and technological advancements, is fueling the growth of the metal recycling industry. The increasing demand for recycled metals is creating a robust market for scrap metal, incentivizing recycling efforts.
- Demand for Recycled Metals: The demand for recycled metals is increasing due to the growing awareness of environmental sustainability and the rising cost of virgin materials. Recycled metals offer a cost-effective and environmentally friendly alternative to virgin materials, making them attractive to manufacturers and consumers.
- Emerging Applications: The development of new technologies and applications, such as electric vehicles, renewable energy systems, and advanced electronics, is driving demand for specific metals, including copper, aluminum, and lithium. Recycling these metals is essential to meet the growing demand while minimizing environmental impact.
- Metal Price Fluctuations: Metal prices are subject to fluctuations influenced by factors such as global economic conditions, supply and demand dynamics, and geopolitical events. These price fluctuations can create opportunities for metal recyclers to profit from market arbitrage and capitalize on price differentials between virgin and recycled metals.
Case Studies of Successful Metal Recycling Initiatives
Successful metal recycling initiatives demonstrate the effectiveness of various strategies and technologies in achieving environmental and economic benefits. These initiatives provide valuable insights into best practices and lessons learned, guiding future efforts towards sustainable metal management.
Examples of Successful Metal Recycling Projects
This section explores notable examples of successful metal recycling projects worldwide, showcasing their strategies, technologies, and outcomes.
- The Aluminum Recycling Initiative in the United States: This initiative, launched in the 1970s, has significantly increased aluminum recycling rates through public awareness campaigns, infrastructure development, and economic incentives. The program has resulted in a substantial reduction in aluminum production, leading to significant energy savings and decreased greenhouse gas emissions.
- The Electronic Waste Recycling Program in Japan: Japan’s stringent regulations and well-established recycling infrastructure have led to high rates of electronic waste recycling. The program involves a comprehensive system of collection, sorting, and processing, ensuring the recovery of valuable metals like gold, silver, and copper.
- The Copper Recycling Project in Chile: Chile’s copper mining industry has implemented a successful recycling program, utilizing advanced technologies to recover copper from discarded products and industrial waste. The program has significantly extended the lifespan of copper resources, reducing the environmental impact of mining operations.
Strategies and Technologies Employed in Successful Metal Recycling Initiatives
Successful metal recycling initiatives often employ a combination of strategies and technologies to maximize recovery rates and minimize environmental impact.
- Public Awareness and Education: Raising public awareness about the importance of metal recycling and providing clear guidelines for proper waste disposal are crucial for increasing participation and promoting sustainable practices.
- Infrastructure Development: Establishing efficient collection and sorting systems, as well as advanced processing facilities, are essential for managing large volumes of recyclable materials effectively.
- Economic Incentives: Offering financial incentives for recycling, such as deposit-return schemes or tax breaks, can encourage individuals and businesses to participate in recycling programs.
- Technological Advancements: The use of innovative technologies, such as automated sorting systems, advanced metal extraction techniques, and closed-loop recycling processes, can enhance efficiency and recovery rates.
Outcomes and Lessons Learned from Successful Metal Recycling Initiatives
The success of metal recycling initiatives can be measured by their environmental and economic impacts.
- Reduced Environmental Impact: Recycling metals significantly reduces the need for virgin material extraction, minimizing the environmental damage associated with mining and processing. This includes reduced greenhouse gas emissions, land disturbance, and water pollution.
- Economic Benefits: Metal recycling creates jobs, stimulates economic growth, and provides a valuable source of secondary raw materials. It also reduces dependence on imported materials, strengthening national economies.
- Resource Conservation: By extending the lifespan of valuable metals, recycling helps conserve finite natural resources and promotes sustainable development. This is particularly important for metals like copper, aluminum, and steel, which are essential for various industries.
Best Practices for Successful Metal Recycling Initiatives
Based on the experiences of successful initiatives, several best practices can be identified for future metal recycling efforts.
- Strong Policy Framework: Implementing clear and comprehensive policies that support metal recycling, including regulations, incentives, and funding mechanisms, is crucial for creating a favorable environment for recycling.
- Collaborative Partnerships: Fostering partnerships between government agencies, industry stakeholders, and research institutions can leverage expertise, resources, and innovation to enhance recycling efforts.
- Continuous Innovation: Investing in research and development to advance metal recycling technologies, such as automated sorting systems, advanced metal extraction techniques, and closed-loop recycling processes, is essential for improving efficiency and recovery rates.
- Public Engagement: Engaging the public through awareness campaigns, education programs, and community outreach initiatives can promote a culture of recycling and encourage active participation.
End of Discussion
Metal recycling technologies offer a promising path towards a more sustainable future. By embracing innovative solutions, optimizing existing processes, and fostering collaboration within the industry, we can unlock the full potential of metal recycling and create a world where resources are valued and reused. The future of metal recycling is bright, promising a circular economy that benefits both the environment and society.
Metal recycling technologies are constantly evolving to meet the growing demand for sustainable solutions. One key area of innovation is in the development of advanced sorting and processing equipment, such as those offered by tuan technology products. These technologies enable efficient separation of different metal types, leading to higher purity and value recovery.
This, in turn, fuels the circular economy by reducing reliance on virgin materials and minimizing environmental impact.