Metal Recycling Technologies: Sustainable Solutions
Metal recycling technologies are at the forefront of sustainable practices, offering a powerful alternative to extracting new metals from the earth. By reusing and repurposing metals, we not only conserve […]
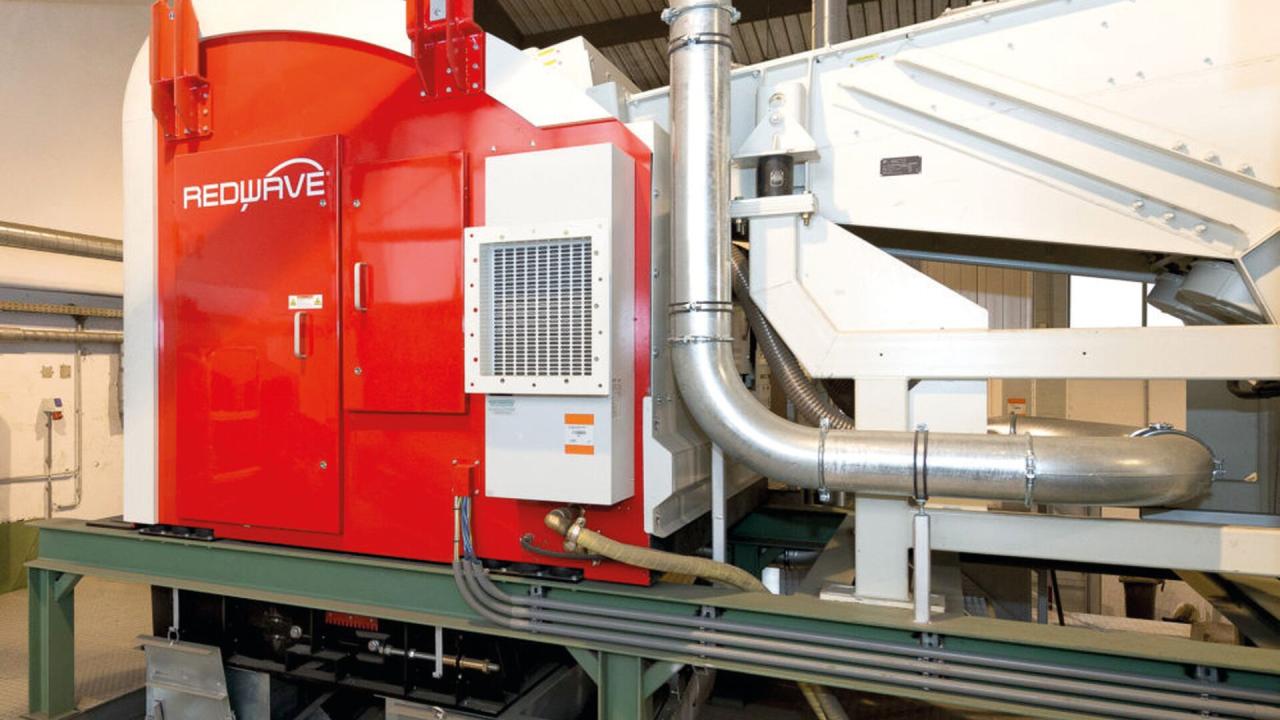
Metal recycling technologies are at the forefront of sustainable practices, offering a powerful alternative to extracting new metals from the earth. By reusing and repurposing metals, we not only conserve precious resources but also reduce the environmental impact of mining and manufacturing. The economic benefits are significant, with cost savings and job creation in the recycling sector, making it a win-win for both the environment and the economy.
This article delves into the diverse world of metal recycling technologies, exploring the different processes, innovations, and applications that are transforming the way we manage and utilize metals. From traditional methods to cutting-edge advancements, we’ll uncover the fascinating journey of metal recycling and its vital role in building a more sustainable future.
Introduction to Metal Recycling
Metal recycling is the process of collecting and reprocessing used metal materials into new products. It is a crucial practice for promoting sustainability and mitigating environmental impacts. Metal recycling plays a vital role in reducing the need for virgin metal extraction, which has significant environmental and economic implications.
Environmental Benefits of Metal Recycling
Metal recycling offers numerous environmental advantages compared to extracting new metals. Recycling metals significantly reduces the need for mining, which is a resource-intensive process with substantial environmental consequences. Mining operations often involve deforestation, habitat destruction, and soil and water contamination. Moreover, the extraction and refining of virgin metals require substantial energy consumption, leading to greenhouse gas emissions.
Recycling metals helps conserve natural resources by reducing the demand for virgin metals. For instance, recycling aluminum requires only 5% of the energy needed to produce aluminum from bauxite ore. This energy saving translates into reduced greenhouse gas emissions and a smaller carbon footprint. Furthermore, metal recycling minimizes the generation of waste materials. Recycling aluminum cans, for example, prevents the accumulation of landfill waste and reduces the need for new landfills.
Economic Benefits of Metal Recycling
Metal recycling provides significant economic benefits, contributing to cost savings and job creation. Recycling metals is often more cost-effective than extracting new metals. The cost savings are primarily due to the reduced energy consumption and material costs associated with recycling. For example, recycling steel can save up to 74% of the energy required to produce steel from iron ore.
Metal recycling generates numerous job opportunities in various sectors, including collection, processing, and manufacturing. The recycling industry creates jobs in areas such as sorting, cleaning, and reprocessing metal materials. Additionally, recycling operations stimulate economic activity in local communities by providing raw materials for manufacturing industries.
Metal Recycling Processes
Metal recycling is a crucial aspect of sustainable resource management, playing a significant role in reducing the environmental impact of manufacturing and construction. The process involves several stages, each with its own set of challenges and innovations.
Collection and Sorting
The first step in metal recycling is the collection and sorting of scrap metal. This can be done through various channels, including curbside pickup, drop-off centers, and industrial scrap collection. Once collected, the scrap metal is sorted based on its type, composition, and quality.
- Manual Sorting: This traditional method involves human workers inspecting and categorizing the scrap metal. This process can be labor-intensive and prone to errors, especially when dealing with large volumes of mixed materials.
- Automated Sorting: Advances in technology have led to the development of automated sorting systems that utilize various techniques, such as eddy current separation, magnetic separation, and optical sorting. These systems can efficiently and accurately separate different types of metal based on their physical and magnetic properties. For example, eddy current separators use electromagnetic fields to separate non-ferrous metals like aluminum from ferrous metals like steel. Optical sorting systems use cameras and sensors to identify different metals based on their color, shape, and size.
Pre-treatment, Metal recycling technologies
Once the scrap metal is sorted, it often requires pre-treatment to prepare it for further processing. This stage typically involves shredding, crushing, and other processes to reduce the size and bulk of the scrap metal.
- Shredding: Shredders are used to break down large pieces of scrap metal into smaller, more manageable pieces. This process is particularly important for bulky items like cars and appliances. Shredders are equipped with powerful rotating blades that can cut through metal with ease. Some shredders are designed to separate ferrous and non-ferrous metals during the shredding process.
- Crushing: Crushing is used to further reduce the size of shredded metal or other scrap materials. Crushers use heavy jaws or rollers to compress and break down the metal. This process helps to reduce the volume of the scrap metal and make it easier to handle.
Separation and Purification
After pre-treatment, the scrap metal needs to be separated and purified to remove impurities and contaminants. This step is essential to ensure the quality of the recycled metal.
- Magnetic Separation: This method is used to separate ferrous metals from non-ferrous metals. A strong magnet is used to attract the ferrous metals, leaving the non-ferrous metals behind.
- Density Separation: This method is used to separate metals based on their density. A slurry of water and scrap metal is fed into a rotating drum. The heavier metals settle to the bottom of the drum, while the lighter metals are discharged at the top.
- Chemical Separation: This method involves using chemical processes to remove impurities from the scrap metal. For example, molten metal can be treated with chemicals to remove unwanted elements like sulfur or phosphorus.
Melting and Refining
The final stage of metal recycling is melting and refining. The scrap metal is melted in a furnace and then refined to remove any remaining impurities.
- Melting: Scrap metal is melted in a furnace, typically using electric arc furnaces or induction furnaces. These furnaces generate high temperatures that melt the metal, allowing it to be poured into molds or used in other manufacturing processes.
- Refining: Once the metal is melted, it is refined to remove any remaining impurities. This can be done using various techniques, such as vacuum degassing, ladle refining, or continuous casting. Refining processes can improve the quality of the recycled metal and ensure it meets specific standards for use in various applications.
Summary: Metal Recycling Technologies
As we move towards a circular economy, metal recycling technologies will play an increasingly crucial role in ensuring a sustainable future. The continuous development and implementation of these technologies will not only reduce our reliance on virgin materials but also create a more efficient and environmentally responsible approach to metal production and consumption. By embracing innovation and collaboration, we can unlock the full potential of metal recycling and pave the way for a more sustainable and prosperous world.
Metal recycling technologies are constantly evolving, driven by the need for sustainable practices and resource recovery. Companies like blue owl technology finance corp. play a crucial role in supporting this sector by providing financial solutions and fostering innovation. These technologies are essential for minimizing waste, reducing environmental impact, and creating a circular economy for valuable metals.