International Welding Technologies: Shaping the Future of Manufacturing
International welding technologies take center stage as a critical force in shaping the future of manufacturing. From the ancient art of forging to modern marvels of laser welding, the evolution […]
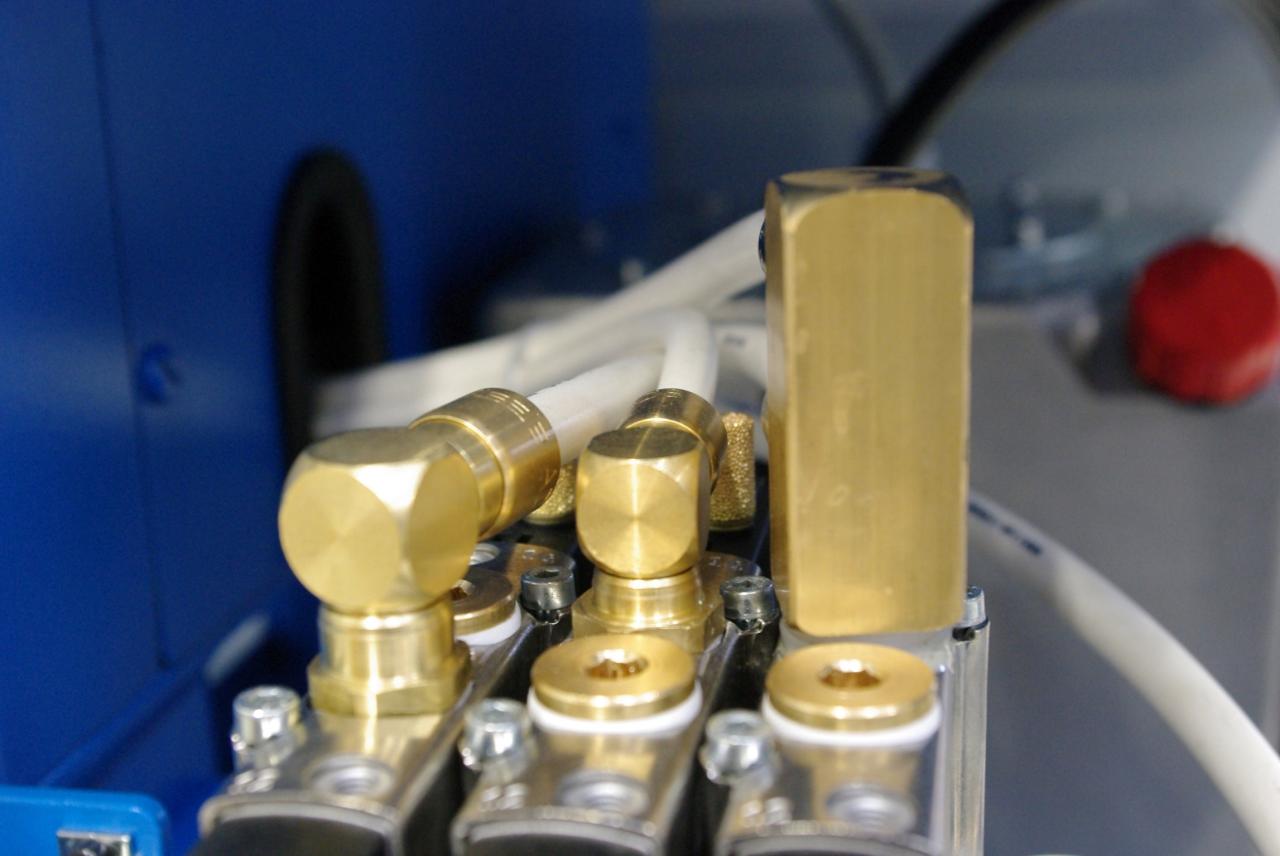
International welding technologies take center stage as a critical force in shaping the future of manufacturing. From the ancient art of forging to modern marvels of laser welding, the evolution of welding has been a testament to human ingenuity. Today, welding techniques are integral to a vast array of industries, connecting everything from skyscrapers to spacecraft.
This exploration delves into the fascinating world of international welding, examining its historical roots, current trends, and future prospects. We will uncover the intricate dance between science, engineering, and artistry that defines this essential field.
Evolution of Welding Technologies
Welding, the process of joining materials by melting them together, has been a fundamental skill in human civilization for millennia. From ancient blacksmiths to modern industrial giants, welding technology has evolved significantly, shaping the world around us. This evolution is a testament to human ingenuity and the relentless pursuit of efficiency, quality, and innovation.
Historical Development of Welding
The earliest forms of welding can be traced back to ancient civilizations. Egyptians used rudimentary forms of forge welding to create tools and weapons, while the Romans employed brazing techniques for joining metal objects. These early methods, often reliant on heat and hammering, laid the foundation for the development of more sophisticated welding techniques.
- Forge Welding: This ancient method involved heating two pieces of metal to a high temperature and then hammering them together, forcing out impurities and creating a bond.
- Brazing: This technique, dating back to the Roman era, involved using a filler metal with a lower melting point than the base metals to join them. The filler metal flowed into the gap between the pieces, creating a strong bond.
Key Milestones and Breakthroughs, International welding technologies
The 19th century saw significant advancements in welding technology. The invention of the oxyacetylene torch in 1903 revolutionized welding, providing a portable and controllable heat source. This invention paved the way for the development of various welding processes, including gas metal arc welding (GMAW) and shielded metal arc welding (SMAW), which are still widely used today.
- Oxyacetylene Welding: This process utilizes a mixture of oxygen and acetylene gas to generate a high-temperature flame, melting the base metals and the filler material to create a weld.
- Gas Metal Arc Welding (GMAW): This process, also known as MIG welding, utilizes a continuous wire electrode that is fed into the weld pool, melting both the electrode and the base metals.
- Shielded Metal Arc Welding (SMAW): This process, also known as stick welding, uses a coated electrode that melts and releases shielding gas, protecting the weld pool from atmospheric contamination.
Comparison of Traditional and Modern Welding Techniques
Modern welding techniques, building upon the foundations laid by their predecessors, have introduced automation, precision, and efficiency to the welding process. These advancements have enabled the creation of complex structures and intricate designs, previously unimaginable.
- Automation: Robots and automated welding systems have significantly increased productivity and repeatability in welding, reducing human error and fatigue.
- Precision: Laser welding and electron beam welding offer unparalleled precision, allowing for the creation of intricate welds with minimal heat distortion.
- Efficiency: Modern welding techniques, such as plasma arc welding and friction stir welding, offer higher welding speeds and reduced energy consumption, enhancing efficiency and sustainability.
International Standards and Regulations
The global nature of welding necessitates a standardized approach to ensure safety, quality, and consistency across projects and borders. International organizations play a crucial role in establishing and promoting these standards, ensuring a common understanding and implementation of best practices.
International Organizations and Standards
International organizations like the International Organization for Standardization (ISO) and the American Welding Society (AWS) are key players in shaping the global welding landscape. These organizations develop and publish comprehensive standards covering various aspects of welding, including:
- Welding processes: These standards specify the requirements and procedures for different welding processes, such as gas metal arc welding (GMAW), shielded metal arc welding (SMAW), and tungsten inert gas welding (TIG).
- Welding materials: Standards define the properties and requirements of welding consumables, such as electrodes, wires, and fluxes, ensuring compatibility and performance in different applications.
- Welding qualifications: Standards establish the criteria for welder qualification and certification, ensuring that welders possess the necessary skills and knowledge to perform safe and quality welding.
- Quality control: Standards Artikel the procedures for inspecting and testing welds to ensure they meet the required specifications and are free from defects.
Safety Protocols and Regulations
Safety is paramount in welding, and international regulations are crucial for protecting welders and others in the workplace. These regulations address various aspects of welding safety, including:
- Personal protective equipment (PPE): Standards mandate the use of appropriate PPE, such as welding helmets, gloves, and clothing, to minimize the risk of burns, eye damage, and other injuries.
- Workplace safety: Regulations specify the safe working environment, including ventilation, fire safety, and the proper handling of hazardous materials.
- Emergency procedures: Standards Artikel the procedures for responding to welding-related accidents and emergencies, ensuring prompt and effective action.
Impact of International Standards
International standards have a profound impact on welding practices and materials, leading to:
- Enhanced quality: Standardized procedures and materials contribute to improved weld quality, reducing defects and increasing reliability.
- Increased safety: Safety protocols and regulations ensure a safer working environment for welders and others in the vicinity.
- Global compatibility: International standards facilitate the exchange of welding products, services, and expertise across borders, promoting global collaboration and innovation.
- Reduced costs: Standardization can streamline processes, minimize rework, and reduce material waste, leading to overall cost savings.
Welding Processes and Applications
Welding is a fundamental process in various industries, playing a crucial role in joining materials to create structures, components, and products. The selection of a welding process depends on factors such as the materials being joined, the desired joint geometry, and the specific application.
Welding Processes and Their Advantages and Disadvantages
A wide array of welding processes are available, each with its unique characteristics, advantages, and disadvantages. Understanding these aspects is essential for selecting the most appropriate process for a given application.
- Shielded Metal Arc Welding (SMAW): This process uses a consumable electrode coated with flux, which melts along with the base metal, forming a protective slag covering the weld pool.
- Advantages: Relatively inexpensive, versatile, and portable, making it suitable for various applications and environments.
- Disadvantages: Produces a relatively rough weld bead, limited welding speed, and requires skilled operators.
- Gas Metal Arc Welding (GMAW): Also known as MIG welding, this process uses a continuous wire electrode fed into the weld pool, with a shielding gas protecting the molten metal.
- Advantages: High welding speed, good weld quality, and relatively easy to learn.
- Disadvantages: Requires a dedicated welding power source and shielding gas, limiting its portability.
- Gas Tungsten Arc Welding (GTAW): Also known as TIG welding, this process uses a non-consumable tungsten electrode to create an arc, with a shielding gas protecting the weld pool.
- Advantages: Produces high-quality welds with excellent control over the weld bead, suitable for precision applications.
- Disadvantages: Relatively slow welding speed, requires skilled operators, and can be expensive.
- Submerged Arc Welding (SAW): This process uses a consumable electrode submerged in a granular flux, which protects the weld pool and provides a slag cover.
- Advantages: High welding speed, excellent penetration, and good weld quality.
- Disadvantages: Requires specialized equipment, limited portability, and can be difficult to inspect.
- Resistance Welding (RW): This process uses electrical resistance to heat and fuse the materials together.
- Advantages: Fast welding speed, high production rates, and suitable for joining thin materials.
- Disadvantages: Limited to specific materials and joint types, requires specialized equipment.
- Laser Beam Welding (LBW): This process uses a high-energy laser beam to melt and fuse the materials together.
- Advantages: High precision, narrow heat-affected zone, and minimal distortion.
- Disadvantages: Expensive equipment, limited to specific materials, and requires skilled operators.
- Electron Beam Welding (EBW): This process uses a high-energy electron beam to melt and fuse the materials together.
- Advantages: High welding speed, deep penetration, and minimal heat input.
- Disadvantages: Expensive equipment, requires a vacuum environment, and limited to specific materials.
Comparison of Welding Processes
The choice of welding process depends on various factors, including material compatibility, joint type, and application. The following table summarizes the key characteristics of different welding processes:
Welding Process | Material Compatibility | Joint Type | Application |
---|---|---|---|
SMAW | Steel, stainless steel, cast iron | Butt, fillet, lap, corner | Construction, maintenance, repair |
GMAW | Steel, aluminum, stainless steel | Butt, fillet, lap, corner | Automotive, aerospace, manufacturing |
GTAW | Steel, aluminum, stainless steel, titanium | Butt, fillet, lap, corner | Aerospace, medical, electronics |
SAW | Steel, stainless steel | Butt, fillet, lap, corner | Pipelines, pressure vessels, shipbuilding |
RW | Steel, aluminum, copper | Butt, spot, seam | Automotive, appliances, electronics |
LBW | Steel, aluminum, stainless steel, titanium | Butt, fillet, lap, corner | Aerospace, medical, electronics |
EBW | Steel, aluminum, stainless steel, titanium | Butt, fillet, lap, corner | Aerospace, medical, electronics |
International Applications of Welding Techniques
Welding techniques find widespread applications in various industries worldwide, contributing to the construction, manufacturing, and repair of numerous products and structures.
- Construction: SMAW is commonly used for structural steel fabrication in buildings, bridges, and other infrastructure projects.
- Automotive: GMAW and resistance welding are extensively used in the automotive industry for manufacturing car bodies, chassis, and other components.
- Aerospace: GTAW, LBW, and EBW are employed in the aerospace industry for joining high-strength alloys used in aircraft and spacecraft construction.
- Pipelines: SAW is a preferred welding process for constructing pipelines, ensuring high-quality welds for transporting oil, gas, and other fluids.
- Medical: GTAW and LBW are used in the medical device industry for fabricating surgical instruments, implants, and other medical equipment.
Advanced Welding Technologies: International Welding Technologies
The world of welding has witnessed remarkable advancements in recent decades, driven by the pursuit of greater efficiency, precision, and the ability to join materials that were once considered impossible. These advancements have led to the development of sophisticated welding technologies that are revolutionizing industries ranging from aerospace and automotive to electronics and medical devices.
Laser Welding
Laser welding utilizes a highly focused beam of coherent light to melt and fuse materials. This process offers exceptional precision and control, allowing for the creation of narrow, deep welds with minimal heat input. The high energy density of the laser beam ensures rapid melting and solidification, resulting in reduced distortion and improved weld quality.
- Principle: Laser welding employs a high-power laser beam that is focused onto the workpiece. The concentrated energy melts the material, forming a weld pool. The laser beam can be precisely controlled to achieve intricate weld geometries.
- Applications: Laser welding is widely used in industries such as automotive, aerospace, electronics, and medical devices. Some specific applications include welding thin-gauge materials, joining dissimilar metals, and creating intricate designs.
Electron Beam Welding
Electron beam welding (EBW) utilizes a focused beam of high-energy electrons to melt and fuse materials. This process is characterized by its extremely high energy density, which allows for deep penetration and high welding speeds. The vacuum environment required for EBW eliminates atmospheric contamination and enhances weld quality.
- Principle: EBW involves generating a beam of high-energy electrons that are accelerated towards the workpiece. The electrons bombard the material, releasing their kinetic energy as heat, leading to melting and fusion.
- Applications: EBW is primarily used in high-precision applications where deep penetration and minimal heat input are essential. Examples include welding aerospace components, turbine blades, and medical implants.
Friction Stir Welding
Friction stir welding (FSW) is a solid-state welding process that utilizes a rotating tool to generate heat and plastic deformation. The tool, typically made of a non-consumable material, is inserted into the joint line and rotated, creating friction and heat. The heat softens the material, and the tool’s rotation forces the softened material to flow and intermix, forming a solid-state weld.
- Principle: FSW involves a non-consumable rotating tool that is inserted into the joint line. The tool’s rotation creates friction and heat, softening the material. The tool then forces the softened material to intermix, creating a solid-state weld.
- Applications: FSW is well-suited for joining dissimilar metals, aluminum alloys, and other materials that are difficult to weld using conventional methods. Applications include manufacturing aerospace components, automotive parts, and shipbuilding.
Comparison of Advanced Welding Technologies
Technology | Benefits | Limitations |
---|---|---|
Laser Welding |
|
|
Electron Beam Welding |
|
|
Friction Stir Welding |
|
|
Automation and Robotics in Welding
The integration of automation and robotics in welding has revolutionized the industry, offering significant benefits in terms of efficiency, quality, and safety. These technologies have become increasingly prevalent, particularly in high-volume manufacturing and demanding applications.
Benefits of Automated Welding Systems
Automated welding systems offer a range of advantages, making them attractive for diverse applications.
- Enhanced Productivity: Automated systems can operate continuously, eliminating downtime associated with human fatigue or breaks. They can also execute tasks with high precision and repeatability, resulting in increased production rates.
- Improved Weld Quality: Robots can perform welds with exceptional consistency and accuracy, reducing the likelihood of defects. This results in improved weld quality, reduced rework, and enhanced product reliability.
- Enhanced Safety: Automated welding eliminates the need for human workers to perform hazardous tasks, reducing the risk of injuries and accidents. This is particularly important in applications involving high temperatures, toxic fumes, or confined spaces.
- Reduced Labor Costs: By automating welding processes, manufacturers can reduce their reliance on skilled welders, potentially lowering labor costs and improving profitability.
- Increased Flexibility: Automated systems can be easily reprogrammed to adapt to different welding tasks, enabling manufacturers to quickly adjust to changes in production requirements.
Challenges of Implementing Automated Welding Systems
While automated welding offers numerous benefits, implementing these systems presents certain challenges:
- Initial Investment Costs: Acquiring and installing automated welding systems can be a significant capital expenditure. The cost of robots, programming software, and integration into existing production lines can be substantial.
- Programming Complexity: Programming robots for specific welding tasks can be complex and time-consuming, requiring specialized expertise and training.
- Maintenance and Support: Automated welding systems require regular maintenance and support to ensure optimal performance and reliability. This can involve specialized technicians and spare parts, adding to operational costs.
- Adaptability to Complex Geometries: While robots can perform intricate welds, they may struggle with complex geometries or intricate designs that require manual dexterity or adaptability.
- Integration with Existing Infrastructure: Integrating automated welding systems into existing production lines can be challenging, requiring careful planning and coordination to ensure seamless operation.
Impact of Robotics on International Welding Industries
The adoption of robotics has had a profound impact on international welding industries, transforming manufacturing processes and shaping the industry landscape.
- Increased Efficiency and Productivity: Robotics has enabled manufacturers to achieve significant increases in welding efficiency and productivity, allowing them to produce more products in less time. This has led to cost savings and improved competitiveness in global markets.
- Enhanced Product Quality: The precision and consistency of robotic welding have resulted in higher-quality products, reducing defects and rework, and improving customer satisfaction.
- Job Creation and Skill Development: While robotics may automate certain welding tasks, it also creates new job opportunities in areas such as robot programming, maintenance, and system integration. This has driven the demand for skilled professionals with specialized knowledge and training in robotics and automation.
- Global Competitiveness: The adoption of robotics has become a key factor in global competitiveness for welding industries. Countries and companies that invest in robotics and automation technologies are better positioned to compete in the international marketplace.
- Future Trends: The future of robotics in welding is expected to involve further advancements in artificial intelligence, machine learning, and collaborative robots (cobots). These technologies will enhance robot capabilities, improve safety, and create new opportunities for automation in the industry.
Quality Control and Inspection
Quality control and inspection are crucial aspects of welding, ensuring the structural integrity and safety of welded structures. These processes aim to identify and rectify defects, ensuring the weld meets the required specifications and standards.
Methods and Techniques for Quality Control and Inspection
Quality control in welding involves a series of methods and techniques employed at various stages of the welding process. These methods are designed to prevent defects and ensure the production of high-quality welds. Here are some commonly used methods:
- Visual Inspection: This is the most basic and widely used method, involving a visual examination of the weld for surface defects, such as cracks, porosity, and undercut. Experienced welders can often identify potential problems based on the appearance of the weld.
- Dimensional Inspection: This method checks the weld geometry, including its size, shape, and alignment, using measuring tools like calipers, micrometers, and rulers. This ensures the weld conforms to the specified dimensions.
- Radiographic Testing (RT): This technique uses X-rays or gamma rays to create images of the internal structure of the weld. It can detect internal defects like cracks, porosity, and inclusions, providing a comprehensive assessment of the weld’s integrity.
- Ultrasonic Testing (UT): This method uses high-frequency sound waves to detect internal defects. The sound waves are transmitted through the weld, and the reflections are analyzed to identify defects like cracks, voids, and laminations.
- Magnetic Particle Testing (MT): This technique applies a magnetic field to the weld and then uses fine iron particles to detect surface cracks and other defects. The particles are attracted to areas of magnetic flux leakage caused by the defects, revealing their location.
- Eddy Current Testing (ET): This method uses electromagnetic induction to detect surface and near-surface defects. An alternating current is passed through a coil, creating a magnetic field that interacts with the weld. Changes in the magnetic field caused by defects are detected, providing information about their location and size.
- Leak Testing: This method is used to check for leaks in pressure vessels and pipelines. It involves pressurizing the vessel or pipeline with a gas or liquid and then using a leak detector to identify any leaks.
Importance of Non-Destructive Testing (NDT)
Non-destructive testing (NDT) plays a crucial role in ensuring the integrity of welded structures. NDT methods allow for the inspection of welds without damaging the material. This is essential for detecting internal defects that may not be visible through visual inspection. NDT helps to:
- Prevent catastrophic failures: By identifying hidden defects, NDT helps to prevent catastrophic failures that could result in loss of life, property damage, and environmental pollution.
- Reduce repair costs: Early detection of defects through NDT allows for timely repairs, which are often less costly than repairs made after a failure has occurred.
- Ensure safety and reliability: NDT ensures that welded structures meet safety standards and are reliable for their intended use.
Latest Advancements in Quality Control Technologies
Advancements in technology have led to the development of new and improved quality control techniques in welding. These advancements have improved the accuracy, speed, and efficiency of inspection processes. Some of the latest advancements include:
- Automated NDT systems: Automated NDT systems use robots and sensors to perform inspections quickly and accurately. These systems can reduce human error and improve the consistency of inspection results.
- Advanced imaging techniques: New imaging techniques, such as digital radiography and phased array ultrasonics, provide higher resolution images and more detailed information about defects.
- Real-time monitoring systems: Real-time monitoring systems can track welding parameters and provide immediate feedback on the quality of the weld. This allows for corrective action to be taken during the welding process, reducing the likelihood of defects.
Final Review
As we conclude our journey through the world of international welding technologies, it’s clear that this field is poised for continued growth and innovation. From the intricate dance of materials science to the precision of robotic welding, the future holds exciting possibilities for transforming the way we build and connect our world.
International welding technologies are constantly evolving, driven by advancements in materials and automation. From the intricate welds used in aerospace to the robust connections found in infrastructure, welding plays a crucial role in our modern world. If you’re considering a new vehicle, the decision between the Acura RDX base and technology package might seem like a simpler choice, but you can find a detailed comparison here.
Ultimately, the choice between these two packages comes down to your individual needs and priorities, just like the selection of welding techniques depends on the specific application.