Industrial Air Technology: Keeping the Air Clean in Factories
Industrial air technology is essential for maintaining a safe and healthy working environment in factories and industrial settings. From manufacturing plants to chemical processing facilities, industries rely on advanced technologies […]
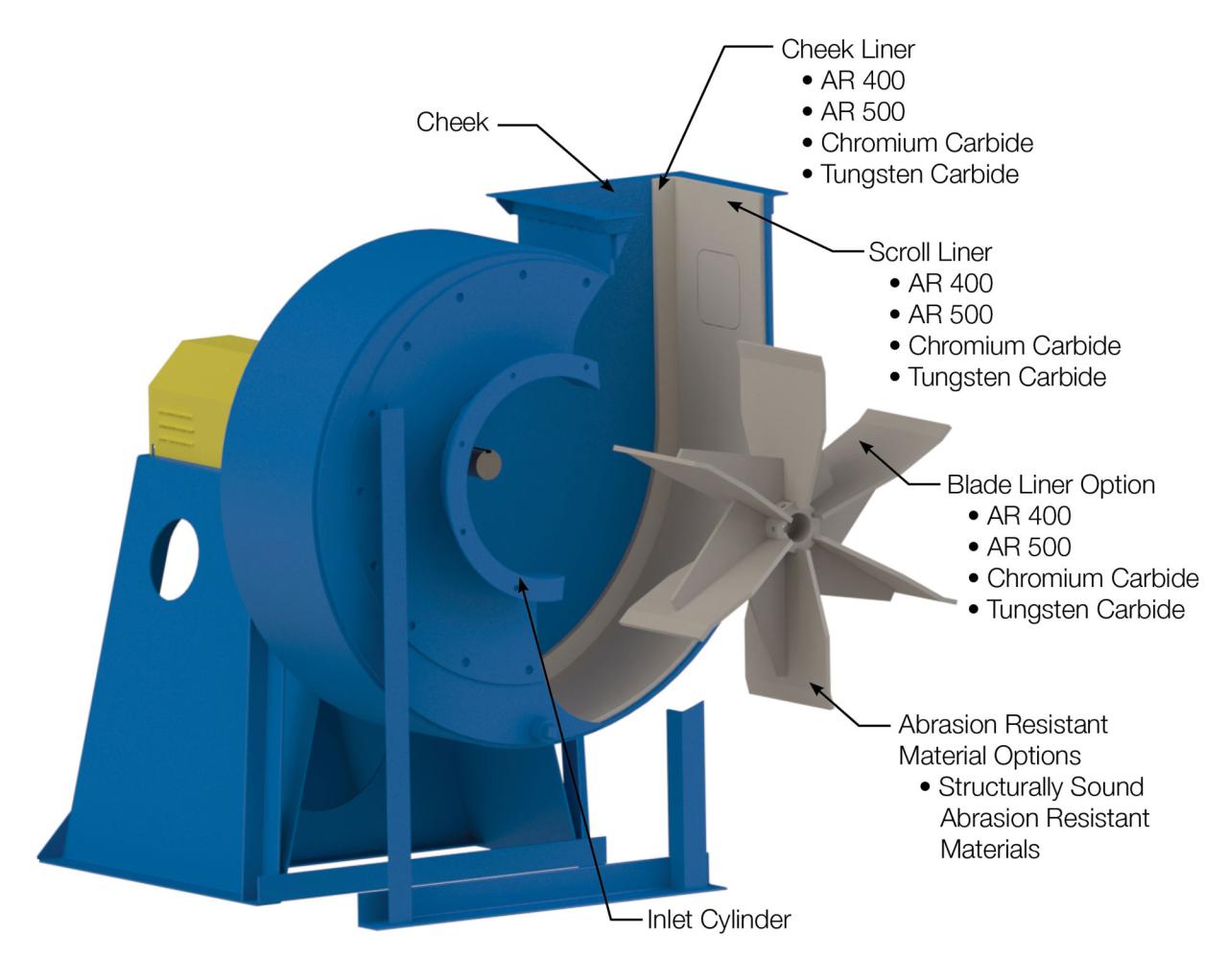
Industrial air technology is essential for maintaining a safe and healthy working environment in factories and industrial settings. From manufacturing plants to chemical processing facilities, industries rely on advanced technologies to control air pollution and ensure the well-being of workers and the surrounding community.
The importance of clean air in industrial settings cannot be overstated. Air pollution can lead to a range of health problems, including respiratory illnesses, cardiovascular disease, and cancer. It can also damage equipment and reduce productivity. Industrial air technology plays a crucial role in mitigating these risks by effectively controlling and removing harmful pollutants from the air.
Introduction to Industrial Air Technology
In the realm of industrial operations, maintaining optimal air quality is paramount. Industrial air technology encompasses the diverse range of technologies and practices employed to ensure clean and safe air within industrial environments. It plays a crucial role in safeguarding worker health, protecting equipment, and upholding environmental regulations.
Importance of Air Quality in Industrial Settings
Air quality in industrial settings is of paramount importance for various reasons. Firstly, it directly impacts the health and well-being of workers. Exposure to harmful pollutants, such as dust, fumes, and gases, can lead to respiratory illnesses, skin irritations, and long-term health problems. Secondly, industrial air quality significantly affects the performance and longevity of industrial equipment. Dust and other airborne contaminants can cause corrosion, clogging, and premature wear and tear on machinery, leading to costly repairs and downtime. Finally, environmental regulations are increasingly stringent, requiring industries to minimize their emissions and maintain clean air quality to protect the surrounding environment.
Industries Relying on Industrial Air Technology
A wide array of industries heavily rely on industrial air technology to ensure clean and safe air environments. These include:
- Manufacturing: From automotive manufacturing to electronics production, factories rely on industrial air technology to control dust, fumes, and other contaminants generated during production processes.
- Pharmaceuticals: Pharmaceutical companies require stringent air quality control to maintain sterile environments and prevent contamination of sensitive products.
- Food Processing: Food processing facilities rely on industrial air technology to control dust, microorganisms, and other contaminants that can affect food safety and quality.
- Power Generation: Power plants, particularly coal-fired power plants, utilize industrial air technology to capture and control emissions, such as sulfur dioxide and particulate matter.
- Construction: Construction sites generate significant dust and debris, and industrial air technology is employed to mitigate these hazards and protect workers’ health.
Challenges and Considerations
Industrial air quality presents numerous challenges and considerations:
- Identifying and Quantifying Contaminants: Determining the specific contaminants present in industrial environments and their concentrations is crucial for designing effective air quality control systems.
- Choosing Appropriate Control Technologies: A wide range of air pollution control technologies exists, each with its strengths and limitations. Selecting the most suitable technology depends on factors such as the type of contaminant, the required level of control, and cost considerations.
- Maintaining System Efficiency: Industrial air quality systems require regular maintenance and optimization to ensure continued effectiveness. This includes filter changes, system cleaning, and monitoring of performance parameters.
- Compliance with Regulations: Industrial air quality regulations vary depending on location and industry. Ensuring compliance with these regulations is essential to avoid penalties and maintain environmental responsibility.
- Cost-Effectiveness: Implementing and maintaining industrial air quality systems can be expensive. Balancing the need for clean air with cost considerations is a crucial aspect of industrial air technology.
Air Pollution Control Technologies
Air pollution control technologies are essential for mitigating the negative impacts of industrial emissions on human health and the environment. Industrial processes often release various pollutants into the atmosphere, posing risks to air quality and contributing to climate change.
Types of Air Pollutants
Industrial air pollutants can be broadly categorized into particulate matter, gaseous pollutants, and volatile organic compounds (VOCs).
- Particulate Matter (PM): This includes solid particles or liquid droplets suspended in the air, classified by size. PM2.5, with a diameter less than 2.5 micrometers, can penetrate deep into the lungs, posing significant health risks.
- Gaseous Pollutants: These are harmful gases released into the atmosphere, including carbon monoxide (CO), sulfur dioxide (SO2), nitrogen oxides (NOx), and ozone (O3). These gases can contribute to respiratory problems, acid rain, and smog formation.
- Volatile Organic Compounds (VOCs): These are organic compounds that easily evaporate at room temperature. Examples include benzene, toluene, and formaldehyde. VOCs can contribute to smog formation, ozone depletion, and some are known carcinogens.
Air Pollution Control Technologies
Air pollution control technologies are employed to remove or reduce the concentration of pollutants in industrial emissions before they are released into the atmosphere.
- Control technologies are selected based on factors like the type of pollutant, emission source, desired emission reduction level, and cost-effectiveness.
Examples of Air Pollution Control Technologies
A table summarizing various air pollution control technologies, their principles, applications, and advantages/disadvantages is provided below.
Technology | Principle | Applications | Advantages/Disadvantages |
---|---|---|---|
Cyclone Separator | Centrifugal force separates particulate matter from gas streams. | Removal of coarse particles from industrial processes like cement production and power generation. | Low operating cost, simple design, but limited efficiency for fine particles. |
Electrostatic Precipitator (ESP) | Electrically charged particles are collected on oppositely charged plates. | Removal of fine particles from flue gases in power plants and industrial boilers. | High efficiency for fine particles, but requires high voltage and can be bulky. |
Fabric Filter (Baghouse) | Particulate matter is trapped in filter bags made of fabric material. | Removal of dust and fine particles from industrial processes like cement production and wood processing. | High efficiency for fine particles, but can be expensive and require regular maintenance. |
Scrubber | Pollutants are removed by dissolving them in a liquid solution. | Removal of sulfur dioxide (SO2) and other gaseous pollutants from flue gases in power plants and industrial boilers. | High efficiency for gas removal, but requires significant water consumption and can generate wastewater. |
Catalytic Converter | Harmful gases are converted into less harmful compounds using a catalyst. | Reduction of carbon monoxide (CO), nitrogen oxides (NOx), and hydrocarbons in vehicle exhaust. | High efficiency for gas conversion, but requires precious metals as catalysts and can be sensitive to poisoning. |
Incineration | Pollutants are destroyed by combustion at high temperatures. | Destruction of hazardous waste and VOCs in industrial processes. | High efficiency for pollutant destruction, but can generate ash and requires high energy input. |
Selection Criteria for Air Pollution Control Technologies
The choice of an appropriate air pollution control technology depends on various factors, including:
- Type of pollutant: Different technologies are more effective for specific types of pollutants.
- Emission source: The characteristics of the emission source, such as flow rate, temperature, and pressure, influence technology selection.
- Desired emission reduction level: The required level of pollutant reduction dictates the technology’s efficiency and cost.
- Cost-effectiveness: Economic factors, including capital costs, operating costs, and maintenance costs, play a crucial role in technology selection.
- Environmental impact: The technology’s impact on the environment, such as waste generation and energy consumption, needs to be considered.
- Regulations: Compliance with environmental regulations and standards is a critical factor.
Air Filtration Systems
Air filtration systems are essential components in industrial settings, playing a crucial role in maintaining clean air quality and protecting both workers and equipment from harmful contaminants. These systems utilize various technologies to remove particulate matter, gases, and other pollutants from the air, effectively reducing the risks associated with exposure to hazardous substances.
Types of Air Filtration Systems
Different types of air filtration systems are designed to address specific types of contaminants and achieve varying levels of air purity. Here are some common types:
HEPA Filters
HEPA filters, or High-Efficiency Particulate Air filters, are renowned for their exceptional efficiency in capturing airborne particles, including dust, pollen, mold spores, and bacteria. Their effectiveness stems from their intricate structure, consisting of a fine mesh of fibers that traps particles as air passes through.
HEPA filters are typically rated to capture 99.97% of particles 0.3 microns or larger in size.
HEPA filters are widely used in various applications, including hospitals, laboratories, cleanrooms, and industrial settings where maintaining a high level of air purity is paramount.
Carbon Filters
Carbon filters are primarily used to remove gaseous pollutants from the air. These filters utilize activated carbon, a highly porous material with a vast surface area, to adsorb and trap various gases, including volatile organic compounds (VOCs), odors, and chemical fumes.
Activated carbon’s porous structure provides numerous adsorption sites, enabling it to effectively capture and retain gaseous contaminants.
Carbon filters are commonly found in applications such as air purifiers, ventilation systems, and industrial processes involving the release of harmful gases.
Electrostatic Precipitators
Electrostatic precipitators operate on the principle of electrostatic attraction to remove particulate matter from the air. They utilize a high-voltage electric field to charge particles, causing them to adhere to collection plates with opposite charges.
Electrostatic precipitators are particularly effective in capturing fine particles, such as dust, smoke, and fly ash, which are difficult to remove using other methods.
These systems are commonly employed in power plants, industrial furnaces, and other applications where large volumes of particulate matter are generated.
Maintenance and Replacement Requirements, Industrial air technology
Maintaining and replacing air filtration systems is crucial for ensuring their continued effectiveness and preventing potential health and safety hazards. The frequency of maintenance and replacement depends on factors such as the type of filter, the level of contamination, and the operating conditions.
HEPA Filters
HEPA filters typically require regular inspection and cleaning to maintain their efficiency.
A visual inspection should be conducted regularly to assess the filter’s condition and identify any signs of clogging or damage.
HEPA filters can be cleaned by vacuuming or using compressed air, but excessive cleaning can damage the filter’s delicate structure. When the filter becomes significantly clogged or damaged, it should be replaced with a new one.
Carbon Filters
Carbon filters also require regular maintenance to ensure their effectiveness.
The lifespan of a carbon filter depends on the concentration of contaminants and the airflow rate.
Over time, the activated carbon material becomes saturated with contaminants, reducing its adsorption capacity. When the filter’s performance deteriorates, it should be replaced with a fresh one.
Electrostatic Precipitators
Electrostatic precipitators require regular maintenance to ensure their optimal performance.
This includes cleaning the collection plates, replacing worn-out components, and inspecting the electrical system.
The frequency of maintenance depends on the operating conditions and the type of contaminants being removed.
Ventilation and Air Movement
Ventilation is a crucial aspect of industrial facilities, playing a vital role in maintaining a safe, healthy, and productive working environment. It involves the controlled exchange of air within a building to remove contaminants, regulate temperature and humidity, and ensure adequate oxygen supply. Effective ventilation systems are essential for protecting workers from hazardous substances, preventing the spread of diseases, and optimizing production processes.
Types of Ventilation Systems
Ventilation systems can be broadly categorized into natural and mechanical ventilation, each with its own advantages and limitations.
- Natural Ventilation: This system relies on natural forces like wind and temperature differences to draw fresh air into the building and exhaust stale air. It typically involves the use of windows, doors, and roof vents to create air movement. Natural ventilation is often cost-effective and energy-efficient, but its effectiveness can be limited by factors such as wind direction, temperature variations, and building design.
- Mechanical Ventilation: Mechanical ventilation systems use fans and other equipment to force air movement. They offer greater control over air flow and can be designed to handle specific ventilation needs, such as removing pollutants or maintaining a specific temperature and humidity level. However, mechanical systems require ongoing maintenance and can be more expensive to operate than natural ventilation.
Factors Influencing Ventilation Design and Optimization
Several factors must be considered when designing and optimizing ventilation systems for industrial facilities. These include:
- Nature of the Industrial Process: The type of work being done and the materials used will influence the ventilation requirements. For example, facilities that generate dust, fumes, or other pollutants will require more robust ventilation systems than those with less hazardous operations.
- Building Design: The layout, size, and structural features of the building will affect air flow patterns and ventilation effectiveness. Factors such as ceiling height, window placement, and the presence of partitions will all play a role in ventilation design.
- Climate and Weather Conditions: The local climate and weather patterns will influence the design and operation of ventilation systems. For example, buildings in hot and humid climates will require more effective cooling systems than those in cooler climates.
- Occupancy Levels: The number of people working in the facility will affect the amount of fresh air required. Higher occupancy levels will necessitate increased ventilation rates to maintain adequate oxygen supply and remove pollutants.
- Safety Regulations: Various regulations and standards govern ventilation requirements in industrial settings. These regulations are designed to protect workers from hazardous substances and ensure a safe working environment. It is essential to comply with all applicable safety regulations when designing and operating ventilation systems.
Air Quality Monitoring and Analysis: Industrial Air Technology
Air quality monitoring and analysis are crucial aspects of industrial air technology, ensuring compliance with regulations and optimizing processes for efficiency and sustainability. This involves the continuous measurement and evaluation of various pollutants in the air, providing valuable insights for informed decision-making.
Methods and Instruments for Air Quality Monitoring
Air quality monitoring in industrial settings employs a diverse range of methods and instruments to measure and analyze various pollutants. These methods are tailored to the specific pollutants and the nature of the industrial environment.
- Continuous Monitoring: This method involves the use of automated instruments that continuously collect and analyze air quality data. These instruments are often deployed in fixed locations, providing real-time data for immediate responses to changing conditions. Examples of continuous monitoring instruments include:
- Gas Analyzers: These instruments are used to measure the concentration of specific gases in the air, such as carbon monoxide, sulfur dioxide, and nitrogen oxides. They typically employ techniques like infrared spectroscopy, chemiluminescence, or electrochemical sensors.
- Particulate Matter Samplers: These instruments collect airborne particulate matter (PM) of different sizes, ranging from coarse particles to fine PM2.5 and ultrafine PM0.1. They can use filters, impactors, or other techniques to separate and quantify PM.
- Meteorological Sensors: These sensors measure environmental parameters like wind speed and direction, temperature, humidity, and atmospheric pressure. This data is crucial for understanding the dispersion and transport of pollutants.
- Discrete Sampling: This method involves collecting air samples at specific times and locations for later analysis in a laboratory. Discrete sampling is often used for monitoring pollutants that are not easily measured by continuous instruments or for collecting samples for specific research purposes. Common techniques include:
- Passive Samplers: These samplers collect pollutants over a period of time, typically days or weeks, without the need for active pumping. They are often used for long-term monitoring of pollutants like ozone and volatile organic compounds.
- Impingers: These devices collect air samples by drawing air through a liquid solution, where pollutants are absorbed or trapped. Impingers are commonly used for collecting gases like sulfur dioxide and nitrogen oxides.
- Filters: Filters are used to collect particulate matter from the air, which is then analyzed in the laboratory to determine the concentration and composition of different PM fractions.
Importance of Air Quality Data Analysis
The analysis of air quality data plays a critical role in optimizing industrial processes and ensuring compliance with regulations. It provides valuable insights into the effectiveness of pollution control measures, identifies potential issues, and helps to prioritize corrective actions.
- Process Optimization: By analyzing air quality data, industries can identify areas where emissions are high and optimize their processes to reduce pollution. For example, monitoring data can reveal inefficiencies in combustion processes or identify leaks in equipment, leading to targeted improvements.
- Compliance Monitoring: Air quality data is essential for ensuring compliance with regulatory standards. By tracking emissions levels, industries can demonstrate that they are meeting the required limits and avoid penalties.
- Risk Assessment: Analyzing air quality data can help to identify potential risks to human health and the environment. This information can be used to develop appropriate mitigation strategies and prevent adverse impacts.
Examples of Using Air Quality Data to Address Issues
Real-world examples demonstrate how air quality data can be used to identify and address potential issues in industrial settings.
- Identifying Source of Emissions: A manufacturing plant noticed an increase in particulate matter emissions. By analyzing data from multiple monitoring stations located around the facility, they identified the source of the increased emissions as a specific piece of equipment. This allowed them to focus their efforts on fixing the equipment and reducing emissions.
- Optimizing Combustion Processes: A power plant used air quality data to optimize its combustion processes. By analyzing data from the flue gas, they identified areas where the combustion process was inefficient. By adjusting the air-fuel ratio and other parameters, they were able to reduce emissions of NOx and improve fuel efficiency.
- Developing Emission Reduction Strategies: A chemical plant used air quality data to develop a comprehensive emission reduction strategy. By analyzing historical data and modeling future scenarios, they identified key emission sources and developed targeted interventions, such as upgrading equipment, implementing cleaner production practices, and installing pollution control technologies.
Safety and Regulations
Industrial air pollution poses significant safety hazards to workers and the surrounding community. It is crucial to implement robust safety protocols and comply with regulations to minimize these risks. This section delves into the safety hazards, relevant regulations, and best practices for ensuring a safe working environment and environmental compliance.
Safety Hazards Associated with Industrial Air Pollution
Industrial air pollution can lead to various health issues, ranging from mild respiratory irritation to severe chronic diseases.
- Respiratory problems: Exposure to pollutants like particulate matter, sulfur dioxide, and nitrogen oxides can irritate the lungs, leading to coughing, wheezing, and shortness of breath. In severe cases, it can cause asthma, chronic obstructive pulmonary disease (COPD), and lung cancer.
- Cardiovascular diseases: Fine particulate matter can penetrate deep into the lungs and enter the bloodstream, increasing the risk of heart attacks, strokes, and other cardiovascular problems.
- Cancer: Some industrial pollutants, such as benzene and formaldehyde, are known carcinogens and can contribute to the development of cancer.
- Other health effects: Exposure to industrial air pollution can also cause eye irritation, skin problems, neurological disorders, and reproductive issues.
Beyond health risks, industrial air pollution can also pose safety hazards in the workplace.
- Explosions and fires: Certain pollutants, such as flammable gases and vapors, can create hazardous conditions that increase the risk of explosions and fires.
- Asphyxiation: Some industrial processes release gases that can displace oxygen in the air, leading to asphyxiation.
- Equipment malfunctions: Air pollution can corrode equipment, leading to malfunctions and accidents.
Regulations and Standards Governing Industrial Air Quality
To protect public health and the environment, governments worldwide have implemented regulations and standards governing industrial air quality. These regulations aim to limit emissions of pollutants from industrial sources and promote the use of cleaner technologies.
- The Clean Air Act (CAA): In the United States, the Environmental Protection Agency (EPA) enforces the Clean Air Act, which sets national ambient air quality standards (NAAQS) for six common pollutants: carbon monoxide, lead, nitrogen dioxide, ozone, particulate matter, and sulfur dioxide. Industries must comply with these standards by reducing their emissions.
- European Union (EU) Directives: The EU has implemented several directives to regulate industrial emissions, such as the Industrial Emissions Directive (IED) and the Large Combustion Plant Directive (LCPD). These directives establish emission limits for various pollutants and require industries to obtain permits for their operations.
- International Standards: Organizations like the World Health Organization (WHO) set international air quality guidelines that provide recommendations for safe exposure levels of various pollutants. These guidelines serve as a reference for countries developing their own air quality regulations.
Best Practices for Workplace Safety and Environmental Compliance
- Regular monitoring and analysis: Industries should regularly monitor air quality within their facilities and surrounding areas to identify potential hazards and ensure compliance with regulations. This involves using air quality monitoring equipment and conducting periodic air sampling.
- Employee training and awareness: Training employees on the hazards of industrial air pollution and the importance of safety protocols is crucial. This includes providing information on the risks associated with specific pollutants, safe work practices, and emergency procedures.
- Implementation of control technologies: Industries should implement control technologies, such as scrubbers, filters, and electrostatic precipitators, to reduce emissions of pollutants. These technologies capture and remove pollutants from exhaust streams before they are released into the atmosphere.
- Process optimization: Optimizing industrial processes can significantly reduce emissions. This may involve using cleaner raw materials, improving energy efficiency, and implementing waste reduction strategies.
- Regular maintenance and inspections: Regular maintenance and inspections of air pollution control equipment are essential to ensure its effectiveness and prevent malfunctions. This includes checking for leaks, replacing filters, and calibrating instruments.
- Emergency preparedness: Industries should have a plan in place to respond to emergencies related to air pollution. This plan should include procedures for evacuating workers, contacting emergency services, and mitigating the effects of pollution releases.
Emerging Trends and Innovations
The industrial air technology landscape is constantly evolving, driven by the need to improve air quality, enhance efficiency, and minimize environmental impact. Advancements in nanotechnology, artificial intelligence (AI), and energy-efficient systems are transforming how we approach industrial air management.
Nanotechnology in Air Filtration
Nanotechnology is revolutionizing air filtration by enabling the development of highly efficient and compact filters. Nanomaterials, such as carbon nanotubes and graphene, possess exceptional surface area and pore size, allowing them to capture even the smallest airborne particles, including ultrafine particles and gases.
- Enhanced Filtration Efficiency: Nanomaterials provide a larger surface area for particle capture, leading to higher filtration efficiency and reduced emissions. For instance, a study by the National Institute for Occupational Safety and Health (NIOSH) found that nanofiber filters effectively removed over 99% of airborne particles smaller than 0.3 micrometers in diameter.
- Reduced Filter Size: The high surface area of nanomaterials allows for the creation of smaller and lighter filters, which can be easily integrated into existing equipment. This is particularly advantageous in applications with space constraints, such as portable air purifiers or industrial ventilation systems.
- Improved Durability: Nanomaterials exhibit excellent chemical and thermal stability, leading to longer filter life and reduced maintenance costs. This is crucial in industrial settings where filters are exposed to harsh conditions.
AI-Powered Air Quality Monitoring
Artificial intelligence (AI) is transforming air quality monitoring by enabling real-time data analysis, predictive maintenance, and automated response systems. AI algorithms can analyze data from multiple sensors, identify trends, and predict potential air quality issues before they occur.
- Real-Time Data Analysis: AI-powered systems can process large volumes of data from sensors in real time, providing immediate insights into air quality conditions and identifying potential problems. This allows for prompt action to mitigate risks and ensure worker safety.
- Predictive Maintenance: AI algorithms can analyze sensor data and equipment performance to predict potential failures, allowing for proactive maintenance and minimizing downtime. This reduces maintenance costs and ensures uninterrupted operations.
- Automated Response Systems: AI-powered systems can automatically adjust ventilation systems, air filtration units, and other equipment based on real-time air quality data. This optimizes air quality management and minimizes human intervention.
Energy-Efficient Air Technology
Energy efficiency is a crucial aspect of sustainable industrial air management. Innovations in air technology are focused on reducing energy consumption while maintaining or improving air quality.
- Variable Speed Drives: Variable speed drives (VSDs) are used to adjust the speed of fans and blowers based on demand, reducing energy consumption during periods of low air flow requirements. A study by the U.S. Department of Energy found that VSDs can reduce energy consumption by up to 30% in ventilation systems.
- Heat Recovery Systems: Heat recovery systems capture waste heat from exhaust air and use it to preheat incoming fresh air, reducing the energy required for heating. This can significantly reduce heating costs and improve overall energy efficiency. For example, a heat recovery system can recover up to 70% of the heat from exhaust air, depending on the application.
- Smart Sensors and Controls: Smart sensors and control systems can optimize air flow and filtration based on real-time conditions, reducing energy consumption and ensuring optimal air quality. These systems can adapt to changing environmental conditions, ensuring efficient operation and minimizing energy waste.
Closing Notes
As industries continue to evolve and face new challenges, the importance of industrial air technology will only grow. Emerging trends like nanotechnology, AI-powered monitoring, and energy-efficient systems are revolutionizing how we approach air quality management. By embracing these innovations, we can create a future where industries operate sustainably and responsibly, ensuring clean air for all.
Industrial air technology plays a crucial role in ensuring clean and safe working environments. It’s a field that requires specialized knowledge and skills, which is why institutions like the fayette institute of technology are so important. These institutes provide comprehensive training programs, equipping students with the necessary tools and expertise to excel in this dynamic industry.