Epoxy Technology 353nd: A Comprehensive Overview
Epoxy technology 353nd has revolutionized industries, from adhesives and coatings to composites and electronics. This versatile material offers exceptional strength, durability, and versatility, making it a cornerstone in modern engineering […]
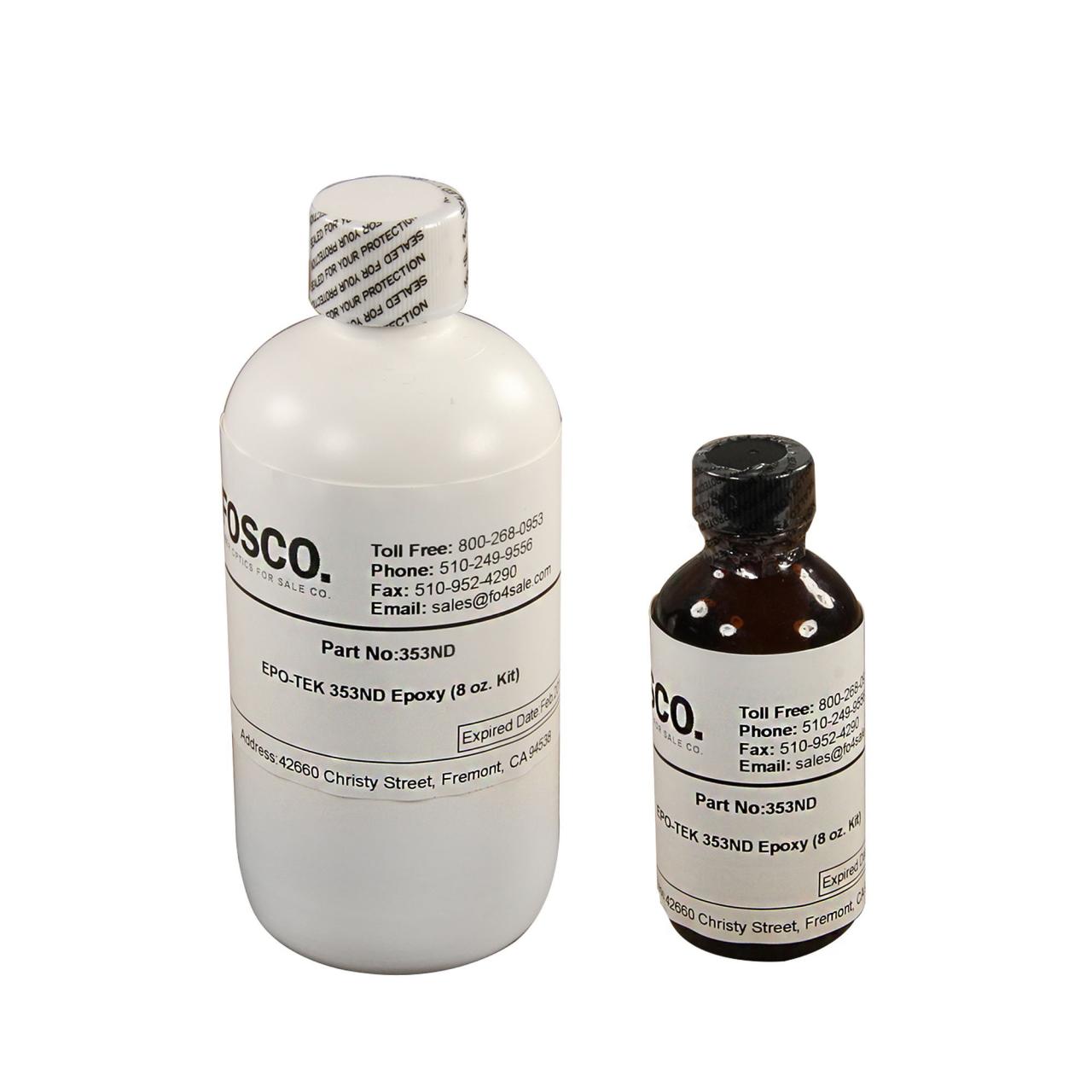
Epoxy technology 353nd has revolutionized industries, from adhesives and coatings to composites and electronics. This versatile material offers exceptional strength, durability, and versatility, making it a cornerstone in modern engineering and manufacturing.
Epoxy technology 353nd encompasses the science and engineering behind the development, production, and application of epoxy resins. These resins, formed by reacting an epoxy with a curing agent, exhibit remarkable properties that have propelled their widespread use in various fields. From aerospace and automotive to construction and electronics, epoxy technology plays a vital role in shaping our world.
Introduction to Epoxy Technology: Epoxy Technology 353nd
Epoxy technology is a fascinating field that revolves around the creation and utilization of epoxy resins. Epoxy resins are synthetic polymers known for their exceptional adhesive, structural, and protective properties. They form strong bonds with a wide range of materials, making them incredibly versatile and indispensable in numerous industries.
Basic Principles of Epoxy Technology, Epoxy technology 353nd
Epoxy technology is based on the chemical reaction between an epoxy resin and a hardener. This reaction, known as curing, transforms the liquid resin into a solid, rigid, and durable material. The properties of the cured epoxy are influenced by the specific types of resin and hardener used, as well as the curing conditions, such as temperature and time.
Historical Development and Evolution of Epoxy Technology
The history of epoxy technology dates back to the early 20th century. In 1934, Swiss chemist Pierre Castan discovered the first epoxy resin, which was a synthetic, thermosetting polymer. This discovery laid the foundation for the development of a wide range of epoxy-based products.
- Early Developments: The initial applications of epoxy resins were primarily focused on adhesives and coatings. During World War II, epoxy resins gained significant importance due to their ability to bond various materials, including metals, plastics, and ceramics. This led to their widespread use in aircraft and other military applications.
- Advancements in Technology: Over the years, epoxy technology has undergone significant advancements. The development of new resin and hardener formulations has expanded the range of properties and applications of epoxy resins. Today, epoxy resins are used in a vast array of industries, including construction, aerospace, electronics, and automotive.
Applications of Epoxy Technology
Epoxy technology finds extensive applications in various industries, showcasing its remarkable versatility and durability.
- Construction: Epoxy resins are widely used in construction for bonding, sealing, and coating applications. They are used in adhesives for bonding concrete, wood, and metal, as well as in sealants for preventing water ingress and corrosion.
- Aerospace: Epoxy resins are essential materials in the aerospace industry, where their high strength-to-weight ratio and resistance to extreme temperatures are highly valued. They are used in aircraft components, such as fuselages, wings, and tail sections.
- Electronics: Epoxy resins play a crucial role in electronics manufacturing. They are used as encapsulants for protecting electronic components from moisture, heat, and mechanical shock.
- Automotive: Epoxy resins are extensively used in the automotive industry for bonding, sealing, and coating applications. They are used in adhesives for bonding body panels, as well as in sealants for preventing leaks and corrosion.
- Other Applications: Epoxy resins have numerous other applications, including in flooring, marine coatings, and medical devices.
Types of Epoxy Resins
Epoxy resins are a versatile class of polymers known for their exceptional adhesive properties, mechanical strength, and chemical resistance. They are widely used in various industries, including construction, aerospace, electronics, and automotive. Epoxy resins are typically formed by the reaction of an epoxy compound with a curing agent, which leads to the formation of a strong, rigid, and durable network structure. The type of epoxy resin used depends on the specific application requirements, such as the desired mechanical properties, thermal resistance, and chemical resistance.
Epoxy Resin Types Based on Chemical Structure
The chemical structure of epoxy resins plays a crucial role in determining their properties. Different types of epoxy resins are classified based on their structural features, which affect their performance characteristics.
- Bisphenol A (BPA) Epoxy Resins: BPA epoxy resins are the most common type of epoxy resin and are derived from the reaction of bisphenol A with epichlorohydrin. These resins exhibit excellent mechanical strength, chemical resistance, and adhesion properties. They are widely used in structural adhesives, coatings, and composites.
- Bisphenol F (BPF) Epoxy Resins: BPF epoxy resins are similar to BPA epoxy resins but are derived from bisphenol F instead of bisphenol A. They offer similar properties to BPA epoxy resins but have lower viscosity, making them easier to process. BPF epoxy resins are used in applications where lower viscosity is desired, such as in coatings and molding compounds.
- Novolac Epoxy Resins: Novolac epoxy resins are derived from the reaction of phenol with formaldehyde. They have higher glass transition temperatures (Tg) and are more resistant to heat and moisture than BPA and BPF epoxy resins. Novolac epoxy resins are commonly used in high-performance applications, such as in aerospace and electronics.
- Cycloaliphatic Epoxy Resins: Cycloaliphatic epoxy resins are based on cycloaliphatic structures, which provide excellent resistance to UV radiation and weathering. They are often used in outdoor applications, such as in coatings and adhesives for marine and automotive industries.
- Glycidyl Ether Epoxy Resins: Glycidyl ether epoxy resins are a diverse group of resins with varying properties depending on the specific chemical structure. They are commonly used in adhesives, coatings, and composites.
Epoxy Resin Systems
Epoxy resins are rarely used alone; they are typically formulated into systems by combining them with curing agents, fillers, and other additives. The specific components and their proportions determine the final properties of the epoxy system.
- Epoxy-Amine Systems: Amine curing agents are the most common type of curing agent used with epoxy resins. They react with the epoxy groups to form a cross-linked network, leading to the hardening of the epoxy system. Amine curing agents are available in various forms, including liquid amines, solid amines, and polyamides.
- Epoxy-Anhydride Systems: Anhydride curing agents are another type of curing agent used with epoxy resins. They react with the epoxy groups to form a cross-linked network, leading to the hardening of the epoxy system. Anhydride curing agents typically require higher curing temperatures than amine curing agents.
- Epoxy-Phenolic Systems: Phenolic resins are often used as curing agents for epoxy resins. They provide excellent adhesion and heat resistance to the final epoxy system.
Advantages and Disadvantages of Different Epoxy Resin Types
The choice of epoxy resin type depends on the specific application requirements. Different epoxy resin types offer unique advantages and disadvantages.
- Advantages of BPA Epoxy Resins:
- Excellent mechanical strength and stiffness
- Good chemical resistance
- Excellent adhesion to various substrates
- Widely available and relatively inexpensive
- Disadvantages of BPA Epoxy Resins:
- Can be brittle at low temperatures
- Susceptible to yellowing under UV exposure
- Potential environmental concerns due to BPA’s endocrine disrupting properties
- Advantages of BPF Epoxy Resins:
- Lower viscosity compared to BPA epoxy resins
- Easier to process and handle
- Good mechanical strength and chemical resistance
- Disadvantages of BPF Epoxy Resins:
- Generally lower mechanical strength compared to BPA epoxy resins
- May have lower heat resistance
- Advantages of Novolac Epoxy Resins:
- High glass transition temperature (Tg)
- Excellent heat and moisture resistance
- Good chemical resistance
- Disadvantages of Novolac Epoxy Resins:
- Higher viscosity, making them more difficult to process
- May have lower adhesion compared to BPA epoxy resins
- Advantages of Cycloaliphatic Epoxy Resins:
- Excellent resistance to UV radiation and weathering
- Good mechanical strength and chemical resistance
- Disadvantages of Cycloaliphatic Epoxy Resins:
- Higher cost compared to other epoxy resin types
- May have lower adhesion to some substrates
- Advantages of Glycidyl Ether Epoxy Resins:
- Wide range of properties depending on the specific chemical structure
- Good flexibility and toughness
- Excellent adhesion to various substrates
- Disadvantages of Glycidyl Ether Epoxy Resins:
- May have lower mechanical strength compared to BPA epoxy resins
- Can be more susceptible to moisture absorption
Curing Mechanisms and Properties of Epoxy Systems
Epoxy resins, in their raw form, are viscous liquids. To achieve their desired strength and rigidity, they undergo a chemical reaction called curing, where they transition from a liquid to a solid state. This curing process involves the formation of a cross-linked network structure, enhancing the material’s mechanical, thermal, and chemical properties.
Curing Mechanisms
The curing process of epoxy resins involves a chemical reaction between the epoxy groups and a curing agent. The curing agent, also known as a hardener, reacts with the epoxy groups, opening the epoxide ring and forming a three-dimensional network structure. This network structure provides the cured epoxy with its characteristic strength, rigidity, and other desirable properties.
The most common curing mechanism involves the reaction of an amine curing agent with the epoxy groups. The amine group attacks the epoxide ring, opening it and forming a secondary amine. This reaction can occur at various temperatures, depending on the specific epoxy resin and curing agent used.
Another common curing mechanism involves the use of an anhydride curing agent. The anhydride reacts with the epoxy groups to form an ester linkage. This reaction requires higher temperatures than the amine curing process, typically around 100°C.
The curing process can be influenced by several factors, including temperature, time, and the presence of catalysts. Increasing the temperature generally accelerates the curing reaction, leading to a faster cure time. The time required for complete curing can vary widely depending on the specific epoxy system and curing conditions. Catalysts can be used to accelerate the curing process by lowering the activation energy of the reaction.
Factors Influencing Curing Kinetics and Properties
Several factors influence the curing kinetics and properties of epoxy systems. Understanding these factors is crucial for controlling the curing process and achieving desired properties in the final cured material.
- Epoxy Resin Type: The type of epoxy resin used significantly affects the curing kinetics and properties of the cured material. Different epoxy resins have different reactivity, viscosity, and glass transition temperatures. For example, bisphenol A epoxy resins are known for their good mechanical properties and resistance to chemicals, while cycloaliphatic epoxy resins are known for their low viscosity and good adhesion to various substrates.
- Curing Agent Type and Stoichiometry: The type and amount of curing agent used directly influence the curing kinetics and properties of the cured epoxy. The stoichiometry, or the ratio of epoxy groups to curing agent, is critical for achieving optimal cure. Excess curing agent can lead to a brittle material, while insufficient curing agent can result in an under-cured material with poor mechanical properties.
- Temperature: Temperature plays a significant role in the curing kinetics. Higher temperatures accelerate the curing process, leading to a faster cure time. However, excessive heat can lead to degradation of the epoxy resin and poor properties.
- Catalysts: Catalysts can be used to accelerate the curing process by lowering the activation energy of the reaction. However, the choice of catalyst must be carefully considered, as it can affect the final properties of the cured epoxy.
- Humidity: Humidity can affect the curing process, especially for certain epoxy systems. High humidity can lead to slower curing times and reduced mechanical properties.
Mechanical Properties of Cured Epoxy Materials
Cured epoxy materials are known for their excellent mechanical properties, including high tensile strength, flexural strength, and impact resistance. These properties make them suitable for a wide range of applications, such as structural adhesives, coatings, and composites.
The mechanical properties of cured epoxy materials can be influenced by several factors, including the type of epoxy resin, curing agent, and curing conditions. For example, the addition of fillers can increase the strength and stiffness of the cured epoxy, while the use of flexible curing agents can improve its toughness.
Thermal Properties of Cured Epoxy Materials
Cured epoxy materials exhibit good thermal stability, making them suitable for applications requiring resistance to high temperatures. They have a high glass transition temperature (Tg), which is the temperature at which the material transitions from a glassy state to a rubbery state. The Tg of cured epoxy materials can be tailored by selecting appropriate epoxy resins and curing agents.
Epoxy resins with higher Tg values are generally more resistant to heat distortion and creep. However, the thermal conductivity of cured epoxy materials is relatively low. For applications requiring high thermal conductivity, epoxy composites containing conductive fillers can be used.
Chemical Properties of Cured Epoxy Materials
Cured epoxy materials exhibit excellent resistance to chemicals, solvents, and moisture. This resistance makes them suitable for applications such as coatings, sealants, and adhesives in harsh environments. However, the chemical resistance of cured epoxy materials can vary depending on the specific epoxy resin and curing agent used.
For example, some epoxy resins are highly resistant to acids, while others are more resistant to bases. The presence of fillers and other additives can also affect the chemical resistance of cured epoxy materials.
Electrical Properties of Cured Epoxy Materials
Cured epoxy materials have excellent electrical insulating properties. They are commonly used as encapsulants for electronic components, providing protection from moisture, dust, and other environmental factors. The electrical properties of cured epoxy materials can be influenced by the presence of fillers and other additives.
For example, the addition of conductive fillers can increase the electrical conductivity of the cured epoxy, making it suitable for applications such as conductive adhesives and coatings.
Manufacturing and Processing of Epoxy Materials
Epoxy materials are manufactured through a series of chemical reactions involving the synthesis of epoxy resins and hardeners. The processing of these materials involves shaping, molding, and curing techniques to create desired shapes and properties. This section delves into the methods used for manufacturing epoxy resins and composites, explores the processing techniques employed, and provides examples of common equipment and technologies used in epoxy manufacturing.
Epoxy Resin Manufacturing
The production of epoxy resins involves several steps, beginning with the synthesis of bisphenol-A and epichlorohydrin. These two chemicals are reacted under specific conditions to form the epoxy resin. The process typically involves a ring-opening polymerization reaction where the epoxide group in epichlorohydrin reacts with the hydroxyl group in bisphenol-A, resulting in a chain-like structure.
The following methods are commonly employed in epoxy resin manufacturing:
- Batch Process: This traditional method involves mixing the reactants in a reactor vessel and heating them to initiate the polymerization reaction. The process is typically carried out in batches, and the reaction time and temperature are carefully controlled to ensure the desired molecular weight and properties of the epoxy resin are achieved. Batch processes offer flexibility in terms of resin formulation and production volume, making them suitable for small-scale production and research and development purposes.
- Continuous Process: This method involves a continuous flow of reactants through a series of reactors, where the polymerization reaction occurs under controlled conditions. Continuous processes are highly efficient and can produce large volumes of epoxy resins consistently. This method is particularly advantageous for large-scale production, as it allows for continuous operation and minimizes downtime.
Epoxy Composite Manufacturing
Epoxy composites are produced by combining epoxy resins with reinforcing materials such as fibers, fabrics, or particles. These composites exhibit enhanced mechanical properties, including strength, stiffness, and impact resistance, compared to the individual components. The manufacturing process for epoxy composites typically involves the following steps:
- Preparation of the Reinforcement: This involves cleaning and preparing the reinforcing material, such as fibers or fabrics, to ensure proper adhesion to the epoxy resin. This may involve surface treatments, such as sizing or coupling agents, to enhance the bonding between the reinforcement and the resin.
- Mixing and Impregnation: The epoxy resin and hardener are mixed together according to specific ratios, and the resulting mixture is impregnated into the reinforcement. This process can be done manually or using automated equipment. Vacuum bagging or pressure impregnation techniques are often employed to ensure complete and uniform impregnation of the reinforcement with the resin.
- Curing: The impregnated composite is then cured at a specific temperature and time to solidify the resin and achieve the desired mechanical properties. The curing process can be carried out in an oven, under pressure, or at ambient temperature, depending on the specific epoxy system and the desired properties of the composite.
Processing Techniques
Epoxy materials can be processed using various techniques to create desired shapes and properties. These techniques include:
- Casting: This method involves pouring the liquid epoxy resin into a mold and allowing it to cure. Casting is commonly used for producing simple shapes, such as blocks, slabs, or decorative items.
- Molding: Molding techniques involve using a mold to shape the epoxy material. Several types of molding techniques are used for epoxy processing, including:
- Compression Molding: This technique involves pressing the epoxy material into a mold under pressure and heat. Compression molding is suitable for producing complex shapes with high production volumes.
- Injection Molding: In this method, the liquid epoxy resin is injected into a mold under pressure. Injection molding is a highly automated process suitable for producing large quantities of identical parts.
- Transfer Molding: This technique involves transferring the epoxy material from a reservoir into a mold under pressure. Transfer molding is well-suited for producing parts with intricate details and high precision.
- Lay-up: This technique involves manually placing layers of reinforcement material, such as fiber mats or fabrics, into a mold and impregnating them with the epoxy resin. Lay-up is a versatile technique used for producing a wide range of composite structures, including boat hulls, aircraft parts, and wind turbine blades.
Equipment and Technologies
Epoxy manufacturing and processing involve the use of specialized equipment and technologies. Some common examples include:
- Mixers: Mixers are essential for blending the epoxy resin and hardener in the correct proportions. Various types of mixers are used, including planetary mixers, high-shear mixers, and vacuum mixers, depending on the specific application and viscosity of the materials.
- Molds: Molds are used to shape the epoxy material. Molds can be made from various materials, including steel, aluminum, fiberglass, and silicone, depending on the desired shape, size, and production volume.
- Ovens: Ovens are used for curing the epoxy material at a controlled temperature. Ovens can be equipped with various features, such as temperature control systems, ventilation systems, and pressure control systems, to ensure optimal curing conditions.
- Vacuum Systems: Vacuum systems are often used to remove air bubbles from the epoxy resin and to facilitate the impregnation of the reinforcement material. Vacuum systems can also be used to create a controlled atmosphere for curing the epoxy material.
- Automated Dispensing Systems: Automated dispensing systems are used to precisely control the amount of epoxy resin and hardener dispensed into molds. These systems improve efficiency and consistency in production.
Applications of Epoxy Technology
Epoxy technology has revolutionized various industries, playing a crucial role in the development and manufacturing of numerous products. The versatility of epoxy resins, coupled with their unique properties, has led to their widespread use in diverse applications.
Adhesives
Epoxy adhesives are known for their exceptional bonding strength, chemical resistance, and durability. They are widely used in various applications, including:
- Structural Bonding: Epoxy adhesives are employed in structural bonding applications, such as aircraft, automotive, and marine structures. Their high strength and durability make them ideal for joining different materials, including metals, composites, and plastics.
- Industrial Applications: Epoxy adhesives find extensive use in industrial applications, such as bonding wood, metal, and ceramic components. They are commonly used in manufacturing, construction, and repair processes.
- Consumer Products: Epoxy adhesives are prevalent in consumer products, such as woodworking, craft projects, and home repairs. They offer a convenient and reliable solution for bonding various materials.
Coatings
Epoxy coatings are known for their exceptional resistance to chemicals, abrasion, and corrosion. They are used in various applications, including:
- Protective Coatings: Epoxy coatings are applied to protect surfaces from environmental factors, such as corrosion, abrasion, and chemical attack. They are commonly used in industrial facilities, marine environments, and infrastructure projects.
- Floor Coatings: Epoxy coatings are widely used for floor coatings in industrial and commercial settings. They provide a durable, easy-to-clean surface that can withstand heavy traffic and harsh conditions.
- Automotive Coatings: Epoxy coatings are employed in automotive applications, such as primer coatings, underbody coatings, and protective coatings for components.
Composites
Epoxy resins are essential components in composite materials, which combine the properties of different materials to create high-performance materials.
- Fiber-Reinforced Plastics (FRP): Epoxy resins are widely used in FRP composites, such as fiberglass, carbon fiber, and Kevlar. These composites offer excellent strength-to-weight ratio, stiffness, and durability, making them suitable for applications in aerospace, automotive, and construction industries.
- Advanced Composites: Epoxy resins are used in advanced composites, such as carbon nanotube composites and graphene composites. These composites exhibit exceptional mechanical properties, electrical conductivity, and thermal stability, making them ideal for applications in electronics, aerospace, and energy storage.
Electronics
Epoxy resins are used in various electronic applications, including:
- Encapsulation: Epoxy resins are used to encapsulate electronic components, protecting them from moisture, dust, and mechanical shock. They provide electrical insulation and thermal stability, ensuring the reliability and longevity of electronic devices.
- Printed Circuit Boards (PCBs): Epoxy resins are used in the manufacturing of PCBs, providing a substrate for electronic components and ensuring electrical conductivity and mechanical strength.
- Semiconductors: Epoxy resins are used in semiconductor manufacturing, providing a protective layer for delicate components and ensuring their performance and reliability.
Emerging Trends and Future Developments in Epoxy Technology
Epoxy technology is constantly evolving, driven by advancements in materials science, chemistry, and manufacturing techniques. Research and development efforts are focused on improving the performance, sustainability, and versatility of epoxy systems.
Emerging Trends in Epoxy Technology
The following are some of the key trends shaping the future of epoxy technology:
- Development of High-Performance Epoxy Systems: Researchers are exploring novel epoxy resins and curing agents to create high-performance epoxy systems with enhanced mechanical properties, such as higher strength, stiffness, and toughness. These advancements are driven by the demand for stronger and more durable materials in various applications, including aerospace, automotive, and construction.
- Focus on Sustainability and Environmental Friendliness: The epoxy industry is actively seeking to reduce the environmental impact of epoxy production and use. This includes developing bio-based epoxy resins derived from renewable resources, exploring alternative curing agents with lower toxicity, and optimizing manufacturing processes to minimize waste and emissions.
- Integration of Nanotechnology: Nanotechnology is revolutionizing materials science, and epoxy technology is no exception. The incorporation of nanoparticles, such as carbon nanotubes and graphene, into epoxy matrices can significantly enhance properties like electrical conductivity, thermal conductivity, and mechanical strength. This opens up new possibilities for developing advanced functional materials with tailored properties.
- Additive Manufacturing of Epoxy Composites: Additive manufacturing, also known as 3D printing, is gaining traction in the epoxy industry. This technology enables the fabrication of complex epoxy composite structures with intricate designs and customized properties. It offers significant advantages in terms of design freedom, reduced material waste, and on-demand production.
Potential Areas for Future Development
Future research and development efforts in epoxy technology are likely to focus on the following areas:
- Development of Self-Healing Epoxies: Self-healing epoxies are materials that can repair minor cracks and damage on their own, extending their lifespan and improving their reliability. This technology has the potential to revolutionize the use of epoxies in applications where durability and longevity are critical, such as in aerospace and infrastructure.
- Design of Multifunctional Epoxy Systems: Multifunctional epoxies combine multiple functionalities, such as structural strength, electrical conductivity, and thermal insulation, in a single material. This approach can simplify design and manufacturing processes, reducing the need for multiple materials and components. The development of multifunctional epoxies is particularly relevant for applications in electronics, sensors, and energy storage.
- Advanced Curing Technologies: Research is underway to develop novel curing technologies that enable faster curing times, lower curing temperatures, and improved control over the curing process. These advancements will lead to more efficient and sustainable manufacturing processes for epoxy composites.
- Integration of Artificial Intelligence (AI): AI is playing an increasingly important role in materials science, and epoxy technology is no exception. AI algorithms can be used to predict and optimize the properties of epoxy systems, accelerate the discovery of new materials, and enhance manufacturing processes.
Environmental and Safety Considerations
Epoxy technology, while offering numerous benefits, also poses certain environmental and safety concerns that need careful consideration. Understanding these aspects is crucial for responsible use and minimizing potential risks.
Environmental Impact of Epoxy Technology
Epoxy resins are generally considered durable and resistant to degradation, making them valuable for various applications. However, this durability also translates to potential environmental challenges related to their disposal and recycling.
Disposal and Recycling
- Landfill Disposal: Epoxy waste, if not properly treated, can persist in landfills for extended periods, potentially leaching harmful substances into the surrounding environment.
- Incineration: Incineration can be a method for disposing of epoxy waste, but it’s important to ensure complete combustion to avoid the release of toxic byproducts.
- Recycling: Recycling of epoxy materials is challenging due to their complex chemical composition and the difficulty in separating them from other materials. However, advancements in recycling technologies are exploring ways to recover valuable components from epoxy waste.
Health and Safety Hazards
Epoxy resins and their curing agents can pose various health and safety hazards during handling, processing, and use. It’s crucial to implement appropriate safety measures to mitigate these risks.
Potential Hazards
- Skin and Eye Irritation: Some epoxy resins and curing agents can cause skin and eye irritation, leading to redness, itching, and burning sensations.
- Respiratory Problems: Inhalation of epoxy fumes or dust can trigger respiratory issues, including coughing, shortness of breath, and allergic reactions.
- Dermatitis: Repeated exposure to epoxy resins can cause skin sensitization, leading to allergic reactions and dermatitis.
- Toxicity: Some epoxy components, particularly curing agents, can be toxic and may cause systemic effects, including organ damage, if ingested or absorbed through the skin.
Safe Handling and Disposal
To ensure the safe handling and disposal of epoxy materials, it’s essential to follow these recommendations:
Safe Handling Practices
- Personal Protective Equipment (PPE): Always wear appropriate PPE, including gloves, eye protection, and respirators, when handling epoxy materials.
- Ventilation: Ensure adequate ventilation in work areas to minimize exposure to fumes and dust.
- Proper Mixing and Application: Follow the manufacturer’s instructions carefully for mixing ratios, application procedures, and curing times.
- Emergency Procedures: Have readily available emergency procedures and first aid kits in case of accidents or spills.
Disposal Practices
- Container Labeling: Properly label all containers of epoxy materials with hazard warnings and disposal instructions.
- Waste Segregation: Separate epoxy waste from other types of waste to facilitate proper disposal or recycling.
- Authorized Disposal: Dispose of epoxy waste in accordance with local regulations and through authorized disposal facilities.
Case Studies and Examples
Epoxy technology has found widespread applications in various industries, demonstrating its versatility and remarkable properties. From structural adhesives to protective coatings, epoxy resins have revolutionized numerous sectors, offering solutions to complex engineering challenges. This section delves into real-world examples of successful applications of epoxy technology, analyzing case studies to highlight the benefits and challenges of using epoxy materials in specific applications. It also explores the economic and social impact of this technology.
Epoxy Technology in Aerospace Applications
The aerospace industry demands materials that possess exceptional strength, lightweight properties, and resistance to extreme temperatures and environmental conditions. Epoxy resins have proven to be indispensable in this sector, contributing to the development of high-performance aircraft and spacecraft.
- Boeing 787 Dreamliner: The Boeing 787 Dreamliner, a revolutionary aircraft, incorporates epoxy-based composites extensively in its construction. These composites, made from carbon fiber reinforced epoxy (CFRP), provide significant weight reduction, leading to improved fuel efficiency and reduced emissions. CFRP also offers superior strength-to-weight ratio, enabling the aircraft to achieve greater structural integrity.
- SpaceX Starship: The SpaceX Starship, a reusable spacecraft designed for deep-space exploration, utilizes epoxy-based adhesives and composites for various structural components. These materials are crucial for the Starship’s ability to withstand the extreme temperatures and stresses encountered during launch, re-entry, and landing.
Epoxy Technology in Wind Energy
The wind energy industry relies on epoxy resins for blade construction, ensuring durability and resistance to harsh environmental conditions. Epoxy-based composites are used to manufacture wind turbine blades, offering a combination of strength, stiffness, and lightweight properties.
- Vestas V164 Wind Turbine: The Vestas V164 wind turbine, one of the largest wind turbines in the world, features epoxy-based composites in its blades. These composites contribute to the blade’s aerodynamic efficiency and ability to withstand high wind speeds and extreme weather conditions.
- Siemens Gamesa SG 14-222 DD Wind Turbine: The Siemens Gamesa SG 14-222 DD wind turbine, another significant development in wind energy technology, utilizes epoxy-based composites in its blades. These composites enable the turbine to generate higher power output and operate efficiently in challenging environments.
Economic and Social Impact of Epoxy Technology
Epoxy technology has had a significant economic and social impact, driving innovation and contributing to sustainable development.
- Job Creation: The epoxy industry has created numerous jobs in manufacturing, research and development, and applications across various sectors.
- Economic Growth: The widespread adoption of epoxy resins has stimulated economic growth by creating new markets and promoting technological advancements.
- Environmental Sustainability: Epoxy technology contributes to environmental sustainability by enabling the development of lightweight materials, reducing energy consumption, and promoting the use of renewable resources.
Epilogue
Epoxy technology 353nd continues to evolve, driven by innovation and the pursuit of enhanced performance. As researchers explore new formulations and applications, the future of epoxy technology holds exciting possibilities for creating even more durable, sustainable, and high-performing materials. From advanced composites to biocompatible materials, epoxy technology is poised to play a crucial role in addressing global challenges and shaping the future of our world.
Epoxy technology 353nd is a complex field with applications ranging from industrial coatings to advanced composites. Understanding the properties and performance of these materials requires robust data analysis, which is where data technology solutions can play a crucial role. By leveraging data analytics and machine learning, we can optimize epoxy 353nd formulations, predict their behavior under various conditions, and ensure consistent quality across production runs.