Edge Technologies Transforming Bar Feeding
Edge technologies bar feeder are revolutionizing the manufacturing industry, especially in bar feeding operations. These advanced technologies, including artificial intelligence, the Internet of Things, and cloud computing, are enabling manufacturers […]
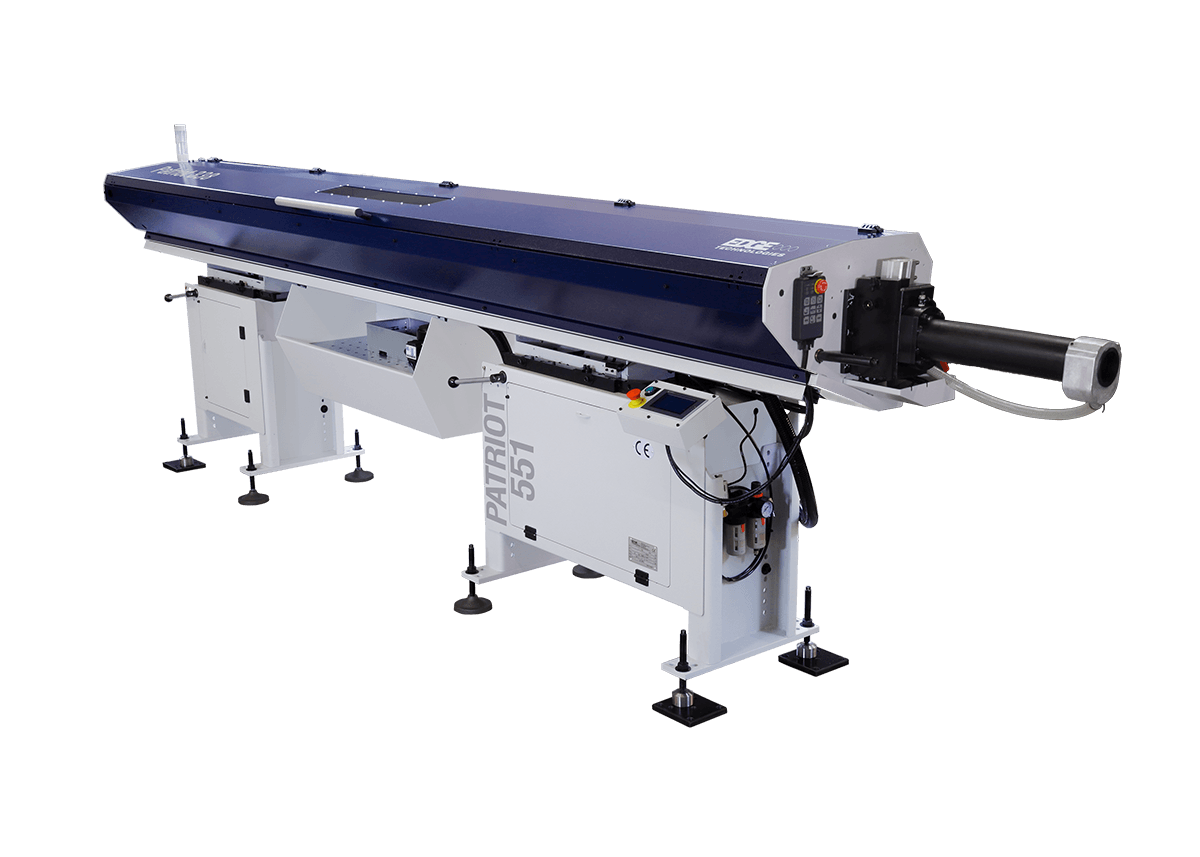
Edge technologies bar feeder are revolutionizing the manufacturing industry, especially in bar feeding operations. These advanced technologies, including artificial intelligence, the Internet of Things, and cloud computing, are enabling manufacturers to optimize their processes, improve efficiency, and achieve greater accuracy and precision.
Bar feeders play a crucial role in manufacturing by automating the feeding of raw materials, such as bars and rods, into machining centers. Edge technologies are transforming this process by enhancing automation, data analysis, and predictive maintenance capabilities, ultimately leading to significant improvements in production efficiency and overall manufacturing performance.
Introduction to Edge Technologies in Bar Feeding
The manufacturing industry is constantly evolving, with new technologies emerging to improve efficiency, accuracy, and productivity. Edge technologies, specifically, are playing a significant role in transforming various manufacturing processes, including bar feeding.
Bar feeders are essential components in CNC machining, supplying material to machine tools for automated operation. Edge technologies are enhancing the capabilities of bar feeders, leading to more efficient, precise, and flexible production.
Impact of Edge Technologies on Bar Feeding Operations
Edge technologies are revolutionizing bar feeding operations, offering numerous benefits that enhance overall manufacturing processes. These technologies enable manufacturers to achieve greater efficiency, accuracy, and flexibility in their production lines.
- Improved Efficiency: Edge technologies streamline bar feeding operations, reducing downtime and increasing throughput. For example, automated bar loading systems can automatically load and unload bars, minimizing manual intervention and reducing the time required for setup and operation.
- Enhanced Accuracy: Advanced sensors and control systems, driven by edge technologies, ensure precise bar feeding, minimizing material waste and improving the quality of finished products. For example, real-time monitoring systems can track bar length and diameter, ensuring accurate feeding and preventing errors that could lead to defects.
- Increased Flexibility: Edge technologies enable bar feeders to handle a wider range of materials and sizes, allowing for greater flexibility in production. For example, adaptive control systems can adjust feeding parameters based on the specific material and size of the bar, allowing for efficient processing of various materials.
- Remote Monitoring and Control: Edge technologies facilitate remote monitoring and control of bar feeding operations, enabling operators to monitor machine performance and make adjustments remotely. This enhances efficiency and allows for proactive maintenance, minimizing downtime and production disruptions.
Key Edge Technologies in Bar Feeding
The bar feeding industry is constantly evolving, with the integration of advanced technologies enhancing efficiency, precision, and overall productivity. These technologies, often referred to as “edge technologies,” are transforming the way bar feeding systems operate, enabling manufacturers to achieve greater levels of automation and optimization.
Artificial Intelligence (AI) in Bar Feeding Optimization
AI is revolutionizing bar feeding by providing intelligent insights and automated decision-making capabilities. By analyzing vast amounts of data collected from sensors and machine operations, AI algorithms can identify patterns, predict potential issues, and optimize various aspects of the bar feeding process.
- Predictive Maintenance: AI can analyze historical data and real-time sensor readings to anticipate machine failures and schedule preventative maintenance, minimizing downtime and ensuring continuous production.
- Process Optimization: AI algorithms can analyze bar feeding parameters, such as feed rate, cutting speed, and tool wear, to identify optimal settings for different materials and machining tasks, resulting in improved efficiency and reduced waste.
- Quality Control: AI-powered vision systems can inspect bar stock for defects, ensuring consistent material quality and preventing the use of defective bars, reducing scrap and rework.
Internet of Things (IoT) Sensors in Bar Feeding Systems
IoT sensors play a crucial role in collecting real-time data from various components within bar feeding systems, providing valuable insights into system performance and enabling data-driven decision-making.
- Real-time Monitoring: Sensors can monitor key parameters like bar length, feed rate, tool wear, and machine temperature, providing real-time data that can be used to optimize operations and identify potential issues.
- Remote Monitoring and Diagnostics: IoT connectivity allows remote access to sensor data, enabling operators to monitor system performance from anywhere, facilitating proactive maintenance and troubleshooting.
- Data Collection and Analysis: IoT sensors generate vast amounts of data that can be analyzed to identify trends, optimize processes, and improve overall system efficiency.
Cloud Computing for Data Management and Analysis
Cloud computing provides a scalable and secure platform for storing, managing, and analyzing the massive amounts of data generated by IoT sensors and AI algorithms in bar feeding systems.
- Data Storage and Security: Cloud-based data storage offers secure and scalable solutions for storing large datasets, ensuring data integrity and availability.
- Data Analytics and Visualization: Cloud platforms provide powerful analytics tools that enable users to visualize data, identify trends, and gain insights into system performance.
- Collaboration and Data Sharing: Cloud computing facilitates data sharing and collaboration among different stakeholders, enabling manufacturers to optimize operations across multiple facilities.
Robotics and Automation in Bar Feeding
Robotics and automation are transforming bar feeding operations, increasing efficiency, precision, and safety.
- Automated Bar Loading and Unloading: Robots can automate the loading and unloading of bar stock, reducing manual labor and improving safety.
- Automated Bar Handling and Positioning: Robots can precisely handle and position bars, ensuring accurate feeding and minimizing material waste.
- Integration with Machine Tools: Automated bar feeding systems can be seamlessly integrated with machine tools, creating a fully automated production line.
Applications of Edge Technologies in Bar Feeding
Edge technologies play a crucial role in enhancing the efficiency, accuracy, and automation of bar feeding systems, particularly in high-speed machining applications. These technologies enable real-time data collection, analysis, and control, optimizing bar feeding processes for improved productivity and quality.
Edge Technologies in High-Speed Machining
High-speed machining demands precise and rapid material removal, requiring advanced bar feeding systems that can keep up with the pace. Edge technologies like real-time monitoring, predictive maintenance, and adaptive control systems are essential for ensuring uninterrupted operation and optimal performance in such demanding environments.
- Real-time monitoring of critical parameters like bar length, feed rate, and tool wear provides insights into the machining process, enabling adjustments to maintain optimal cutting conditions and prevent tool breakage. This ensures uninterrupted production and minimizes downtime.
- Predictive maintenance algorithms analyze sensor data to anticipate potential failures in the bar feeding system, allowing for proactive maintenance and minimizing unplanned downtime. This approach ensures continuous operation and reduces maintenance costs.
- Adaptive control systems adjust the bar feeding rate and other parameters based on real-time data from sensors, optimizing the machining process for different materials and cutting conditions. This results in improved surface finish, dimensional accuracy, and overall machining efficiency.
Edge Technologies for Improved Accuracy and Precision
Edge technologies contribute significantly to enhancing the accuracy and precision of bar feeding systems, leading to improved part quality and reduced scrap rates.
- Vision systems integrated into the bar feeding system can precisely identify and measure bar dimensions, ensuring accurate material loading and minimizing errors in the cutting process. This results in consistent part dimensions and reduces scrap due to misfeeding or inaccurate material length.
- Advanced sensors, such as laser displacement sensors, can monitor bar position and movement with high accuracy, providing real-time feedback to the control system for precise bar feeding. This minimizes variations in bar feed rates and ensures accurate material delivery to the machine.
- Machine learning algorithms can analyze data from sensors and vision systems to identify patterns and predict potential errors in the bar feeding process. This allows for proactive adjustments and preventive measures, further improving accuracy and precision.
Edge Technologies in Automated Bar Feeding Systems
Edge technologies play a crucial role in automating bar feeding systems, increasing efficiency, reducing labor requirements, and improving overall process reliability.
- Automated bar loading systems use sensors and robotics to load bars into the feeding system automatically, minimizing manual intervention and reducing the risk of human error. This improves efficiency and frees up operators for other tasks.
- Robotic bar handling enables automated bar manipulation, including loading, unloading, and transferring bars between different machines. This eliminates the need for manual handling, reducing the risk of accidents and improving overall safety.
- Remote monitoring and control systems allow operators to monitor and control the bar feeding system from a distance, enabling real-time adjustments and troubleshooting. This provides greater flexibility and reduces the need for on-site personnel.
Case Studies of Successful Edge Technology Implementations in Bar Feeding
Several successful case studies demonstrate the benefits of implementing edge technologies in bar feeding systems.
- Company A, a manufacturer of precision components, implemented a vision system integrated with their bar feeding system. This resulted in a significant reduction in scrap rates, improved part accuracy, and increased production efficiency.
- Company B, a leading automotive parts supplier, adopted a predictive maintenance system for their automated bar feeding system. This approach minimized downtime due to unexpected failures, reduced maintenance costs, and ensured continuous production.
- Company C, a manufacturer of medical devices, implemented a robotic bar handling system to automate their bar feeding process. This resulted in improved accuracy, reduced labor requirements, and enhanced safety in the manufacturing environment.
Future Trends in Edge Technologies for Bar Feeding
The realm of bar feeding is poised for a significant transformation as emerging technologies continue to reshape manufacturing processes. From the rise of 5G connectivity to the integration of predictive maintenance, edge technologies are set to revolutionize bar feeding operations, enhancing efficiency, reducing costs, and promoting sustainability.
5G Connectivity in Bar Feeding Operations, Edge technologies bar feeder
The advent of 5G connectivity will dramatically impact bar feeding operations, paving the way for a more connected and responsive manufacturing environment. With its ultra-low latency and high bandwidth capabilities, 5G will enable real-time data exchange between bar feeders, CNC machines, and other equipment, fostering seamless communication and enhanced control.
The potential of 5G in bar feeding lies in its ability to facilitate remote monitoring, real-time data analysis, and predictive maintenance, ultimately leading to improved operational efficiency and reduced downtime.
Predictive Maintenance for Optimized Bar Feeder Performance
Predictive maintenance leverages data analytics and machine learning algorithms to anticipate potential equipment failures, allowing for proactive maintenance interventions before breakdowns occur. By analyzing sensor data from bar feeders, predictive maintenance systems can identify patterns and anomalies, providing early warnings of impending issues.
Predictive maintenance empowers manufacturers to optimize bar feeder performance by reducing unscheduled downtime, minimizing repair costs, and extending the lifespan of equipment.
Impact of Edge Technologies on Bar Feeding
Edge technologies are poised to significantly impact bar feeding efficiency, cost reduction, and sustainability. The table below Artikels the expected impact of these technologies across these key areas:
Area | Impact of Edge Technologies |
---|---|
Efficiency | – Improved data analysis and real-time monitoring for enhanced productivity. – Optimized bar loading and unloading processes for reduced cycle times. – Automated process adjustments for increased throughput. |
Cost Reduction | – Reduced downtime and maintenance costs through predictive maintenance. – Optimized material usage and reduced waste through real-time monitoring and control. – Improved process efficiency and reduced energy consumption. |
Sustainability | – Reduced waste generation through optimized material utilization and process control. – Minimized energy consumption through efficient operations and predictive maintenance. – Enhanced environmental performance through reduced emissions and resource utilization. |
Challenges and Considerations for Implementing Edge Technologies in Bar Feeding: Edge Technologies Bar Feeder
The integration of edge technologies into existing bar feeding systems presents a unique set of challenges and considerations. These challenges stem from the need to adapt legacy systems, address security concerns, and ensure data privacy while reaping the benefits of edge computing.
Challenges of Integrating Edge Technologies
The integration of edge technologies into existing bar feeding systems poses several challenges.
- Legacy System Compatibility: Many bar feeding systems are based on older technologies, making it challenging to integrate modern edge devices and software. Upgrading or replacing existing infrastructure can be costly and time-consuming.
- Data Connectivity and Bandwidth: Edge devices require reliable and high-bandwidth connectivity to transmit data to the cloud or other systems. This can be a challenge in manufacturing environments with limited network infrastructure or fluctuating connectivity.
- Deployment and Maintenance: Deploying and maintaining edge devices in a manufacturing setting requires specialized expertise and can be complex due to the harsh environment and the need for regular updates and security patches.
Security Risks Associated with Edge Technologies
Edge technologies introduce new security risks that need to be addressed.
- Data Breaches: Edge devices store and process sensitive data, making them vulnerable to cyberattacks. Hackers could exploit vulnerabilities in the devices or the network to steal data or disrupt operations.
- Unauthorized Access: Edge devices can be accessed remotely, creating opportunities for unauthorized users to gain access to data or control the devices. Strong authentication and authorization mechanisms are essential to prevent unauthorized access.
- Device Tampering: Edge devices can be physically tampered with, compromising their security and integrity. Secure hardware and software design, as well as physical security measures, are crucial to prevent tampering.
Data Privacy and Security in Edge-Enabled Bar Feeding
Data privacy and security are paramount in edge-enabled bar feeding systems.
- Data Encryption: All data transmitted and stored on edge devices should be encrypted to protect it from unauthorized access. Encryption algorithms should be robust and regularly updated to stay ahead of evolving threats.
- Data Access Control: Access to data stored on edge devices should be restricted to authorized personnel. Access control mechanisms should be implemented to ensure only authorized users can view, modify, or delete data.
- Data Retention and Disposal: Data retention policies should be established to determine how long data is stored on edge devices and how it is disposed of when no longer needed. This helps to prevent unauthorized access to sensitive data and comply with relevant regulations.
Recommendations for Overcoming Challenges and Ensuring Successful Implementation
Overcoming the challenges and ensuring successful implementation of edge technologies in bar feeding requires a comprehensive approach.
- Start with a Pilot Project: Implementing edge technologies in a small-scale pilot project allows for testing and evaluation before a full-scale deployment. This helps identify potential challenges and refine the implementation strategy.
- Invest in Security Measures: Robust security measures, including strong authentication, encryption, and access control, are essential to protect data and devices from cyberattacks. Regular security audits and updates are also crucial to maintain security.
- Partner with Experienced Vendors: Collaborating with experienced vendors who specialize in edge technologies can provide valuable expertise and support for deployment and maintenance. This can help mitigate risks and ensure successful implementation.
- Develop a Comprehensive Data Privacy and Security Policy: A comprehensive data privacy and security policy should be developed and implemented to guide the collection, use, storage, and disposal of data. This policy should be aligned with relevant regulations and industry best practices.
Summary
The integration of edge technologies in bar feeding operations is poised to unlock a new era of efficiency and innovation in manufacturing. As these technologies continue to evolve and become more readily available, we can expect to see even greater advancements in bar feeding automation, precision, and overall manufacturing productivity. The future of bar feeding is bright, driven by the transformative power of edge technologies.
Edge technologies in bar feeders are constantly evolving, aiming to improve efficiency and accuracy in manufacturing. One notable innovation in this field is the transcell technology ti 500e , a compact and reliable system designed to optimize bar feeding processes.
By incorporating advanced features like automatic bar length detection and precise bar handling, the ti 500e contributes to the overall advancement of edge technologies in bar feeders.