ACH Foam Technologies: A Revolutionary Material
ACH foam technologies, a revolutionary material, have reshaped various industries with their unique properties and applications. From their humble beginnings, ACH foams have evolved into a versatile and sustainable solution […]
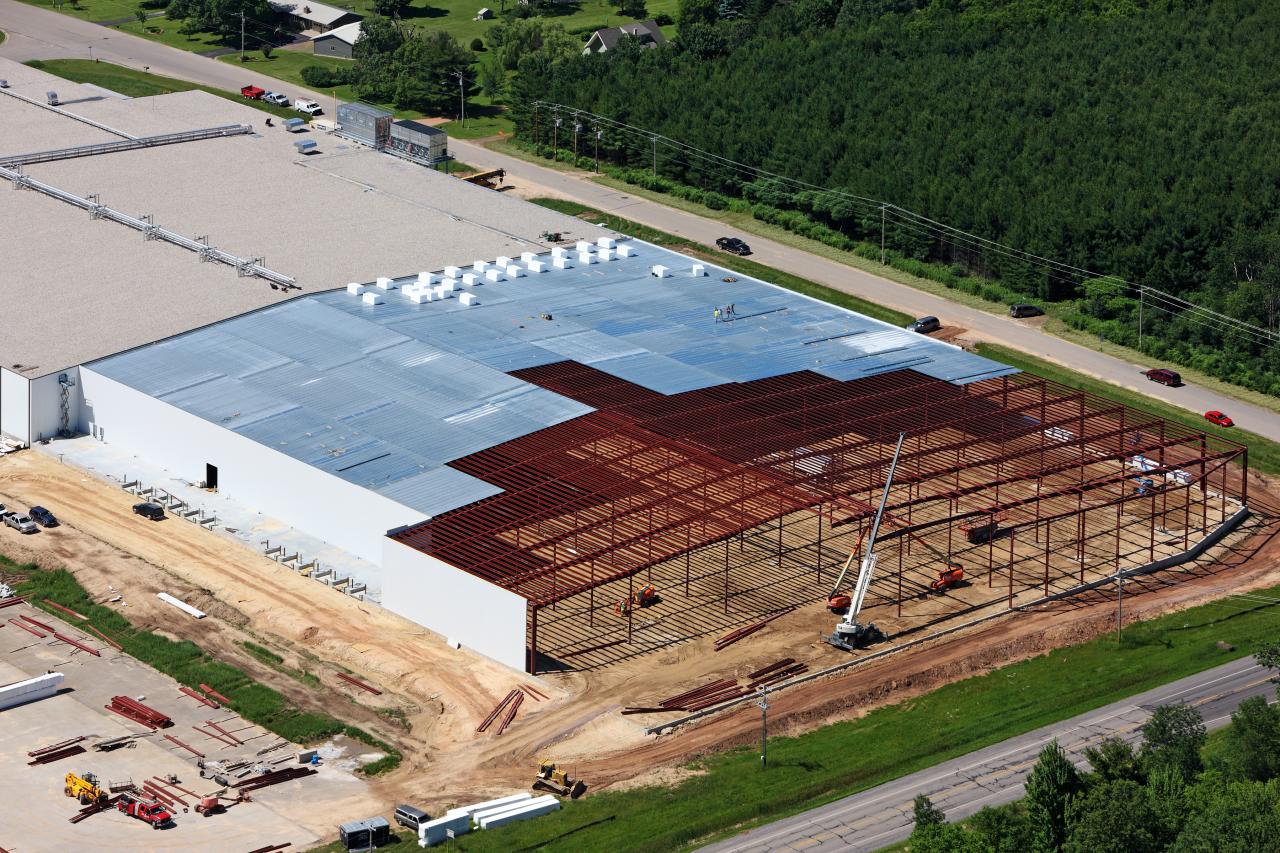
ACH foam technologies, a revolutionary material, have reshaped various industries with their unique properties and applications. From their humble beginnings, ACH foams have evolved into a versatile and sustainable solution for numerous challenges across diverse sectors.
This article delves into the fascinating world of ACH foam technologies, exploring their history, properties, manufacturing processes, and diverse applications. We will also discuss the future trends and innovations shaping this dynamic field, highlighting its potential to drive further progress in sustainability and innovation.
Introduction to ACH Foam Technologies
ACH foam technologies have revolutionized the way we think about cushioning and insulation. The journey of this innovative material spans decades, marked by constant development and refinement.
History and Evolution of ACH Foam Technologies
ACH foam technology originated in the early 20th century, with the development of polyurethane foam. This initial foam was relatively simple in its structure and had limited applications. However, the inherent properties of polyurethane, such as its flexibility, cushioning, and insulation, made it a promising material for further development.
Over the years, researchers and engineers have made significant strides in refining polyurethane foam technology. The development of advanced chemical formulations, precise manufacturing techniques, and innovative processing methods have led to the creation of high-performance ACH foams with unique properties.
- Increased Density and Strength: ACH foams have become denser and stronger, enabling them to withstand heavier loads and provide more durable support.
- Enhanced Cushioning: Advanced formulations have resulted in foams with superior shock absorption capabilities, offering improved comfort and protection.
- Improved Insulation: ACH foams now provide superior thermal and acoustic insulation, making them ideal for a wide range of applications.
- Customizable Properties: Modern ACH foam technologies allow for precise control over the foam’s density, resilience, and other properties, making it adaptable to specific needs.
Key Applications of ACH Foam
ACH foams have found their way into a vast array of industries, revolutionizing product design and functionality. Their versatility and performance make them indispensable in various sectors.
- Furniture: ACH foams are widely used in furniture manufacturing, providing comfort and support in cushions, mattresses, and seating.
- Automotive: ACH foams play a crucial role in automotive interiors, providing sound insulation, thermal protection, and impact absorption.
- Construction: ACH foams are used as insulation materials in buildings, reducing energy consumption and improving indoor comfort.
- Packaging: ACH foams are excellent packaging materials, offering protection against shock, vibration, and environmental factors.
- Sports and Recreation: ACH foams are found in sports equipment, providing cushioning and support for athletes.
Innovative Uses of ACH Foam in Modern Products, Ach foam technologies
The innovative nature of ACH foam technologies has led to the development of novel products that push the boundaries of design and functionality.
- Smart Cushioning: ACH foams are being integrated with sensors and electronics, creating smart cushions that adapt to user preferences and provide personalized comfort.
- Self-Healing Foams: Researchers are developing ACH foams that can repair themselves after damage, extending their lifespan and reducing waste.
- Biodegradable Foams: The environmental impact of traditional foams is being addressed by the development of biodegradable ACH foams that decompose naturally, reducing landfill waste.
- 3D-Printed Foams: Advanced manufacturing techniques like 3D printing are being used to create custom-designed ACH foams with complex shapes and functionalities.
Properties and Advantages of ACH Foam
ACH foam, also known as acrylic closed-cell foam, is a versatile material with unique properties that make it ideal for various applications. Its closed-cell structure, which consists of tiny air-filled cells, gives it distinct physical and chemical characteristics that contribute to its advantages.
Physical Properties of ACH Foam
The closed-cell structure of ACH foam contributes to its exceptional physical properties. It is lightweight yet strong, providing excellent resistance to compression and impact. This strength and durability make it suitable for use in demanding environments. Its low thermal conductivity and high resistance to moisture make it an excellent insulator, effectively reducing heat transfer and preventing water absorption. These properties make ACH foam a valuable material for thermal insulation in buildings and other structures.
Advantages of ACH Foam Compared to Other Materials
ACH foam offers several advantages over traditional materials used in construction and insulation. Its high compressive strength and resilience make it a durable and long-lasting material, capable of withstanding significant loads and impact. ACH foam’s closed-cell structure makes it highly resistant to moisture absorption, preventing water damage and maintaining its insulating properties over time. This resistance to moisture also makes it suitable for use in damp environments. Compared to other insulation materials, ACH foam offers a superior thermal performance, effectively reducing heat loss in winter and heat gain in summer. Its lightweight nature also makes it easier to handle and install, reducing labor costs and improving efficiency.
Sustainability and Environmental Impact of ACH Foam
ACH foam is a sustainable and environmentally friendly material. Its closed-cell structure makes it highly resistant to mold and mildew growth, reducing the need for chemical treatments and promoting a healthier indoor environment. The material is also recyclable, minimizing waste and contributing to a circular economy. Its excellent thermal performance contributes to energy efficiency in buildings, reducing energy consumption and lowering greenhouse gas emissions. ACH foam’s long lifespan and resistance to degradation also minimize the need for replacements, further reducing its environmental footprint.
Manufacturing Processes of ACH Foam
The creation of ACH foam involves a series of intricate processes that dictate the final properties and applications of the material. This section delves into the diverse manufacturing techniques employed to produce ACH foam, highlighting their unique characteristics and advantages.
ACH Foam Manufacturing Techniques
ACH foam manufacturing involves a series of steps that transform raw materials into a lightweight, resilient, and durable foam. The key manufacturing techniques are:
- Extrusion: This process involves forcing a mixture of liquid polymers and blowing agents through a die, creating a continuous foam sheet. This method is ideal for producing large quantities of ACH foam with consistent density and uniform cell structure.
- Injection Molding: This technique involves injecting a mixture of liquid polymers and blowing agents into a mold, where the foam expands and solidifies. Injection molding is particularly suited for creating complex shapes and intricate designs in ACH foam.
- Reaction Injection Molding (RIM): This method involves mixing two liquid components, a polyol and an isocyanate, in a mold. The reaction between these components generates heat, causing the mixture to foam and solidify. RIM is well-suited for producing large, lightweight, and durable ACH foam components.
Comparison of ACH Foam Manufacturing Techniques
Technique | Advantages | Disadvantages |
---|---|---|
Extrusion | High production rate, consistent density, uniform cell structure | Limited design flexibility, potential for surface imperfections |
Injection Molding | High design flexibility, intricate shapes possible, excellent dimensional control | Lower production rate compared to extrusion, potential for sink marks |
Reaction Injection Molding (RIM) | Large component production, high strength-to-weight ratio, good surface finish | Higher capital investment, potential for uneven foam density |
Flowchart of ACH Foam Manufacturing Process
[Flowchart]
The flowchart depicts the key steps involved in the manufacturing process of ACH foam. It starts with the preparation of raw materials, including polymers, blowing agents, and additives. These materials are then mixed and processed according to the chosen manufacturing technique. The mixture is then injected into a mold or extruded through a die, where it expands and solidifies. Finally, the ACH foam is inspected, trimmed, and packaged for distribution.
Applications of ACH Foam in Various Industries
ACH foam’s versatility and unique properties make it suitable for a wide range of applications across diverse industries. From construction and automotive to aerospace and packaging, ACH foam plays a vital role in enhancing performance, safety, and efficiency.
ACH Foam in Construction
ACH foam finds extensive use in the construction industry due to its exceptional thermal insulation, sound absorption, and structural reinforcement properties.
- Insulation: ACH foam’s closed-cell structure provides superior thermal insulation, preventing heat loss in buildings and reducing energy consumption. It is commonly used in wall and roof insulation, creating comfortable and energy-efficient living spaces.
- Sound Absorption: ACH foam’s porous structure effectively absorbs sound waves, reducing noise levels in buildings and improving acoustic comfort. It is widely used in wall and ceiling panels, as well as in acoustic barriers for noise control.
- Structural Reinforcement: ACH foam can be incorporated into concrete structures to enhance their strength and durability. It acts as a lightweight filler, reducing the weight of concrete while improving its structural integrity.
ACH Foam in Automotive
The automotive industry leverages ACH foam’s lightweight, impact-absorbing, and thermal insulation properties to enhance vehicle performance and safety.
- Interior Components: ACH foam is widely used in car interiors for dashboard padding, seat cushions, and headliners, providing comfort, sound insulation, and impact protection.
- Underbody Protection: ACH foam is used in underbody panels to protect the vehicle from damage caused by road debris and other impacts. Its lightweight nature helps maintain vehicle efficiency.
- Engine Bay Insulation: ACH foam is used in engine compartments to insulate against heat, reducing noise and improving engine performance.
ACH Foam in Aerospace
The aerospace industry utilizes ACH foam’s lightweight, high-strength, and thermal insulation properties for critical applications.
- Aircraft Interiors: ACH foam is used in aircraft interiors for cabin insulation, sound absorption, and impact protection, enhancing passenger comfort and safety.
- Structural Components: ACH foam is used in aircraft structural components, such as wings and fuselage, providing lightweight reinforcement and impact resistance.
- Thermal Protection: ACH foam is used as a thermal barrier in spacecraft and rockets, protecting sensitive components from extreme temperatures.
ACH Foam in Packaging
ACH foam’s protective and cushioning properties make it an ideal material for packaging delicate and fragile goods.
- Protective Packaging: ACH foam is used as a cushioning material in packaging for electronics, appliances, and other fragile items, preventing damage during shipping and handling.
- Insulated Packaging: ACH foam is used in packaging for temperature-sensitive products, such as pharmaceuticals and food, to maintain their quality and prevent spoilage.
- Customizable Packaging: ACH foam can be easily molded and shaped to create custom packaging solutions for specific products, ensuring a secure and protective fit.
Final Thoughts: Ach Foam Technologies
As we conclude our exploration of ACH foam technologies, it is evident that these materials are poised to play an increasingly pivotal role in shaping the future. Their remarkable properties, coupled with ongoing research and development, promise to unlock a new era of sustainable solutions and innovative applications across diverse industries.
ACH foam technologies are known for their versatility and adaptability, finding applications in diverse fields. From cushioning in sports equipment to soundproofing in buildings, their ability to conform and absorb impact makes them a valuable material. Interestingly, a similar focus on comfort and precision is seen in the development of new teeth braces technology , which utilizes advanced materials and designs to minimize discomfort and enhance treatment efficiency.
Like ACH foam, these new braces aim to provide a more personalized and comfortable experience, ultimately leading to improved outcomes.