SPC Technologies: Optimizing Processes for Quality
SPC technologies, or Statistical Process Control, are a powerful set of tools used to improve the efficiency and quality of processes across a wide range of industries. From manufacturing to […]
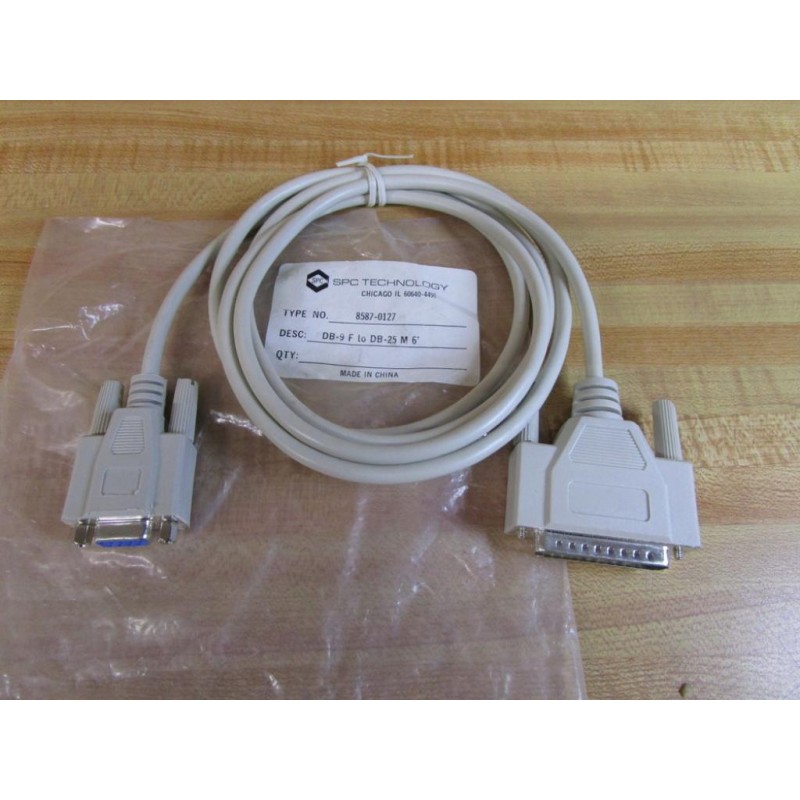
SPC technologies, or Statistical Process Control, are a powerful set of tools used to improve the efficiency and quality of processes across a wide range of industries. From manufacturing to healthcare, SPC technologies help organizations identify and eliminate sources of variation, leading to consistent results and increased customer satisfaction.
SPC technologies are based on the principle of using data to monitor and control processes. By collecting and analyzing data on key process variables, organizations can identify trends, patterns, and potential problems before they become significant issues. This proactive approach allows for timely adjustments and improvements, ultimately leading to greater efficiency and effectiveness.
Key Components of SPC Technologies
SPC technologies are a set of tools and methods used to monitor and control the variability of processes. They are essential for organizations that want to improve the quality of their products or services and reduce costs.
Statistical Process Control Charts, Spc technologies
SPC charts are graphical representations of data collected over time. They are used to monitor the process and identify any deviations from the expected behavior.
- X-bar and R charts: These charts are used to monitor the average and range of a process. They are suitable for monitoring processes with continuous data, such as the weight of a product or the temperature of a reaction.
- p charts: These charts are used to monitor the proportion of defective units in a sample. They are suitable for monitoring processes with discrete data, such as the number of defective parts in a batch.
- c charts: These charts are used to monitor the number of defects per unit. They are suitable for monitoring processes where the number of defects is important, such as the number of scratches on a surface.
Data Collection Methods
Data collection is a critical step in SPC. Accurate and reliable data is essential for effective process monitoring and control.
- Manual data collection: This method involves manually recording data from the process. It is a simple and inexpensive method but can be time-consuming and prone to errors.
- Automated data collection: This method involves using sensors or other devices to automatically collect data from the process. It is more accurate and efficient than manual data collection but can be more expensive.
- Statistical sampling: This method involves collecting data from a representative sample of the process. It is a cost-effective way to collect data and can be used to estimate the overall process performance.
Analysis Tools
Data analysis is an essential part of SPC. It helps to identify trends, patterns, and anomalies in the data.
- Descriptive statistics: These tools are used to summarize and describe the data. They include measures such as the mean, standard deviation, and range.
- Control chart analysis: This method involves using control charts to identify points outside the control limits, which indicate potential process problems.
- Hypothesis testing: This method is used to test hypotheses about the process. For example, a hypothesis test can be used to determine if a change in the process has had a significant effect on the output.
Role of Data Analysis and Interpretation in SPC Technologies
Data analysis and interpretation play a crucial role in SPC technologies. They help to:
- Identify process variation: By analyzing data collected over time, SPC tools can identify patterns and trends in process variation.
- Determine the root causes of variation: Once variation is identified, data analysis can help to determine the root causes, such as changes in materials, equipment, or operator behavior.
- Monitor process performance: SPC charts provide a visual representation of process performance over time, allowing for early detection of problems and timely corrective action.
- Evaluate the effectiveness of process improvements: SPC tools can be used to evaluate the effectiveness of changes made to the process, ensuring that improvements are actually resulting in better performance.
SPC Technologies and Industry 4.0
The integration of SPC technologies with Industry 4.0 principles, such as the Internet of Things (IoT) and Big Data analytics, is revolutionizing manufacturing processes and driving significant improvements in efficiency, quality, and productivity.
SPC Technologies and the Internet of Things
The Internet of Things (IoT) plays a crucial role in enabling real-time data collection and analysis, which is essential for effective SPC implementation. By connecting sensors and devices across the manufacturing process, IoT facilitates continuous monitoring of key process parameters. This real-time data stream enables SPC software to identify deviations from target values immediately, triggering alerts and enabling timely corrective actions.
SPC Technologies and Big Data Analytics
Big Data analytics empowers SPC technologies to extract valuable insights from the massive amounts of data generated by IoT-connected devices. This data can be analyzed to identify patterns, trends, and root causes of process variations. By leveraging advanced analytics techniques, SPC software can provide predictive insights into potential process issues, allowing manufacturers to proactively address problems before they impact production quality.
SPC Technologies and Real-Time Process Monitoring
SPC technologies, in conjunction with IoT and Big Data analytics, enable real-time process monitoring, allowing manufacturers to track and control process variations in real-time. This continuous monitoring provides a comprehensive view of the manufacturing process, enabling prompt detection and correction of deviations from target values.
SPC Technologies and Predictive Maintenance
Predictive maintenance, a key component of Industry 4.0, leverages SPC technologies to predict potential equipment failures and schedule maintenance proactively. By analyzing historical data on equipment performance and process parameters, SPC software can identify patterns that indicate impending failures. This allows manufacturers to schedule maintenance before failures occur, minimizing downtime and ensuring uninterrupted production.
SPC Technologies and Automation
SPC technologies can significantly enhance automation in Industry 4.0 environments. By integrating with automated systems, SPC software can trigger automated adjustments to process parameters based on real-time data analysis. This automation reduces manual intervention and improves consistency in production processes.
SPC Technologies and Decision-Making
SPC technologies provide valuable data and insights that support informed decision-making in Industry 4.0 environments. By analyzing process data and identifying trends, SPC software enables manufacturers to optimize process parameters, improve quality control, and make data-driven decisions regarding production planning and resource allocation.
Final Thoughts: Spc Technologies
As we move into the future, SPC technologies are becoming increasingly sophisticated, incorporating advanced analytics, machine learning, and artificial intelligence. This evolution will enable organizations to further optimize their processes, improve decision-making, and gain a competitive edge. SPC technologies are not simply a set of tools but a powerful framework for continuous improvement, ensuring that organizations can consistently deliver high-quality products and services.
SPC technologies are a vital part of modern manufacturing, offering a wide range of solutions for precise and efficient production. For applications requiring high-volume, high-quality coatings, the CA Technologies air-assisted airless system provides an ideal solution. This technology combines the benefits of airless spraying with the control and atomization of air-assisted systems, making it a popular choice in various industries.
By integrating such advanced technologies, SPC continues to drive innovation and efficiency in manufacturing processes.