Laser Marking Technologies Dominator: Shaping Industries
Laser marking technologies dominator, a phrase that captures the essence of a rapidly evolving field, has revolutionized how we mark and identify products across various industries. From intricate medical devices […]
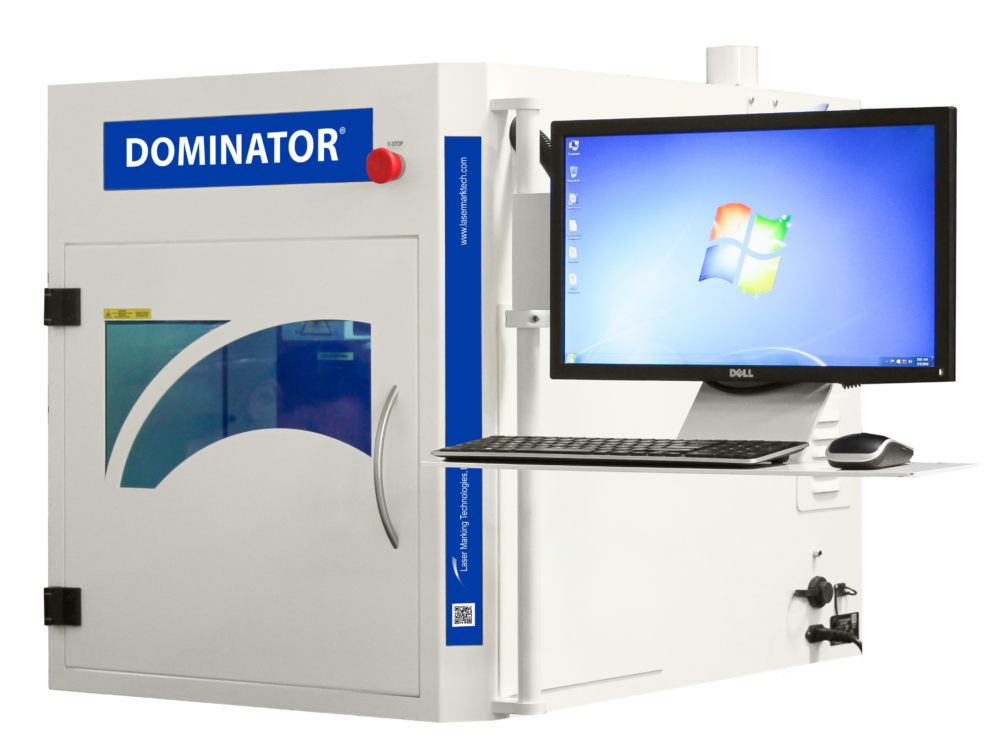
Laser marking technologies dominator, a phrase that captures the essence of a rapidly evolving field, has revolutionized how we mark and identify products across various industries. From intricate medical devices to durable automotive parts, laser marking offers unmatched precision, speed, and versatility.
This technology, driven by advancements in laser sources, optics, and software, allows for permanent and high-resolution markings on a wide range of materials. It has become a critical component in manufacturing, enabling traceability, product authentication, and brand protection.
Challenges and Opportunities in Laser Marking
Laser marking technologies have revolutionized the way we identify and track products, creating a wide range of applications in various industries. However, like any technology, laser marking faces challenges and opportunities for growth and advancement. This section will explore the challenges faced by dominant laser marking technologies, discuss the opportunities for innovation and improvement, and analyze the potential impact of emerging technologies on the future of laser marking.
Challenges in Laser Marking Technologies, Laser marking technologies dominator
The dominant laser marking technologies, including fiber lasers, CO2 lasers, and UV lasers, face several challenges, including limitations, cost considerations, and environmental concerns. These challenges can hinder the adoption of laser marking technologies in certain applications and drive the need for further innovation.
- Limitations of Laser Marking Technologies: Laser marking technologies have limitations in terms of the materials they can mark, the depth of the mark, and the complexity of the designs that can be achieved. For example, marking certain plastics or very hard materials can be challenging. The depth of the mark is limited by the laser power and the material properties, and intricate designs may require advanced laser systems or multiple passes.
- Cost Considerations: Laser marking systems can be expensive to purchase and maintain. The cost of the laser itself, the supporting equipment, and the consumables can be significant, especially for high-power or specialized systems. The cost of training operators and ensuring proper system maintenance can also be a factor.
- Environmental Concerns: Laser marking processes can generate waste materials, such as dust or fumes, depending on the material being marked and the laser type. These byproducts need to be managed and disposed of properly to minimize environmental impact. Some laser systems also require cooling systems, which can consume energy and contribute to greenhouse gas emissions.
Opportunities for Innovation and Improvement in Laser Marking
Despite the challenges, laser marking technologies offer significant opportunities for innovation and improvement. Advancements in laser technology, materials science, and automation are creating new possibilities for marking applications and improving the efficiency and effectiveness of laser marking systems.
- Development of New Laser Sources: Researchers are continuously developing new laser sources with improved characteristics, such as higher power, shorter pulse durations, and better beam quality. These advancements enable the marking of a wider range of materials, the creation of deeper and more intricate marks, and the reduction of processing time.
- Integration of Automation and Robotics: The integration of automation and robotics into laser marking systems can enhance production efficiency, reduce labor costs, and improve accuracy and repeatability. Automated systems can handle complex tasks, such as part loading and unloading, mark positioning, and quality control, allowing for high-volume production with minimal human intervention.
- Development of Advanced Marking Techniques: New marking techniques, such as laser-induced forward transfer (LIFT) and direct laser interference patterning (DLIP), offer unique capabilities for creating complex three-dimensional structures and micro-features. These techniques are finding applications in areas like microelectronics, medical devices, and bio-printing.
Impact of Emerging Technologies on Laser Marking
Emerging technologies, such as artificial intelligence (AI), machine learning (ML), and the Internet of Things (IoT), are poised to have a significant impact on the future of laser marking. These technologies can enhance the capabilities of laser marking systems, improve process control, and enable new applications.
- AI-Powered Optimization: AI algorithms can analyze data from laser marking processes to optimize system parameters, such as laser power, scan speed, and marking depth. This can improve the efficiency, accuracy, and consistency of the marking process.
- Machine Learning for Quality Control: ML models can be trained to detect defects in laser-marked products, enabling real-time quality control and reducing the risk of defective products reaching the market.
- IoT Integration for Remote Monitoring and Control: IoT-enabled laser marking systems can be remotely monitored and controlled, allowing for real-time data collection, predictive maintenance, and remote troubleshooting.
Wrap-Up: Laser Marking Technologies Dominator
As we delve deeper into the world of laser marking technologies dominator, it becomes clear that this field is poised for continued growth and innovation. The future holds exciting possibilities for further miniaturization, automation, and sustainable solutions. With its ability to adapt to evolving industry needs, laser marking technology will undoubtedly remain a dominant force in shaping the future of manufacturing and beyond.
Laser marking technologies have become a dominant force in many industries, offering precision and durability that traditional methods can’t match. However, achieving optimal results often requires meticulous surface preparation, and this is where Franklin cleaning technology excels. Their specialized solutions effectively remove contaminants and residues, ensuring that laser marking processes operate efficiently and deliver consistent, high-quality results.
By integrating these two technologies, manufacturers can unlock the full potential of laser marking, leading to superior product quality and increased productivity.