Car Body Technology: Evolution and Innovation
Car body technology has undergone a remarkable transformation, evolving from simple steel frames to sophisticated composite structures. This journey reflects advancements in materials science, manufacturing processes, and design principles, all […]
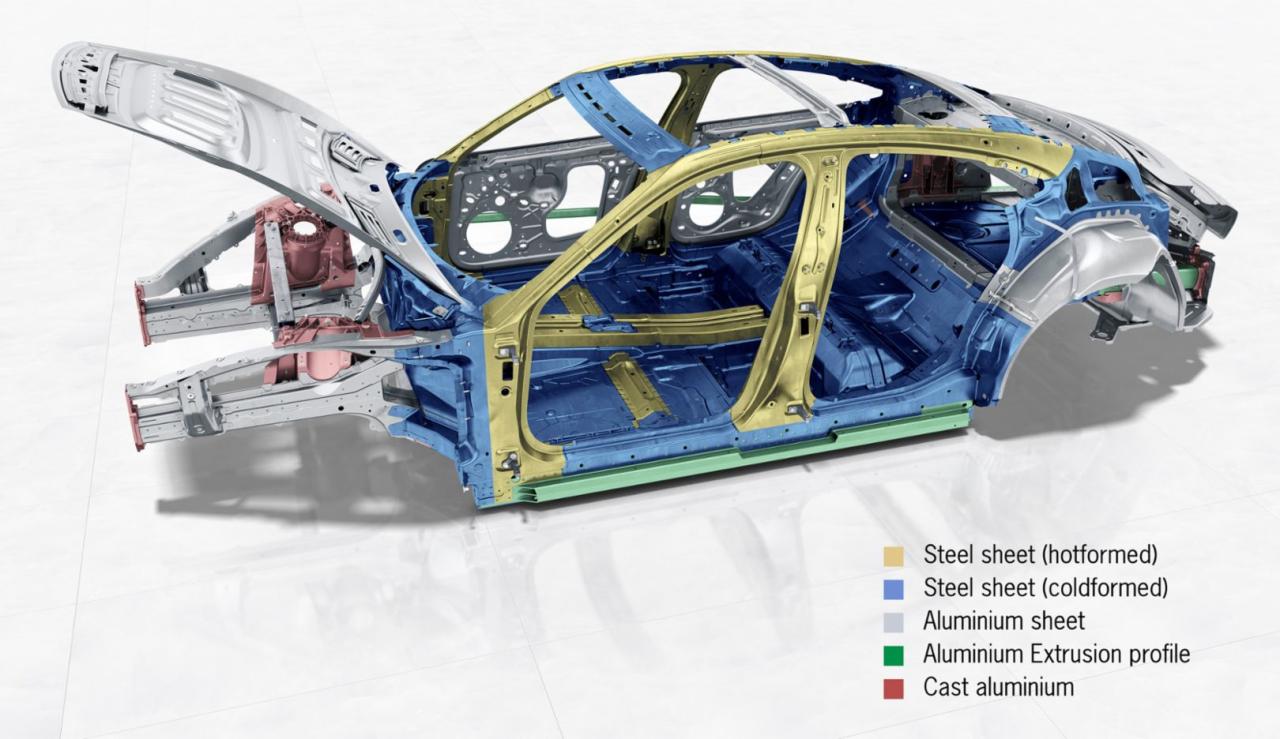
Car body technology has undergone a remarkable transformation, evolving from simple steel frames to sophisticated composite structures. This journey reflects advancements in materials science, manufacturing processes, and design principles, all aimed at creating safer, lighter, and more efficient vehicles.
From the introduction of aluminum to the widespread adoption of carbon fiber, each material has brought unique advantages and challenges. These innovations have not only reshaped the aesthetics of cars but also significantly impacted their performance, fuel economy, and safety.
Advanced Manufacturing Processes
The car body manufacturing process involves a complex interplay of advanced manufacturing techniques to transform raw materials into the intricate structures we see on the road. This section delves into the key processes, their evolution, and the role of automation in shaping modern car body production.
Stamping
Stamping is a fundamental process in car body manufacturing. It involves using a press to shape sheet metal into specific forms, creating components like doors, hoods, and roof panels.
The process begins with a sheet of metal being fed into a press where a die, shaped to the desired form, exerts pressure on the metal. The die’s shape is transferred to the metal, resulting in a precise and repeatable component.
- Evolution of Stamping: Stamping has evolved significantly to accommodate the demands of modern car body design. Advanced stamping techniques include:
- High-strength steel (HSS) stamping: HSS materials are used to create lighter and stronger components, requiring presses with higher tonnage and specialized dies.
- Hydroforming: This process uses water pressure to form complex shapes in sheet metal, allowing for greater design freedom.
- Laser cutting: Precise laser cutting replaces traditional cutting methods, ensuring accuracy and minimizing waste.
Welding
Welding is a crucial step in car body assembly, joining the stamped components together to form the complete structure. Different welding techniques are employed depending on the materials and desired strength.
- Resistance Spot Welding: This technique is widely used in car body assembly. It involves applying pressure and electrical current to two metal surfaces, creating a localized weld point.
- Laser Welding: This precise method uses a focused laser beam to melt and fuse metal surfaces, enabling high-quality welds and minimizing heat distortion.
- Arc Welding: Arc welding utilizes an electric arc to melt and join metal surfaces. While less common in car body assembly, it is used for specific applications.
Assembly
The final stage of car body manufacturing involves assembling the welded components into the complete structure. This process requires precision, efficiency, and effective coordination.
- Assembly Line Automation: Modern car body assembly lines heavily rely on automation and robotics. Robots perform tasks like lifting, positioning, and welding components, ensuring consistency and speed.
- Flexible Manufacturing Systems (FMS): FMS systems allow for adaptable production lines that can easily adjust to changes in design or model variations. This flexibility is crucial in the automotive industry, where product lifecycles are constantly evolving.
Role of Automation and Robotics
Automation and robotics play a transformative role in modern car body manufacturing. They offer numerous advantages, including:
- Increased Efficiency: Robots can perform tasks faster and more consistently than human workers, leading to higher production rates.
- Improved Quality: Robots are programmed for precision, resulting in consistent and high-quality welds and assemblies.
- Enhanced Safety: Robots can perform hazardous tasks, protecting human workers from potential injuries.
- Flexibility: Robots can be reprogrammed to handle different tasks, making production lines more adaptable to changing demands.
Safety and Crashworthiness
The car body plays a crucial role in ensuring the safety of occupants during a collision. It’s designed to absorb and dissipate impact energy, minimizing the forces transferred to the passengers. This concept is known as crashworthiness.
Crumple Zones
Crumple zones are strategically designed areas of the car body that are engineered to deform in a controlled manner during a crash. These zones, typically located in the front and rear of the vehicle, are made of materials that can absorb and dissipate energy, preventing it from reaching the passenger compartment.
The principle behind crumple zones is to extend the time it takes for the vehicle to come to a stop, thereby reducing the deceleration forces experienced by the occupants.
This controlled deformation helps to minimize the severity of injuries by spreading the impact force over a longer period.
Side Impact Beams
Side impact beams are reinforced structures embedded within the doors and side panels of the car body. These beams are designed to withstand side impacts, protecting occupants from intrusion into the passenger compartment.
Modern side impact beams are often made of high-strength steel or aluminum, providing excellent resistance to deformation.
These beams are crucial for safeguarding passengers in side collisions, which can be particularly dangerous due to the lack of crumple zones on the sides of the vehicle.
Airbags, Car body technology
Airbags are inflatable safety devices that deploy rapidly during a crash, providing a cushion between the occupants and the interior of the vehicle.
Airbags are typically located in the steering wheel, dashboard, and side panels, providing protection for the head, chest, and pelvis.
They work by inflating with compressed gas in milliseconds, creating a barrier that absorbs impact energy and reduces the severity of injuries.
Crash Testing Regulations and Standards
Crash testing regulations and standards are crucial for ensuring the safety of vehicles. These regulations specify the types of crashes, impact speeds, and test procedures that manufacturers must adhere to.
The most common crash tests include the frontal impact test, side impact test, and rollover test.
These tests are conducted using sophisticated crash test dummies that simulate human bodies and measure the forces experienced during a collision.
The results of these tests are used to assess the safety performance of vehicles and to identify areas for improvement in car body design.
These regulations have a significant impact on car body design, pushing manufacturers to continuously improve safety features and enhance crashworthiness.
Future Trends in Car Body Technology
The automotive industry is constantly evolving, driven by advancements in technology, sustainability concerns, and changing consumer preferences. Car body technology is at the forefront of this evolution, with emerging trends shaping the future of vehicle design, manufacturing, and performance.
Bio-Based Materials
The use of bio-based materials in car body construction is gaining traction as a sustainable alternative to traditional materials like steel and aluminum. These materials, derived from renewable sources such as plants and agricultural waste, offer several advantages.
- Reduced Environmental Impact: Bio-based materials have a lower carbon footprint compared to traditional materials, contributing to a more sustainable automotive industry.
- Lightweight Construction: Bio-based materials are often lighter than conventional materials, leading to improved fuel efficiency and reduced emissions.
- Enhanced Performance: Some bio-based materials exhibit superior strength-to-weight ratios and impact resistance, enhancing vehicle safety and performance.
Examples of bio-based materials used in car bodies include flax fibers, hemp fibers, and bioplastics. These materials can be incorporated into composite structures, providing strength and stiffness while reducing weight. For instance, the Ford Focus Electric features a bio-based composite material in its dashboard, demonstrating the growing adoption of these sustainable materials.
3D Printing
3D printing, also known as additive manufacturing, is revolutionizing car body production by offering unprecedented design flexibility and customization options.
- Complex Geometries: 3D printing allows for the creation of intricate and complex car body designs that would be impossible to manufacture using traditional methods.
- Lightweight Structures: 3D printing enables the production of lightweight and hollow structures, optimizing weight distribution and enhancing fuel efficiency.
- On-Demand Manufacturing: 3D printing allows for on-demand manufacturing, reducing lead times and inventory costs. It also facilitates localized production, potentially reducing transportation emissions.
The use of 3D printing in car body production is still in its early stages, but several car manufacturers are exploring its potential. For example, Local Motors, a US-based company, has used 3D printing to manufacture entire car bodies, showcasing the technology’s transformative potential.
Smart Materials
Smart materials are materials that respond to changes in their environment, such as temperature, pressure, or light. Their application in car body technology holds significant potential for enhancing safety, performance, and efficiency.
- Adaptive Aerodynamics: Smart materials can be used to create adaptive aerodynamic surfaces that adjust their shape based on driving conditions, reducing drag and improving fuel efficiency.
- Self-Healing Materials: Self-healing materials can repair minor scratches and dents, extending the lifespan of car bodies and reducing maintenance costs.
- Active Safety Features: Smart materials can be integrated into car bodies to provide active safety features, such as warning systems for impending collisions or lane departures.
Examples of smart materials used in car bodies include shape memory alloys, piezoelectric materials, and thermochromic materials. These materials can be incorporated into various components, such as bumpers, grilles, and windshields, to enhance vehicle performance and safety.
Sustainable Manufacturing Processes
The automotive industry is increasingly focusing on sustainable manufacturing processes to reduce its environmental impact. This includes adopting circular economy principles, minimizing waste, and using recycled materials.
- Closed-Loop Manufacturing: Implementing closed-loop manufacturing processes, where materials are reused or recycled at the end of their lifecycle, minimizes waste and reduces the need for virgin materials.
- Recycled Materials: Utilizing recycled materials in car body production reduces reliance on virgin materials, contributing to a more sustainable supply chain.
- Energy-Efficient Processes: Optimizing manufacturing processes to minimize energy consumption and emissions is crucial for achieving sustainability goals.
The adoption of sustainable manufacturing processes is crucial for the future of car body technology. By minimizing waste, using recycled materials, and optimizing energy efficiency, the industry can significantly reduce its environmental footprint.
Ending Remarks: Car Body Technology
As we look towards the future, the landscape of car body technology continues to evolve. Emerging materials like bio-based composites and advanced manufacturing techniques like 3D printing hold immense potential for creating sustainable and personalized vehicles. The relentless pursuit of innovation promises to push the boundaries of what’s possible, shaping the automotive industry in ways we can only begin to imagine.
Car body technology has come a long way, with advancements in materials, design, and manufacturing processes. One key aspect of maintaining a vehicle’s appearance is cleaning, and here, franklin cleaning technology offers innovative solutions. From specialized cleaning agents to advanced equipment, these technologies help preserve the car’s body, ensuring a lasting shine and protecting it from the elements.