Aircraft Engineering & Aerospace Technology: A Journey of Innovation
Aircraft engineering & aerospace technology represents a fascinating blend of science, engineering, and innovation. From the pioneering flights of the Wright brothers to the marvels of modern space exploration, this […]
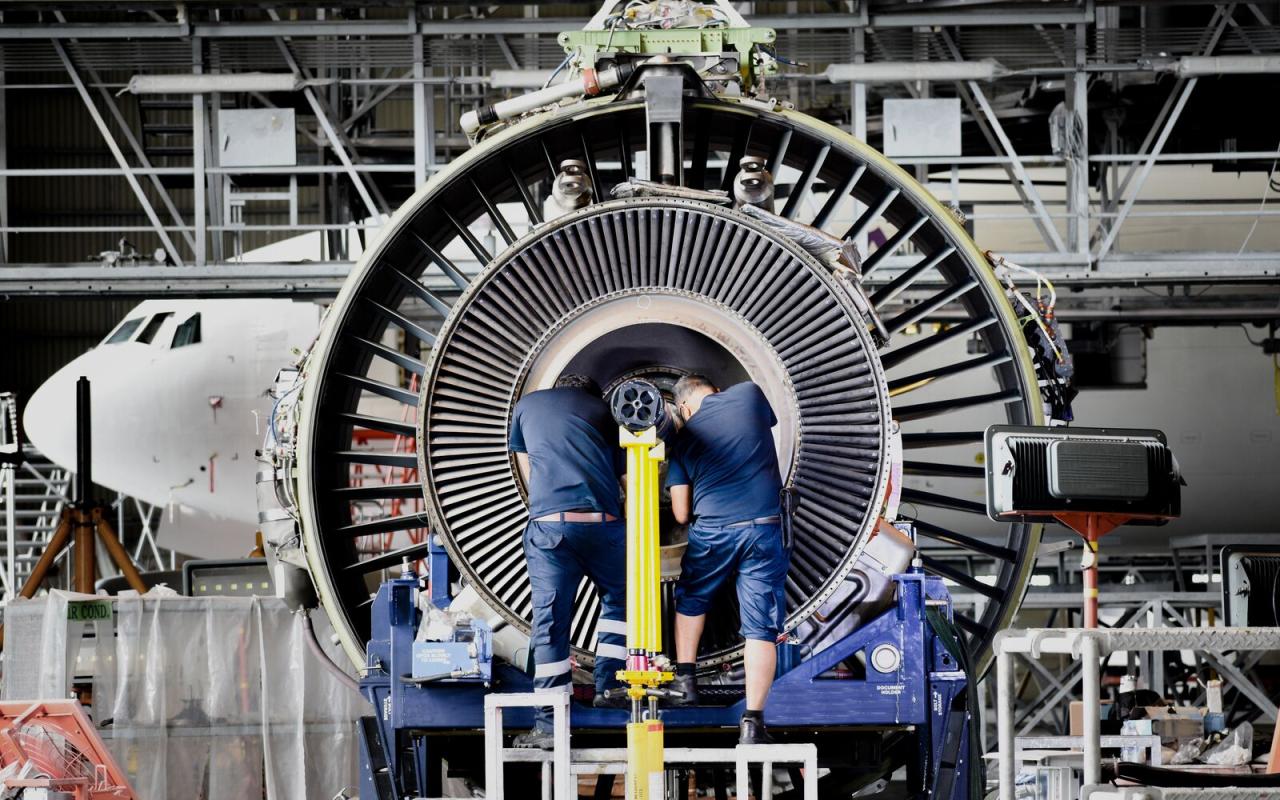
Aircraft engineering & aerospace technology represents a fascinating blend of science, engineering, and innovation. From the pioneering flights of the Wright brothers to the marvels of modern space exploration, this field has consistently pushed the boundaries of human ingenuity, transforming the way we travel, explore, and understand the world around us.
This comprehensive exploration delves into the historical evolution, fundamental principles, and cutting-edge advancements that define this dynamic field. We will examine the intricate designs of aircraft, the powerful engines that propel them, the sophisticated avionics that guide them, and the future possibilities that lie ahead.
Aerospace Propulsion Systems: Aircraft Engineering & Aerospace Technology
Aircraft propulsion systems are the heart of aviation, enabling flight by generating thrust to overcome drag and lift the aircraft into the air. The choice of propulsion system depends on various factors such as aircraft size, mission requirements, and operational environment.
Piston Engines
Piston engines, commonly used in smaller aircraft, operate on the principle of converting chemical energy from fuel into mechanical energy through a series of controlled explosions within cylinders. The combustion process drives pistons, which in turn rotate a crankshaft, generating power that is transmitted to a propeller.
- Operating Principle: The four-stroke cycle involves intake, compression, combustion, and exhaust stages. During the intake stroke, air is drawn into the cylinder. The compression stroke compresses the air-fuel mixture. Combustion occurs when a spark ignites the mixture, expanding the gases and driving the piston downward. The exhaust stroke expels the burnt gases from the cylinder.
- Efficiency: Piston engines have relatively lower fuel efficiency compared to jet engines, especially at higher speeds. However, they are efficient at lower speeds and altitudes.
- Applications: Piston engines are commonly used in general aviation aircraft, light aircraft, and some smaller commercial aircraft.
Jet Engines
Jet engines are highly efficient propulsion systems that operate on the principle of jet propulsion. They utilize the principle of Newton’s third law of motion, where for every action, there is an equal and opposite reaction.
- Operating Principle: Jet engines draw in air, compress it, mix it with fuel, and ignite the mixture to create hot, expanding gases. These gases are then accelerated through a nozzle, generating thrust. Jet engines can be categorized into turbojet, turbofan, and turboprop engines, each with variations in their design and operating characteristics.
- Efficiency: Jet engines are highly efficient at high speeds and altitudes, exceeding the efficiency of piston engines. They are widely used in commercial airliners and military aircraft.
- Applications: Turbojet engines are typically used in supersonic aircraft, while turbofan engines are more common in subsonic aircraft. Turboprop engines are often used in regional aircraft and some military aircraft.
Turboprop Engines
Turboprop engines combine the efficiency of jet engines with the propulsive power of propellers. They are a hybrid propulsion system that utilizes a turbine to drive a propeller.
- Operating Principle: Turboprop engines work similarly to jet engines, but instead of directly expelling the hot gases, they use the turbine to drive a propeller. The propeller generates thrust by pushing air backward.
- Efficiency: Turboprop engines are efficient at lower speeds and altitudes, offering a balance between the power of jet engines and the fuel efficiency of propellers.
- Applications: Turboprop engines are commonly used in regional aircraft, cargo aircraft, and some military aircraft.
Rocket Engines
Rocket engines are propulsion systems that generate thrust by expelling hot gases at high velocity. They are typically used for space travel and ballistic missiles.
- Operating Principle: Rocket engines operate on the principle of burning fuel and oxidizer, producing hot gases that are expelled through a nozzle. The momentum of the expelled gases creates an equal and opposite force, propelling the rocket forward.
- Efficiency: Rocket engines are highly efficient in a vacuum, where there is no atmospheric resistance. They are designed for high thrust and acceleration.
- Applications: Rocket engines are essential for launching satellites, spacecraft, and ballistic missiles into space. They are also used in some experimental aircraft for high-speed flight.
Aircraft Structures & Materials
Aircraft structures are designed and constructed to withstand the demanding forces of flight, ensuring the safety and efficiency of the aircraft. This involves a careful selection of materials and construction techniques, taking into account factors such as weight, strength, stiffness, and fatigue resistance.
Fuselage
The fuselage is the main body of the aircraft, housing the passengers, cargo, and systems. It is typically constructed from a combination of materials, including aluminum, composites, and titanium, depending on the size and type of aircraft.
- Monocoque Construction: This design uses a thin, strong outer shell to provide structural support, often reinforced with stringers and frames. This construction is commonly used for smaller aircraft, offering a lightweight and aerodynamic design.
- Semi-Monocoque Construction: This design combines a thin outer skin with internal structures, such as frames and stringers, to provide additional strength and stiffness. This is a common design for larger aircraft, providing the necessary strength to withstand higher loads and stresses.
Wings, Aircraft engineering & aerospace technology
The wings are responsible for generating lift, enabling the aircraft to take off and fly. They are typically designed with a streamlined shape and are made from lightweight and strong materials, including aluminum, composites, and titanium.
- Spars: These are the main structural components of the wing, providing the primary load-bearing function. They are typically made from aluminum or composites and are designed to withstand the bending forces generated during flight.
- Ribs: These are smaller structural components that connect the spars and skin, providing shape and support to the wing. They are also typically made from aluminum or composites.
- Skin: The outer covering of the wing, which is typically made from aluminum or composites, provides aerodynamic shaping and contributes to the wing’s strength.
Tail
The tail of the aircraft is responsible for stability and control during flight. It typically consists of a horizontal stabilizer and a vertical stabilizer, both of which are designed to be lightweight and strong.
- Horizontal Stabilizer: This provides stability about the aircraft’s pitch axis, preventing the aircraft from pitching up or down. It is typically made from aluminum or composites.
- Vertical Stabilizer: This provides stability about the aircraft’s yaw axis, preventing the aircraft from drifting sideways. It is typically made from aluminum or composites.
- Rudder: This is a movable control surface on the vertical stabilizer, used to control the aircraft’s yaw. It is typically made from aluminum or composites.
- Elevator: This is a movable control surface on the horizontal stabilizer, used to control the aircraft’s pitch. It is typically made from aluminum or composites.
Landing Gear
The landing gear is responsible for supporting the aircraft during takeoff, landing, and taxiing. It is typically made from a combination of materials, including steel, aluminum, and titanium, depending on the design and size of the aircraft.
- Main Landing Gear: This is the largest and strongest part of the landing gear, supporting the main weight of the aircraft. It is typically located under the wings or fuselage and consists of struts, wheels, and brakes.
- Nose Landing Gear: This is located at the front of the aircraft and is responsible for steering and supporting the nose of the aircraft. It is typically smaller than the main landing gear and is often retractable.
Aircraft Materials
The choice of materials for aircraft structures is crucial, as it directly impacts the aircraft’s performance, weight, and cost.
- Aluminum: This is the most common material used in aircraft structures, due to its lightweight, high strength-to-weight ratio, and good corrosion resistance. Aluminum alloys are widely used in fuselage, wings, and tail structures.
- Titanium: This is a strong and lightweight metal with excellent heat resistance, making it suitable for high-temperature applications such as engine components and landing gear. Titanium is also highly resistant to corrosion.
- Composites: These materials are made from two or more materials, typically a fiber reinforcement (such as carbon fiber or glass fiber) embedded in a matrix (such as epoxy resin or thermoplastic). Composites offer high strength-to-weight ratios, excellent fatigue resistance, and the ability to be tailored for specific applications. They are increasingly used in aircraft structures, including fuselage, wings, and tail sections.
- Advanced Alloys: These are specialized alloys that offer enhanced properties, such as increased strength, improved fatigue resistance, or better corrosion resistance. Examples include aluminum-lithium alloys, which offer a lower density than traditional aluminum alloys, and nickel-based superalloys, which have excellent high-temperature strength and creep resistance.
Material Selection
The selection of materials for different aircraft components is a complex process, considering factors such as:
- Strength and Stiffness: The material must be strong enough to withstand the stresses and loads encountered during flight, including takeoff, landing, and maneuvering.
- Weight: The material must be lightweight to minimize fuel consumption and improve aircraft performance.
- Fatigue Resistance: The material must be able to withstand repeated cycles of stress, which can cause fatigue cracks and ultimately lead to failure.
- Corrosion Resistance: The material must be resistant to corrosion, especially in environments with high humidity or salt spray.
- Cost: The cost of the material must be considered, balancing performance requirements with affordability.
- Manufacturing Process: The material must be suitable for the manufacturing processes used to create the aircraft component.
Space Exploration & Aerospace Technology
Space exploration, a captivating endeavor that pushes the boundaries of human ingenuity, relies heavily on advanced aerospace technology. From the design of spacecraft to the development of propulsion systems and life support systems, aerospace engineering plays a crucial role in enabling humanity’s ventures beyond Earth.
Spacecraft Design
Spacecraft design is a complex and multifaceted discipline that involves considering various factors, including mission objectives, payload requirements, and the harsh environment of space. The design of a spacecraft must ensure its structural integrity, thermal control, and efficient operation in the vacuum of space.
Propulsion Systems
Propulsion systems are essential for launching spacecraft into orbit, maneuvering them in space, and propelling them to distant destinations. Different types of propulsion systems are used depending on the mission requirements. For example, chemical rockets are commonly used for initial launch, while ion propulsion systems are more suitable for long-duration missions.
Life Support Systems
Life support systems are critical for the survival of astronauts during space missions. These systems provide essential functions such as oxygen generation, carbon dioxide removal, water recycling, and waste management.
Challenges and Advancements in Space Exploration
Space exploration presents numerous challenges, including the extreme conditions of space, the high costs involved, and the risks associated with human spaceflight. Despite these challenges, significant advancements have been made in recent years, enabling us to reach farther into space and explore new frontiers.
Reaching Mars
Reaching Mars is a major goal of space exploration. Several space agencies are working on developing technologies to enable human missions to the Red Planet. These technologies include advanced propulsion systems, life support systems, and landing technologies.
Establishing Space Stations
Space stations provide a platform for conducting scientific research, testing new technologies, and observing Earth. The International Space Station (ISS) is a testament to international collaboration in space exploration.
Developing Reusable Spacecraft
Reusable spacecraft are designed to be launched and landed multiple times, reducing the cost of space travel. Companies like SpaceX are leading the way in developing reusable rockets and spacecraft.
Applications of Space Technology
Space technology has numerous applications beyond space exploration. These applications benefit various fields, including telecommunications, Earth observation, and scientific research.
Telecommunications
Satellites play a vital role in global telecommunications, providing communication services to remote areas and enabling high-speed internet access.
Earth Observation
Earth observation satellites provide valuable data for monitoring environmental changes, managing natural resources, and responding to disasters.
Scientific Research
Space technology enables scientists to conduct research in areas such as astronomy, astrophysics, and planetary science.
Final Wrap-Up
As we conclude our journey through the world of aircraft engineering and aerospace technology, it becomes clear that this field is not only shaping the future of transportation but also driving innovation across diverse sectors. From the development of sustainable and efficient aircraft to the exploration of distant planets, the impact of this dynamic field is undeniable.
Aircraft engineering and aerospace technology are dynamic fields constantly pushing the boundaries of innovation. From advanced materials to cutting-edge propulsion systems, these industries are ripe with opportunities for growth and investment. If you’re considering entering this exciting space, connecting with experienced technology business brokers can be invaluable.
Their expertise in navigating complex transactions and understanding the nuances of these specialized sectors can provide the guidance needed to make informed decisions and achieve success in the world of aircraft engineering and aerospace technology.