Spray Foam Technologies: Insulation and Beyond
Spray foam technologies have revolutionized the insulation industry, offering a versatile and efficient solution for a wide range of applications. From residential homes to commercial buildings, spray foam provides superior […]
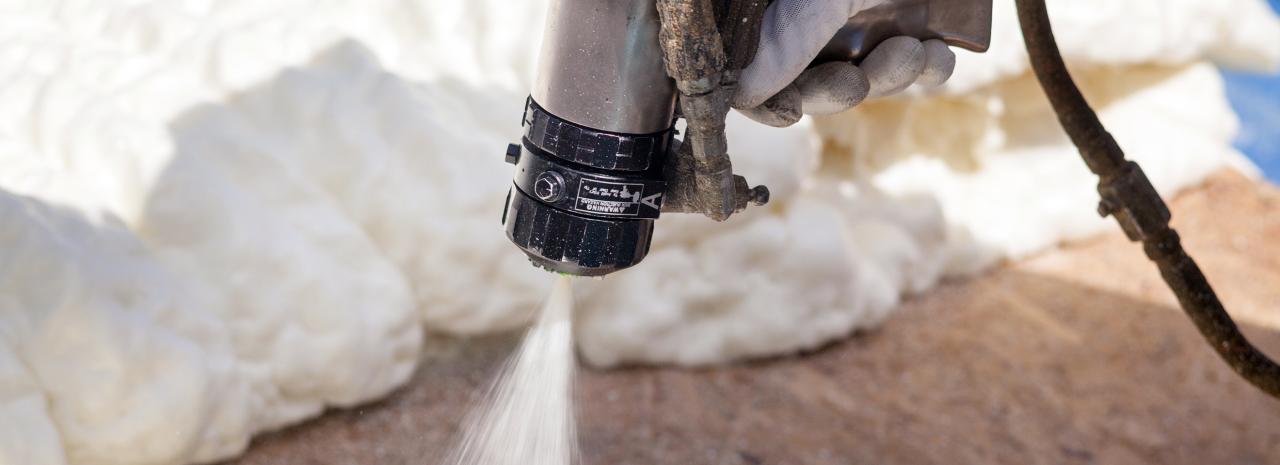
Spray foam technologies have revolutionized the insulation industry, offering a versatile and efficient solution for a wide range of applications. From residential homes to commercial buildings, spray foam provides superior thermal performance, air sealing, and moisture resistance, contributing to energy efficiency and improved indoor comfort.
This comprehensive guide delves into the world of spray foam, exploring its fundamental principles, diverse applications, and the science behind its remarkable properties. We’ll examine the different types of spray foam, their installation techniques, and the latest advancements in this ever-evolving field.
Introduction to Spray Foam Technologies
Spray foam insulation is a modern and effective method of insulating buildings and structures. It involves applying a liquid mixture of polymers and chemicals that expand and harden into a dense, insulating foam. This foam creates an airtight and moisture-resistant barrier, significantly improving energy efficiency and reducing heating and cooling costs.
Types of Spray Foam
The two main types of spray foam insulation are open-cell and closed-cell.
- Open-cell foam is a lightweight and flexible foam with a porous structure. It is known for its excellent sound absorption properties and is often used for interior applications. Due to its open structure, it allows for some air movement, making it less effective at blocking air infiltration compared to closed-cell foam.
- Closed-cell foam is a denser and more rigid foam with a closed-cell structure. It is highly effective at blocking air infiltration and moisture, making it ideal for exterior applications and areas prone to moisture buildup. Closed-cell foam also provides a higher R-value per inch, meaning it offers better thermal resistance than open-cell foam.
Historical Development of Spray Foam Technologies
The development of spray foam insulation can be traced back to the mid-20th century.
- In the 1950s, the first spray foam products were developed and used primarily for industrial applications.
- During the 1970s and 1980s, advancements in foam technology led to the development of more environmentally friendly and energy-efficient spray foam products.
- In the 1990s and early 2000s, spray foam insulation gained popularity in residential and commercial construction due to its superior performance and versatility.
- Today, spray foam insulation is widely used in various applications, including new construction, retrofitting existing buildings, and industrial and commercial projects.
Composition and Chemistry of Spray Foam
Spray foam insulation is a remarkable material formed through a chemical reaction between two primary components: isocyanates and polyols. This reaction results in the creation of a rigid or semi-rigid foam that expands significantly, adhering to surfaces and providing excellent thermal insulation.
The Role of Isocyanates and Polyols
Isocyanates and polyols are the key ingredients in spray foam insulation. They are reactive chemicals that, when mixed, undergo a polymerization reaction to form a polyurethane foam.
- Isocyanates are organic compounds containing the isocyanate functional group (-N=C=O). They act as the “building blocks” of the foam structure, linking together with polyols to create long chains of molecules. Common isocyanates used in spray foam include methylene diphenyl diisocyanate (MDI) and toluene diisocyanate (TDI).
- Polyols are organic compounds containing multiple hydroxyl groups (-OH). They provide the reactive sites for the isocyanates to attach to, forming the polyurethane chains. Polyols come in various forms, influencing the foam’s properties, such as density, flexibility, and fire resistance.
The reaction between isocyanates and polyols is highly exothermic, releasing heat and causing the foam to expand rapidly. This expansion is essential for achieving the desired thickness and coverage.
Additives in Spray Foam Formulations, Spray foam technologies
In addition to isocyanates and polyols, various additives are incorporated into spray foam formulations to modify its properties and enhance its performance. These additives play crucial roles in achieving specific characteristics, such as:
- Catalysts: Catalysts accelerate the chemical reaction between isocyanates and polyols, controlling the rate of foam expansion and cure time. Common catalysts include tertiary amines and organometallic compounds.
- Surfactants: Surfactants reduce the surface tension of the foam mixture, enabling it to spread evenly and adhere to various surfaces. They also contribute to the foam’s cell structure and stability.
- Flame Retardants: Flame retardants are incorporated to improve the fire resistance of the foam. They typically work by interrupting the combustion process, preventing the spread of flames. Examples include halogenated compounds and phosphorus-based compounds.
- Stabilizers: Stabilizers prevent the foam from degrading prematurely, maintaining its integrity over time. They protect against factors such as moisture, UV radiation, and temperature fluctuations.
- Pigments: Pigments are added to provide color to the foam, enhancing its aesthetic appeal and allowing for easy identification.
The specific combination and amounts of additives used in spray foam formulations vary depending on the desired application and performance requirements.
Emerging Trends and Innovations in Spray Foam: Spray Foam Technologies
The field of spray foam insulation is constantly evolving, driven by a desire to create more sustainable, efficient, and high-performance building materials. Researchers and manufacturers are actively developing new formulations and technologies to address the challenges of energy consumption, environmental impact, and building performance.
High-Performance and Eco-Friendly Formulations
The development of high-performance, eco-friendly spray foam products is a major focus in the industry. Manufacturers are working to improve the thermal insulation properties of spray foam while reducing its environmental footprint.
- Bio-based spray foams: These foams are made using renewable resources such as plant oils and agricultural byproducts. This reduces reliance on petroleum-based ingredients and lowers the overall carbon footprint. For example, soy-based spray foams have gained popularity due to their excellent insulation properties and reduced environmental impact.
- Recycled content spray foams: Manufacturers are incorporating recycled materials into spray foam formulations. This approach helps divert waste from landfills and reduces the demand for virgin materials. For instance, some spray foams now include recycled plastic or other post-consumer materials.
- Low-VOC spray foams: Volatile organic compounds (VOCs) can contribute to air pollution and indoor air quality issues. Low-VOC spray foams are formulated to minimize VOC emissions, creating a healthier indoor environment. These foams often use water-based formulations or alternative blowing agents to reduce VOC content.
Emerging Applications in Sustainable Building Design
Spray foam insulation is finding new applications in sustainable building design and construction. Its versatility and high performance make it a valuable tool for creating energy-efficient and environmentally friendly buildings.
- Passive house construction: Spray foam insulation is a key component in passive house design, which aims to minimize energy consumption for heating and cooling. The high R-value of spray foam helps achieve the stringent thermal performance standards required for passive houses.
- Net-zero energy buildings: Spray foam can contribute to achieving net-zero energy building goals. Its airtight seal helps prevent heat loss and gain, reducing the energy required for heating and cooling. This, in turn, lowers the building’s carbon footprint.
- Green building certifications: Spray foam insulation often meets the requirements of green building certifications such as LEED and WELL. Its environmental performance and energy efficiency contribute to earning points towards these certifications.
Advanced Spray Foam Technologies
The development of advanced spray foam technologies is further enhancing the performance and versatility of this material.
- Closed-cell spray foam with improved fire resistance: Closed-cell spray foam provides excellent thermal insulation but can be susceptible to fire. Researchers are developing formulations with improved fire resistance, allowing for safer applications in various building environments.
- Spray foam with enhanced sound absorption: Spray foam can effectively reduce noise transmission. Advancements in formulations are leading to spray foams with enhanced sound absorption properties, making them ideal for applications in noise-sensitive environments like theaters and recording studios.
- Spray foam with integrated functionalities: Researchers are exploring the integration of additional functionalities into spray foam. This includes features like moisture management, antimicrobial properties, and even solar energy absorption.
Final Wrap-Up
As we conclude our exploration of spray foam technologies, it’s clear that this innovative material has become an indispensable tool for building a more sustainable and comfortable future. With its remarkable versatility, energy efficiency, and environmental benefits, spray foam continues to shape the landscape of construction and insulation, offering a promising solution for a wide range of challenges.
Spray foam technologies have revolutionized insulation, providing a seamless barrier against heat loss and noise. Similarly, linen tracking technology has transformed laundry operations, offering real-time visibility and control over linen inventory. Just as spray foam creates a secure and efficient seal, linen tracking technology ensures smooth and efficient laundry processes, ultimately leading to cost savings and improved operational efficiency.