Metals Technologies: Shaping the World
Metals technologies set the stage for this enthralling narrative, offering readers a glimpse into a story that is rich in detail and brimming with originality from the outset. From the […]
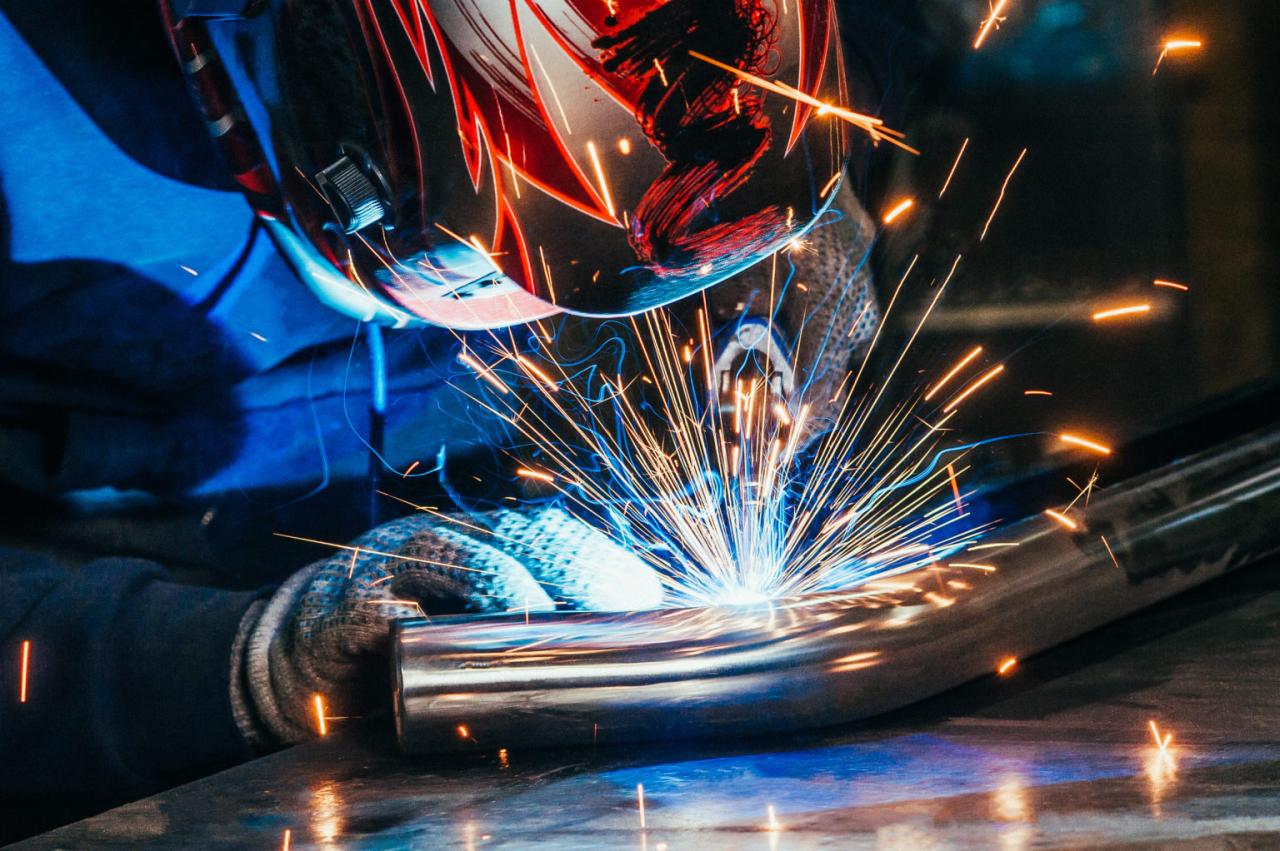
Metals technologies set the stage for this enthralling narrative, offering readers a glimpse into a story that is rich in detail and brimming with originality from the outset. From the dawn of civilization, humans have harnessed the power of metals, shaping them into tools, weapons, and structures that have defined our progress. This journey through time reveals the evolution of metal processing, highlighting the innovations that have propelled our world forward.
This exploration delves into the heart of modern metal processing techniques, revealing the intricacies of smelting, casting, forging, and machining. We uncover the secrets behind the creation of metal alloys, their unique properties, and their indispensable roles in various industries. The narrative culminates in a glimpse into the future of metals technologies, where cutting-edge advancements promise to redefine our relationship with these essential materials.
Modern Metal Processing Techniques
Metal processing techniques have evolved significantly over time, driven by technological advancements and the increasing demand for high-performance materials. From traditional methods like smelting and casting to modern techniques like additive manufacturing, the industry has witnessed a transformation in the way metals are shaped and utilized. This section will delve into the intricacies of these techniques, exploring their advantages, disadvantages, and applications.
Smelting
Smelting is a fundamental process in metal extraction, involving the heating of metal ores to high temperatures to separate the desired metal from impurities. This process typically involves the use of a furnace and reducing agents like carbon or coke. Smelting is essential for obtaining base metals like iron, copper, aluminum, and lead from their naturally occurring forms.
The primary advantage of smelting is its ability to produce large quantities of metal at relatively low costs. However, the process can be energy-intensive and generate significant environmental pollution. Moreover, the quality of the extracted metal can be affected by impurities and the efficiency of the smelting process.
Casting
Casting is a versatile metal processing technique that involves pouring molten metal into a mold, allowing it to solidify into a desired shape. This technique is widely used in various industries, including automotive, aerospace, and construction. Different casting methods, such as sand casting, die casting, and investment casting, are employed depending on the complexity of the desired shape, production volume, and required material properties.
The advantages of casting include its ability to produce complex shapes, high production rates, and cost-effectiveness for large-scale production. However, casting processes can be limited by the size and complexity of the mold, potential for internal defects, and surface finish.
Forging, Metals technologies
Forging is a metalworking process that involves shaping metal by applying compressive forces using hammers, presses, or dies. This technique is particularly suited for producing strong and durable components with intricate shapes. Forging can be performed at both room temperature and elevated temperatures, depending on the desired properties of the final product.
Forging offers several advantages, including enhanced material strength, improved grain structure, and the ability to create complex shapes with high dimensional accuracy. However, forging processes can be energy-intensive, require specialized equipment, and may be unsuitable for large-scale production.
Machining
Machining is a subtractive manufacturing process that removes material from a workpiece using cutting tools. This technique is used to create precise shapes and dimensions, typically on smaller components. Machining processes include turning, milling, drilling, and grinding, each employing different cutting tools and techniques to achieve desired results.
Machining offers high precision, versatility, and the ability to produce complex geometries. However, machining can be time-consuming, generate waste material, and may be unsuitable for large-scale production due to its relatively low production rate.
Additive Manufacturing
Additive manufacturing, also known as 3D printing, is a revolutionary metal processing technique that builds objects layer by layer from a digital design. This technology uses a variety of processes, such as powder bed fusion, directed energy deposition, and material extrusion, to create intricate geometries and complex designs.
Additive manufacturing offers several advantages, including design freedom, reduced lead times, minimal waste generation, and the ability to create customized parts with complex geometries. However, the technology is still relatively expensive compared to traditional methods and may have limitations in terms of production scale and material properties.
Comparison of Metal Processing Techniques
| Technique | Applications | Advantages | Limitations |
|—|—|—|—|
| Smelting | Extraction of base metals | High production rate, low cost | Energy-intensive, environmental pollution, limited control over material quality |
| Casting | Automotive, aerospace, construction | Complex shapes, high production rates, cost-effectiveness | Limited by mold size and complexity, potential for defects, surface finish |
| Forging | Automotive, aerospace, machinery | Enhanced strength, improved grain structure, high dimensional accuracy | Energy-intensive, specialized equipment, unsuitable for large-scale production |
| Machining | Tooling, machinery, electronics | High precision, versatility, complex geometries | Time-consuming, waste generation, low production rate |
| Additive Manufacturing | Aerospace, medical, tooling | Design freedom, reduced lead times, minimal waste, complex geometries | High cost, limited production scale, material property limitations |
Metals in Various Industries
Metals have played a crucial role in shaping human civilization and continue to be essential components in various industries, driving innovation and technological advancements. Their unique properties, including strength, durability, conductivity, and malleability, make them indispensable materials for a wide range of applications.
Aerospace
Metals are integral to the aerospace industry, where lightweight, high-strength materials are paramount. Aluminum alloys, for example, are extensively used in aircraft construction due to their excellent strength-to-weight ratio and corrosion resistance. Titanium alloys, known for their exceptional strength and heat resistance, are employed in critical components like jet engine parts and spacecraft structures.
Automotive
The automotive industry relies heavily on metals for manufacturing vehicles. Steel, a versatile and cost-effective material, forms the backbone of car bodies and chassis. Aluminum alloys are increasingly used in automotive components to reduce weight and improve fuel efficiency. Magnesium alloys, known for their lightweight properties, are incorporated in engine parts and other components.
Construction
Metals are fundamental to the construction industry, providing structural support, durability, and longevity to buildings and infrastructure. Steel is the dominant metal used in construction, forming the framework of skyscrapers, bridges, and other large-scale structures. Aluminum is also used in construction, particularly for cladding, roofing, and window frames, due to its lightweight and corrosion-resistant properties.
Electronics
Metals play a vital role in the electronics industry, facilitating the flow of electricity and providing essential components for electronic devices. Copper, known for its excellent conductivity, is widely used in wiring and circuit boards. Gold, a highly conductive and corrosion-resistant metal, is used in connectors and other sensitive electronic components.
Healthcare
Metals have numerous applications in healthcare, ranging from surgical instruments to medical implants. Stainless steel, known for its biocompatibility and resistance to corrosion, is commonly used in surgical tools, medical implants, and medical equipment. Titanium alloys are used in orthopedic implants, dental implants, and other medical devices due to their biocompatibility and strength.
Closing Summary: Metals Technologies
As we conclude this journey through the world of metals technologies, we are left with a profound appreciation for the ingenuity and resilience of human innovation. The story of metals is a testament to our ability to transform raw materials into instruments of progress, shaping not only our physical world but also the course of history itself. From the ancient forges to the frontiers of nanotechnology, the evolution of metals technologies continues to inspire and empower us, paving the way for a future where the potential of these remarkable materials is fully realized.
Metals technologies are constantly evolving, finding new applications in various industries. For example, the sichuan ai-link technology camera utilizes advanced metals in its construction to ensure durability and performance. This camera showcases how metals play a crucial role in modern technology, pushing boundaries and enabling innovation.