Unibloc Hygienic Technologies: A Revolution in Sanitation
Unibloc hygienic technologies represent a revolutionary approach to sanitation, transforming industries by offering seamless, hygienic, and efficient solutions. These technologies are specifically designed to eliminate contamination risks and ensure product […]
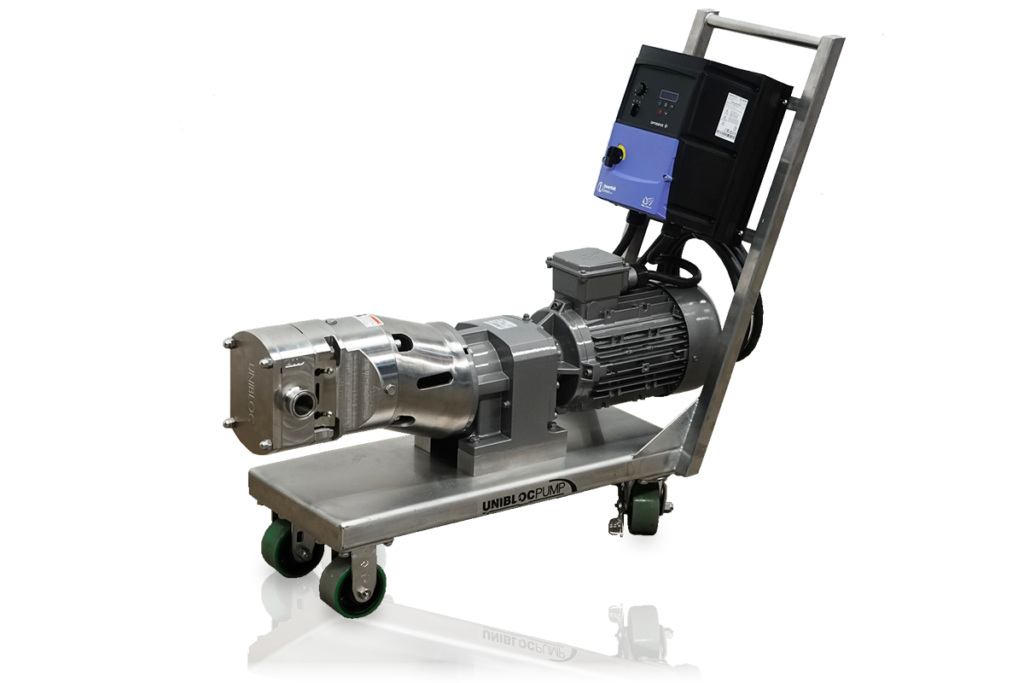
Unibloc hygienic technologies represent a revolutionary approach to sanitation, transforming industries by offering seamless, hygienic, and efficient solutions. These technologies are specifically designed to eliminate contamination risks and ensure product quality, making them crucial for food processing, pharmaceuticals, and other sensitive sectors.
The core concept of Unibloc hygienic technologies lies in their integrated design, where all components are seamlessly joined without crevices or gaps. This eliminates potential contamination points, making cleaning and sanitizing processes significantly easier and more effective. Unibloc systems are constructed from materials that are resistant to corrosion and chemicals, ensuring long-term durability and hygiene.
Unibloc Technology Applications: Unibloc Hygienic Technologies
Unibloc technology has become a widely adopted solution in various industries due to its inherent advantages in terms of hygiene, efficiency, and cost-effectiveness. The modular design of Unibloc components allows for easy assembly, cleaning, and maintenance, making them ideal for applications where sanitation and reliability are paramount.
Unibloc Technology Applications Across Industries
Unibloc technology finds diverse applications across various industries, contributing to improved hygiene, efficiency, and operational performance. The following table provides an overview of specific applications and their benefits within different industry sectors:
Industry | Specific Applications | Benefits |
---|---|---|
Food & Beverage |
|
|
Pharmaceutical |
|
|
Chemical & Petrochemical |
|
|
Water Treatment |
|
|
Unibloc Components and Functionalities
Unibloc technology encompasses a range of components designed for specific functionalities. The following table provides details on different types of Unibloc components, their materials, and key features:
Component Type | Materials Used | Key Features |
---|---|---|
Unibloc Pumps | Stainless steel, cast iron, plastics |
|
Unibloc Valves | Stainless steel, cast iron, plastics |
|
Unibloc Mixers | Stainless steel, cast iron |
|
Unibloc Reactors | Stainless steel, glass-lined steel |
|
Unibloc Filters | Stainless steel, plastics |
|
Unibloc Technology Design Considerations
Unibloc technology design prioritizes hygiene by integrating all process components into a single, seamless unit. This approach eliminates crevices and gaps where contaminants can accumulate, making cleaning and sanitation more efficient and effective. The design considerations encompass materials, surface finishes, and overall construction to ensure optimal hygiene performance.
Materials Used in Unibloc Technologies, Unibloc hygienic technologies
The selection of materials for Unibloc technologies is critical for achieving the desired hygienic properties. The materials must be resistant to corrosion, chemical attack, and abrasion, ensuring long-term durability and maintaining the integrity of the processing environment.
- Stainless Steel: The most common material used in Unibloc technology due to its excellent corrosion resistance, strength, and ease of cleaning. It is often chosen in grades 304 and 316, which are known for their high resistance to various chemicals and harsh environments.
- Polymers: Certain polymers, such as high-density polyethylene (HDPE), polypropylene (PP), and polyvinyl chloride (PVC), are employed in Unibloc systems for specific applications. These materials offer excellent chemical resistance and are lightweight, making them suitable for certain components like tanks and pipes.
- Glass-lined Steel: This material is used in applications requiring high chemical resistance, such as in the pharmaceutical industry. The glass lining provides a smooth, inert surface that is resistant to a wide range of chemicals.
Surface Finishes and Their Role in Hygiene
Surface finishes play a crucial role in maintaining hygiene within Unibloc systems. Smooth, non-porous surfaces prevent the accumulation of microorganisms and facilitate cleaning.
- Electropolished Surfaces: This finish creates a smooth, microscopically polished surface, reducing surface roughness and minimizing the potential for bacterial adhesion. Electropolishing is commonly used for stainless steel components.
- Sandblasted Surfaces: While not as smooth as electropolished surfaces, sandblasting creates a rougher texture that can enhance surface adhesion for certain coatings, like epoxy, which provide additional protection against corrosion and chemical attack.
- Coated Surfaces: Coatings, such as epoxy, polyurethane, and PTFE, can be applied to various surfaces to enhance their resistance to chemicals, abrasion, and microbial growth. These coatings are often chosen for specific applications and are designed to withstand the rigors of the processing environment.
Cleaning and Maintenance of Unibloc Technologies
Unibloc technologies, renowned for their hygienic design and ease of operation, demand meticulous cleaning and maintenance protocols to ensure optimal performance and longevity. These systems are typically employed in critical environments where contamination control is paramount, making regular cleaning and maintenance essential.
Cleaning and Sanitizing Unibloc Systems
Cleaning and sanitizing Unibloc systems is crucial to eliminate potential contamination sources and maintain product quality. This process involves a series of steps, each designed to achieve a specific objective.
- Disassembly: Before cleaning, disassemble the Unibloc system as per the manufacturer’s instructions. This step allows for thorough access to all surfaces and components.
- Pre-cleaning: Rinse the disassembled components with clean water to remove loose debris and residues. This step prepares the surfaces for the next stage of cleaning.
- Cleaning: Apply a cleaning solution appropriate for the specific material of the Unibloc system. Ensure the solution is compatible with the system’s components and effectively removes contaminants. Follow the manufacturer’s recommendations for cleaning solution concentration and contact time.
- Rinsing: Thoroughly rinse the components with clean water to remove all traces of the cleaning solution. This step ensures no residues remain on the surfaces, potentially contaminating the product.
- Sanitization: Apply a sanitizing agent, such as chlorine or iodine-based solutions, to kill microorganisms. Follow the manufacturer’s instructions for concentration, contact time, and application method.
- Final Rinse: Rinse the components with clean water to remove any residual sanitizing agent. This step ensures the system is ready for reassembly and operation.
- Reassembly: Assemble the Unibloc system carefully, following the manufacturer’s instructions. Ensure all components are properly seated and secured.
Cleaning Methods
Various cleaning methods are employed for Unibloc technologies, each suited to specific applications and requirements.
- Manual Cleaning: This method involves manually cleaning the system components using brushes, sponges, and cleaning solutions. It is suitable for smaller Unibloc systems or components that can be easily accessed.
- Automated Cleaning: This method utilizes specialized equipment, such as robotic arms or automated spray systems, to clean the system components. Automated cleaning is ideal for larger Unibloc systems and applications where efficiency and consistency are critical.
- Clean-in-Place (CIP): This method involves cleaning the system in place, without disassembly. CIP systems utilize a series of tanks and pumps to circulate cleaning solutions through the system, effectively cleaning all surfaces. CIP is particularly suitable for Unibloc systems used in pharmaceutical and food processing industries, where sterility is paramount.
Importance of Regular Maintenance
Regular maintenance of Unibloc systems is essential for ensuring their longevity and optimal performance.
- Preventative Maintenance: Regular inspections and maintenance tasks, such as lubrication, component replacement, and calibration, help prevent potential failures and ensure the system operates reliably.
- Extended Lifespan: Proper maintenance extends the lifespan of the Unibloc system by minimizing wear and tear on components. This reduces the need for premature replacements and lowers operational costs.
- Product Quality: Regular maintenance ensures the system operates efficiently and consistently, minimizing the risk of contamination and maintaining product quality. This is particularly important in industries where product safety is paramount.
- Compliance: In regulated industries, regular maintenance and documentation are crucial for meeting regulatory requirements and ensuring compliance with industry standards.
Future Trends in Unibloc Hygienic Technologies
Unibloc hygienic technologies are constantly evolving, driven by the demand for enhanced efficiency, sustainability, and safety in food and beverage production. As the industry embraces new materials, manufacturing techniques, and digital tools, the future of Unibloc systems is poised for significant advancements.
Advanced Materials and Manufacturing Techniques
The use of advanced materials and manufacturing techniques is transforming the design and performance of Unibloc systems. These innovations are leading to:
- Enhanced Durability and Resistance: New materials like high-performance polymers and ceramics offer superior resistance to wear, corrosion, and chemical attack, extending the lifespan of Unibloc components and reducing maintenance requirements.
- Improved Hygienic Properties: Advanced materials with smooth surfaces and low-friction properties minimize the accumulation of microorganisms, facilitating easier cleaning and reducing the risk of contamination.
- Lightweight and Compact Designs: Lighter and more compact Unibloc systems are possible with advanced materials, reducing installation and transportation costs and optimizing space utilization in production facilities.
- Tailored Solutions: Additive manufacturing (3D printing) allows for the creation of highly customized Unibloc components with complex geometries, enabling the development of tailored solutions for specific process requirements.
Automation and Digitalization
Automation and digitalization are revolutionizing the operation and management of Unibloc hygienic technologies. Key trends include:
- Automated Cleaning and Sanitization: Integrated cleaning systems with automated control and monitoring ensure consistent and effective cleaning cycles, reducing manual labor and minimizing the risk of human error.
- Real-time Monitoring and Data Analytics: Sensors and data acquisition systems provide real-time monitoring of critical process parameters like temperature, pressure, and flow, enabling proactive maintenance and optimization of Unibloc system performance.
- Predictive Maintenance: Data analysis and machine learning algorithms can predict potential equipment failures, allowing for preventative maintenance and minimizing downtime.
- Remote Monitoring and Control: Digital platforms enable remote monitoring and control of Unibloc systems, allowing for real-time troubleshooting and optimization from anywhere in the world.
Last Recap
Unibloc hygienic technologies are a testament to the power of innovative design in achieving optimal sanitation. By integrating hygiene into the very core of their design, these technologies offer a future where contamination risks are minimized, and product quality is consistently maintained. As industries continue to prioritize hygiene and safety, Unibloc technologies will undoubtedly play a pivotal role in shaping a cleaner and safer future.
Unibloc hygienic technologies are designed to minimize contamination and ensure safe and clean environments, especially in healthcare settings. These technologies are often integrated with advanced occupational therapy technology to create ergonomic and accessible spaces for patients and therapists. For example, Unibloc’s modular wall systems can be easily adjusted to accommodate specific needs, while their antimicrobial surfaces help prevent the spread of infections.