G Glass Technology: A Revolution in Glassmaking
G glass technology, a revolutionary advancement in glassmaking, has reshaped numerous industries with its exceptional properties and diverse applications. This specialized type of glass, renowned for its superior strength, durability, […]
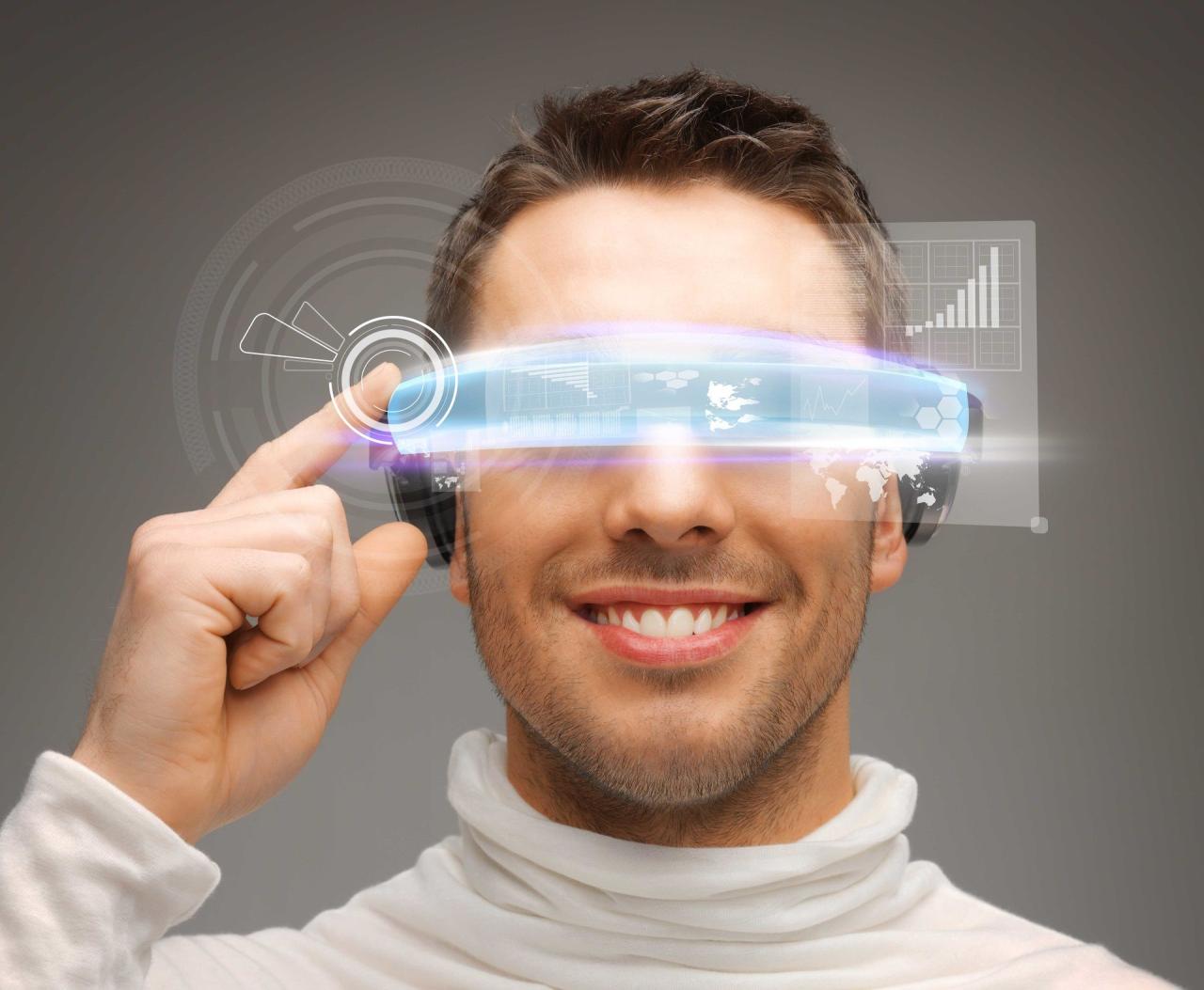
G glass technology, a revolutionary advancement in glassmaking, has reshaped numerous industries with its exceptional properties and diverse applications. This specialized type of glass, renowned for its superior strength, durability, and thermal stability, has propelled innovation across various sectors, from construction and automotive to electronics and aerospace.
The journey of G glass began with the quest for a glass composition that could withstand extreme temperatures and pressures, surpassing the limitations of traditional glass types. Through meticulous research and development, scientists and engineers have crafted a material that exhibits exceptional resistance to thermal shock, chemical attack, and mechanical stress, opening doors to unprecedented possibilities in diverse fields.
History and Evolution of G Glass Technology
G glass technology has a rich history, evolving significantly since its inception. Its origins can be traced back to the early 20th century, with its initial applications primarily focused on the production of optical lenses and scientific instruments. Over time, advancements in glassmaking techniques and a deeper understanding of the properties of G glass have led to its widespread use in various industries.
Key Milestones and Innovations
The evolution of G glass technology has been marked by several key milestones and innovations. These advancements have significantly enhanced its properties and expanded its applications.
- Early 20th Century: The development of the first G glass formulations, primarily for optical lenses, marked the beginning of this technology.
- Mid-20th Century: The introduction of controlled melting and annealing processes significantly improved the homogeneity and optical clarity of G glass, paving the way for its use in high-precision optical instruments.
- Late 20th Century: The development of advanced glass compositions, incorporating elements like barium and lanthanum, further enhanced the refractive index and dispersion properties of G glass. This led to its use in high-performance camera lenses and other optical systems.
- 21st Century: Recent advancements in G glass technology include the development of ultra-low dispersion (ULD) glasses, which minimize chromatic aberration and improve image quality. These innovations have led to its use in high-end telescopes, microscopes, and other scientific instruments.
Comparison of G Glass Properties with Other Glass Types
G glass stands out for its unique properties, making it a valuable material in various applications. Here’s a comparison of its properties with other commonly used glass types:
Property | G Glass | Soda-Lime Glass | Borosilicate Glass |
---|---|---|---|
Refractive Index | High | Medium | Medium |
Dispersion | Low | High | Low |
Chemical Durability | Good | Moderate | Excellent |
Thermal Expansion | Moderate | High | Low |
Optical Clarity | Excellent | Good | Excellent |
G glass, with its high refractive index and low dispersion, excels in optical applications where precise light control is crucial. Its superior optical clarity and good chemical durability make it suitable for use in high-performance lenses and instruments. While other glass types like soda-lime glass and borosilicate glass have their own advantages, G glass’s unique combination of properties sets it apart for specific applications.
Composition and Properties of G Glass
G glass, a type of soda-lime glass, is a versatile material commonly used in various applications, including windows, bottles, and tableware. Its unique properties are a result of its specific chemical composition.
Chemical Composition
The chemical composition of G glass primarily consists of silica (SiO2), soda ash (Na2CO3), and lime (CaO). These components contribute to the glass’s properties in distinct ways.
- Silica (SiO2) forms the fundamental building block of glass. It provides structural integrity and resistance to chemical attack.
- Soda ash (Na2CO3) acts as a flux, lowering the melting point of silica, making it easier to process. It also enhances the glass’s fluidity, allowing it to be shaped more easily.
- Lime (CaO) improves the glass’s chemical durability and resistance to water. It also increases the glass’s strength and reduces its tendency to deform under heat.
Key Properties of G Glass
The following table summarizes the key physical and chemical properties of G glass:
Property | Value |
---|---|
Refractive index | 1.52 |
Thermal expansion coefficient | 9 x 10-6 / °C |
Density | 2.5 g/cm3 |
Hardness | 5.5 on Mohs scale |
Resistance to chemicals | Good resistance to most acids and bases, except hydrofluoric acid |
Manufacturing Processes of G Glass
The production of G glass involves a complex series of steps, each contributing to the final quality and characteristics of the glass. These processes are carefully controlled and optimized to ensure consistency and meet the specific requirements of various applications.
Overview of G Glass Manufacturing Processes
The manufacturing of G glass generally follows a well-established flow, starting with raw material preparation and culminating in the final product.
- Raw Material Preparation: The process begins with the careful selection and preparation of raw materials, including silica sand, soda ash, limestone, and other additives. These materials are meticulously weighed and blended to achieve the desired chemical composition for G glass.
- Melting and Refining: The blended raw materials are then fed into a furnace where they are heated to extremely high temperatures (around 1500°C) to melt and form a homogeneous glass melt. The molten glass undergoes a refining process to remove bubbles and impurities, resulting in a clear and uniform glass.
- Forming: The refined molten glass is then shaped into the desired product using various forming techniques, including float glass, sheet glass, and tube glass processes.
- Annealing: After forming, the glass is carefully annealed to relieve internal stresses that can lead to breakage or distortion. This involves slowly cooling the glass to room temperature, allowing the glass structure to relax.
- Inspection and Quality Control: Throughout the manufacturing process, rigorous quality control measures are implemented to ensure the consistency and quality of G glass products. This includes visual inspection, dimensional checks, and various physical and chemical tests.
- Finishing and Packaging: Finally, the finished G glass products undergo further finishing processes, such as cutting, edging, or polishing, depending on the specific application. They are then carefully packaged and shipped to customers.
Float Glass Process
The float glass process is a widely used technique for producing flat glass sheets, including G glass. This method is renowned for its ability to create high-quality, flat, and uniform glass sheets.
- Molten Glass Flow: Molten glass from the furnace is continuously fed onto a bed of molten tin, which acts as a support and provides a perfectly flat surface for the glass to spread out.
- Controlled Cooling: The glass sheet is then slowly cooled and solidified while floating on the tin bath. This controlled cooling process helps to reduce internal stresses and achieve a uniform thickness.
- Inspection and Cutting: After cooling, the glass sheet is inspected for defects and then cut to the desired size and shape.
Sheet Glass Process
The sheet glass process is another commonly used technique for producing flat glass sheets, although it is less prevalent than the float glass process.
- Vertical Drawing: In this method, molten glass is drawn vertically from a furnace through a narrow opening, creating a continuous sheet of glass.
- Cooling and Inspection: The drawn sheet is then cooled and inspected for defects before being cut to size.
Tube Glass Process
The tube glass process is used to produce hollow glass tubes, which are commonly used in applications like lighting, pharmaceuticals, and laboratory equipment.
- Vertical Drawing: Molten glass is drawn vertically from a furnace through a small opening, forming a continuous tube.
- Cooling and Annealing: The tube is then cooled and annealed to relieve internal stresses.
- Cutting and Finishing: Finally, the tube is cut to the desired length and further finished according to specific requirements.
Key Equipment and Technologies
The manufacturing of G glass relies on specialized equipment and advanced technologies to ensure the production of high-quality glass products.
- Furnaces: Furnaces are essential for melting and refining the raw materials, and they are typically designed to operate at very high temperatures.
- Float Bath: The float bath, used in the float glass process, is a large tank containing molten tin, providing a flat surface for the glass to spread out and solidify.
- Drawing Machines: Drawing machines are used in the sheet glass and tube glass processes to draw molten glass vertically, creating continuous sheets or tubes.
- Annealing Lehrs: Annealing lehrs are long, oven-like structures that slowly cool the formed glass, reducing internal stresses and preventing breakage.
- Inspection Systems: Automated inspection systems are used to detect defects in the glass, ensuring the quality of the final product.
- Cutting and Finishing Equipment: Various cutting and finishing equipment are used to shape and polish the glass according to specific requirements.
Quality Control and Testing
Quality control and testing are crucial aspects of G glass manufacturing, ensuring the consistency and reliability of the final product.
- Visual Inspection: Visual inspection is performed throughout the manufacturing process to identify any defects or imperfections in the glass.
- Dimensional Checks: Dimensional checks are conducted to ensure the glass meets the required specifications for thickness, width, and length.
- Physical Tests: Physical tests, such as tensile strength, impact resistance, and thermal shock resistance, are conducted to assess the mechanical properties of the glass.
- Chemical Tests: Chemical tests are performed to determine the chemical composition of the glass and ensure it meets the required standards.
Applications of G Glass Technology
G glass, with its unique combination of properties, finds widespread applications across various industries, shaping innovative products and technologies. Its exceptional thermal stability, chemical resistance, and electrical insulation make it a versatile material for diverse purposes.
Applications in the Electronics Industry
G glass’s high dielectric strength and low thermal expansion coefficient make it ideal for applications in the electronics industry. Its ability to withstand high temperatures and maintain its structural integrity under extreme conditions makes it a preferred choice for:
- Printed Circuit Boards (PCBs): G glass is used as a substrate for PCBs, providing a stable platform for electronic components. Its low thermal expansion ensures that the board does not warp or distort during the soldering process, preventing damage to sensitive components.
- Electronic Enclosures: G glass’s electrical insulation properties and resistance to chemical attack make it suitable for enclosures that protect electronic devices from environmental hazards.
- Optical Fiber Manufacturing: G glass’s high purity and low attenuation properties make it an ideal material for the production of optical fibers used in high-speed data transmission.
Applications in the Automotive Industry
G glass’s strength, lightweight nature, and thermal stability make it a valuable material in the automotive industry. It is used in various components, including:
- Windshields and Windows: G glass’s high impact resistance and clarity make it a safe and reliable material for automotive glass. Its ability to withstand high temperatures and maintain its structural integrity ensures passenger safety in case of accidents.
- Body Panels: G glass-reinforced composites are increasingly used in automotive body panels, reducing vehicle weight and improving fuel efficiency.
- Exhaust Systems: G glass’s thermal stability and resistance to chemical attack make it suitable for exhaust system components, such as heat shields and mufflers.
Applications in the Construction Industry
G glass’s strength, durability, and resistance to weathering make it a versatile material in the construction industry. It is used in:
- Building Facades: G glass panels are used in building facades, providing natural light and enhancing aesthetic appeal. Its high thermal insulation properties contribute to energy efficiency in buildings.
- Insulated Glass Units (IGUs): G glass is used in IGUs, which are widely used in windows and doors to improve thermal insulation and reduce energy consumption.
- Reinforced Concrete: G glass fibers are incorporated into concrete, enhancing its strength, durability, and resistance to cracking.
Applications in the Aerospace Industry, G glass technology
G glass’s high strength-to-weight ratio and resistance to extreme temperatures make it suitable for applications in the aerospace industry. It is used in:
- Aircraft Components: G glass-reinforced composites are used in aircraft components, such as wings, fuselages, and tail sections, reducing aircraft weight and improving fuel efficiency.
- Spacecraft Components: G glass’s ability to withstand extreme temperatures and harsh environments makes it suitable for spacecraft components, such as heat shields and thermal insulation.
Advantages and Disadvantages of G Glass Technology
G glass technology, with its exceptional properties and wide range of applications, offers both advantages and disadvantages. This section explores the key benefits and drawbacks of using G glass in various industries, providing a comprehensive overview of its strengths and limitations.
Advantages of G Glass Technology
The advantages of G glass technology stem from its unique composition and properties, making it suitable for a variety of applications.
- High Strength and Durability: G glass exhibits exceptional strength and durability, making it resistant to breakage and impact. This characteristic makes it ideal for applications requiring high mechanical strength, such as windshields, aircraft windows, and protective eyewear.
- Chemical Resistance: G glass is highly resistant to chemical attack, making it suitable for use in environments where exposure to corrosive substances is a concern. For instance, it is used in laboratory equipment, chemical processing plants, and industrial applications where resistance to acids, bases, and solvents is critical.
- Heat Resistance: G glass has a high melting point and excellent thermal stability, allowing it to withstand high temperatures without significant degradation. This property makes it suitable for applications such as ovenware, heat-resistant windows, and high-temperature industrial processes.
- Optical Transparency: G glass exhibits excellent optical transparency, making it ideal for applications requiring clear visibility, such as windows, lenses, and optical instruments. Its clarity allows for the transmission of light with minimal distortion or absorption.
- Versatility: G glass is versatile and can be processed into various shapes and forms, making it suitable for a wide range of applications. It can be easily cut, drilled, and shaped to meet specific design requirements.
- Cost-Effectiveness: In many applications, G glass offers a cost-effective solution compared to alternative materials, such as polycarbonate or other specialized glass types. Its durability and longevity make it a long-term investment.
Disadvantages of G Glass Technology
While G glass offers numerous advantages, it also has certain disadvantages that must be considered.
- Weight: G glass is heavier than other materials, such as polycarbonate, which can be a disadvantage in applications where weight is a critical factor, such as aircraft windows or automotive parts.
- Brittleness: Despite its high strength, G glass is still brittle and can shatter under extreme impact or stress. This brittleness can be a safety concern in certain applications, especially those involving high-impact scenarios.
- Environmental Impact: The production of G glass requires significant energy consumption and can generate greenhouse gas emissions. This environmental impact needs to be considered, particularly in the context of sustainable development and environmental regulations.
- Recycling Challenges: While G glass can be recycled, the process can be complex and costly. The recycling of G glass often requires specialized facilities and technologies, making it less readily recyclable compared to other materials.
- Cost: While G glass can be cost-effective in some applications, it can be more expensive than other materials, such as ordinary soda-lime glass, for certain applications. The cost of G glass production and processing can vary depending on the specific requirements and desired properties.
Comparison with Alternative Materials
G glass offers a unique set of advantages and disadvantages compared to other materials commonly used in various applications.
- Polycarbonate: Polycarbonate is a lightweight and impact-resistant plastic often used as an alternative to G glass. However, polycarbonate is less chemically resistant and has a lower melting point than G glass. Polycarbonate is also susceptible to scratching and can degrade under prolonged exposure to UV radiation.
- Acrylic: Acrylic is another plastic alternative to G glass, known for its clarity and impact resistance. However, acrylic is less scratch-resistant and can be more susceptible to chemical attack than G glass. Acrylic also has a lower melting point and can become brittle at low temperatures.
- Soda-Lime Glass: Soda-lime glass is a common and inexpensive type of glass, but it lacks the strength, durability, and chemical resistance of G glass. Soda-lime glass is also more susceptible to thermal shock and can crack or break when exposed to sudden temperature changes.
Future Trends and Innovations in G Glass Technology
The field of G glass technology is constantly evolving, with ongoing research and development leading to new compositions, manufacturing processes, and applications. These advancements are driven by the need for improved performance, cost-effectiveness, and sustainability in various industries.
Emerging Trends and Research in G Glass Technology
- Development of New Compositions: Researchers are exploring novel glass compositions with enhanced properties, such as increased strength, thermal resistance, and optical clarity. For example, the incorporation of nanomaterials, such as graphene, into G glass matrices has shown promising results in improving mechanical strength and electrical conductivity. This can lead to applications in high-performance structural components and electronic devices.
- Advanced Manufacturing Processes: The development of innovative manufacturing techniques, such as 3D printing and sol-gel processing, allows for the creation of complex G glass structures with tailored properties. 3D printing enables the fabrication of intricate designs and functional components, while sol-gel processing offers a cost-effective route for producing thin films and coatings with desired properties.
- Applications in Renewable Energy: G glass is playing an increasingly important role in renewable energy technologies. For instance, its use in solar panels and wind turbines is expanding, as it offers excellent optical transparency and durability. Advancements in G glass technology are enabling the development of more efficient and cost-effective solar cells and wind turbine blades.
Potential Future Innovations in G Glass Technology
- Self-Healing G Glass: Researchers are investigating the development of self-healing G glass, which can repair microscopic cracks and defects upon exposure to heat or light. This could significantly enhance the durability and lifespan of G glass components, particularly in demanding environments. One approach involves incorporating microcapsules filled with a healing agent into the glass matrix. When a crack occurs, the capsules rupture, releasing the healing agent that fills the crack and solidifies, effectively repairing the damage.
- Bioactive G Glass: Bioactive G glass is being explored for its potential in biomedical applications. This type of glass can interact with living tissues, promoting cell growth and bone regeneration. For example, bioactive G glass can be used in implants, such as bone grafts, to enhance integration with the surrounding tissues. This can lead to improved healing outcomes and reduced implant rejection.
- G Glass with Enhanced Optical Properties: Advancements in G glass technology are leading to the development of glasses with improved optical properties, such as increased refractive index and reduced light scattering. This can benefit applications in optical fibers, lenses, and displays. For example, G glass with a higher refractive index can be used to create smaller and more powerful lenses, leading to miniaturized optical devices.
Impact of G Glass Advancements on Industries and Sectors
- Construction: Improved G glass properties, such as increased strength and thermal resistance, can lead to lighter, more durable, and energy-efficient buildings. This can benefit both residential and commercial construction, reducing building costs and environmental impact.
- Transportation: Lightweight and strong G glass components can be used in vehicles, reducing fuel consumption and emissions. For example, G glass can be used in windshields, windows, and other structural components of cars, trucks, and airplanes.
- Electronics: G glass is being incorporated into various electronic devices, including smartphones, tablets, and laptops. Its optical transparency and electrical conductivity make it suitable for touchscreens, displays, and other components. Advancements in G glass technology can lead to thinner, lighter, and more durable electronic devices.
- Healthcare: Bioactive G glass has the potential to revolutionize healthcare, with applications in implants, drug delivery systems, and tissue engineering. This can lead to improved treatment outcomes and reduced healthcare costs.
Closing Notes
As we delve deeper into the fascinating world of G glass technology, we witness its transformative impact on modern society. Its remarkable properties have propelled advancements in numerous industries, pushing the boundaries of innovation and redefining the possibilities of glass. From towering skyscrapers to high-performance vehicles, G glass stands as a testament to human ingenuity and its ability to create materials that shape the future.
G glass technology, with its exceptional strength and durability, has revolutionized various industries. Companies like mccown technology corporation are at the forefront of utilizing this innovative material, integrating it into their products and services. This integration of g glass technology not only enhances the performance and longevity of their offerings but also signifies a commitment to pushing the boundaries of what’s possible in the world of technology.