GOL Pump Technology: A Revolutionary Approach to Fluid Movement
GOL pump technology, a groundbreaking innovation in fluid mechanics, harnesses the power of electromagnetic fields and plasma to propel fluids with unprecedented efficiency and precision. This technology, still in its […]
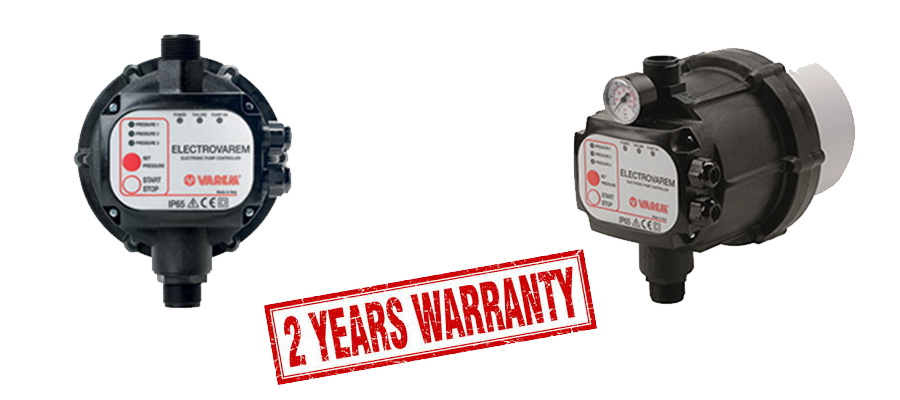
GOL pump technology, a groundbreaking innovation in fluid mechanics, harnesses the power of electromagnetic fields and plasma to propel fluids with unprecedented efficiency and precision. This technology, still in its nascent stages, promises to revolutionize industries reliant on fluid movement, from water treatment to aerospace.
The core principle behind GOL pumps lies in the creation of a plasma channel within a specially designed chamber. This channel, generated by high-voltage electrical discharges, acts as a conduit for energy transfer, propelling the fluid forward with remarkable force. The unique properties of plasma, a superheated ionized gas, allow for energy transfer at rates exceeding traditional pump systems.
Introduction to GOL Pump Technology
GOL pump technology is a specialized type of pump that utilizes a gas-liquid mixture as the working fluid to transfer energy to the liquid phase. This technology finds application in various industries, including oil and gas, chemical processing, and power generation. GOL pumps are particularly suited for handling liquids with high viscosity, high vapor pressure, or a tendency to form solids.
The fundamental principle behind GOL pump operation is the transfer of energy from a gas phase to a liquid phase. The gas, typically compressed air or inert gas, is injected into the pump chamber, where it mixes with the liquid. The gas-liquid mixture then flows through a specially designed impeller, which imparts kinetic energy to the liquid. As the gas-liquid mixture exits the impeller, the gas is separated from the liquid, and the liquid is discharged at a higher pressure.
History of GOL Pump Development
The development of GOL pump technology can be traced back to the early 20th century. Early GOL pumps were primarily used in the oil and gas industry for handling crude oil and other viscous fluids. Over time, GOL pump technology has evolved significantly, with advancements in pump design, materials, and operating principles. Modern GOL pumps are highly efficient and reliable, capable of handling a wide range of fluids and operating conditions.
GOL pumps have gained widespread acceptance in various industries due to their ability to handle challenging fluids and their high efficiency.
Components of a GOL Pump
A GOL pump, or Gas-Operated Liquid Pump, is a unique and innovative technology that harnesses the power of expanding gases to generate high pressures and drive liquids. It consists of several key components working in concert to achieve this goal. These components are meticulously designed and integrated to ensure efficient and reliable operation, enabling the pump to deliver impressive performance in various applications.
GOL Generator
The GOL generator is the heart of the GOL pump system. It is responsible for producing the expanding gas that drives the pump. This is typically achieved through the combustion of a fuel source, such as natural gas, propane, or diesel fuel. The combustion process generates high-temperature and high-pressure gases that are then directed to the pump chamber.
The GOL generator is typically constructed using robust materials such as stainless steel or heat-resistant alloys. These materials are chosen for their high strength, corrosion resistance, and ability to withstand the extreme temperatures and pressures involved in the combustion process.
Pump Chamber
The pump chamber is where the energy from the expanding gas is transferred to the liquid being pumped. It is typically a cylindrical chamber with a piston or diaphragm that is driven by the expanding gas. As the gas expands, it pushes against the piston or diaphragm, creating pressure that forces the liquid out of the chamber and into the discharge line.
The pump chamber is often made of materials like cast iron, stainless steel, or other corrosion-resistant materials, depending on the specific application and the fluid being pumped. These materials are chosen for their durability, strength, and ability to withstand the high pressures generated within the chamber.
Energy Transfer Mechanism
The energy transfer mechanism is the component that connects the expanding gas to the piston or diaphragm in the pump chamber. This mechanism is typically a valve or a series of valves that control the flow of gas into the chamber. These valves are often made of materials like stainless steel or other corrosion-resistant alloys to ensure long-term durability and reliable operation.
The energy transfer mechanism is critical to the pump’s efficiency and performance. It must be designed to allow for rapid and controlled gas flow into the chamber, ensuring that the expanding gas can efficiently drive the piston or diaphragm. This, in turn, translates to high pressure and efficient pumping of the liquid.
Materials Used in GOL Pump Construction, Gol pump technology
The materials used in GOL pump construction are carefully selected to ensure the pump’s durability, performance, and safety. These materials must be able to withstand the high temperatures, pressures, and corrosive environments that are common in GOL pump applications.
- Stainless Steel: A widely used material in GOL pump construction due to its excellent corrosion resistance, high strength, and ability to withstand high temperatures. It is commonly used in components such as the pump chamber, piston, and valves.
- Cast Iron: Often used for the pump chamber due to its high strength and durability, making it suitable for handling high pressures. It is also relatively inexpensive, making it a cost-effective option for many applications.
- Heat-Resistant Alloys: These alloys, such as Inconel and Hastelloy, are used in components exposed to extremely high temperatures, such as the GOL generator and combustion chamber. They offer excellent resistance to oxidation, corrosion, and creep at elevated temperatures.
- Polymers: Certain polymers, such as PTFE (Teflon), are used in components that require low friction and excellent chemical resistance. These polymers are often used in seals and gaskets to prevent leakage and ensure smooth operation.
Working Principle of GOL Pumps
GOL pumps, also known as Gas-dynamic Optical Lasers, harness the energy of a rapidly expanding plasma to generate a powerful laser beam. This unique approach utilizes a combination of electromagnetic fields and plasma physics to create a highly efficient and versatile laser system.
Electromagnetic Fields and Plasma
The operation of a GOL pump relies on the interaction between electromagnetic fields and a highly ionized plasma. The plasma, a superheated gas composed of free electrons and ions, is created by discharging a large capacitor bank into a gas. The rapid release of energy creates a shock wave that accelerates the plasma to extreme velocities. This high-velocity plasma then interacts with a series of magnetic coils, generating a powerful electromagnetic field.
Stages of the Pump Cycle
The operation of a GOL pump can be broken down into several distinct stages:
- Energy Generation: The process begins with the discharge of a capacitor bank into a gas, creating a plasma. This energy discharge is highly efficient, converting electrical energy into kinetic energy of the plasma.
- Plasma Acceleration: The plasma, propelled by the shock wave, accelerates rapidly. This acceleration is further enhanced by the magnetic fields generated by the coils, directing the plasma flow and increasing its velocity.
- Laser Cavity Interaction: The high-velocity plasma enters the laser cavity, where it interacts with a resonant optical cavity. The energy stored in the plasma is then transferred to the laser medium, stimulating the emission of photons.
- Laser Beam Generation: The stimulated emission of photons within the laser cavity results in the amplification of the laser beam. The energy stored in the plasma is efficiently converted into a powerful laser beam.
Energy Transfer in a GOL Pump
The transfer of energy in a GOL pump is a complex process involving multiple stages. The initial energy source is the capacitor bank, which discharges a large amount of electrical energy into the gas. This energy is then converted into the kinetic energy of the plasma, which is accelerated by the magnetic fields. The accelerated plasma then interacts with the laser cavity, transferring its energy to the laser medium. This energy transfer process is highly efficient, resulting in the generation of a powerful laser beam.
Advantages and Disadvantages of GOL Pump Technology
GOL pump technology, while innovative and promising, comes with its own set of advantages and disadvantages. Understanding these aspects is crucial for making informed decisions regarding its implementation and application.
Advantages of GOL Pump Technology
The high efficiency of GOL pumps is a significant advantage. They achieve this by minimizing energy losses due to friction and turbulence, resulting in a higher percentage of input energy being converted into fluid flow. This translates into lower operating costs and a reduced environmental footprint.
- High Efficiency: GOL pumps excel in energy efficiency, converting a greater portion of input energy into fluid flow. This leads to lower operating costs and reduced energy consumption.
- Low Maintenance: Due to their simple design with fewer moving parts, GOL pumps require less maintenance compared to traditional pumps. This translates to lower operational downtime and maintenance costs.
- High Pressure Capabilities: GOL pumps can generate significantly higher pressures compared to conventional pumps, making them suitable for applications requiring high-pressure fluid delivery.
- Quiet Operation: GOL pumps are known for their quiet operation, minimizing noise pollution and enhancing the overall working environment.
- Wide Range of Applications: GOL pumps are versatile and can be applied in various industries, including water treatment, chemical processing, and oil and gas extraction.
Disadvantages of GOL Pump Technology
While offering significant advantages, GOL pump technology also comes with certain drawbacks that need to be considered.
- High Initial Cost: GOL pumps are typically more expensive to manufacture than conventional pumps, leading to higher initial investment costs.
- Complexity: The design and operation of GOL pumps can be more complex compared to traditional pumps, requiring specialized expertise for installation, maintenance, and troubleshooting.
- Potential Safety Concerns: The high pressures generated by GOL pumps can pose safety risks if not handled properly. Adequate safety protocols and procedures are essential for safe operation.
- Limited Availability: GOL pumps are still a relatively new technology, and their availability in the market may be limited compared to conventional pumps.
- Research and Development: Further research and development are needed to optimize the performance and address the challenges associated with GOL pump technology.
Applications of GOL Pump Technology
GOL pump technology, with its unique advantages in handling various fluids, finds applications across diverse industries. These pumps are particularly well-suited for situations involving high viscosity, abrasive slurries, or fluids with a high solids content.
Industrial Applications
The robust design and high-performance capabilities of GOL pumps make them ideal for various industrial processes.
- Mining and Mineral Processing: GOL pumps are widely used in mining operations for transporting slurries containing ore, minerals, and other materials. Their ability to handle abrasive and corrosive materials, along with their high flow rates, makes them a reliable choice for this demanding application.
- Power Generation: In power plants, GOL pumps play a crucial role in handling coal ash, fly ash, and other byproducts of combustion. Their ability to handle abrasive and high-temperature materials ensures efficient and reliable operation of power generation systems.
- Chemical Processing: GOL pumps are employed in chemical processing plants for handling various chemicals, including corrosive and viscous fluids. Their resistance to chemical attack and their ability to handle high pressures make them suitable for a wide range of chemical applications.
- Wastewater Treatment: GOL pumps are used in wastewater treatment plants for pumping sludge, grit, and other solids. Their ability to handle high solids content and abrasive materials makes them an effective solution for wastewater treatment processes.
Benefits and Challenges of GOL Pump Implementation
Implementing GOL pumps in various applications brings numerous benefits, but it also presents certain challenges.
- Benefits:
- High Efficiency: GOL pumps offer high efficiency, minimizing energy consumption and reducing operating costs.
- Reduced Maintenance: Their robust design and simple construction minimize maintenance requirements, leading to increased uptime and reduced downtime.
- Handling Abrasive Materials: GOL pumps are designed to handle abrasive materials, reducing wear and tear on the pump components.
- High Flow Rates: GOL pumps can achieve high flow rates, making them suitable for applications requiring large volumes of fluid transfer.
- Challenges:
- Initial Investment: GOL pumps can have a higher initial investment cost compared to other types of pumps.
- Limited Fluid Viscosity Range: While GOL pumps can handle high viscosity fluids, their operating range may be limited compared to other pump types.
- Noise and Vibration: GOL pumps can generate significant noise and vibration during operation, which may require noise mitigation measures.
Case Studies
GOL pump technology has been successfully implemented in various sectors, demonstrating its effectiveness in handling challenging applications.
- Mining: In a large-scale mining operation in Australia, GOL pumps were deployed to transport iron ore slurry from the mine site to the processing plant. The pumps’ ability to handle abrasive materials and high flow rates ensured efficient and reliable operation, significantly reducing downtime and maintenance costs.
- Wastewater Treatment: In a municipal wastewater treatment plant in the United States, GOL pumps were installed to handle sludge and grit. The pumps’ robust design and high solids handling capacity allowed for efficient and reliable operation, reducing the need for frequent maintenance and ensuring optimal wastewater treatment.
- Chemical Processing: A chemical plant in Europe implemented GOL pumps for handling a highly corrosive and viscous chemical. The pumps’ resistance to chemical attack and their ability to handle high pressures ensured safe and efficient operation, minimizing downtime and production losses.
Future Trends in GOL Pump Technology
GOL pump technology is a rapidly evolving field with significant potential for further development and innovation. Ongoing research and development efforts are focused on enhancing the efficiency, performance, and reliability of GOL pumps, while also exploring new applications and potential breakthroughs.
Advancements in GOL Pump Design and Materials
The design and materials used in GOL pumps are constantly being refined to improve their performance and longevity. For instance, researchers are investigating the use of advanced materials, such as composites and ceramics, to enhance the pump’s resistance to wear and tear, corrosion, and high temperatures. These materials can also contribute to increased efficiency and reduced energy consumption.
- Improved impeller designs: Optimization of impeller geometry and blade profiles to enhance fluid flow and reduce cavitation, thereby increasing efficiency and minimizing wear.
- Advanced materials: Exploration of novel materials, such as high-strength alloys, ceramics, and composites, for improved wear resistance, corrosion resistance, and thermal stability, leading to longer service life and reduced maintenance requirements.
- Magnetic bearings: Integration of magnetic bearings to eliminate mechanical friction and wear, resulting in higher efficiency, quieter operation, and reduced maintenance needs.
Enhanced Efficiency and Performance
Ongoing research focuses on optimizing GOL pump design and operation to improve efficiency and performance. This includes exploring new impeller designs, advanced materials, and control systems. For example, the development of variable-speed drives allows for more precise control of the pump’s operating speed, leading to reduced energy consumption and improved efficiency.
- Variable-speed drives: Implementing variable-speed drives to optimize pump speed based on demand, minimizing energy consumption and maximizing efficiency.
- Smart control systems: Developing advanced control systems that can monitor and adjust pump operation in real-time, optimizing performance and reducing energy waste.
- Cavitation mitigation techniques: Implementing strategies to minimize cavitation, such as optimized impeller design and inlet flow control, to enhance efficiency and reduce wear.
Emerging Applications of GOL Pumps
GOL pumps are finding new applications in diverse industries, driven by their unique advantages. For instance, their ability to handle abrasive and corrosive fluids makes them ideal for use in mining, chemical processing, and wastewater treatment.
- Mining: GOL pumps are increasingly used in mining operations to transport slurries and abrasive materials, offering high efficiency and durability in challenging environments.
- Chemical processing: Their ability to handle corrosive fluids makes them suitable for applications in chemical processing plants, where they can transport and mix chemicals safely and efficiently.
- Wastewater treatment: GOL pumps are employed in wastewater treatment plants to move and process sludge, offering reliable operation in harsh environments.
Integration with Digital Technologies
The integration of digital technologies, such as sensors, data analytics, and cloud computing, is transforming GOL pump technology. These advancements enable real-time monitoring of pump performance, predictive maintenance, and remote control.
- Remote monitoring and control: Enabling remote monitoring and control of GOL pumps through digital platforms, allowing for real-time performance tracking and remote troubleshooting.
- Predictive maintenance: Utilizing data analytics to predict potential failures and schedule maintenance proactively, minimizing downtime and extending pump lifespan.
- Smart grids: Integrating GOL pumps into smart grids to optimize energy consumption and improve overall system efficiency.
Outcome Summary
GOL pump technology holds immense potential to transform various industries by offering a more efficient, environmentally friendly, and versatile approach to fluid movement. While challenges remain in terms of cost and scalability, ongoing research and development are paving the way for widespread adoption. As we continue to explore the possibilities of this revolutionary technology, its impact on our world is sure to be profound.
Gol pump technology is a fascinating field, constantly evolving to meet the demands of various industries. One company that’s making waves in this space is real time technologies llc , known for its innovative solutions and commitment to efficiency. Their expertise in real-time data analysis and automation helps optimize gol pump operations, leading to improved performance and cost savings.