Aircraft Engineering & Aerospace Technology: Shaping the Future of Flight
Aircraft engineering & aerospace technology is a field that has captivated humanity for centuries, pushing the boundaries of human ingenuity and driving innovation in the skies. From the Wright brothers’ […]
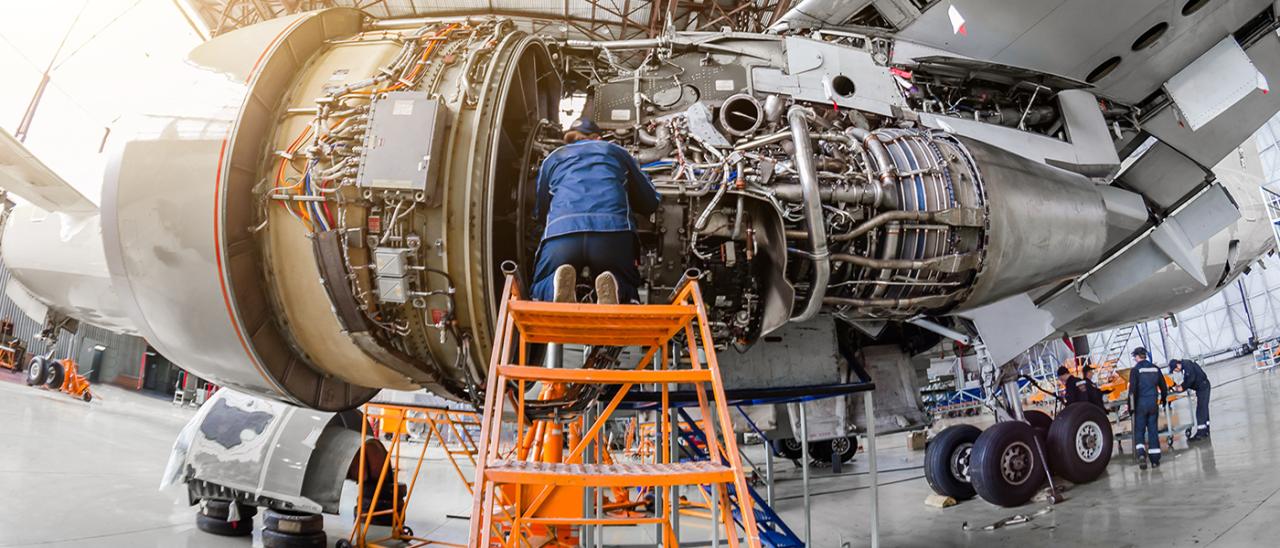
Aircraft engineering & aerospace technology is a field that has captivated humanity for centuries, pushing the boundaries of human ingenuity and driving innovation in the skies. From the Wright brothers’ first flight to the sleek, supersonic jets of today, the quest to conquer the air has led to remarkable advancements in design, materials, and propulsion systems.
This exploration delves into the fascinating world of aircraft engineering and aerospace technology, examining the fundamental principles that govern flight, the evolution of aircraft design, and the cutting-edge innovations shaping the future of aviation. We will journey through the history of this remarkable field, uncovering the key milestones that have paved the way for the incredible feats of modern aerospace engineering.
History of Aircraft Engineering and Aerospace Technology
The history of aircraft engineering and aerospace technology is a captivating journey of human ingenuity and ambition, spanning over a century of groundbreaking inventions and advancements. From the early dream of flight to the exploration of the cosmos, this field has witnessed the transformation of our understanding of the skies and beyond.
Early Pioneers and Their Contributions
The birth of aviation can be traced back to the pioneering efforts of individuals who dared to challenge the limitations of gravity. Their tireless pursuit of flight laid the foundation for the modern aerospace industry.
- George Cayley (1773-1857), often hailed as the “father of aeronautics,” was a British scientist who conducted extensive research on the principles of flight. He developed the concept of fixed wings and recognized the importance of lift and drag forces. His work, although largely theoretical, provided a crucial framework for future aviation pioneers.
- Otto Lilienthal (1848-1896), a German engineer, was a pioneer of glider flight. He designed and built numerous gliders, conducting hundreds of successful flights. Lilienthal’s experiments provided valuable insights into the aerodynamics of flight and helped advance the understanding of wing design.
- The Wright brothers (Wilbur and Orville), American inventors and engineers, achieved the first successful sustained and controlled flight of a heavier-than-air aircraft on December 17, 1903. Their meticulous experimentation, innovative design, and relentless pursuit of their dream led to the groundbreaking invention of the airplane, marking a turning point in human history.
Evolution of Aircraft Design, Aircraft engineering & aerospace technology
From the rudimentary biplanes of the early 20th century to the sophisticated jet aircraft of today, the evolution of aircraft design has been a testament to the relentless pursuit of efficiency, speed, and safety.
- Early Biplanes: The first airplanes were primarily biplanes, characterized by their two sets of wings. These aircraft were relatively slow and had limited range but represented a significant breakthrough in aviation technology. Examples include the Wright Flyer and the Blériot XI, which crossed the English Channel in 1909.
- Monoplanes and the Development of Engines: The development of more powerful engines and improved aerodynamic designs led to the emergence of monoplanes, which offered greater efficiency and speed. The introduction of metal construction, streamlined fuselages, and retractable landing gear further enhanced aircraft performance.
- Jet Age: The advent of jet engines in the mid-20th century revolutionized air travel. Jet aircraft, with their high speeds and long ranges, transformed long-distance transportation. Examples include the de Havilland Comet, the first commercial jet airliner, and the Boeing 707, which ushered in the era of mass air travel.
Key Milestones in Aerospace Technology
The pursuit of flight has extended beyond the Earth’s atmosphere, propelling humanity into the realm of space exploration. The development of rockets, satellites, and space exploration technologies has opened up new frontiers and expanded our understanding of the universe.
- Rocketry: The development of rockets, fueled by the pioneering work of Robert H. Goddard and Wernher von Braun, paved the way for space travel. Goddard’s early experiments with liquid-fueled rockets laid the foundation for modern rocket propulsion, while von Braun’s work with the V-2 rocket during World War II provided valuable insights into rocket technology.
- Satellites: The launch of Sputnik 1, the first artificial satellite, by the Soviet Union in 1957 marked a significant milestone in space exploration. Satellites have become indispensable tools for communication, navigation, weather forecasting, and scientific research.
- Space Exploration: The human race’s journey into space began with the launch of Yuri Gagarin, a Soviet cosmonaut, into Earth orbit in 1961. This historic event sparked the Space Race between the United States and the Soviet Union, leading to advancements in space technology and the development of the Apollo program, which culminated in the first human landing on the Moon in 1969.
Fundamental Principles of Aircraft Engineering: Aircraft Engineering & Aerospace Technology
Aircraft engineering is a multidisciplinary field that encompasses various principles of physics, mathematics, and materials science. It involves the design, construction, and operation of aircraft, encompassing a wide range of aspects from aerodynamics and propulsion to avionics and structural integrity.
Aerodynamics
Aerodynamics is the study of how air interacts with moving objects, particularly aircraft. It forms the cornerstone of aircraft design, as it governs the forces that allow an aircraft to fly.
The four fundamental forces of aerodynamics are lift, drag, thrust, and weight.
Lift
Lift is the upward force that opposes gravity and keeps an aircraft in the air. It is generated by the airfoil shape of the wings, which creates a difference in air pressure between the upper and lower surfaces. The curved upper surface of the wing forces the air to travel a longer distance, causing it to accelerate and decrease in pressure. The lower surface experiences higher pressure, resulting in an upward force called lift.
Lift is proportional to the wing area, air density, and the square of the airspeed.
Drag
Drag is the force that opposes the motion of an aircraft through the air. It is generated by the friction between the air and the aircraft’s surface, as well as by the shape of the aircraft.
There are two main types of drag:
- Parasite drag: This is the drag caused by the friction between the air and the aircraft’s surface. It is directly proportional to the aircraft’s surface area and the square of the airspeed.
- Induced drag: This is the drag caused by the generation of lift. It is inversely proportional to the aspect ratio of the wing (the ratio of wingspan to chord length).
Thrust
Thrust is the forward force that propels the aircraft through the air. It is generated by the engines, which convert fuel energy into kinetic energy of the air.
The thrust produced by an engine is determined by the engine’s power output, the airspeed, and the efficiency of the engine.
Weight
Weight is the force of gravity acting on the aircraft. It is the sum of the weight of the aircraft itself, the weight of the fuel, and the weight of the passengers and cargo.
To achieve flight, the lift generated by the wings must be greater than the weight of the aircraft.
Aircraft Configurations
Aircraft configurations refer to the overall design and arrangement of the aircraft’s components, such as the wings, tail, fuselage, and engines.
Different configurations offer advantages and disadvantages, influencing factors like performance, stability, and cost.
Types of Aircraft Configurations
- Conventional configuration: This is the most common configuration, featuring a high-wing or low-wing layout, a single-engine or multi-engine setup, and a conventional tail. This configuration offers good stability and maneuverability, making it suitable for general aviation and commercial aircraft.
- Canard configuration: This configuration features a small forward wing, called a canard, ahead of the main wing. Canards provide additional lift and control, improving maneuverability and reducing stall speed. They are often found in high-performance aircraft, such as fighter jets and experimental aircraft.
- Flying wing configuration: This configuration eliminates the traditional fuselage and tail, with the wings serving as the primary lifting and control surfaces. Flying wings offer low drag and high fuel efficiency but present challenges in stability and control.
- Tailless configuration: This configuration eliminates the traditional tail, using a swept wing design for stability and control. Tailless aircraft offer aerodynamic efficiency and maneuverability, but require advanced control systems for stability.
Materials Science in Aircraft Design
Materials science plays a crucial role in aircraft design and construction, influencing the aircraft’s strength, weight, and durability.
Aircraft materials must meet stringent requirements for high strength-to-weight ratio, resistance to fatigue and corrosion, and ability to withstand extreme temperatures and environmental conditions.
Types of Aircraft Materials
- Aluminum alloys: These are the most common materials used in aircraft construction due to their high strength-to-weight ratio, ease of fabrication, and relatively low cost. They are used for fuselage, wings, and other structural components.
- Titanium alloys: These are stronger and more heat-resistant than aluminum alloys, making them ideal for high-stress components like landing gear, engine parts, and turbine blades. However, titanium alloys are more expensive and difficult to fabricate.
- Composite materials: These are materials made from two or more different materials, such as carbon fiber, glass fiber, and resin. Composites offer high strength-to-weight ratio, excellent corrosion resistance, and high fatigue strength. They are increasingly used in modern aircraft for wings, fuselages, and other structural components.
- Steel alloys: These are used for certain components where high strength and stiffness are required, such as landing gear, engine mounts, and some fuselage sections.
Aerospace Propulsion Systems
Propulsion systems are the heart of aircraft and spacecraft, enabling them to move through the air and space. These systems generate thrust, the force that propels the vehicle forward. Understanding the different types of propulsion systems is crucial for comprehending the evolution and future of aerospace technology.
Aircraft Engine Types
Aircraft engines can be broadly categorized into three main types: piston engines, jet engines, and turboprop engines. Each type operates on different principles and has unique advantages and disadvantages.
- Piston Engines: These engines operate on the principle of converting the linear motion of pistons into rotational motion, which drives a propeller. They are relatively simple and efficient at lower speeds but become less efficient at higher speeds. Piston engines are commonly used in smaller aircraft, such as general aviation aircraft and some light commercial aircraft.
- Jet Engines: Jet engines work by compressing air, adding heat to it, and then expanding it through a nozzle, creating thrust. They are more efficient at higher speeds and are used in most commercial airliners and military aircraft. Jet engines can be further categorized into turbojet, turbofan, and turboprop engines.
- Turboprop Engines: Turboprop engines combine the efficiency of a jet engine with the propulsive force of a propeller. They are more efficient than piston engines at higher speeds and are used in some regional airliners and military aircraft.
Rocket Propulsion
Rocket propulsion is a unique form of propulsion that relies on the principle of action and reaction. Rockets generate thrust by expelling a mass of hot gas at high velocity. This process is governed by Newton’s third law of motion, which states that for every action, there is an equal and opposite reaction.
- Principles of Rocket Propulsion: The fundamental principle of rocket propulsion is based on the conservation of momentum. A rocket engine burns fuel and oxidizer, creating hot gas that is expelled through a nozzle. The expelled gas has momentum, and according to the conservation of momentum, the rocket must acquire an equal and opposite momentum. This results in the rocket being propelled forward.
- Application in Space Exploration: Rocket propulsion is essential for launching satellites, spacecraft, and humans into space. Rockets are used to provide the initial thrust to overcome Earth’s gravity and to maneuver spacecraft in space. The choice of rocket engine depends on the mission requirements, including the payload mass, the desired trajectory, and the required thrust.
Challenges and Future Trends
Aerospace propulsion technology is constantly evolving, driven by the need for greater efficiency, reduced emissions, and improved performance. The following are some of the challenges and future trends in aerospace propulsion:
- Emissions Reduction: Reducing emissions from aircraft engines is a major challenge, particularly in the context of climate change. Researchers are exploring new technologies, such as biofuels and electric propulsion, to reduce emissions.
- Noise Reduction: Aircraft noise is a significant environmental concern, especially for communities living near airports. New engine designs and noise-reduction technologies are being developed to minimize noise levels.
- Electric Propulsion: Electric propulsion systems are gaining traction in aerospace, particularly for smaller aircraft and spacecraft. These systems offer advantages such as higher efficiency and lower emissions. However, challenges remain in terms of battery capacity and weight.
- Hypersonic Propulsion: Hypersonic propulsion systems are being developed for aircraft that can travel at speeds exceeding Mach 5. These systems face significant challenges related to heat management and engine efficiency.
Aircraft Design and Development
Aircraft design and development is a complex and multifaceted process that involves numerous stages, from initial conceptualization to final certification. It requires a collaborative effort from engineers, designers, and other specialists to create safe, efficient, and innovative aircraft.
Aircraft Development Stages
The development of a new aircraft typically involves a series of well-defined stages, each with its specific objectives and deliverables. These stages ensure a systematic and structured approach to aircraft design, development, and production.
Stage | Description |
---|---|
Conceptual Design | This stage involves defining the aircraft’s mission, performance requirements, and preliminary design parameters. It includes exploring different design concepts, conducting feasibility studies, and generating initial sketches and layouts. |
Detailed Design | In this stage, the aircraft’s design is refined and detailed, including the development of detailed drawings, specifications, and engineering analyses. This involves determining the aircraft’s structural configuration, propulsion system, avionics, and other subsystems. |
Manufacturing | The manufacturing stage involves producing the aircraft components and assembling them into a complete aircraft. This includes procuring materials, machining parts, assembling subassemblies, and conducting quality control checks. |
Testing | The testing stage involves evaluating the aircraft’s performance, safety, and reliability through a series of ground and flight tests. This includes static tests, fatigue tests, and flight tests to validate the aircraft’s design and performance characteristics. |
Certification | Certification is the final stage, where the aircraft is evaluated by regulatory authorities to ensure it meets all safety and airworthiness standards. This involves rigorous inspections, flight tests, and documentation reviews to obtain certification for commercial or military operations. |
Innovative Aircraft Designs
The field of aircraft design is constantly evolving, with advancements in technology driving the development of innovative aircraft designs. These advancements include:
- Unmanned Aerial Vehicles (UAVs): UAVs, also known as drones, have revolutionized various sectors, including military, surveillance, and delivery. They offer significant advantages in terms of cost-effectiveness, flexibility, and safety.
- Electric Aircraft: The development of electric propulsion systems has led to the emergence of electric aircraft, offering potential benefits in terms of reduced emissions and noise pollution.
- Hypersonic Aircraft: Hypersonic aircraft are designed to fly at speeds exceeding Mach 5, enabling faster travel times and new possibilities for space exploration.
- Vertical Takeoff and Landing (VTOL) Aircraft: VTOL aircraft, such as helicopters and tiltrotor aircraft, offer the ability to take off and land vertically, providing flexibility and access to challenging environments.
- Advanced Materials: The use of advanced materials, such as composites and lightweight alloys, has significantly improved aircraft performance, fuel efficiency, and structural integrity.
Aerospace Materials and Manufacturing
The selection and use of materials in aerospace engineering are critical for the performance, safety, and cost-effectiveness of aircraft. Aerospace materials must possess exceptional strength-to-weight ratios, resistance to high temperatures, fatigue, and corrosion, along with excellent manufacturability. This section explores the diverse materials employed in aircraft construction and the manufacturing processes that shape these materials into complex aircraft components.
Aluminum Alloys
Aluminum alloys are the most widely used materials in aircraft construction due to their favorable combination of strength, lightweight, and cost-effectiveness. These alloys are formed by adding elements such as copper, magnesium, manganese, and silicon to pure aluminum, enhancing its mechanical properties. Aluminum alloys are commonly used for fuselage skins, wings, and other structural components.
Composites
Composites are materials composed of two or more distinct components with different properties, resulting in a material with enhanced performance characteristics. In aerospace engineering, composites are widely used due to their high strength-to-weight ratios, excellent fatigue resistance, and resistance to corrosion.
- Fiber-reinforced polymers (FRP): These composites consist of strong fibers, such as carbon fiber, glass fiber, or aramid fiber, embedded in a polymer matrix. The fibers provide strength and stiffness, while the matrix binds the fibers together and distributes load. Carbon fiber reinforced polymers (CFRP) are particularly prevalent in aerospace applications due to their exceptional strength and stiffness, making them ideal for high-performance aircraft components like wings, tail sections, and control surfaces.
- Metal matrix composites (MMC): These composites combine a metal matrix with reinforcing fibers or particles, often ceramic or metal, to improve properties like strength, stiffness, and wear resistance. Aluminum MMCs are used in aircraft components like engine parts, landing gear, and brakes.
Titanium Alloys
Titanium alloys are known for their high strength-to-weight ratio, excellent corrosion resistance, and ability to withstand high temperatures. These alloys are commonly used in high-stress areas like landing gear, engine components, and high-temperature sections of the aircraft. Titanium alloys are more expensive than aluminum alloys, but their exceptional properties justify their use in critical applications.
Manufacturing Processes
The manufacturing processes employed in aerospace engineering are highly specialized, requiring precision, accuracy, and strict quality control.
- Machining: Machining involves removing material from a workpiece using a cutting tool to achieve desired shapes and dimensions. This process is commonly used to create parts from aluminum, titanium, and composites.
- Welding: Welding is a process that joins two or more pieces of metal by melting and fusing them together. Aerospace welding techniques, such as gas tungsten arc welding (GTAW) and laser welding, are employed to create strong and durable joints in aircraft structures.
- Composites Fabrication: The fabrication of composite components involves several steps, including pre-impregnated fiber layup, molding, curing, and post-processing.
Challenges and Advancements
The aerospace industry continuously seeks to improve materials and manufacturing processes to enhance aircraft performance, reduce costs, and minimize environmental impact.
- Lightweight materials: The development of new lightweight materials, such as advanced composites and metal alloys, is a major focus area to reduce aircraft weight and improve fuel efficiency.
- Additive Manufacturing (3D Printing): Additive manufacturing, or 3D printing, is a revolutionary technology that allows for the creation of complex shapes and designs from digital models. This technology offers significant advantages in aerospace manufacturing, including reduced lead times, improved design flexibility, and the ability to create lightweight and complex components.
- Sustainable Materials: The aerospace industry is increasingly focusing on the use of sustainable materials, such as bio-based composites and recycled materials, to minimize environmental impact.
Flight Control and Avionics
Flight control and avionics systems are essential for the safe and efficient operation of aircraft. They provide pilots with the necessary information and tools to control the aircraft, navigate, communicate, and manage flight operations.
Principles of Flight Control Systems
Flight control systems are designed to maintain aircraft stability and maneuverability. They work by manipulating aerodynamic forces, such as lift, drag, and thrust, to control the aircraft’s attitude, direction, and speed.
- Aerodynamic Control Surfaces: These are movable surfaces, such as ailerons, elevators, and rudders, that are used to alter the flow of air over the aircraft’s wings and tail, generating changes in lift, drag, and pitch, roll, and yaw moments.
- Flight Control Actuators: These are mechanical devices that translate pilot commands into movements of the control surfaces. Actuators can be hydraulic, electric, or electromechanical.
- Flight Control Sensors: These sensors provide feedback on the aircraft’s position, attitude, and motion. Sensors include accelerometers, gyroscopes, and airspeed indicators.
- Flight Control Computers: These computers process sensor data and calculate the necessary control surface movements to maintain stability and execute pilot commands.
Evolution of Avionics Systems
Avionics systems have evolved significantly over the years, becoming increasingly sophisticated and integrated.
- Navigation Systems: Early navigation systems relied on ground-based radio beacons and celestial navigation. Modern aircraft use Global Positioning System (GPS) and inertial navigation systems (INS) for precise navigation.
- Communication Systems: Aircraft communication systems have evolved from basic radio systems to advanced satellite-based communication systems that enable high-bandwidth data transfer and voice communication worldwide.
- Flight Management Systems (FMS): FMS are sophisticated computer systems that automate many aspects of flight operations, including route planning, navigation, and performance management. They provide pilots with real-time information and guidance to optimize flight efficiency and safety.
Impact of Artificial Intelligence and Automation
Artificial intelligence (AI) and automation are revolutionizing aircraft flight control.
- Automated Flight Control: AI-powered systems are being developed to automate various aspects of flight control, such as takeoff, landing, and cruise flight. This can enhance safety and efficiency by reducing pilot workload and improving situational awareness.
- Adaptive Flight Control: AI algorithms can analyze flight data in real-time and adapt control inputs to optimize performance and safety. This can improve aircraft handling characteristics and reduce the risk of accidents.
- Predictive Maintenance: AI can analyze sensor data to predict potential maintenance issues before they occur, reducing downtime and improving aircraft reliability.
Aerospace Safety and Regulations
Ensuring the safety of aircraft and passengers is paramount in the aviation industry. This involves stringent regulations and standards that govern every aspect of aircraft design, operation, and maintenance. A comprehensive safety framework encompassing international collaboration, regulatory bodies, and continuous improvement efforts plays a vital role in minimizing risks and promoting safe air travel.
Aircraft Design and Certification Standards
Aircraft design and certification standards are crucial for ensuring the safety and airworthiness of aircraft. These standards are established by regulatory bodies like the Federal Aviation Administration (FAA) in the United States and the European Aviation Safety Agency (EASA) in Europe.
- Airworthiness Certification: This process involves rigorous testing and evaluation of aircraft designs to ensure they meet specific safety requirements. Certification is granted after the aircraft demonstrates compliance with all applicable regulations and standards.
- Design Standards: These standards cover various aspects of aircraft design, including structural integrity, flight control systems, engine performance, and emergency procedures. They aim to minimize the risk of structural failure, control issues, engine malfunctions, and other potential hazards.
- Materials and Manufacturing: Strict regulations govern the selection, testing, and use of materials in aircraft construction. These regulations ensure the durability, strength, and resistance of materials to various environmental conditions and potential stresses.
Aviation Safety Organizations
Aviation safety organizations play a vital role in promoting safety, investigating accidents, and setting standards for the industry.
- International Civil Aviation Organization (ICAO): This UN agency sets global standards for aviation safety and security, including regulations for aircraft design, operation, and maintenance. ICAO provides a platform for international cooperation and promotes the harmonization of safety standards worldwide.
- National Transportation Safety Board (NTSB): In the United States, the NTSB investigates aviation accidents and incidents, aiming to determine the probable cause and make safety recommendations to prevent future occurrences.
- European Aviation Safety Agency (EASA): EASA promotes aviation safety in Europe by developing and implementing regulations, overseeing certification, and conducting safety investigations.
Aircraft Maintenance and Operations
Stringent regulations govern aircraft maintenance and operations to ensure continued airworthiness and safety. These regulations encompass scheduled inspections, maintenance procedures, and operational procedures to minimize the risk of malfunctions and accidents.
- Maintenance Programs: Aircraft undergo regular inspections and maintenance according to strict schedules and procedures. These programs aim to detect and address potential issues before they escalate into safety concerns.
- Pilot Training and Licensing: Pilots must undergo rigorous training and meet stringent licensing requirements to demonstrate proficiency in operating aircraft safely. These requirements ensure that pilots possess the necessary skills and knowledge to handle various flight situations effectively.
- Operational Procedures: Aviation authorities establish detailed operational procedures for aircraft operations, including flight planning, communication protocols, and emergency procedures. These procedures aim to minimize the risk of human error and ensure that pilots and air traffic controllers have clear guidelines to follow during flights.
Research and Development for Enhanced Safety
Ongoing research and development efforts are continuously improving aircraft safety by incorporating new technologies and enhancing existing systems.
- Advanced Flight Control Systems: New technologies like fly-by-wire systems and advanced automation features are enhancing flight control systems, providing pilots with increased situational awareness and assistance in managing complex flight situations.
- Collision Avoidance Systems: Advanced collision avoidance systems are being developed and implemented to detect potential conflicts between aircraft and provide timely warnings to pilots, reducing the risk of mid-air collisions.
- Data Analytics and Predictive Maintenance: Data analytics and predictive maintenance techniques are being used to monitor aircraft performance and predict potential maintenance needs, enabling proactive maintenance and reducing the risk of unexpected failures.
Future Trends in Aerospace Technology
The aerospace industry is constantly evolving, driven by advancements in technology and a growing demand for efficient and sustainable air travel. Emerging trends in aerospace engineering are shaping the future of aviation, promising significant changes in how we travel, explore space, and interact with our environment.
Electric and Hybrid Aircraft
The development of electric and hybrid aircraft is a major focus in the aerospace industry, aiming to reduce reliance on fossil fuels and mitigate environmental impact. Electric aircraft, powered by batteries, offer the potential for quiet, zero-emission flight, particularly for short-haul routes. Hybrid aircraft, combining electric propulsion with traditional jet engines, can extend the range and payload capacity of electric aircraft.
- Increased Efficiency: Electric and hybrid aircraft offer improved fuel efficiency compared to traditional aircraft, contributing to a reduction in greenhouse gas emissions and operating costs.
- Reduced Noise Pollution: Electric propulsion systems generate significantly less noise than conventional engines, leading to quieter operations and reduced noise pollution in communities near airports.
- Enhanced Sustainability: The transition to electric and hybrid aircraft aligns with global efforts to combat climate change and promote sustainable transportation.
Hypersonic Flight
Hypersonic flight, exceeding Mach 5, is another exciting frontier in aerospace technology. Hypersonic aircraft can travel at speeds exceeding 3,800 miles per hour, enabling faster transcontinental travel and potentially revolutionizing space access.
- Rapid Transportation: Hypersonic flight offers the potential for significantly reduced travel times, enabling faster and more efficient transportation across long distances.
- Space Access: Hypersonic vehicles can serve as reusable launch vehicles, providing more affordable and frequent access to space for scientific research, commercial applications, and space tourism.
- Military Applications: Hypersonic aircraft have significant military implications, offering faster deployment of troops and equipment, as well as improved reconnaissance and strike capabilities.
Space Tourism
Space tourism, once a futuristic concept, is becoming increasingly accessible with the development of reusable spacecraft and commercial spaceflight companies. Private companies are investing heavily in space tourism, offering suborbital and orbital flights for adventurous individuals.
- Commercialization of Space: Space tourism is driving the commercialization of space, creating new industries and opportunities for investment and innovation.
- Increased Public Interest: Space tourism is generating widespread public interest in space exploration, inspiring future generations to pursue careers in STEM fields.
- Technological Advancements: The development of reusable spacecraft and space tourism infrastructure is pushing the boundaries of aerospace technology, leading to advancements in propulsion systems, life support, and safety protocols.
Last Recap
As we stand on the precipice of a new era in aviation, the future of aircraft engineering & aerospace technology holds immense promise. From electric and hybrid aircraft to hypersonic flight and space tourism, the possibilities are boundless. The challenges ahead are significant, but with continued innovation, collaboration, and a commitment to pushing the limits of human ingenuity, the sky truly is the limit.
Aircraft engineering and aerospace technology are constantly evolving, pushing the boundaries of what’s possible in flight. This constant drive for innovation is evident in the advancements seen in the Atlas SE and SE with technology, which you can read more about here.
These advancements not only improve performance but also enhance safety and efficiency, contributing to the ongoing progress in aircraft engineering and aerospace technology.