PAC Technologies: A Comprehensive Guide
PAC Technologies, a transformative force in the modern landscape, offer a compelling narrative of innovation and efficiency. This exploration delves into the intricate world of PAC technologies, uncovering their origins, […]
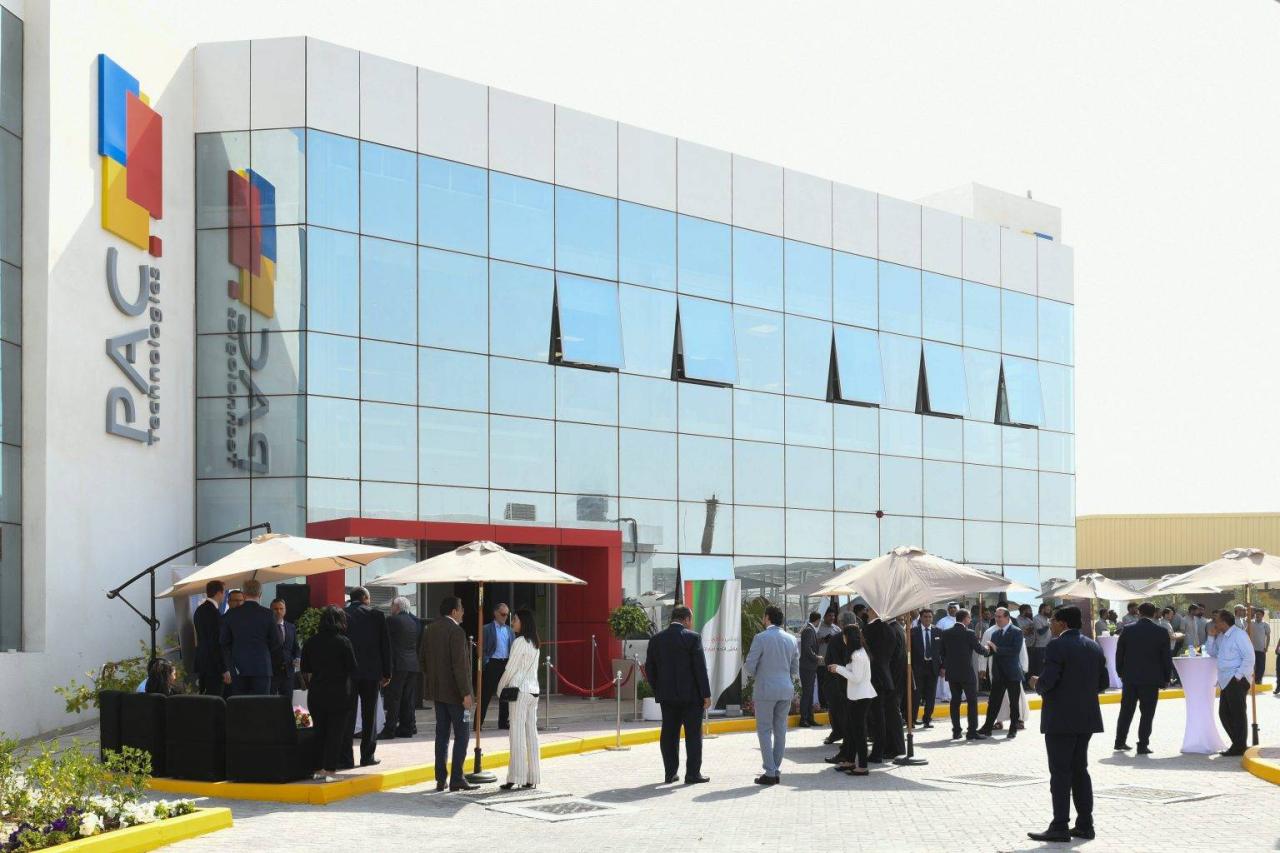
PAC Technologies, a transformative force in the modern landscape, offer a compelling narrative of innovation and efficiency. This exploration delves into the intricate world of PAC technologies, uncovering their origins, diverse applications, and the profound impact they have on various industries.
From the core principles that define PAC technologies to the latest advancements shaping their future, this comprehensive guide provides a detailed examination of this dynamic field. We’ll explore the different types of PAC technologies, their unique benefits, and the challenges that accompany their implementation. Through real-world examples and insightful perspectives, we’ll gain a deeper understanding of the transformative power of PAC technologies and their potential to reshape our future.
PAC Technologies
PAC technologies, also known as Process Automation and Control technologies, encompass a range of tools, techniques, and systems that streamline and optimize industrial processes. They are essential for achieving efficient, reliable, and safe operations in various industries, from manufacturing and energy to pharmaceuticals and food processing.
Key Characteristics and Functionalities
PAC technologies are characterized by their ability to monitor, control, and optimize industrial processes in real-time. They rely on advanced sensors, actuators, and control systems to gather data, analyze it, and make decisions to adjust process parameters automatically.
- Data Acquisition and Monitoring: PAC technologies use sensors to collect real-time data from various process parameters, such as temperature, pressure, flow rate, and level. This data is then transmitted to a central control system for analysis and visualization.
- Process Control: Based on the collected data, PAC technologies use algorithms and control strategies to adjust process variables automatically, ensuring optimal performance and safety. This can involve adjusting flow rates, temperatures, or pressures to maintain desired setpoints.
- Optimization and Efficiency: PAC technologies analyze process data to identify areas for improvement and optimize performance. This can include reducing waste, minimizing energy consumption, and maximizing productivity.
- Safety and Reliability: PAC technologies play a crucial role in enhancing safety by detecting potential hazards and triggering appropriate responses. They also improve reliability by ensuring consistent process performance and reducing downtime.
Evolution of PAC Technologies
PAC technologies have evolved significantly over the years, driven by advancements in computing power, communication networks, and software development.
- Early Days (1960s-1980s): Early PAC systems were primarily based on analog controllers and hardwired logic. They were limited in their capabilities and required extensive manual configuration.
- Rise of Programmable Logic Controllers (PLCs) (1980s-1990s): The introduction of PLCs revolutionized PAC technologies. PLCs offered more flexibility, programmability, and integration capabilities, allowing for more complex process control applications.
- Integration of Distributed Control Systems (DCS) (1990s-2000s): DCS emerged as a distributed approach to process control, allowing for centralized monitoring and control of large-scale industrial processes across multiple locations.
- Modern Era (2000s-Present): Modern PAC technologies are characterized by the convergence of various technologies, including advanced automation, industrial internet of things (IIoT), cloud computing, and artificial intelligence (AI). These technologies enable more sophisticated process control, data analytics, and predictive maintenance capabilities.
Types of PAC Technologies
PAC technologies, also known as programmable automation controllers, are a diverse group of devices that play a crucial role in modern automation systems. They offer a wide range of functionalities and are used across various industries. Understanding the different types of PAC technologies is essential for selecting the most appropriate solution for a given application.
PAC Technology Categories
PAC technologies can be broadly categorized into three main types:
- Programmable Logic Controllers (PLCs): PLCs are the most traditional and widely used type of PAC technology. They are designed for industrial automation applications and are known for their ruggedness, reliability, and ability to handle real-time control tasks. PLCs are typically used in applications such as manufacturing, process control, and robotics.
- Programmable Automation Controllers (PACs): PACs are a more recent development and are designed to address the increasing complexity of modern automation systems. They offer more advanced features and functionalities compared to PLCs, such as integrated motion control, networking capabilities, and advanced programming languages. PACs are often used in applications that require high levels of flexibility and integration.
- Industrial Personal Computers (IPCs): IPCs are essentially industrial-grade PCs that are designed for use in harsh environments. They offer a high level of computing power and flexibility and are often used in applications that require data acquisition, analysis, and visualization. IPCs are also used in conjunction with PLCs and PACs to provide higher-level control and decision-making capabilities.
PAC Technology Applications
The specific applications of PAC technologies vary depending on the type and the specific features and functionalities they offer. Here are some common applications for each type of PAC technology:
PLC Applications
- Machine Control: PLCs are widely used to control various industrial machines, such as conveyors, robots, and packaging machines. They are responsible for controlling the movement, speed, and sequence of operations of these machines.
- Process Control: PLCs are also used in process control applications, such as chemical plants, power plants, and water treatment facilities. They monitor and control the flow of materials, temperature, pressure, and other process parameters.
- Robotics: PLCs are used in robotics applications to control the movement and operation of robots. They are often used in conjunction with other automation components, such as sensors and actuators.
PAC Applications
- Motion Control: PACs are often used in applications that require precise and coordinated motion control, such as CNC machines, robotics, and packaging systems. They offer advanced motion control capabilities, such as interpolation, trajectory planning, and synchronization.
- Data Acquisition and Analysis: PACs can be used to collect data from various sensors and devices and perform real-time data analysis. They can be used to monitor process parameters, identify trends, and optimize system performance.
- Human-Machine Interface (HMI): PACs can be used to provide a user-friendly interface for operators to monitor and control automation systems. They can display real-time data, provide graphical representations of processes, and allow operators to interact with the system.
IPC Applications
- Data Acquisition and Logging: IPCs can be used to collect data from sensors and devices and store it for later analysis. They are often used in applications where data logging is required for compliance or troubleshooting purposes.
- Supervisory Control and Data Acquisition (SCADA): IPCs are often used in SCADA systems to provide a centralized control and monitoring platform for large-scale automation systems. They can collect data from multiple PLCs and PACs and provide a comprehensive view of the entire system.
- Process Optimization: IPCs can be used to analyze data collected from automation systems and identify opportunities for process optimization. They can be used to adjust control parameters, optimize production schedules, and improve overall system efficiency.
PAC Technology Features
Type | Description | Applications | Benefits |
---|---|---|---|
PLC | Rugged, reliable, and designed for industrial automation applications. | Machine control, process control, robotics. | High reliability, ease of programming, rugged design. |
PAC | More advanced and flexible than PLCs, offering integrated motion control, networking capabilities, and advanced programming languages. | Motion control, data acquisition and analysis, human-machine interface (HMI). | Advanced features and functionalities, high flexibility, increased integration capabilities. |
IPC | Industrial-grade PCs designed for harsh environments, offering high computing power and flexibility. | Data acquisition and logging, supervisory control and data acquisition (SCADA), process optimization. | High computing power, flexibility, advanced data processing capabilities. |
Benefits of Implementing PAC Technologies
The adoption of PAC technologies offers numerous advantages across various industries, enhancing operational efficiency, profitability, and overall business success. These technologies empower organizations to streamline processes, improve decision-making, and gain a competitive edge in today’s dynamic marketplace.
Enhanced Efficiency and Productivity
The implementation of PAC technologies can significantly improve efficiency and productivity by automating tasks, streamlining workflows, and minimizing human error. For instance, in manufacturing, PAC systems can optimize production processes by monitoring real-time data, identifying bottlenecks, and adjusting parameters to maximize output. This results in reduced downtime, increased throughput, and improved overall efficiency.
Illustrative Examples
PAC technologies, in their various forms, are transforming the way we interact with the world around us. To better understand their real-world impact, let’s explore some illustrative examples of PAC technologies in action.
Real-World Use Case: Predictive Maintenance in Manufacturing
PAC technologies are revolutionizing the manufacturing industry by enabling predictive maintenance. This involves using sensors and data analytics to anticipate equipment failures before they occur, minimizing downtime and maximizing production efficiency. Consider a large-scale manufacturing plant that produces automobiles. By installing sensors on critical machinery, such as assembly line robots, the plant can collect data on vibration, temperature, and other key parameters. This data is then analyzed using machine learning algorithms to identify patterns that indicate potential failures. If the system detects an anomaly, it can send an alert to maintenance personnel, allowing them to address the issue before it leads to a costly breakdown. This proactive approach significantly reduces downtime, improves product quality, and enhances overall operational efficiency.
“Predictive maintenance is not just about extending the life of equipment; it’s about transforming the way we manage our operations.” – Dr. Sarah Jones, Chief Technology Officer, Global Manufacturing Solutions
Wrap-Up
As we conclude our journey into the realm of PAC technologies, one thing becomes abundantly clear: they are poised to play a pivotal role in shaping the future of industries across the globe. From streamlining operations to enhancing efficiency and fostering innovation, PAC technologies offer a compelling path toward a more intelligent and interconnected world. By embracing the opportunities and addressing the challenges presented by PAC technologies, we can unlock their transformative potential and pave the way for a brighter future.
PAC Technologies is a leading provider of innovative solutions for various industries. Their focus on efficiency and quality has led them to partner with companies like CA Technologies, known for their cutting-edge air-assisted airless technology. CA Technologies air-assisted airless systems offer a unique blend of speed, precision, and control, perfectly aligning with PAC Technologies’ commitment to delivering exceptional results.
This collaboration showcases the synergy between two industry leaders, driving progress in the field of advanced technologies.