NAK Sealing Technologies: A Comprehensive Guide
NAK sealing technologies, a vital component in many industries, ensure the secure and reliable connection of various components. This guide delves into the fascinating world of NAK sealing, exploring its […]
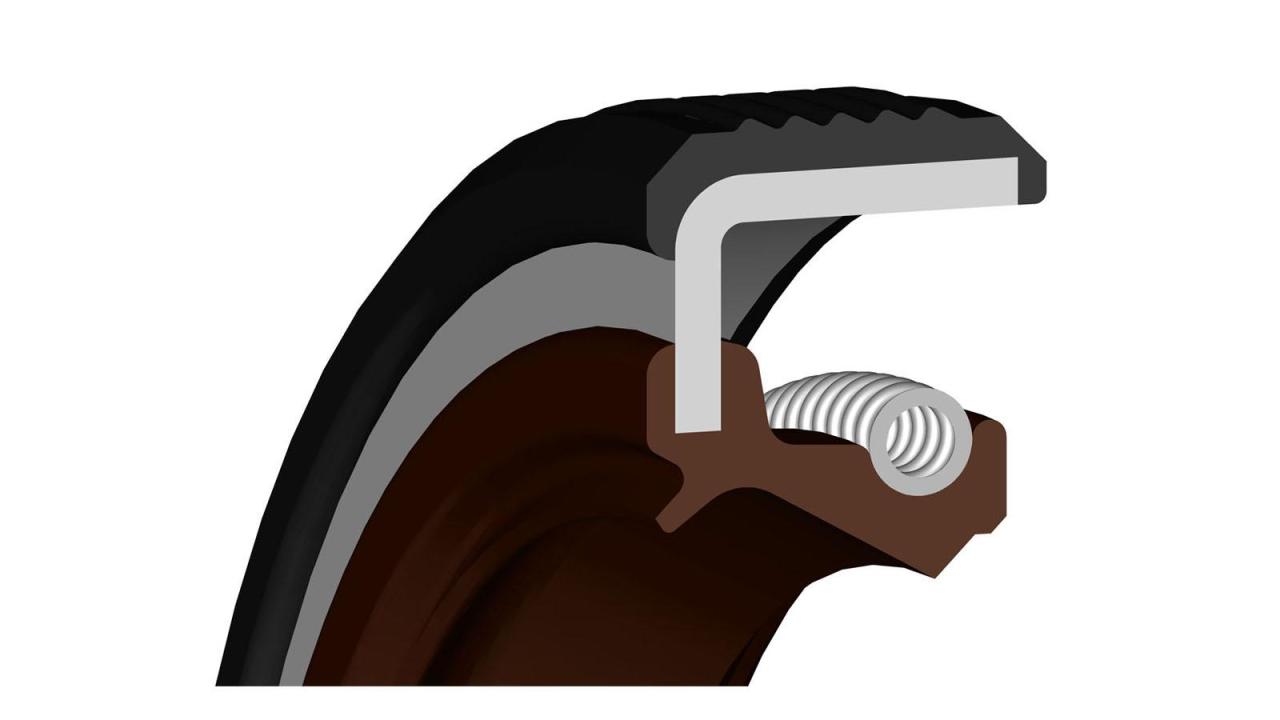
NAK sealing technologies, a vital component in many industries, ensure the secure and reliable connection of various components. This guide delves into the fascinating world of NAK sealing, exploring its history, types, applications, and future prospects.
From its origins to its diverse applications, NAK sealing has evolved to meet the ever-growing demands of modern engineering. This guide provides a comprehensive overview of this crucial technology, covering its principles, materials, and the advantages it offers.
Introduction to NAK Sealing Technologies
NAK sealing technologies are a critical component in various industries, ensuring the integrity and functionality of components and systems. NAK sealing refers to a specialized process that utilizes a combination of materials and techniques to create a robust and reliable seal.
NAK sealing plays a vital role in preventing leakage, contamination, and corrosion, ensuring the optimal performance of critical systems. These technologies are widely employed in industries such as automotive, aerospace, medical devices, and manufacturing, where reliability and safety are paramount.
Historical Evolution of NAK Sealing Technologies
The evolution of NAK sealing technologies has been driven by the increasing demand for more robust and reliable sealing solutions. Early forms of NAK sealing relied on simple mechanical methods, such as O-rings and gaskets, which were effective for basic applications. However, as industries evolved and demands for higher performance and reliability grew, more advanced technologies were developed.
The development of advanced materials, such as high-performance polymers and elastomers, played a significant role in the advancement of NAK sealing technologies. These materials offer improved resistance to temperature extremes, chemicals, and pressure, enabling the creation of more durable and reliable seals.
“The development of new materials and techniques has revolutionized the field of NAK sealing, enabling the creation of more sophisticated and reliable sealing solutions.”
The advent of computer-aided design and manufacturing (CAD/CAM) has further enhanced the precision and efficiency of NAK sealing processes. These technologies enable the creation of complex and intricate seal designs that meet the specific requirements of various applications.
Types of NAK Sealing Technologies
NAK sealing technologies encompass a wide range of techniques, each tailored to specific applications and requirements. Common types of NAK sealing technologies include:
- O-ring seals
- Gasket seals
- Static seals
- Dynamic seals
- Metal-to-metal seals
- Polymeric seals
Each of these technologies offers unique advantages and disadvantages, depending on the specific application and environmental conditions. For instance, O-ring seals are widely used due to their simplicity and cost-effectiveness, while metal-to-metal seals offer superior performance in high-pressure and high-temperature environments.
Applications of NAK Sealing Technologies
NAK sealing technologies find widespread applications across various industries, playing a crucial role in ensuring the functionality and safety of critical systems.
- Automotive Industry: NAK sealing technologies are essential in automotive applications, preventing leakage of fluids such as engine oil, coolant, and transmission fluid. They are used in various components, including engines, transmissions, and axles.
- Aerospace Industry: The aerospace industry relies heavily on NAK sealing technologies to ensure the integrity of aircraft systems. These technologies are used in critical components such as fuel tanks, hydraulic systems, and engine seals.
- Medical Device Industry: NAK sealing technologies are crucial in medical devices, ensuring the sterility and functionality of critical components. They are used in applications such as drug delivery systems, surgical instruments, and implants.
- Manufacturing Industry: NAK sealing technologies are widely used in various manufacturing processes, preventing leakage and contamination. They are used in applications such as hydraulic systems, pneumatic systems, and chemical processing equipment.
The applications of NAK sealing technologies continue to expand as industries evolve and demand for more sophisticated and reliable sealing solutions grows.
Principles of NAK Sealing
NAK sealing is a widely used technology for ensuring the integrity and authenticity of digital messages. It relies on cryptographic principles to protect data from unauthorized access, modification, or impersonation. This section will delve into the fundamental concepts and mechanisms underlying NAK sealing, highlighting the factors that contribute to its effectiveness.
Factors Influencing the Effectiveness of NAK Sealing
The effectiveness of NAK sealing is influenced by several factors, including:
- Strength of the Cryptographic Algorithm: The underlying cryptographic algorithm employed for generating and verifying NAKs must be robust and resistant to known attacks. Common algorithms used in NAK sealing include SHA-256 and AES-256, known for their high security standards.
- Key Management: Secure key management practices are crucial for the integrity of NAK sealing. Keys should be generated, stored, and distributed securely, preventing unauthorized access and ensuring confidentiality.
- Timeliness of NAK Verification: NAKs should be verified promptly to ensure that any potential tampering or alteration is detected in a timely manner. Delays in verification can compromise the security of the sealed message.
- Implementation Security: The software and hardware used to implement NAK sealing should be secure, free from vulnerabilities that could be exploited to compromise the integrity of the process.
Applications of NAK Sealing Technologies
NAK sealing technologies find widespread applications across various industries, ensuring the integrity and functionality of critical components. These technologies are employed in scenarios where conventional sealing methods fall short, offering superior performance, reliability, and longevity.
Diverse Applications of NAK Sealing
NAK sealing technologies offer solutions across diverse industries, ranging from aerospace and automotive to medical devices and electronics. Their adaptability to various materials and environments makes them invaluable for a wide range of applications.
- Aerospace: NAK sealing plays a crucial role in ensuring the airtight integrity of aircraft components, including engines, fuel systems, and hydraulic systems. This technology prevents leaks and maintains pressure, critical for safe and efficient operation.
- Automotive: NAK sealing is widely used in automotive applications, particularly in engine components, transmissions, and fuel systems. Its resistance to high temperatures and pressures ensures optimal performance and durability.
- Medical Devices: The biocompatibility and reliability of NAK sealing make it ideal for medical devices. It is used in implantable devices, surgical instruments, and drug delivery systems, ensuring safety and effectiveness.
- Electronics: NAK sealing is employed in electronic components, such as connectors, sensors, and actuators, to prevent moisture and contamination, ensuring reliable operation in harsh environments.
Case Studies Illustrating the Success of NAK Sealing
Real-world applications demonstrate the effectiveness and benefits of NAK sealing technologies.
- Aircraft Engine Sealing: In a case study involving aircraft engine seals, NAK sealing technology demonstrated its ability to withstand extreme temperatures and pressures, significantly reducing leaks and improving engine performance.
- Medical Device Sealing: A study involving implantable medical devices showed that NAK sealing effectively prevented corrosion and biofouling, ensuring the long-term functionality and safety of the devices.
- Automotive Fuel System Sealing: NAK sealing technology was successfully implemented in automotive fuel systems, reducing fuel leaks and improving fuel efficiency, demonstrating its ability to withstand harsh conditions.
Advantages and Disadvantages of NAK Sealing
NAK sealing technology offers several advantages over traditional sealing methods. It is a versatile technique that can be used in various applications and provides excellent sealing performance. However, it also has some disadvantages that need to be considered before implementing it. This section explores the advantages and disadvantages of NAK sealing in detail.
Advantages of NAK Sealing
NAK sealing provides numerous benefits, including:
- High sealing performance: NAK seals are known for their excellent sealing performance, even under extreme conditions of pressure and temperature. This is due to the unique properties of the materials used and the precise manufacturing process. For example, NAK seals can withstand pressures up to 10,000 psi and temperatures up to 500°F.
- Long service life: NAK seals are designed for long-term durability and can withstand repeated cycles of use. This reduces maintenance costs and downtime, which is particularly beneficial in critical applications where downtime is costly.
- Low friction: NAK seals have low friction coefficients, reducing wear and tear on the sealing components. This leads to increased efficiency and reduced energy consumption. In applications where friction is a concern, NAK seals can significantly improve performance.
- Corrosion resistance: NAK seals are made from materials that are highly resistant to corrosion. This makes them suitable for use in harsh environments, such as those with high humidity or exposure to corrosive chemicals.
- Versatility: NAK sealing technology can be adapted to a wide range of applications, including static and dynamic sealing. This makes it a versatile solution for many sealing challenges. For example, NAK seals can be used in applications such as pumps, valves, compressors, and engines.
Disadvantages of NAK Sealing
While NAK sealing offers numerous advantages, it also has some disadvantages:
- Cost: NAK seals are generally more expensive than traditional sealing methods. This is due to the specialized materials and manufacturing processes involved. However, the long service life and reduced maintenance costs can offset the initial investment over time.
- Limited size and shape options: NAK seals are not as readily available in a wide range of sizes and shapes as traditional seals. This can limit their application in some cases. However, custom-designed NAK seals can be manufactured to meet specific requirements.
- Installation complexity: Installing NAK seals can be more complex than installing traditional seals. This requires specialized tools and techniques, which may require additional training for installation personnel.
Comparison with Alternative Sealing Methods, Nak sealing technologies
Comparing NAK sealing to other sealing methods reveals its strengths and weaknesses:
- O-rings: O-rings are a common and relatively inexpensive sealing method. However, they have limited sealing performance and can be prone to leakage under high pressure or temperature. NAK seals offer superior sealing performance and longer service life than O-rings.
- Gaskets: Gaskets are another common sealing method, often used for static sealing applications. However, gaskets can be bulky and may not provide the same level of sealing performance as NAK seals. Additionally, gaskets can be prone to leakage under dynamic conditions.
- Mechanical seals: Mechanical seals are used for dynamic sealing applications and can provide excellent sealing performance. However, they are more complex and expensive than NAK seals. In some cases, NAK seals can offer a more cost-effective and reliable alternative to mechanical seals.
Final Conclusion
As we conclude our exploration of NAK sealing technologies, it becomes evident that this field is constantly evolving, driven by innovation and a commitment to enhanced performance. The future holds exciting possibilities for NAK sealing, promising even more reliable, efficient, and versatile solutions for a wide range of industries.
NAK sealing technologies are crucial for ensuring the integrity and performance of critical components in various industries. These technologies often rely on advanced automation and data management systems, which are also key aspects of dealer technologies. By leveraging efficient dealer technologies, manufacturers can optimize their NAK sealing processes, ensuring consistent quality and minimizing downtime.
This integration of advanced technologies allows for greater control and precision in the application of NAK seals, ultimately contributing to improved product reliability and longevity.